El sinterizado tradicional y el sinterizado selectivo por láser (SLS) son procesos utilizados para crear objetos sólidos a partir de materiales en polvo, pero difieren significativamente en sus métodos, aplicaciones y adecuación a las distintas necesidades de producción.El sinterizado tradicional, utilizado a menudo en pulvimetalurgia, consiste en compactar material en polvo en un molde y calentarlo a continuación hasta justo por debajo de su punto de fusión para fusionar las partículas.Este método es muy preciso, rentable para la producción en masa y requiere moldes.En cambio, el sinterizado selectivo por láser es una técnica de fabricación aditiva (impresión 3D) que utiliza un láser para fusionar selectivamente material en polvo capa por capa, guiado por un archivo CAD.El SLS no requiere moldes, ofrece mayor flexibilidad de diseño y es más adecuado para la creación de prototipos y la producción de bajo volumen, aunque suele ser menos preciso y más caro que el sinterizado tradicional.
Explicación de los puntos clave:
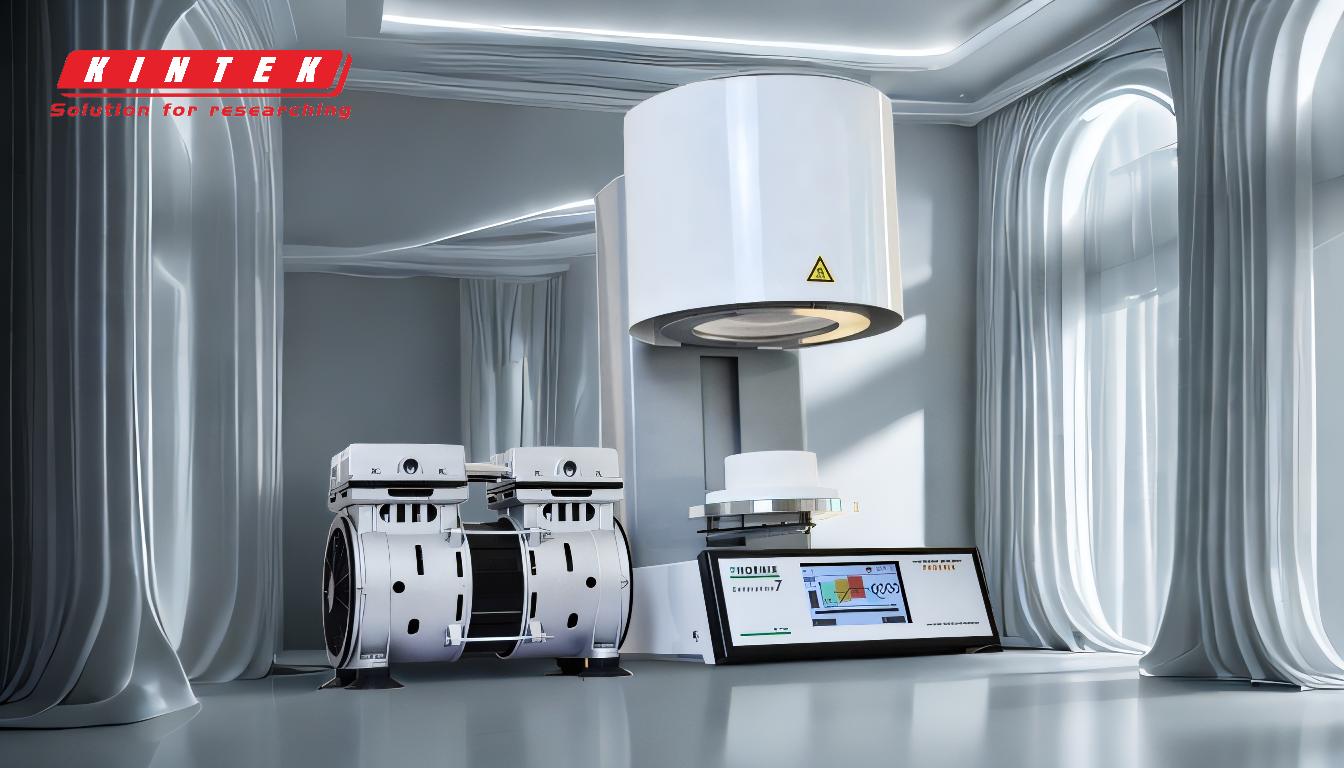
-
Metodología del proceso:
- Sinterización tradicional:Consiste en compactar material en polvo en un molde y luego calentarlo para fusionar las partículas.El molde define la forma del producto final.
- Sinterización selectiva por láser (SLS):Utiliza un láser para fusionar selectivamente material en polvo capa por capa, guiado por un archivo CAD.Este proceso no requiere molde, lo que permite geometrías más complejas.
-
Requisitos del molde:
- Sinterización tradicional:Requiere un molde para dar forma al objeto, lo que puede limitar la flexibilidad del diseño y aumentar los costes de las formas complejas.
- Sinterización selectiva por láser:No requiere molde, lo que permite crear diseños intrincados y complejos sin costes adicionales de utillaje.
-
Idoneidad para la producción:
- Sinterización tradicional:Más adecuado para la producción en serie de bajo coste debido a su precisión y rentabilidad.Es ideal para producir grandes cantidades de piezas idénticas.
- Sinterización selectiva por láser:Más adecuado para la creación de prototipos y la producción de bajo volumen.No se suele utilizar para la producción en serie debido a los costes más elevados y a los ritmos de producción más lentos.
-
Precisión y coste:
- Sinterización tradicional:Generalmente más precisas y baratas para la producción en serie.El uso de moldes garantiza piezas consistentes y precisas.
- Sinterización selectiva por láser:Menos preciso y más caro que el sinterizado tradicional.La falta de moldes y el proceso capa a capa pueden introducir ligeras variaciones.
-
Flexibilidad de diseño:
- Sinterización tradicional:Limitado por la necesidad de moldes, que puede restringir la complejidad de los diseños.
- Sinterización selectiva por láser:Ofrece una mayor flexibilidad de diseño, permitiendo la creación de geometrías complejas e intrincadas que serían difíciles o imposibles de conseguir con la sinterización tradicional.
-
Aplicaciones:
- Sinterización tradicional:Comúnmente utilizado en industrias que requieren la producción de grandes volúmenes de piezas, como la automotriz y la aeroespacial.
- Sinterización selectiva por láser:A menudo se utiliza en industrias que requieren prototipos rápidos, piezas personalizadas y producción de bajo volumen, como dispositivos médicos y productos de consumo.
En resumen, aunque tanto el sinterizado tradicional como el sinterizado selectivo por láser se utilizan para crear objetos sólidos a partir de materiales en polvo, difieren en sus metodologías, requisitos de molde, idoneidad de producción, precisión, coste, flexibilidad de diseño y aplicaciones.El sinterizado tradicional es más rentable y preciso para la producción en masa, mientras que el sinterizado selectivo por láser ofrece una mayor flexibilidad de diseño y es más adecuado para la creación de prototipos y la producción de bajo volumen.
Tabla resumen:
Aspecto | Sinterizado tradicional | Sinterizado Láser Selectivo (SLS) |
---|---|---|
Metodología del proceso | Se compacta el polvo en un molde y se calienta para fundirlo | Utiliza un láser para fusionar el polvo capa por capa (sin molde) |
Requiere molde | Requiere moldes | No necesita moldes |
Idoneidad para la producción | Ideal para la producción en serie | Ideal para prototipos y producción de bajo volumen |
Precisión | Mayor precisión para la producción en serie | Menos preciso debido al proceso capa por capa |
Coste | Rentable para grandes volúmenes de producción | Más caro, adecuado para bajo volumen |
Flexibilidad de diseño | Limitado por los requisitos del molde | Gran flexibilidad, admite geometrías complejas |
Aplicaciones | Automoción, aeroespacial (piezas de gran volumen) | Dispositivos médicos, productos de consumo (prototipos) |
¿Aún no está seguro de qué método de sinterización es el mejor para su proyecto? Póngase en contacto con nuestros expertos para un asesoramiento personalizado.