La distancia del sustrato objetivo en el sputtering es un parámetro crítico que influye directamente en la calidad, uniformidad y espesor de la película fina depositada.Esta distancia debe controlarse cuidadosamente para garantizar unas condiciones de deposición óptimas, ya que afecta a la energía cinética de las partículas pulverizadas, a su direccionalidad y a la velocidad de deposición global.La distancia ideal entre el blanco y el sustrato varía en función de factores como el método de sputtering, el material del blanco, el material del sustrato, la presión de la cámara y la potencia del sputtering.Por lo general, se suele utilizar una distancia de 5 a 15 cm, pero las aplicaciones específicas pueden requerir ajustes para conseguir las propiedades deseadas de la película.Un espaciado adecuado garantiza una cobertura uniforme, minimiza los defectos y mejora la calidad general del revestimiento.
Explicación de los puntos clave:
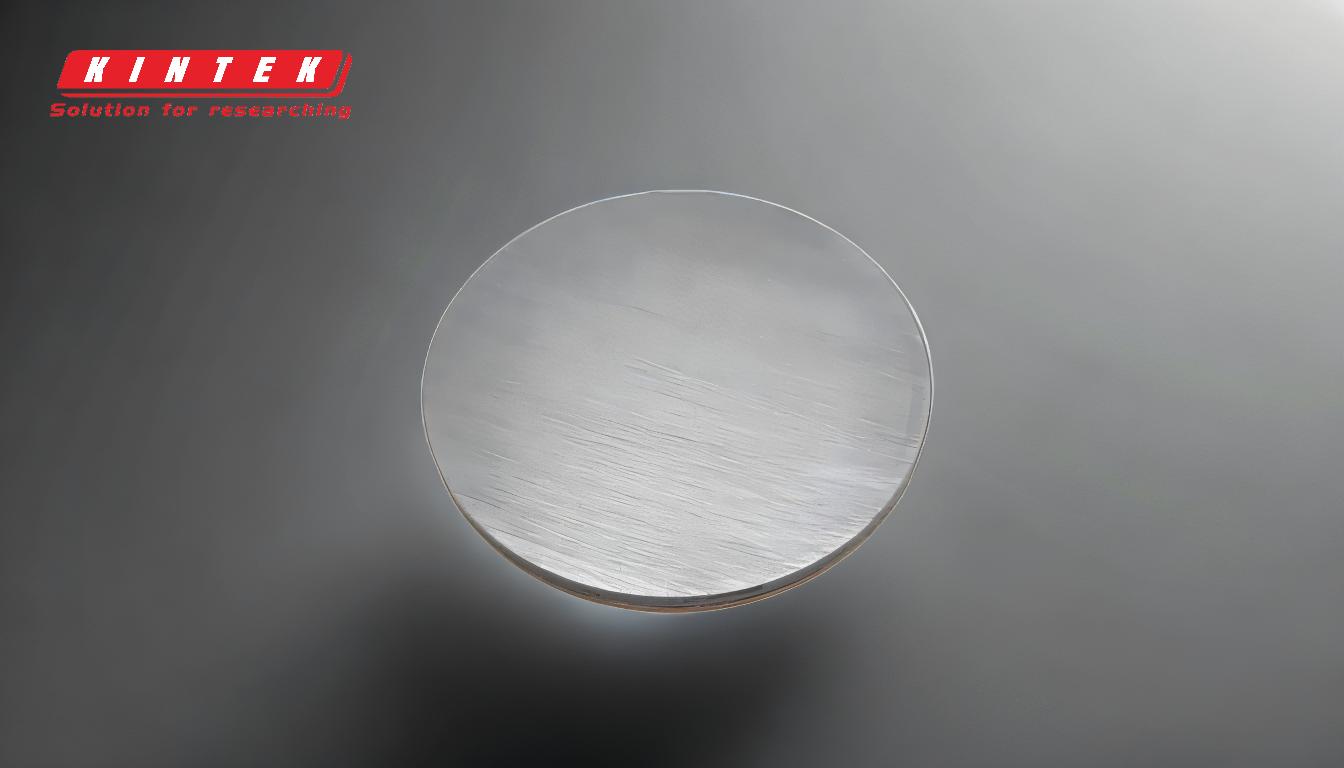
-
Importancia de la distancia al sustrato de destino:
- La distancia entre el blanco y el sustrato es crucial para lograr una deposición uniforme de la película fina.
- Afecta a la energía cinética y la direccionalidad de las partículas pulverizadas, lo que a su vez influye en el grosor, la uniformidad y la calidad de la película.
- Un espaciado adecuado garantiza velocidades de deposición uniformes y minimiza defectos como el revestimiento desigual o los huecos.
-
Intervalo típico para la distancia del sustrato objetivo:
- Un rango común para la distancia del sustrato objetivo en sputtering es 5 a 15 cm .
- Este rango es adecuado para la mayoría de las aplicaciones estándar de sputtering, proporcionando un equilibrio entre la velocidad de deposición y la calidad de la película.
- Sin embargo, puede ser necesario ajustar la distancia exacta en función de requisitos experimentales o industriales específicos.
-
Factores que influyen en la distancia óptima:
- Método Sputtering:Las diferentes técnicas de pulverización catódica (por ejemplo, CC, RF, magnetrón) pueden requerir distancias variables debido a las diferencias en la energía iónica y los mecanismos de deposición.
- Materiales del blanco y del sustrato:La masa y las propiedades de los materiales del cátodo y del sustrato influyen en el rendimiento del sputtering y en el comportamiento de las partículas.
- Presión de la cámara:Las presiones más altas pueden reducir la trayectoria libre media de las partículas, lo que requiere distancias más cortas para mantener la eficacia de la deposición.
- Potencia de pulverización catódica:Los niveles de potencia más altos pueden aumentar la energía de las partículas pulverizadas, permitiendo potencialmente mayores distancias del sustrato objetivo sin comprometer la calidad de la película.
-
Impacto en la velocidad de deposición y la calidad de la película:
- Tasa de deposición:Una distancia más corta generalmente aumenta la tasa de deposición debido a la reducción de la dispersión de partículas y a un mayor flujo de partículas sobre el sustrato.
- Calidad de la película:Una distancia mayor puede mejorar la uniformidad de la película al permitir que las partículas se extiendan más uniformemente por el sustrato, pero también puede reducir la eficacia de la deposición.
-
Consideraciones prácticas para la configuración del equipo:
- Uniformidad:Asegurarse de que el sustrato está colocado en paralelo a la superficie objetivo es esencial para conseguir un espesor de película uniforme.
- Ajustabilidad:Los sistemas de pulverización catódica deben permitir un ajuste preciso de la distancia del sustrato objetivo para adaptarse a diferentes materiales y condiciones de proceso.
- Monitorización:La supervisión en tiempo real del espesor y la calidad de la película puede ayudar a optimizar la distancia durante el proceso de sputtering.
-
Ajustes específicos de la aplicación:
- Revestimientos de alta precisión:Para aplicaciones que requieren revestimientos extremadamente uniformes o sin defectos, puede ser necesario minimizar y controlar cuidadosamente la distancia del sustrato de destino.
- Deposición a gran escala:En entornos industriales, pueden utilizarse distancias mayores para recubrir sustratos más grandes o múltiples sustratos simultáneamente, aunque esto puede requerir ajustes de otros parámetros (por ejemplo, potencia, presión) para mantener la calidad.
-
Optimización experimental:
- La distancia óptima del sustrato de destino suele determinarse experimentalmente para aplicaciones específicas.
- Factores como el espesor de película deseado, el tamaño del sustrato y las propiedades del material deben guiar el proceso de optimización.
En resumen, la distancia del sustrato objetivo en el sputtering es un parámetro clave que debe controlarse cuidadosamente para conseguir una deposición de película fina de alta calidad.Aunque se suele utilizar un intervalo general de 5 a 15 cm, la distancia exacta debe adaptarse al método de sputtering específico, a los materiales y a los requisitos de la aplicación.Un espaciado adecuado garantiza una deposición uniforme, minimiza los defectos y mejora el rendimiento general del sustrato recubierto.
Tabla resumen:
Factor clave | Impacto en el sustrato de destino Distancia |
---|---|
Alcance típico | 5 a 15 cm |
Método de sputtering | El sputtering DC, RF o magnetrón puede requerir ajustes en la distancia para obtener una energía iónica y un rendimiento óptimos. |
Materiales del blanco/sustrato | La masa y las propiedades del material afectan al rendimiento del sputtering y al comportamiento de las partículas. |
Presión de la cámara | Una presión más alta puede requerir distancias más cortas para mantener la eficacia de la deposición. |
Potencia de sputtering | Una mayor potencia permite mayores distancias sin comprometer la calidad de la película. |
Velocidad de deposición | Las distancias más cortas aumentan la tasa de deposición; las distancias más largas mejoran la uniformidad. |
Necesidades específicas de la aplicación | Los revestimientos de alta precisión o la deposición a gran escala pueden requerir distancias a medida. |
¿Necesita ayuda para optimizar su proceso de sputtering? Póngase en contacto con nuestros expertos para obtener soluciones a medida.