La evaporación y el sputtering son técnicas de deposición física de vapor (PVD) que se utilizan para crear películas finas sobre sustratos, pero difieren fundamentalmente en sus mecanismos, condiciones operativas y aplicaciones.La evaporación se basa en calentar un material hasta que se vaporiza, mientras que el sputtering utiliza iones energéticos para desprender átomos de un material objetivo.Estas diferencias dan lugar a variaciones en la velocidad de deposición, la calidad de la película, la escalabilidad y la idoneidad para aplicaciones específicas.A continuación, exploramos estas diferencias en detalle.
Explicación de los puntos clave:
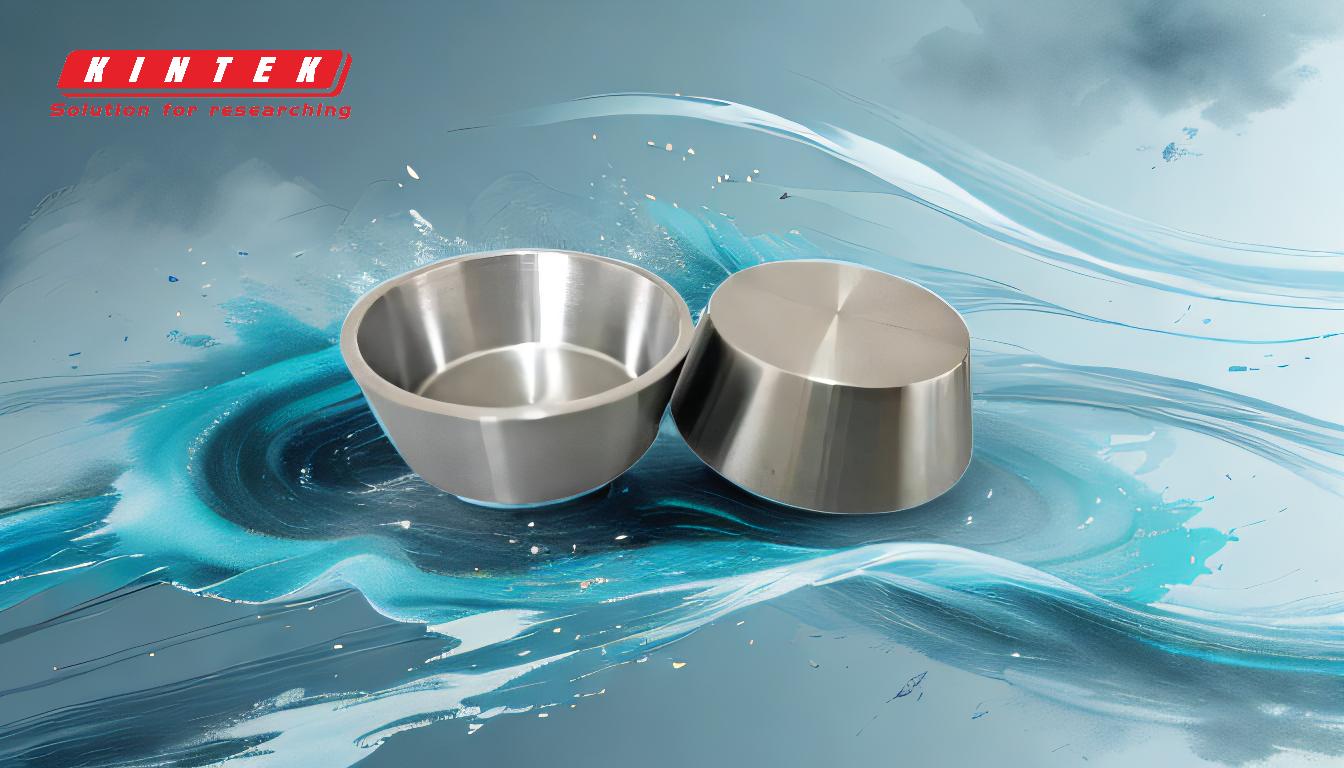
-
Mecanismo de vaporización de materiales:
-
Evaporación:
- Utiliza energía térmica (por ejemplo, calentamiento resistivo o haz de electrones) para calentar el material fuente hasta que alcanza su temperatura de vaporización.
- Produce una corriente de vapor robusta, lo que permite mayores velocidades de deposición.
- Funciona en un entorno de alto vacío para minimizar las colisiones en fase gaseosa.
-
Pulverización catódica:
- Consiste en bombardear un material objetivo con iones energéticos (normalmente argón) en un entorno de plasma.
- Expulsa átomos individuales o pequeños grupos del material objetivo.
- Funciona a presiones de gas más altas (5-15 mTorr), donde las partículas pulverizadas sufren colisiones en fase gaseosa antes de alcanzar el sustrato.
-
Evaporación:
-
Velocidad y eficacia de deposición:
-
Evaporación:
- Típicamente tiene una tasa de deposición más alta en comparación con el sputtering, especialmente para materiales de alta temperatura.
- Tiempos de ejecución más cortos debido a la robustez de la corriente de vapor.
-
Pulverización catódica:
- Generalmente tiene una tasa de deposición más baja, excepto para metales puros.
- El proceso es más lento pero ofrece mayor escalabilidad y potencial de automatización.
-
Evaporación:
-
Calidad y propiedades de la película:
-
Evaporación:
- Produce películas con mayor tamaño de grano y menor homogeneidad.
- Menor adherencia al sustrato debido a la menor energía de las especies depositadas.
- Menor absorción de gas en la película, ya que se trabaja en alto vacío.
-
Pulverización catódica:
- Produce películas de menor tamaño de grano y mayor homogeneidad.
- Mayor adherencia debido a la mayor energía de las partículas pulverizadas.
- Mayor absorción de gas en la película, ya que funciona a presiones de gas más elevadas.
-
Evaporación:
-
Condiciones de funcionamiento:
-
Evaporación:
- Requiere un entorno de alto vacío para garantizar colisiones mínimas en fase gaseosa.
- Deposición en la línea de visión, lo que significa que el sustrato debe estar directamente expuesto a la corriente de vapor.
-
Pulverización catódica:
- Funciona a niveles de vacío más bajos (presiones de gas más altas).
- La deposición es menos direccional debido a las colisiones en fase gaseosa, lo que permite una mejor cobertura de geometrías complejas.
-
Evaporación:
-
Versatilidad de materiales:
-
Evaporación:
- Adecuada para materiales que pueden soportar altas temperaturas sin descomponerse.
- Puede crear aleaciones mediante la coevaporación de varios materiales.
-
Pulverización catódica:
- Puede depositar una gama más amplia de materiales, incluidos los que tienen puntos de fusión elevados o los que se descomponen al calentarse.
- Pueden realizarse recubrimientos secuenciales en función de la configuración de la barnizadora.
-
Evaporación:
-
Aplicaciones:
-
Evaporación:
- Ideal para aplicaciones que requieren altas velocidades de deposición y geometrías sencillas, como revestimientos ópticos y algunas aplicaciones de semiconductores.
-
Pulverización catódica:
- Más adecuado para aplicaciones que requieren alta calidad de película, adhesión y cobertura de formas complejas, como microelectrónica, revestimientos decorativos y revestimientos resistentes al desgaste.
-
Evaporación:
-
Escalabilidad y automatización:
-
Evaporación:
- Menos escalable debido a la necesidad de condiciones de alto vacío y deposición en línea de visión.
-
Pulverización catódica:
- Altamente escalable y automatizable para la producción a gran escala, lo que la hace adecuada para aplicaciones industriales.
-
Evaporación:
En resumen, aunque tanto la evaporación como el sputtering son técnicas de PVD eficaces, se adaptan a diferentes aplicaciones en función de sus mecanismos, condiciones operativas y propiedades de la película resultante.La evaporación destaca por su elevada velocidad de deposición y su simplicidad, mientras que el sputtering ofrece una calidad de película, una adherencia y una escalabilidad superiores.Comprender estas diferencias es crucial para seleccionar la técnica adecuada para las necesidades específicas de deposición de películas finas.
Tabla resumen:
Aspecto | Evaporación | Pulverización catódica |
---|---|---|
Mecanismo | La energía térmica calienta el material para vaporizarlo. | Los iones energéticos desprenden átomos del material objetivo. |
Velocidad de deposición | Más alto, especialmente para materiales de alta temperatura. | Inferior, excepto para metales puros. |
Calidad de la película | Granulometría mayor, menor homogeneidad, menor adherencia. | Granos más pequeños, mayor homogeneidad, mejor adherencia. |
Condiciones operativas | Alto vacío, deposición direccional. | Menor vacío, deposición menos direccional. |
Versatilidad de materiales | Limitada a materiales resistentes a altas temperaturas. | Gama más amplia, incluidos materiales de alto punto de fusión. |
Aplicaciones | Recubrimientos ópticos, geometrías sencillas. | Microelectrónica, formas complejas, revestimientos resistentes al desgaste. |
Escalabilidad | Menos escalable debido a los requisitos de alto vacío y línea de visión. | Altamente escalable y automatizable para uso industrial. |
¿Necesita ayuda para elegir la técnica de PVD adecuada para su aplicación? Póngase en contacto con nuestros expertos hoy mismo ¡!