El recubrimiento por deposición física de vapor (PVD) es una técnica versátil y muy utilizada para aplicar películas finas a diversos sustratos.El proceso consiste en vaporizar un material sólido en un entorno de vacío y depositarlo sobre un sustrato para formar un revestimiento fino y duradero.Existen varios tipos de revestimientos y procesos PVD, cada uno con características y ventajas únicas, que los hacen adecuados para diferentes aplicaciones y materiales.
Explicación de los puntos clave:
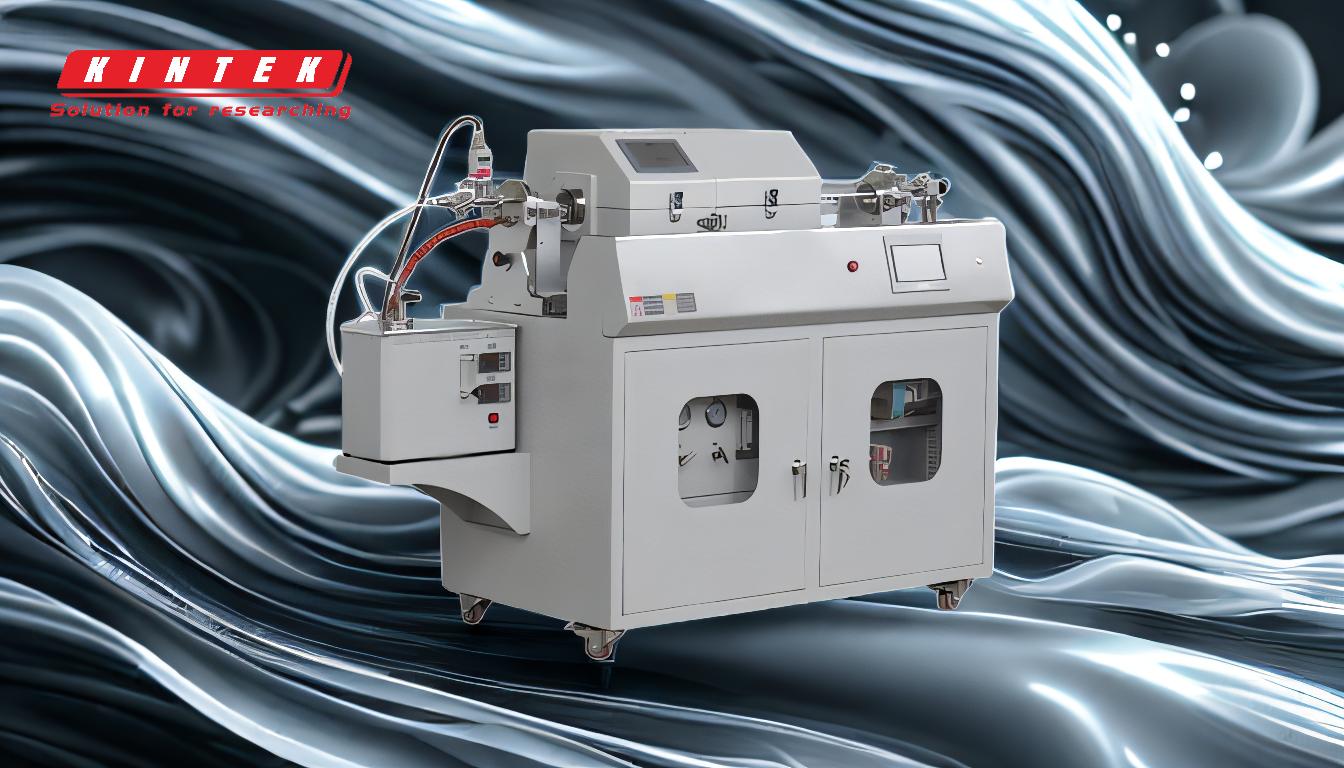
-
Tipos de recubrimientos PVD:
- Nitruro de titanio (TiN): Conocido por su color dorado, el TiN se utiliza ampliamente por su dureza, resistencia al desgaste y propiedades de baja fricción.Se suele aplicar a herramientas de corte, moldes y dispositivos médicos.
- Nitruro de cromo (CrN): Los revestimientos de CrN ofrecen una excelente resistencia a la corrosión, estabilidad a altas temperaturas y baja fricción.Suelen utilizarse en aplicaciones que requieren gran resistencia al desgaste y protección contra la corrosión, como en las industrias automovilística y aeroespacial.
- Nitruro de titanio y aluminio (TiAlN): Este recubrimiento es conocido por su alta resistencia a la oxidación y dureza, por lo que es ideal para el mecanizado de alta velocidad y herramientas de corte.
- Nitruro de titanio y boro (TiBN): Los revestimientos de TiBN combinan las propiedades del TiN y el nitruro de boro, ofreciendo alta dureza, baja fricción y excelente resistencia al desgaste.Se utilizan en aplicaciones que requieren una durabilidad y un rendimiento extremos.
-
Procesos de recubrimiento PVD:
- Deposición por arco catódico: Este proceso implica la creación de un arco entre un cátodo (material objetivo) y un ánodo, que vaporiza el material objetivo.A continuación, el material vaporizado se condensa en el sustrato.Este método es conocido por producir revestimientos densos y de alta calidad con una excelente adherencia.
- Deposición física en fase vapor por haz de electrones (EB-PVD): En este proceso, se utiliza un haz de electrones para vaporizar el material objetivo.A continuación, el material vaporizado se deposita sobre el sustrato.El EB-PVD es conocido por su capacidad para producir revestimientos de gran pureza y se utiliza a menudo en la industria aeroespacial para revestimientos de barrera térmica.
- Deposición evaporativa: Este método consiste en calentar el material objetivo hasta que se evapora.A continuación, el material vaporizado se condensa en el sustrato.La deposición evaporativa se utiliza habitualmente para recubrir componentes ópticos y dispositivos electrónicos.
- Deposición por láser pulsado (PLD): La PLD utiliza un láser de alta potencia para vaporizar el material objetivo.A continuación, el material vaporizado se deposita sobre el sustrato.Este método es conocido por su capacidad para producir revestimientos complejos de varias capas con un control preciso del grosor y la composición.
- Deposición por pulverización catódica: En este proceso, se utilizan iones para bombardear el material objetivo, provocando la expulsión de átomos que se depositan sobre el sustrato.La deposición por pulverización catódica se utiliza ampliamente para producir películas finas con excelente uniformidad y adherencia.Se utiliza habitualmente en las industrias óptica y de semiconductores.
-
Técnicas comunes de recubrimiento PVD:
- Evaporación térmica: Esta técnica consiste en calentar el material objetivo hasta que se evapora.A continuación, el material vaporizado se deposita sobre el sustrato.La evaporación térmica se utiliza habitualmente para el revestimiento de metales y aleaciones.
- Recubrimiento por pulverización catódica: El revestimiento por pulverización catódica consiste en bombardear el material objetivo con iones, lo que provoca la expulsión de átomos que se depositan sobre el sustrato.Esta técnica es conocida por producir revestimientos uniformes de alta calidad y se utiliza mucho en las industrias electrónica y óptica.
- Metalizado iónico: El metalizado iónico combina las técnicas de evaporación y pulverización catódica.El material objetivo se vaporiza y se utilizan iones para mejorar el proceso de deposición, lo que da lugar a revestimientos densos y adherentes.Esta técnica suele utilizarse para recubrir herramientas y componentes que requieren una gran resistencia al desgaste.
- Ablación por láser: En esta técnica se utiliza un láser de alta potencia para vaporizar el material objetivo.A continuación, el material vaporizado se deposita sobre el sustrato.La ablación por láser es conocida por su capacidad para producir revestimientos complejos de alta calidad con un control preciso del grosor y la composición.
-
Aplicaciones de los recubrimientos PVD:
- Herramientas de corte: Los revestimientos de PVD se utilizan ampliamente para mejorar el rendimiento y la vida útil de las herramientas de corte, ya que proporcionan resistencia al desgaste, baja fricción y alta dureza.
- Dispositivos médicos: Los revestimientos de PVD se aplican a dispositivos médicos para mejorar la biocompatibilidad, la resistencia a la corrosión y la resistencia al desgaste.
- Componentes de automoción: Los revestimientos de PVD se utilizan en la industria del automóvil para mejorar el rendimiento y la durabilidad de los componentes del motor, las piezas de la transmisión y otros componentes críticos.
- Componentes aeroespaciales: Los revestimientos PVD se utilizan en la industria aeroespacial para revestimientos de barrera térmica, revestimientos resistentes al desgaste y revestimientos resistentes a la corrosión en álabes de turbinas, componentes de motores y otras piezas críticas.
- Componentes ópticos: Los revestimientos PVD se utilizan para mejorar el rendimiento de los componentes ópticos mediante revestimientos antirreflectantes, antirrayado y protectores.
En resumen, el revestimiento PVD ofrece una amplia gama de opciones tanto en términos de tipos de revestimientos como de procesos utilizados para aplicarlos.Cada tipo de revestimiento y proceso tiene características y ventajas únicas, lo que los hace adecuados para diferentes aplicaciones y materiales.Comprender los requisitos específicos de su aplicación le ayudará a elegir la opción de revestimiento PVD más adecuada.
Tabla resumen:
Aspecto | Detalles |
---|---|
Tipos de recubrimientos PVD | - Nitruro de titanio (TiN): Dureza, resistencia al desgaste, baja fricción. |
- Nitruro de cromo (CrN):Resistencia a la corrosión, estabilidad a altas temperaturas. | |
- Nitruro de titanio y aluminio (TiAlN): Alta resistencia a la oxidación, dureza. | |
- Nitruro de titanio y boro (TiBN): Alta dureza, baja fricción, resistencia al desgaste. | |
Procesos de revestimiento PVD | - Deposición por arco catódico:Recubrimientos densos y de alta calidad. |
- PVD por haz de electrones (EB-PVD):Recubrimientos de alta pureza, aplicaciones aeroespaciales. | |
- Deposición evaporativa:Recubrimientos ópticos y electrónicos. | |
- Deposición por láser pulsado (PLD):Recubrimientos complejos multicapa. | |
- Deposición por pulverización catódica:Películas finas uniformes y adherentes. | |
Aplicaciones | - Herramientas de corte:Mayor resistencia al desgaste y vida útil. |
- Dispositivos médicos:Biocompatibilidad y resistencia a la corrosión mejoradas. | |
- Automoción:Componentes duraderos de motores y transmisiones. | |
- Aeroespacial:Recubrimientos de barrera térmica y resistentes al desgaste. | |
- Componentes ópticos:Revestimientos antirreflectantes y protectores. |
Descubra cómo los recubrimientos PVD pueden optimizar sus aplicaciones. póngase en contacto con nosotros para recibir asesoramiento experto.