El sinterizado por láser, en particular el sinterizado selectivo por láser (SLS), es una técnica versátil de fabricación aditiva que ofrece ventajas y desventajas únicas.Es capaz de producir formas muy complejas y funcionales, difíciles de conseguir con los métodos de sinterización tradicionales.Sin embargo, conlleva costes considerables, tanto en equipos como en materiales, y requiere operarios cualificados.Por otro lado, métodos alternativos como la pulvimetalurgia son más rentables para la producción a gran escala, pero pueden dar lugar a componentes no uniformes.La sinterización a alta velocidad ha demostrado ser prometedora para mejorar la densidad y la resistencia, pero no cuenta con el respaldo universal, lo que indica posibles limitaciones.
Explicación de los puntos clave:
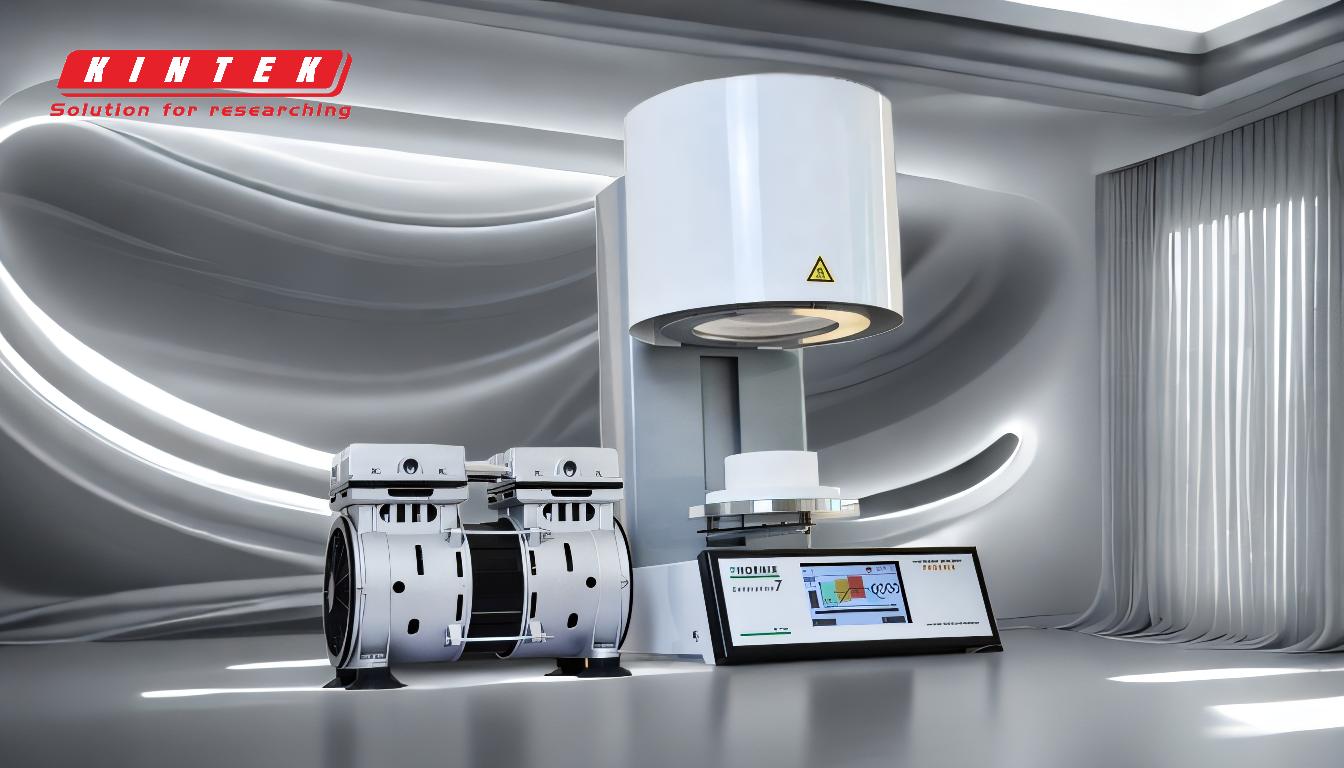
-
Ventajas del Sinterizado Láser:
- Formas complejas y funcionales: El sinterizado láser, especialmente el SLS, destaca en la creación de geometrías intrincadas y funcionales que son difíciles o imposibles de conseguir con los métodos de sinterizado tradicionales.Esto lo hace ideal para aplicaciones que requieren gran precisión y complejidad, como los dispositivos aeroespaciales o médicos.
- Versatilidad de materiales: El SLS puede trabajar con una amplia gama de materiales, incluidos polímeros, metales y cerámicas, lo que permite diversas aplicaciones en todos los sectores.
- Procesamiento posterior mínimo: Las piezas producidas mediante SLS suelen requerir menos postprocesado en comparación con otros métodos de fabricación aditiva, ya que el proceso produce inherentemente componentes de forma casi neta.
-
Desventajas del sinterizado láser:
- Costes elevados: La inversión inicial de las máquinas de SLS es considerable, superando a menudo los 250.000 dólares.Además, los materiales utilizados en SLS son caros, lo que aumenta aún más el coste global.
- Operadores cualificados: El SLS requiere operadores con conocimientos y formación especializados, lo que aumenta los costes operativos y la complejidad.
- Escalabilidad limitada: Aunque el SLS es excelente para la creación de prototipos y la producción a pequeña escala, es menos eficiente para la fabricación a gran escala en comparación con métodos como la pulvimetalurgia.
-
Comparación con la pulvimetalurgia:
- Rentabilidad: La pulvimetalurgia suele ser más asequible, tanto en términos de equipos como de materiales, lo que la hace más adecuada para la producción a gran escala.
- Facilidad de manejo: A diferencia del SLS, la pulvimetalurgia no requiere operarios altamente cualificados, lo que reduce los costes de mano de obra y los requisitos de formación.
- Problemas de uniformidad: Uno de los inconvenientes de la pulvimetalurgia es la posibilidad de que los componentes no sean uniformes debido a la fricción entre el polvo y el utillaje, lo que puede afectar a la calidad y consistencia del producto final.
-
Sinterización a alta velocidad:
- Mayor densidad y resistencia: Algunos estudios sugieren que el sinterizado de alta velocidad puede producir piezas con una densidad y resistencia ligeramente superiores en comparación con los métodos de sinterizado tradicionales.
- Respaldo limitado: A pesar de estas ventajas, no todos los proveedores de materiales, en particular los de circonio, respaldan la sinterización a alta velocidad.Esto puede deberse a problemas de compatibilidad de materiales, estabilidad del proceso u otras limitaciones técnicas.
-
Consideraciones para los compradores de equipos y consumibles:
- Requisitos de la aplicación: Al decidir entre SLS y otros métodos de sinterización, los compradores deben tener en cuenta los requisitos específicos de su aplicación, como la necesidad de geometrías complejas, las propiedades del material y el volumen de producción.
- Limitaciones presupuestarias: Los elevados costes asociados al SLS pueden ser un factor limitante para algunas organizaciones, especialmente las que tienen presupuestos limitados o las que requieren una producción a gran escala.
- Experiencia de los operarios: La necesidad de operadores cualificados debe tenerse en cuenta en el proceso de toma de decisiones, ya que puede afectar tanto a la configuración inicial como a los costes operativos continuos.
- Compatibilidad de materiales: Para aquellos que estén considerando el sinterizado de alta velocidad, es esencial verificar la compatibilidad de los materiales y consultar con los proveedores para asegurarse de que el método es adecuado para la aplicación prevista.
En resumen, el sinterizado láser, en particular el SLS, ofrece importantes ventajas en cuanto a flexibilidad de diseño y versatilidad de materiales, pero conlleva costes elevados y complejidades operativas.Los métodos alternativos, como la pulvimetalurgia, son más rentables para la producción a gran escala, pero pueden comprometer la uniformidad de los componentes.La sinterización a alta velocidad tiene potencial para mejorar las propiedades de los materiales, pero no goza de aceptación universal, lo que indica la necesidad de estudiar detenidamente sus limitaciones.Los compradores deben sopesar estos factores con sus necesidades y limitaciones específicas para tomar una decisión informada.
Cuadro sinóptico:
Aspecto | Sinterizado láser (SLS) | Metalurgia de polvos | Sinterización a alta velocidad |
---|---|---|---|
Formas complejas | Sobresale en la creación de geometrías intrincadas y funcionales | Capacidad limitada para producir formas complejas | Datos disponibles limitados |
Versatilidad de materiales | Funciona con polímeros, metales y cerámica | Opciones de materiales limitadas | Posibles problemas de compatibilidad con materiales como el óxido de circonio |
Coste | Inversión inicial elevada (>250.000 dólares) y materiales caros | Más rentable para la producción a gran escala | Los costes varían; no están universalmente aceptados |
Habilidad del operador | Requiere operarios altamente cualificados | Más fácil de manejar; requiere menos mano de obra cualificada | Requiere conocimientos especializados |
Escalabilidad | Ideal para prototipos y producción a pequeña escala | Adecuado para la producción a gran escala | Escalabilidad limitada debido a limitaciones técnicas |
Tratamiento posterior | Postprocesamiento mínimo | Puede requerir más tratamiento posterior | Postprocesamiento mínimo |
Uniformidad de los componentes | Alta precisión y consistencia | Posibilidad de componentes no uniformes | Mayor densidad y resistencia, pero respaldo limitado |
¿Necesita ayuda para elegir el método de sinterización adecuado para su aplicación? Póngase en contacto con nuestros expertos para un asesoramiento personalizado.