Una forja de inducción, también conocida como horno de inducción, funciona según el principio de inducción electromagnética para calentar y fundir metales.Funciona convirtiendo la energía eléctrica en energía calorífica sin contacto directo entre el elemento calefactor (bobina de inducción) y el metal.El proceso consiste en generar una corriente alterna (CA) de alta frecuencia que fluye a través de una bobina de cobre, creando un campo magnético que se invierte rápidamente.Este campo magnético induce corrientes de Foucault dentro del metal conductor, generando calor por resistencia (calentamiento Joule).En los materiales ferromagnéticos, se produce calor adicional por histéresis magnética.El sistema es eficaz, preciso y capaz de fundir una amplia gama de metales, como acero, cobre y aluminio, manteniendo su compacidad y eficiencia energética.
Explicación de los puntos clave:
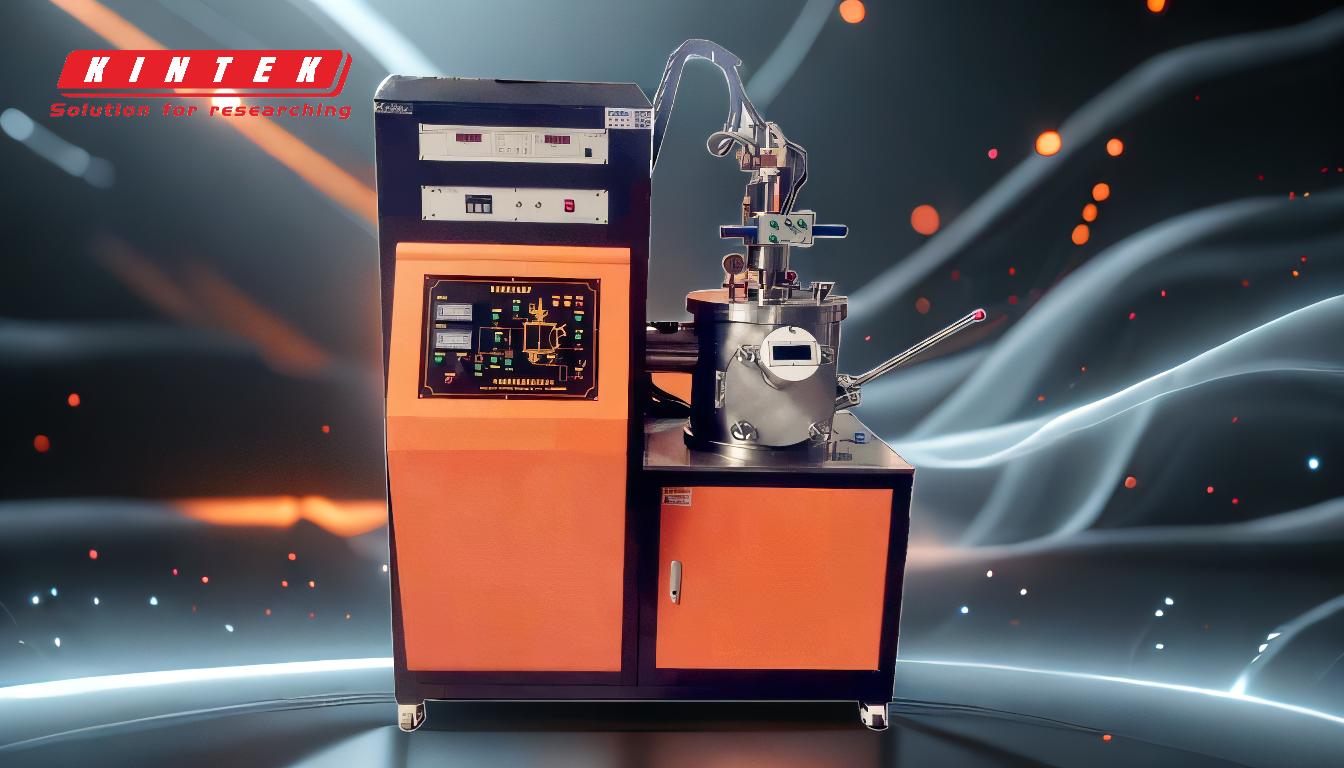
-
Inducción electromagnética:
- El principio básico de una forja de inducción es la inducción electromagnética.Cuando una corriente alterna circula por la bobina de inducción, crea un campo magnético que cambia rápidamente.
- Este campo magnético penetra en el metal colocado dentro de la bobina, induciendo corrientes de Foucault dentro del metal debido a la ley de inducción de Faraday.
-
Corrientes de Foucault y calentamiento Joule:
- Las corrientes inducidas fluyen a través del metal, encontrando resistencia.Según la ley de Joule, esta resistencia convierte la energía eléctrica en energía térmica, aumentando la temperatura del metal.
- El calor generado es proporcional al cuadrado de la corriente y la resistencia del metal, lo que garantiza un calentamiento eficaz.
-
Histéresis magnética (para materiales ferromagnéticos):
- En los materiales ferromagnéticos como el hierro, se produce un calentamiento adicional debido a la histéresis magnética.El campo magnético alterno hace que los dominios magnéticos del material se realineen continuamente, generando calor como subproducto.
- Este efecto es más pronunciado a bajas frecuencias y disminuye a medida que el material alcanza su temperatura de Curie.
-
Conversión de frecuencias:
- Las forjas de inducción suelen funcionar a frecuencias medias (de 300 Hz a 1.000 Hz).La fuente de alimentación convierte la corriente alterna estándar de 50 Hz o 60 Hz en esta gama de frecuencias más altas.
- Esta conversión implica rectificar la CA en corriente continua (CC) e invertirla de nuevo en CA de frecuencia media ajustable mediante un circuito inversor.
-
Bobina de inducción y campo magnético:
- La bobina de inducción, generalmente de cobre, es un componente esencial.Transporta la corriente alterna de alta frecuencia y genera el campo magnético necesario para el calentamiento por inducción.
- La bobina suele estar refrigerada por agua para evitar el sobrecalentamiento y mantener la eficacia durante un funcionamiento prolongado.
-
Calentamiento sin contacto:
- A diferencia de los hornos tradicionales, las forjas de inducción no requieren contacto directo entre la fuente de calor y el metal.Esto elimina la contaminación y permite un control preciso de la temperatura.
- La naturaleza sin contacto también reduce el desgaste del equipo, alargando su vida útil.
-
Crisol y carga metálica:
- El metal a fundir se coloca dentro de un crisol no conductor, que está rodeado por la bobina de inducción.
- El material del crisol debe soportar altas temperaturas y no interferir en el proceso electromagnético.
-
Aplicaciones y ventajas:
- Las forjas de inducción se utilizan ampliamente para fundir acero al carbono, aceros aleados, aceros especiales y metales no férreos como cobre, aluminio, plomo y zinc.
- Son compactas, ligeras, energéticamente eficientes y capaces de fundir rápidamente con un control preciso de la temperatura, lo que las hace ideales para aplicaciones industriales y a pequeña escala.
-
Eficiencia energética y productividad:
- Las forjas de inducción son muy eficientes energéticamente porque calientan directamente el metal, minimizando la pérdida de calor al entorno.
- El rápido proceso de calentamiento y fusión aumenta la productividad, por lo que son adecuadas para operaciones de gran volumen.
-
Ventajas para la seguridad y el medio ambiente:
- La ausencia de llamas o gases de combustión reduce el riesgo de accidentes y la contaminación ambiental.
- El diseño cerrado del horno también minimiza la exposición a humos y partículas nocivas.
Al aprovechar estos principios, las forjas de inducción proporcionan un método limpio, eficaz y preciso para calentar y fundir metales, lo que las hace indispensables en la metalurgia y los procesos de fabricación modernos.
Cuadro sinóptico:
Aspecto clave | Detalles |
---|---|
Principio | La inducción electromagnética genera calor mediante corrientes parásitas e histéresis. |
Método de calentamiento | Calentamiento sin contacto mediante bobina de inducción, eliminando la contaminación. |
Gama de frecuencias | Frecuencia media (300 Hz a 1000 Hz) para un calentamiento eficaz. |
Materiales calentados | Acero, cobre, aluminio, plomo, zinc y otros metales. |
Ventajas | Compacta, de bajo consumo, fusión rápida, control preciso de la temperatura. |
Aplicaciones | Fundición de metales industrial y a pequeña escala, operaciones de gran volumen. |
Ventajas de seguridad | Sin llamas, menor contaminación ambiental, diseño cerrado. |
Descubra cómo una forja de inducción puede revolucionar su proceso metalúrgico. contacte con nosotros para obtener más información.