El proceso de fabricación de un molde implica varios pasos críticos, empezando por la fase de diseño y conceptualización, en la que se crea un modelo 3D de la pieza.A continuación se selecciona el material adecuado para el molde, que es esencial para garantizar la durabilidad y el rendimiento.Los pasos siguientes incluyen la creación del diseño del molde, su fabricación mediante técnicas como el mecanizado CNC o la impresión 3D y, por último, el ensayo y perfeccionamiento del molde para garantizar que cumple las especificaciones requeridas.Cada paso requiere una cuidadosa planificación y ejecución para producir un molde de alta calidad.
Explicación de los puntos clave:
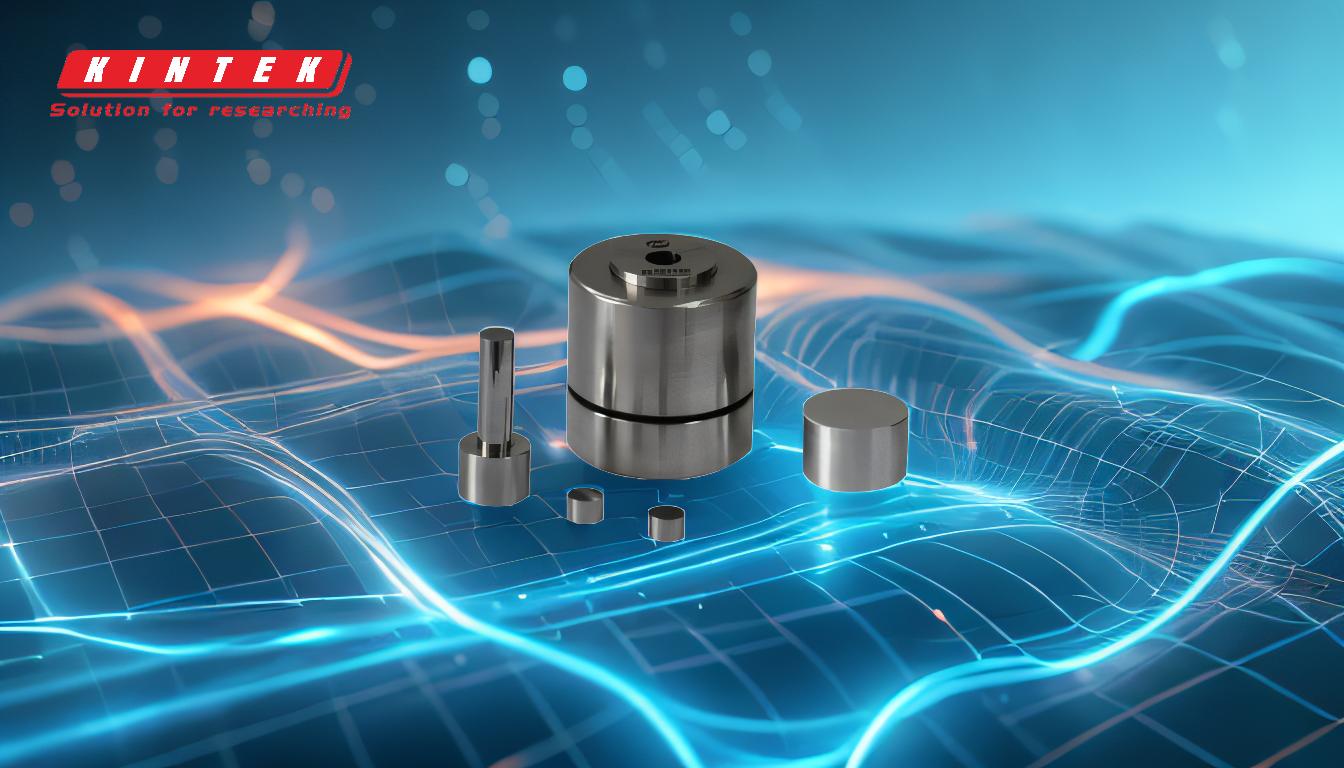
-
Diseño y conceptualización:
- Propósito:Esta fase consiste en crear un modelo 3D detallado de la pieza que se va a fabricar.Garantiza que el molde reproducirá con precisión la forma y las características deseadas.
- Proceso:Los ingenieros y diseñadores utilizan software CAD (diseño asistido por ordenador) para desarrollar el modelo, teniendo en cuenta factores como la geometría de la pieza, el flujo de material y los requisitos de refrigeración.
- Resultado:Un plano preciso que guía todo el proceso de fabricación del molde.
-
Selección de materiales:
- Importancia:El material utilizado para el molde debe soportar las tensiones del proceso de fabricación, incluidas las altas temperaturas y presiones.
- Criterios:Se tienen en cuenta factores como la conductividad térmica, la dureza y la resistencia al desgaste.Los materiales más comunes son el acero, el aluminio y los materiales compuestos.
- Impacto:El material adecuado garantiza la longevidad del molde y la calidad del producto final.
-
Diseño del molde:
- Detalles:Este paso consiste en traducir el modelo 3D en un diseño de molde, incluida la creación de cavidades, núcleos y canales de refrigeración.
- Consideraciones:Los diseñadores deben tener en cuenta la expulsión de piezas, la contracción y los posibles defectos, como alabeos o trampas de aire.
- Herramientas:Se utilizan herramientas de software avanzadas para simular el proceso de moldeo por inyección, optimizando el diseño en términos de eficacia y calidad.
-
Fabricación de moldes:
- Técnicas:El molde suele fabricarse mediante mecanizado CNC, electroerosión (EDM) o impresión 3D, en función de la complejidad y el material.
- Precisión:Se requiere una gran precisión para garantizar que los componentes del molde encajen perfectamente y que el producto final cumpla las tolerancias dimensionales.
- Control de calidad:A lo largo del proceso de fabricación, se realizan rigurosos controles de calidad para detectar y corregir cualquier desviación del diseño.
-
Pruebas y perfeccionamiento:
- Propósito:Una vez fabricado el molde, se somete a pruebas para garantizar que produce piezas que cumplen las especificaciones requeridas.
- Proceso:Se realizan las primeras pruebas y se comprueba si las piezas producidas presentan defectos.Si es necesario, se realizan ajustes en el molde.
- Finalización:Una vez superadas las pruebas, el molde está listo para la producción, lo que garantiza una calidad constante en las piezas fabricadas.
Siguiendo estos pasos meticulosamente, los fabricantes pueden crear moldes de alta calidad que son esenciales para producir componentes precisos y fiables en diversas industrias.
Tabla resumen:
Paso | Detalles clave |
---|---|
Diseño y conceptualización |
- Cree un modelo 3D utilizando software CAD.
- Tenga en cuenta la geometría de la pieza, el flujo de material y la refrigeración. |
Selección de materiales | - Elija materiales como el acero o el aluminio en función de su conductividad térmica y durabilidad. |
Diseño de moldes |
- Traduzca el modelo 3D en un diseño de molde.
- Incluya cavidades, núcleos y canales de refrigeración. |
Fabricación de moldes |
- Utilice el mecanizado CNC, la electroerosión o la impresión 3D.
- Garantice la precisión y el control de calidad. |
Pruebas y perfeccionamiento |
- Realización de pruebas e inspección de piezas.
- Perfeccione el molde para cumplir las especificaciones. |
¿Necesita un molde de alta calidad para su proyecto? Póngase en contacto con nosotros ¡para empezar!