La sinterización es un proceso crítico para el óxido de circonio, que lo transforma en un material denso, resistente y duradero.Durante la sinterización, la zirconia experimenta importantes cambios físicos y químicos, como la eliminación de la porosidad, la evaporación de los aglutinantes y el crecimiento del grano, que en conjunto mejoran sus propiedades mecánicas.El proceso suele consistir en calentar la zirconia a altas temperaturas, lo que permite que las partículas se adhieran y densifiquen, seguido de un enfriamiento controlado para conseguir la microestructura deseada.El resultado es un material con porosidad reducida, mayor densidad y dureza mejorada, lo que lo hace adecuado para aplicaciones exigentes como coronas dentales, componentes industriales y cerámica avanzada.
Explicación de los puntos clave:
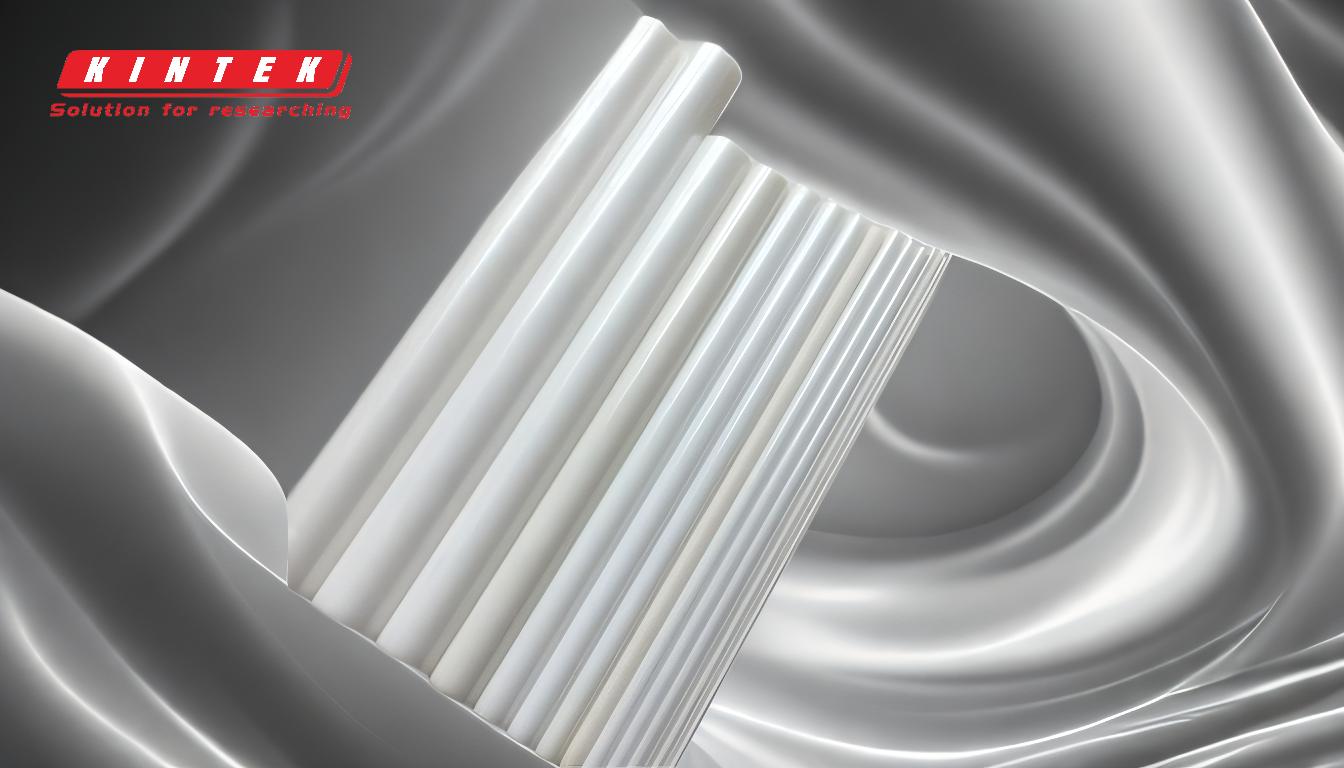
-
Reducción de la porosidad y aumento de la densidad:
- La sinterización reduce significativamente la porosidad de la zirconia al eliminar los huecos entre las partículas.Esto se consigue mediante la aplicación de calor, que hace que las partículas se adhieran y densifiquen.
- La eliminación de la porosidad da lugar a un material más homogéneo y denso, que mejora su resistencia mecánica y durabilidad.
-
Cambios físicos y químicos:
- Durante la sinterización, la zirconia experimenta complejas transformaciones, como la evaporación de agua o aglutinantes orgánicos, la eliminación de gases adsorbidos y la reducción de óxidos superficiales.
- Estos cambios facilitan la migración del material, la recristalización y el crecimiento del grano, que son esenciales para conseguir la microestructura y las propiedades deseadas.
-
Contracción y cambios dimensionales:
- La zirconia experimenta una contracción significativa durante la sinterización, que suele oscilar entre el 20% y el 30%.Esta contracción es el resultado de la unión y densificación de las partículas.
- Es necesario un control adecuado del proceso de sinterización para gestionar los cambios dimensionales y garantizar que el producto final cumpla unas especificaciones precisas.
-
Fases de calentamiento, sinterización y enfriamiento:
-
El proceso de sinterización suele constar de tres fases: calentamiento, sinterización y enfriamiento.
- Fase de calentamiento:El calor se transfiere a la superficie de la zirconia y se conduce a su núcleo, preparando el material para la sinterización.
- Fase de sinterización:A altas temperaturas, las partículas se adhieren y densifican, reduciendo la porosidad y aumentando la densidad.
- Fase de enfriamiento:El enfriamiento controlado garantiza que el material conserve la microestructura y las propiedades mecánicas deseadas.
-
El proceso de sinterización suele constar de tres fases: calentamiento, sinterización y enfriamiento.
-
Propiedades mecánicas mejoradas:
- La sinterización mejora la dureza, resistencia y resistencia al desgaste de la zirconia, lo que la hace idónea para aplicaciones de alto rendimiento.
- El proceso también mejora la estabilidad térmica y química del material, lo que le permite resistir entornos difíciles.
-
Aplicaciones del óxido de circonio sinterizado:
- El óxido de circonio sinterizado se utiliza ampliamente en restauraciones dentales, como coronas y puentes, debido a su biocompatibilidad y resistencia.
- También se utiliza en aplicaciones industriales, como herramientas de corte, cojinetes y componentes resistentes al desgaste, donde la durabilidad y la precisión son fundamentales.
Al comprender el proceso de sinterización y sus efectos sobre la zirconia, los fabricantes y compradores pueden tomar decisiones informadas sobre la selección del material y los parámetros de procesamiento para lograr un rendimiento óptimo en sus aplicaciones.
Tabla resumen:
Efectos clave de la sinterización en el óxido de circonio | Detalles |
---|---|
Reducción de la porosidad | Elimina los huecos, aumentando la densidad y la resistencia. |
Cambios físicos y químicos | Elimina aglutinantes, gases y óxidos; permite el crecimiento del grano. |
Contracción | 20-30% de contracción debida a la unión de las partículas y a la densificación. |
Fases de calentamiento, sinterización y enfriamiento | Las fases controladas garantizan una microestructura óptima. |
Propiedades mejoradas | Mejora la dureza, la resistencia, la resistencia al desgaste y la estabilidad. |
Aplicaciones | Se utiliza en coronas dentales, herramientas industriales y componentes resistentes al desgaste. |
Descubra cómo el sinterizado puede optimizar el óxido de circonio para sus aplicaciones. contacte con nuestros expertos hoy mismo ¡!