Los revestimientos PVD (deposición física de vapor) son famosos por su excepcional dureza, durabilidad y versatilidad.Estos revestimientos se utilizan ampliamente en industrias que requieren materiales de alto rendimiento, como la microelectrónica, la óptica y los dispositivos médicos.La dureza de un recubrimiento PVD depende del material específico utilizado, y algunos recubrimientos alcanzan niveles extremos de dureza debido a sus propiedades y procesos de deposición únicos.Entre los revestimientos PVD más duros se encuentran los basados en carbono diamante (DLC) y nitruro de titanio (TiN), que son conocidos por su resistencia superior al desgaste, su estabilidad a altas temperaturas y su excelente adherencia a los sustratos.Esto los hace ideales para aplicaciones que requieren una durabilidad y un rendimiento extremos.
Explicación de los puntos clave:
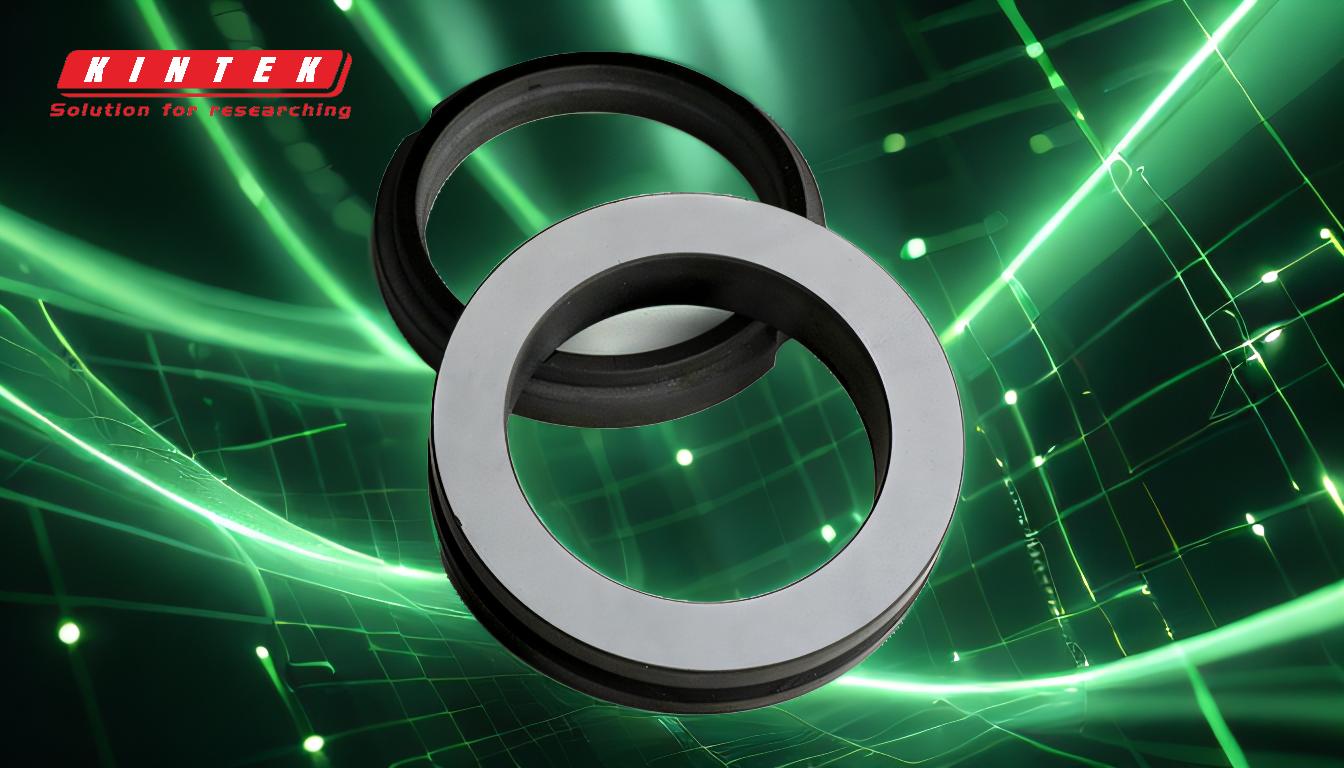
-
¿Qué hace que los revestimientos PVD sean duros?
- Los revestimientos PVD se crean mediante un proceso en el que un material sólido se vaporiza al vacío y luego se deposita sobre un sustrato.Este proceso permite controlar con precisión las propiedades del revestimiento, incluida la dureza.
- La dureza de los revestimientos PVD depende del material utilizado, el proceso de deposición y la microestructura resultante.Los materiales como el carbono diamante (DLC) y el nitruro de titanio (TiN) son especialmente duros debido a sus fuertes enlaces atómicos y sus densas estructuras.
-
Recubrimientos de carbono tipo diamante (DLC)
- Los recubrimientos DLC se encuentran entre los recubrimientos PVD más duros disponibles.Están formados por una mezcla de enlaces de carbono sp2 (tipo grafito) y sp3 (tipo diamante), que les confieren una dureza y una resistencia al desgaste excepcionales.
- Estos revestimientos se utilizan en aplicaciones que requieren una durabilidad extrema, como herramientas de corte, componentes de automoción y dispositivos médicos.También presentan baja fricción y alta inercia química.
-
Recubrimientos de nitruro de titanio (TiN)
- Los recubrimientos de TiN son otro ejemplo de recubrimientos PVD extremadamente duros.Son conocidos por su color dorado y se utilizan mucho en aplicaciones industriales, como herramientas de corte y componentes de maquinaria.
- Los revestimientos de TiN proporcionan una excelente dureza, resistencia al desgaste y estabilidad térmica, lo que los hace adecuados para entornos de gran tensión.
-
Otros recubrimientos PVD duros
- Otros revestimientos PVD duros son el nitruro de titanio y aluminio (TiAlN), el nitruro de cromo (CrN) y el nitruro de circonio (ZrN).Estos revestimientos ofrecen un equilibrio entre dureza, resistencia a la corrosión y estabilidad térmica, lo que los hace adecuados para aplicaciones especializadas.
- La elección del revestimiento depende de los requisitos específicos de la aplicación, como el entorno operativo, el material del sustrato y los atributos de rendimiento deseados.
-
Ventajas de los revestimientos PVD duros
- Durabilidad: Los revestimientos de PVD duro son muy resistentes al desgaste, la abrasión y los impactos, lo que prolonga la vida útil de los componentes revestidos.
- Estabilidad a altas temperaturas: Estos revestimientos pueden soportar temperaturas extremas, por lo que son adecuados para aplicaciones de alta temperatura.
- Versatilidad: Los revestimientos PVD pueden aplicarse a una amplia gama de sustratos, incluidos metales, cerámicas y polímeros.
- Precisión y control: El proceso de PVD permite un control preciso del espesor, la composición y las propiedades del revestimiento, lo que garantiza un rendimiento óptimo.
-
Aplicaciones de los revestimientos PVD duros
- Herramientas industriales: Las herramientas de corte, brocas y moldes se benefician de la dureza y resistencia al desgaste de los revestimientos PVD.
- Aeroespacial y automoción: Los componentes expuestos a altas tensiones y temperaturas, como piezas de motores y álabes de turbinas, suelen recubrirse con materiales PVD duros.
- Dispositivos médicos: Los instrumentos quirúrgicos y los implantes utilizan revestimientos de PVD por su biocompatibilidad y durabilidad.
- Electrónica y óptica: Los revestimientos PVD se utilizan en microchips, lentes ópticas y paneles solares debido a su pureza y atributos de rendimiento.
En resumen, los recubrimientos PVD más duros, como el DLC y el TiN, son muy apreciados por su excepcional dureza, durabilidad y versatilidad.Estos revestimientos son esenciales en industrias que requieren materiales capaces de soportar condiciones extremas y ofrecer un rendimiento duradero.El control preciso que ofrece el proceso de PVD garantiza que estos revestimientos satisfagan las necesidades específicas de diversas aplicaciones, lo que los convierte en un componente fundamental de la fabricación y la tecnología modernas.
Tabla resumen:
Tipo de revestimiento | Propiedades clave | Aplicaciones |
---|---|---|
Carbono tipo diamante (DLC) | Dureza extrema, baja fricción, alta inercia química | Herramientas de corte, componentes de automoción, dispositivos médicos |
Nitruro de titanio (TiN) | Excelente dureza, resistencia al desgaste, estabilidad térmica | Herramientas industriales, componentes de maquinaria |
Nitruro de titanio y aluminio (TiAlN) | Dureza equilibrada, resistencia a la corrosión, estabilidad térmica | Aplicaciones industriales especializadas |
Nitruro de cromo (CrN) | Alta dureza, resistencia a la corrosión | Industrias aeroespacial, automovilística y médica |
Nitruro de circonio (ZrN) | Dureza superior, estabilidad térmica | Electrónica, óptica y entornos de alto estrés |
Encuentre el recubrimiento PVD perfecto para su aplicación. póngase en contacto con nuestros expertos para empezar.