El revestimiento por deposición física de vapor (PVD) es una tecnología de tratamiento de superficies versátil y avanzada con una amplia gama de aplicaciones en diversos sectores.Se utiliza principalmente para mejorar la durabilidad, la resistencia al desgaste y la resistencia a la corrosión de herramientas, maquinaria y componentes.Además, los revestimientos PVD se valoran por su atractivo estético, su seguridad medioambiental y su capacidad para trabajar con diversos materiales, como metales, cerámica y materiales compuestos.Los sectores clave que se benefician de los revestimientos PVD son el aeroespacial, la automoción, la fabricación de semiconductores, las telecomunicaciones y la iluminación.También se prefiere esta tecnología por su precisión y respeto al medio ambiente en comparación con los métodos tradicionales de revestimiento basados en productos químicos.
Explicación de los puntos clave:
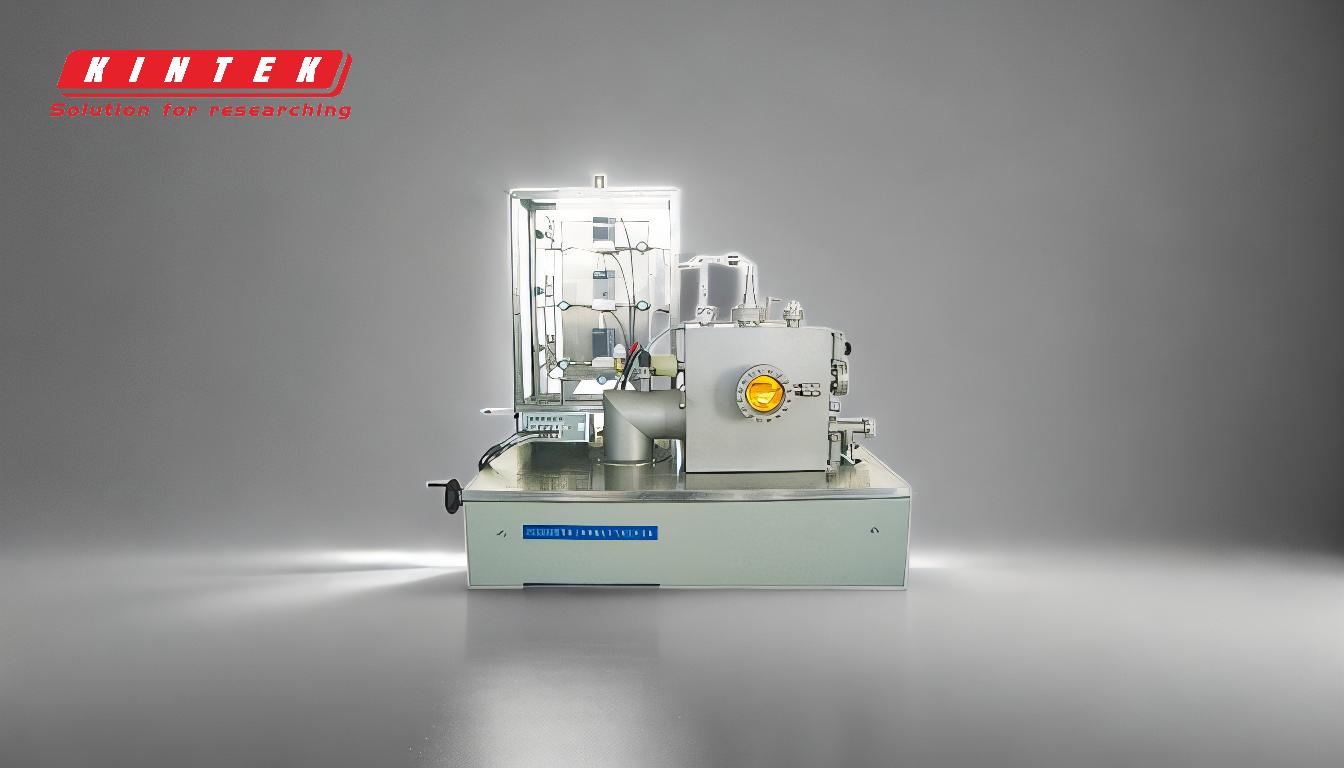
-
Resistencia a la corrosión y al desgaste en los sectores aeroespacial y de automoción
- Los revestimientos PVD se utilizan ampliamente en los sectores aeroespacial y de automoción para proteger las piezas metálicas del desgaste y la corrosión.
- Los revestimientos mejoran la vida útil y el rendimiento de componentes de motores, herramientas de corte y otras piezas sometidas a grandes esfuerzos.
- Materiales como el grafito, el titanio y revestimientos especializados como carburos y nitruros se utilizan habitualmente para aplicaciones de alto rendimiento.
-
Aplicaciones estéticas en automoción y telecomunicaciones
- Los revestimientos de PVD proporcionan colores y acabados vibrantes, lo que los hace ideales para mejorar el atractivo visual de interiores de automóviles, embellecedores de motocicletas y productos electrónicos de consumo.
- La posibilidad de incorporar metales preciosos o materiales similares permite crear diseños personalizables de gama alta.
-
Fabricación de semiconductores
- En la producción de semiconductores, se utilizan técnicas de PVD como el sputtering para depositar películas finas de metales como platino, tungsteno y cobre en microchips.
- Esta tecnología también se emplea en la creación de células fotovoltaicas de película fina, en las que materiales como el cobre, el indio, el galio y el telurio se recubren sobre sustratos de vidrio o plástico.
-
Aplicaciones de iluminación
- Los revestimientos de PVD se utilizan en iluminación con fines tanto estéticos como funcionales.
- Permiten una personalización precisa del color y mejoran la durabilidad de los dispositivos de iluminación, haciéndolos resistentes a las condiciones ambientales.
-
Ventajas medioambientales y de seguridad
- El revestimiento PVD es más seguro y respetuoso con el medio ambiente que los métodos basados en productos químicos, ya que reduce la necesidad de sustancias tóxicas y minimiza los residuos.
- La aplicación a escala molecular garantiza un acabado superior con un impacto medioambiental mínimo.
-
Versatilidad en todos los sectores
- Los revestimientos PVD pueden aplicarse a casi cualquier material inorgánico, por lo que son adecuados para una amplia gama de sectores, como defensa, construcción y herramientas de corte.
- La capacidad de esta tecnología para reducir la fricción y mejorar la durabilidad la convierte en la opción preferida para aplicaciones de alto rendimiento.
En resumen, el revestimiento PVD es una tecnología muy adaptable y eficaz que ofrece importantes ventajas en términos de durabilidad, estética y sostenibilidad medioambiental.Sus aplicaciones se extienden a industrias críticas, lo que la convierte en una herramienta indispensable para la fabricación y el diseño modernos.
Cuadro sinóptico:
Industria | Aplicaciones | Beneficios clave |
---|---|---|
Aeroespacial y automoción | Resistencia a la corrosión y al desgaste para componentes de motores, herramientas de corte y piezas | Vida útil mejorada, materiales de alto rendimiento como el titanio y los carburos |
Automoción y electrónica | Acabados estéticos para interiores, embellecedores y electrónica de consumo | Colores vibrantes, diseños personalizables con metales preciosos |
Fabricación de semiconductores | Deposición de película fina para microchips y células fotovoltaicas | Recubrimiento de precisión con metales como platino, tungsteno y cobre |
Iluminación | Revestimientos estéticos y funcionales para dispositivos de iluminación | Personalización del color, durabilidad en entornos difíciles |
Medio ambiente y seguridad | Alternativa ecológica a los revestimientos de base química | Reducción de sustancias tóxicas, residuos mínimos, acabado superior |
Versatilidad | Aplicable a metales, cerámicas y materiales compuestos en todas las industrias | Mayor durabilidad, menor fricción y aplicaciones de alto rendimiento |
Libere el potencial del recubrimiento PVD para su industria-. póngase en contacto con nuestros expertos para obtener más información.