Principio del prensado isostático en frío (CIP)
Tabla de contenido
- Principio del prensado isostático en frío (CIP)
- Comparación entre CIP y prensado de moldes metálicos
- Introducción al prensado de moldes metálicos
- Procesos automatizados en equipos industriales de prensado de moldes metálicos.
- Diferencias en los procesos de presurización de CIP y prensado de moldes metálicos.
- Comparación de la distribución de densidad en productos moldeados por CIP y Metal Mould Pressing
- Tipos de procesamiento CIP
- Segmentación del mercado
- Detalles del proceso de bolsa húmeda
- Detalles del proceso de bolsa seca
Comprender el principio de CIP basado en el concepto de presión de Blaise Pascal
El prensado isostático en frío (CIP) es un método de procesamiento de materiales que se basa en el principio propuesto por Blaise Pascal, conocido como ley de Pascal. Según este principio, la presión aplicada en un fluido cerrado se transmite en todas direcciones a través del fluido sin ningún cambio en su magnitud.
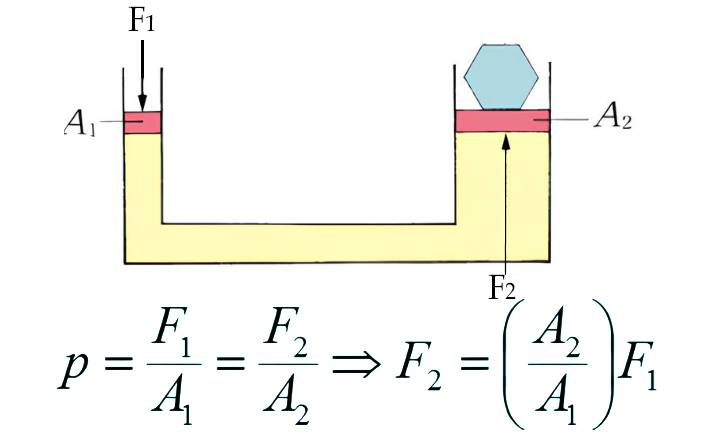
En CIP, los polvos se compactan encerrándolos en un molde de elastómero, que tiene baja resistencia a la deformación. Luego, el molde se somete a una presión líquida uniforme, que comprime los polvos. Esto da como resultado la formación de un sólido muy compacto.
CIP se puede utilizar para procesar una variedad de materiales, incluidos plásticos, grafito, metalurgia en polvo, cerámica y objetivos de pulverización catódica. Es un método versátil para dar forma y compactar polvos en componentes de diferentes tamaños y formas.
Proceso de sellado de materiales en polvo en un molde de formación y aplicación de presión líquida.
En el proceso CIP, los materiales en polvo se sellan en un molde de formación con baja resistencia a la deformación, como una bolsa de goma. Luego se aplica presión líquida al molde de manera uniforme, comprimiendo los polvos. Esta presión del líquido se transmite por todo el molde, dando como resultado la compresión uniforme del cuerpo moldeado en toda su superficie.
La CIP se realiza a temperatura ambiente y utiliza un molde hecho de un material elastómero, como uretano, caucho o cloruro de polivinilo. El fluido utilizado en CIP suele ser aceite o agua, y la presión aplicada durante la operación suele oscilar entre 60.000 lbs/in2 (400 MPa) y 150.000 lbs/in2 (1000 MPa).
La ventaja de CIP es que ayuda a reducir la distorsión, mejorar la precisión y minimizar el riesgo de aire atrapado y huecos. Se utiliza ampliamente en diversas industrias, incluidas la médica, la aeroespacial y la automotriz, para la producción de componentes.
El prensado de moldes de metal es un método similar al CIP. En este proceso, los materiales en polvo se introducen en un espacio limitado por el molde metálico y el punzón inferior. Luego se comprimen reduciendo la distancia entre los punzones superior e inferior.
En general, CIP es un método eficaz para dar forma y compactar materiales en polvo en componentes sólidos, proporcionando un alto nivel de precisión y reduciendo el riesgo de defectos.
Comparación entre CIP y prensado de moldes metálicos
Introducción al prensado de moldes metálicos
El prensado de moldes de metal es un método de procesamiento de materiales similar al prensado isostático en frío (CIP). En este método de prensado, los materiales en polvo se introducen en un espacio cerrado por el molde de metal y el punzón inferior. Luego se comprimen reduciendo la distancia entre los punzones superior e inferior.
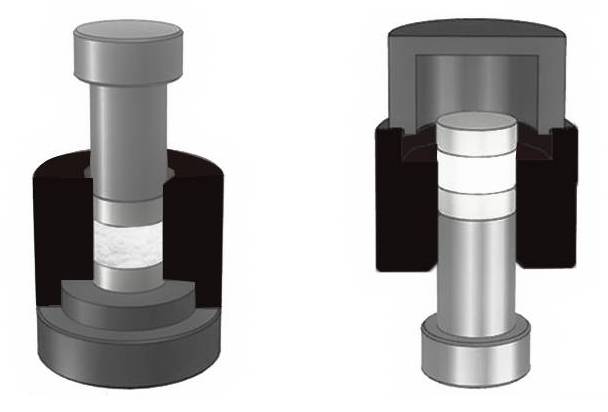
Procesos automatizados en equipos industriales de prensado de moldes metálicos.
Los equipos de prensado de moldes de metal utilizados en entornos industriales constan de una serie de procesos automatizados. Estos procesos incluyen el llenado de polvo, la compresión y la extracción del cuerpo moldeado. El prensado de simple efecto, un método común utilizado, comprime el polvo para darle forma con el punzón inferior fijo.
Diferencias en los procesos de presurización de CIP y prensado de moldes metálicos.
La principal diferencia entre CIP y el prensado de moldes metálicos radica en los procesos de presurización que utilizan. CIP aplica presión isostática a materiales usando presión líquida, mientras que el prensado de moldes metálicos aplica solo presión uniaxial. Esta diferencia da como resultado la producción de productos con diferentes distribuciones de densidad.
Comparación de la distribución de densidad en productos moldeados por CIP y Metal Mould Pressing
CIP produce productos con una densidad y homogeneidad uniforme debido a la ausencia de fricciones con un molde metálico. Por otro lado, el prensado de moldes metálicos puede provocar variaciones en la distribución de densidad. La parte inferior de un cuerpo moldeado producido mediante prensado en molde metálico tiende a tener una densidad menor en comparación con su parte superior. Esto se debe a las fricciones entre el polvo y el molde metálico o el punzón, así como entre las partículas de polvo.
En resumen, tanto el CIP como el prensado de moldes metálicos son métodos de procesamiento de materiales utilizados en diversas industrias. Si bien comparten similitudes, como el uso de materiales en polvo y la compresión, difieren en sus procesos de presurización y la distribución de densidad resultante en los productos moldeados. CIP ofrece una densidad y homogeneidad uniformes, mientras que el prensado de moldes metálicos puede provocar variaciones de densidad.
Tipos de procesamiento CIP
Los métodos de moldeo CIP se clasifican en dos tipos; el proceso de bolsa húmeda y el proceso de bolsa seca, según la relación entre un molde formador para llenar polvo y un medio de presión para transmitir presión.
Proceso de bolsa húmeda
En el proceso de bolsa húmeda, como se muestra en la figura siguiente, el polvo se llena en un molde de formación y se sella herméticamente fuera del recipiente de alta presión antes de la inmersión directa en un medio de presión. Luego, se aplica presión isostática a las superficies exteriores del molde para comprimir el polvo y darle una forma. Este método es adecuado para diversos tipos de producción de pequeña calidad para productos de forma complicada o de gran escala y para investigaciones de producción de prueba.
Limitaciones:
- Tiempo del ciclo: 5-30 min para bolsa mojada
- Frío (temperatura ambiente)
- Densidad verde uniforme
- Más lento que el prensado uniaxial
- Formas complejas y sin cera
- Las piezas pueden requerir posmecanizado
Proceso de bolsa seca
En el proceso de bolsa seca, automatizado, una parte a la vez, el polvo se llena en un molde de formación y se sella herméticamente dentro del recipiente de alta presión. Luego, el medio de presión se introduce en el recipiente a presión y se aplica presión isostática a las superficies exteriores del molde para comprimir el polvo y darle una forma. Este método es adecuado para producir piezas de diferentes formas de forma rentable.
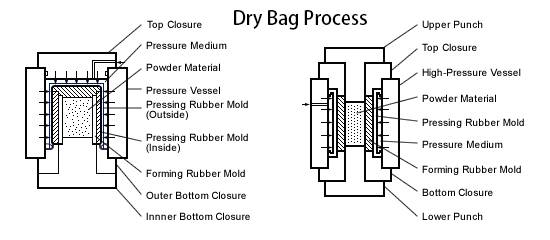
Limitaciones:
- Tiempo del ciclo: 3-5 min
- Cálido (100°C)
- Elimina la post-sinterización
- Caliente (2200°C)
- Mejora las propiedades mecánicas y físicas.
- Los tiempos de ciclo pueden ser lentos: 10-15 h
- Forma casi neta
- Densidad total
CIP con bolsa húmeda
A lo largo de los años han evolucionado dos tipos de métodos CIP: bolsa húmeda y bolsa seca. Para la producción de formas mixtas se utiliza el llamado método de bolsa húmeda. Se estima que hoy en día se utilizan más de 3.000 prensas de bolsa húmeda en todo el mundo, con tamaños que oscilan entre 50 y 2.000 mm de diámetro.
Aplicaciones del Proceso CIP
Como tecnología de procesamiento casi neta, CIP se utiliza normalmente en las siguientes aplicaciones:
- Las aplicaciones en las que el material es relativamente caro y, por lo tanto, se minimizan los residuos (por ejemplo, en forma de virutas de mecanizado) mediante el uso de un proceso de forma casi neta, ofrecerían una importante ventaja económica y medioambiental.
- Aplicaciones donde los materiales son difíciles de mecanizar y es más viable dar forma a la pieza mediante procesamiento de polvo.
- Aplicaciones donde la complejidad geométrica de la pieza requiere herramientas costosas (por ejemplo, recipientes de sacrificio en HIP). CIP utiliza herramientas flexibles reutilizables (o potencialmente desechables) relativamente económicas que permiten producir formas complejas.
- Aplicaciones donde se requiere uniformidad y homogeneidad de la microestructura para lograr un rendimiento mecánico específico. El procesamiento isostático de polvos ofrece una ventaja relativa sobre otros procesos, como el prensado uniaxial o la fundición.
- Aplicaciones donde se requieren múltiples materiales o estructuras graduadas. En algunas aplicaciones, las técnicas de unión tradicionales no son adecuadas, por lo que CIP ofrece un proceso de unión de estado sólido.
Aunque el proceso CIP se desarrolló hace muchos años, las aplicaciones comerciales de metales han sido relativamente limitadas. Las aplicaciones tradicionales se centraban en preformas y formas relativamente simples, como piezas tubulares o sólidas con relaciones de aspecto altas, como tuberías, accesorios de presión hidráulica y revestimientos de recipientes con paredes delgadas. Recientemente, se ha considerado el CIP para aplicaciones relativamente avanzadas en sectores de alto valor. Por ejemplo, las aplicaciones automotrices incluyen forjar preformas para bielas y componentes de aluminio del sistema de levas y fases del vehículo. Las aplicaciones aeroespaciales incluyen cámaras de empuje enfriadas regenerativamente. Las aplicaciones de generación de energía incluyen piezas de reactores de fisión, componentes estructurales de reactores nucleares y aleaciones ferríticas reforzadas con dispersión de óxido utilizadas para revestimientos de combustible o materiales estructurales en futuros sistemas nucleares. Las aplicaciones de defensa incluyen carcasas de ojivas de misiles. Se implementó CIP+HIP para fabricar carcasas de ojivas para misiles Stinger (con volúmenes de producción de hasta).
Segmentación del mercado
Según el tipo de producto, el mercado de equipos de prensado isostático en frío (CIP) se divide en:
- Prensado de bolsas mojadas
En el proceso de bolsa húmeda, el material en polvo se encierra en una bolsa de molde flexible, que se sumerge en un líquido a alta presión en un recipiente a presión. Luego, se aplica presión isostática a las superficies exteriores del molde para comprimir el polvo y darle una forma. Este proceso es ideal para la producción de múltiples formas y de pequeñas a grandes cantidades, y para el prensado de productos grandes.
Tanto el proceso CIP como el HIP utilizan construcciones de múltiples materiales: carcasas de polímero con polvos cerámicos en CIP y carcasa de material de lámina de acero dulce soldada con aleaciones de pulvimetalurgia de alta gama en HIP. Por lo tanto, ambos métodos presentan una oportunidad para el preprocesamiento de construcciones en un solo paso mediante la fabricación aditiva de múltiples materiales. Este enfoque podría ser particularmente beneficioso para producir series pequeñas o prototipos, e incluso podría reducir los costos de fabricación al permitir una mayor complejidad de las piezas con menos pasos y tiempo de procesamiento.
Detalles del proceso de bolsa húmeda
Explicación del proceso de bolsa húmeda
La tecnología de bolsa húmeda es un método que se utiliza para moldear polvo llenándolo en un molde y sellándolo herméticamente. Luego, el molde se sumerge en un fluido a presión dentro de un recipiente a presión. Se aplica presión isostática a la superficie externa del molde, comprimiendo el polvo hasta convertirlo en una masa sólida. Este proceso es adecuado para la producción de múltiples formas y de pequeñas a grandes cantidades.
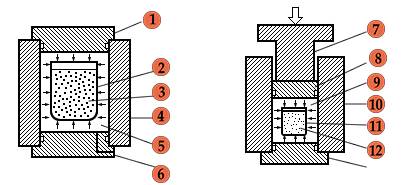
El proceso de bolsa húmeda no es tan común como el proceso de bolsa seca, pero todavía se usa ampliamente. Hoy en día se utilizan más de 3.000 prensas de bolsas húmedas en todo el mundo, con tamaños que van desde 50 mm hasta 2.000 mm de diámetro. Las bombas de gran volumen y los mecanismos de carga mejorados pueden ayudar a acelerar el proceso, que normalmente tarda entre 5 y 30 minutos en completarse.
Idoneidad del proceso de bolsa húmeda para varios tipos de producción
El proceso de bolsa húmeda es adecuado para varios tipos de producción, especialmente para productos de formas complicadas o de gran escala e investigaciones de producción de prueba. Permite la producción de productos con formas complejas que pueden ser difíciles de lograr con otros métodos. Este proceso también es adecuado para la producción en pequeñas cantidades y también puede utilizarse para la producción en masa.
Tipos estructurales de proceso de bolsa húmeda: tipo de presurización externa y tipo de presurización directa de pistón
Hay dos tipos estructurales del proceso de bolsa húmeda: el tipo de presurización externa y el tipo de presurización directa de pistón.
El tipo de presurización externa implica presurizar el medio a presión en el recipiente a presión desde el exterior. El medio de presión se aplica externamente al molde, comprimiendo el polvo en su interior.
El tipo de presurización directa de pistón, por otro lado, presuriza directamente el medio de presión sellado dentro del recipiente de alta presión con un pistón instalado en lugar del cierre superior. Este tipo de proceso de bolsa húmeda elimina la necesidad de presurización externa, lo que lo hace más eficiente.
En general, el proceso de bolsa húmeda ofrece un método único para moldear polvo y es adecuado para varios tipos de producción. Permite la producción de productos de formas complejas y se puede utilizar tanto para producción en pequeña cantidad como en masa. Los dos tipos estructurales del proceso de bolsa húmeda brindan flexibilidad y eficiencia en el proceso de moldeo.
Detalles del proceso de bolsa seca
Explicación del proceso de bolsa seca
El proceso de bolsa seca es un método para moldear polvo llenado en un molde de caucho de formación transmitiendo presión a través de un molde de caucho de presión en el recipiente de alta presión. Este método es adecuado para la producción en masa de una variedad simple y limitada de productos gracias a su operación automática que ahorra mano de obra.
Idoneidad del proceso de bolsa seca para la producción en masa
El prensado de bolsa seca se diferencia del de bolsa húmeda en que se incorpora una membrana flexible al recipiente a presión y se utiliza durante todos los ciclos de prensado. Esta membrana aísla el fluido a presión del molde, que se convierte en una "bolsa seca". Este proceso es mucho más limpio debido a que el molde flexible no se contamina con polvo húmedo. Además, se necesita menos limpieza del recipiente. Este método tiene ciclos rápidos y es ideal para la producción en masa automatizada de productos en polvo.
Clasificación de los sistemas Dry Bag Process: sistema de presurización circunferencial + axial y sistema de presurización circunferencial
El proceso Dry Bag se clasifica en dos sistemas: el sistema de presurización circunferencial + axial y el sistema de presurización circunferencial. El sistema de presurización circunferencial + axial implica presurizar el medio de presión en el recipiente de presión desde el exterior, mientras que el sistema de presurización circunferencial presuriza directamente el medio de presión sellado dentro del recipiente de alta presión con un pistón instalado en lugar del cierre superior.
La tecnología Dry Bag es ideal para la producción masiva de materiales. Este proceso suele tardar tan solo 1 minuto, lo que lo hace mucho más rápido que la tecnología de bolsa húmeda.
Si está interesado en nuestros productos, visite el sitio web de nuestra empresa: https://kindle-tech.com/product-categories/isostatic-press , donde la innovación siempre ha sido una prioridad. Nuestro equipo de I+D está formado por ingenieros y científicos experimentados que siguen de cerca las tendencias de la industria y están constantemente superando los límites de lo posible. Nuestro equipo de laboratorio incorpora la última tecnología para garantizar que pueda obtener resultados precisos y repetibles durante sus experimentos. Desde instrumentos de alta precisión hasta sistemas de control inteligentes, nuestros productos le brindarán posibilidades ilimitadas para su trabajo experimental.
CONTÁCTANOS PARA UNA CONSULTA GRATUITA
Los productos y servicios de KINTEK LAB SOLUTION han sido reconocidos por clientes de todo el mundo. Nuestro personal estará encantado de ayudarle con cualquier consulta que pueda tener. ¡Contáctenos para una consulta gratuita y hable con un especialista del producto para encontrar la solución más adecuada para sus necesidades de aplicación!