La pulvimetalurgia (PM) es un proceso de fabricación versátil y eficaz con numerosas ventajas, como una gran precisión, rentabilidad y un mínimo desperdicio de material.Sin embargo, también tiene varias limitaciones y desventajas que pueden afectar a su idoneidad para determinadas aplicaciones.Entre ellas figuran las restricciones de tamaño debidas a la capacidad de la prensa, las dificultades para producir formas complejas y una menor resistencia mecánica y ductilidad en comparación con métodos tradicionales como la fundición o la forja.Además, pueden ser necesarios procesos de acabado secundarios, lo que añade tiempo y costes a la producción.Comprender estas limitaciones es crucial para seleccionar el método de fabricación adecuado para aplicaciones específicas.
Explicación de los puntos clave:
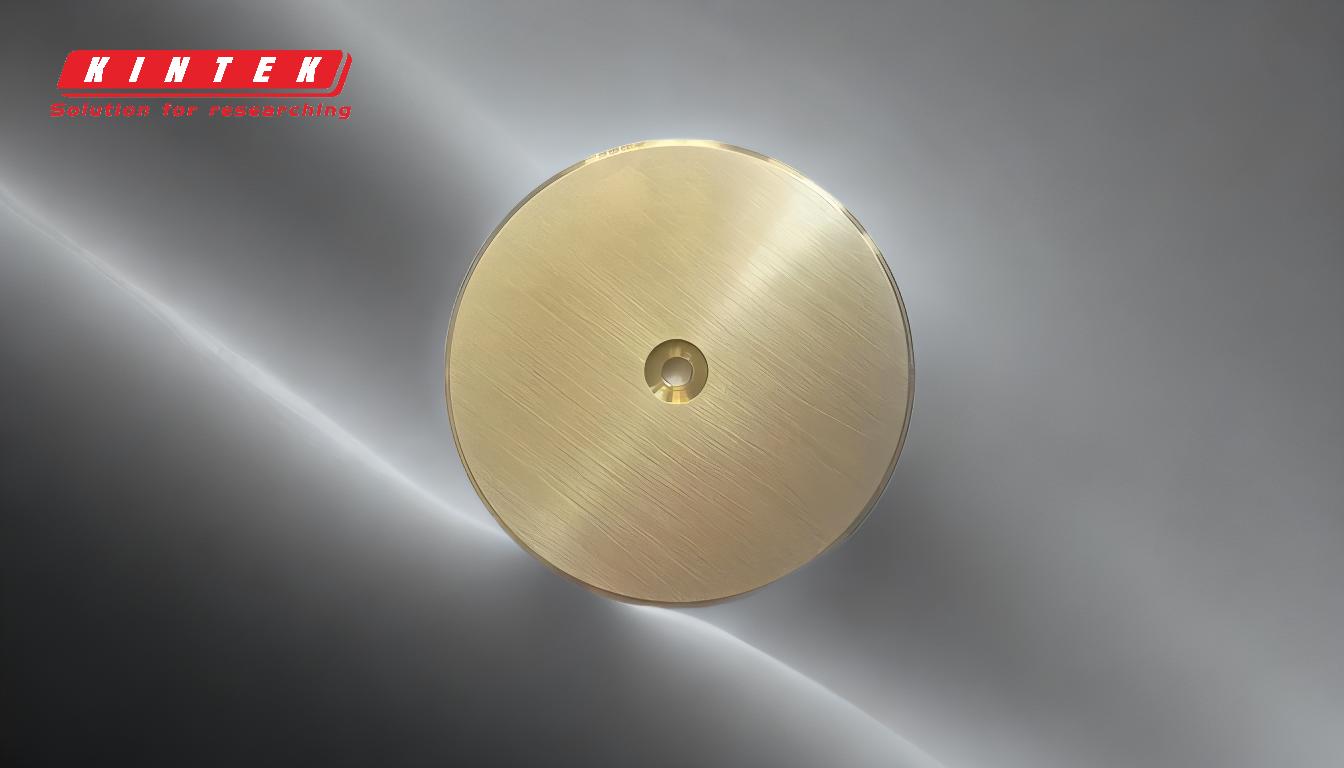
-
Limitaciones de tamaño:
- Explicación:El tamaño de las piezas producidas mediante pulvimetalurgia está limitado por la capacidad de las prensas utilizadas en el proceso.Las prensas más grandes disponibles en la industria son de unas 1.500 toneladas, lo que limita la superficie plana práctica de las piezas a aproximadamente 40-50 pulgadas cuadradas.Esto hace que la PM sea menos adecuada para fabricar componentes de gran tamaño.
- Implicaciones:Para las industrias que requieren piezas grandes, como la maquinaria pesada o la construcción a gran escala, la pulvimetalurgia puede no ser viable.Pueden ser necesarios métodos alternativos como la fundición o la forja.
-
Desafíos de las formas complejas:
- Explicación:Producir piezas de formas complejas puede ser difícil con la pulvimetalurgia.Aunque los fabricantes expertos pueden superar algunos de estos retos, el proceso tiene dificultades intrínsecas con las geometrías complejas en comparación con otros métodos de fabricación.
- Implicaciones:Para aplicaciones que requieren diseños muy complejos o intrincados, puede ser necesario un mecanizado adicional o procesos secundarios, lo que aumenta el tiempo y los costes de producción.
-
Menor resistencia mecánica y ductilidad:
- Explicación:Las piezas de PM no suelen alcanzar el mismo nivel de resistencia o ductilidad que las piezas fabricadas mediante fundición o forja.Esto se debe a la porosidad y microestructura inherentes a los materiales de PM.
- Implicaciones:En aplicaciones en las que un alto rendimiento mecánico es crítico, como en componentes estructurales aeroespaciales o de automoción, la PM puede no ser la mejor opción.Los ingenieros deben tener muy en cuenta las propiedades de los materiales a la hora de seleccionar los métodos de fabricación.
-
Requisitos de acabado secundario:
- Explicación:La pulvimetalurgia requiere a menudo procesos de acabado secundarios para conseguir la calidad superficial y la precisión dimensional deseadas.Estos procesos pueden incluir el mecanizado, el rectificado o el recubrimiento.
- Implicaciones:La necesidad de un acabado secundario aumenta el tiempo y el coste totales de producción, lo que puede ser una desventaja para proyectos con presupuestos o plazos ajustados.
-
Limitaciones del material:
- Explicación:Aunque la pulvimetalurgia es versátil y puede utilizarse con una amplia gama de metales, existen algunas limitaciones.Algunos materiales pueden no ser adecuados para la PM debido a sus propiedades o a la complejidad del procesamiento necesario.
- Implicaciones:La selección de materiales es crucial, y algunas aleaciones de alto rendimiento o materiales especializados pueden no ser viables para la PM, lo que limita su aplicación en determinadas industrias de alta tecnología.
-
Consideraciones económicas:
- Explicación:Aunque la PM suele ser rentable para la producción de grandes volúmenes, los costes iniciales de preparación de herramientas y equipos pueden ser elevados.Además, la necesidad de un acabado secundario puede incrementar aún más los costes.
- Implicaciones:En el caso de series de producción de bajo volumen o personalizadas, las ventajas económicas de la PM pueden no ser tan pronunciadas, lo que hace que otros métodos de fabricación resulten más atractivos.
En resumen, aunque la pulvimetalurgia ofrece muchas ventajas, como precisión, eficacia y ahorro de material, también tiene importantes limitaciones.Entre ellas se encuentran las restricciones de tamaño, los retos que plantean las formas complejas, las propiedades mecánicas inferiores, los requisitos de acabado secundario, las limitaciones de material y las consideraciones económicas.Comprender estos factores es esencial para tomar decisiones informadas sobre el uso de la pulvimetalurgia en diversas aplicaciones de fabricación.
Cuadro sinóptico:
Limitación | Explicación | Implicaciones |
---|---|---|
Limitaciones de tamaño | La capacidad de la prensa limita el tamaño de las piezas a ~40-50 pulgadas cuadradas. | No es adecuada para componentes grandes; se requieren alternativas como fundición/forja. |
Formas complejas | Problemas con geometrías complejas. | Puede ser necesario un mecanizado adicional o procesos secundarios, lo que aumenta los costes. |
Menor resistencia mecánica | Las piezas de PM tienen menor resistencia/ductilidad debido a la porosidad. | No es adecuado para aplicaciones de alto rendimiento como la aeroespacial o la automoción. |
Acabado secundario | Requiere procesos adicionales como el mecanizado o el revestimiento. | Añade tiempo y costes a la producción, lo que repercute en presupuestos o plazos ajustados. |
Limitaciones de los materiales | Algunos materiales son inadecuados debido a sus propiedades o a la complejidad de su procesamiento. | Limita la aplicación en industrias de alta tecnología que requieren materiales especializados. |
Consideraciones económicas | Los elevados costes iniciales de preparación y el acabado secundario aumentan los gastos. | Menos rentable para series pequeñas o personalizadas. |
¿Necesita ayuda para elegir el método de fabricación adecuado? Póngase en contacto con nuestros expertos para hablar de su proyecto.