La producción de hierro en un horno de inducción consiste en utilizar la inducción electromagnética para fundir cargas metálicas, como chatarra o arrabio, y convertirlas en líquido.El proceso comienza con la carga de materias primas en el horno, seguido de su calentamiento a altas temperaturas (alrededor de 1650°C) mediante una bobina de inducción alimentada por electricidad.Una vez fundido, el metal se introduce en una cuchara para su posterior refinado o fundición.Este método es eficaz, ahorra energía y es respetuoso con el medio ambiente en comparación con los altos hornos tradicionales.A continuación, el proceso se desglosa en pasos clave y se explica en detalle.
Explicación de los puntos clave:
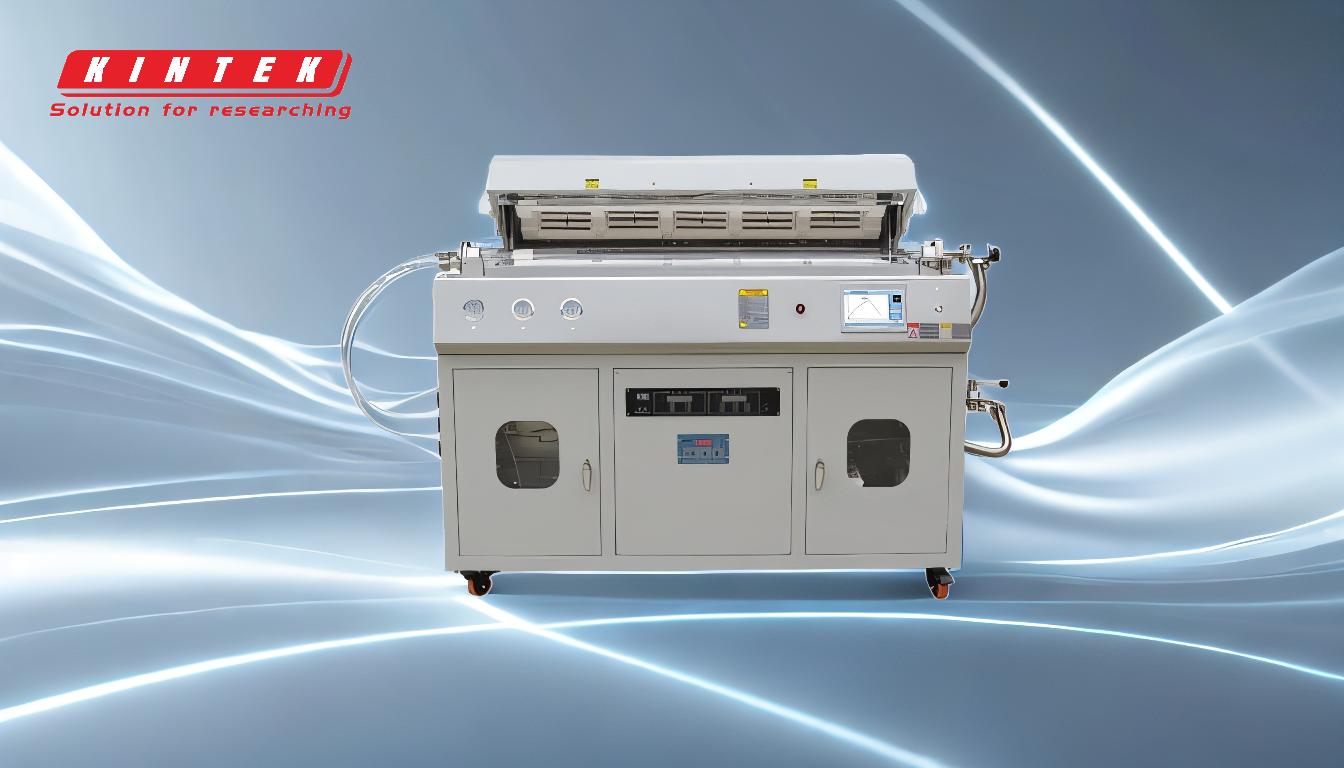
-
Introducción a los hornos de inducción:
- Los hornos de inducción se utilizan mucho en la producción de acero y hierro por su eficacia y precisión.Se basan en la inducción electromagnética para generar calor dentro de la carga metálica, lo que los hace idóneos para fundir y refinar hierro y acero.
- El horno suele constar de un crisol rodeado por una bobina de inducción, alimentada por un horno de inducción IGBT .La tecnología IGBT (transistor bipolar de puerta aislada) garantiza un control preciso del proceso de calentamiento, por lo que resulta ideal para la fabricación moderna de acero.
-
Carga del horno:
- El proceso comienza con la carga del horno con materias primas, que pueden ser chatarra, arrabio u otros materiales que contengan hierro.Estos materiales se seleccionan cuidadosamente en función de la composición deseada del producto final.
- La carga se carga en el crisol, que está diseñado para soportar altas temperaturas y reacciones químicas durante el proceso de fusión.
-
Proceso de fusión:
- Una vez cargado el horno, se activa la bobina de inducción, que genera un campo magnético alterno de alta frecuencia.Este campo induce corrientes de Foucault dentro de la carga metálica, provocando su calentamiento y, finalmente, su fusión.
- La temperatura en el interior del horno puede alcanzar los 1.650 °C, suficiente para fundir el hierro y otros elementos de aleación.El uso de un horno de inducción horno de inducción IGBT garantiza una transferencia de energía eficaz y un control preciso de la temperatura.
-
Refinado y aleación:
- Durante el proceso de fusión, impurezas como el azufre y el fósforo se eliminan mediante reacciones químicas.Pueden añadirse fundentes como piedra caliza o dolomita para facilitar la formación de escoria, que captura las impurezas y flota en la superficie.
- Pueden añadirse elementos de aleación, como carbono, manganeso o cromo, para lograr la composición deseada de acero o hierro.El horno de inducción permite controlar con precisión el proceso de aleación, garantizando una calidad constante.
-
Roscado y fundición:
- Una vez que el hierro fundido alcanza la temperatura y composición deseadas, se extrae del horno y se vierte en una cuchara de acero.Este proceso consiste en inclinar el horno o abrir un orificio para verter el metal fundido.
- A continuación, la cuchara se transporta a la siguiente fase de producción, que puede incluir la colada continua, la colada de lingotes o el refinado posterior en procesos de metalurgia secundaria.
-
Ventajas de los hornos de inducción:
-
Los hornos de inducción ofrecen varias ventajas con respecto a los altos hornos tradicionales, entre ellas
- Eficiencia energética:El calentamiento directo de la carga reduce las pérdidas de energía.
- Precisión:El uso de horno de inducción IGBT permite un control preciso de la temperatura y la composición.
- Beneficios medioambientales:Los hornos de inducción producen menos emisiones que los altos hornos, por lo que son más respetuosos con el medio ambiente.
- Flexibilidad:Pueden manipular una amplia gama de materias primas y producir diversos grados de acero y hierro.
-
Los hornos de inducción ofrecen varias ventajas con respecto a los altos hornos tradicionales, entre ellas
-
Aplicaciones en la fabricación moderna de acero:
- Los hornos de inducción se utilizan habitualmente en la producción de acero a pequeña y mediana escala, así como en fundiciones para moldear componentes de hierro y acero.Su capacidad para producir metal de alta calidad con un impacto medioambiental mínimo los convierte en la opción preferida en la fabricación moderna.
Siguiendo estos pasos, el hierro se produce eficientemente en un horno de inducción, aprovechando tecnologías avanzadas como Horno de inducción IGBT para garantizar una producción de alta calidad.Este método no sólo es rentable, sino que también se ajusta a las prácticas de fabricación sostenibles.
Cuadro sinóptico:
Paso | Descripción |
---|---|
1.Carga | Las materias primas (chatarra, arrabio) se cargan en el crisol. |
2.Fusión | La bobina de inducción genera calor, fundiendo la carga hasta 1650°C. |
3.Refinado | Se eliminan las impurezas y se añaden elementos de aleación para obtener la composición deseada. |
4.Roscado y colada | El hierro fundido se vierte en una cuchara para su posterior refinado o fundición. |
5.Ventajas | Eficientes energéticamente, precisos, ecológicos y flexibles para diversas aplicaciones. |
Descubra cómo los hornos de inducción pueden revolucionar su producción de metal. póngase en contacto con nosotros para recibir asesoramiento experto.