El depósito físico en fase vapor (PVD) es un proceso de recubrimiento al vacío que se utiliza para depositar películas finas de material sobre un sustrato.El proceso implica la vaporización de un material sólido en una fase de vapor, el transporte del vapor al sustrato y la condensación del vapor en el sustrato para formar una película fina.El PVD se utiliza ampliamente en industrias como la de los semiconductores, la óptica y el recubrimiento de herramientas, debido a su capacidad para producir recubrimientos de alta calidad, duraderos y precisos.El proceso se realiza normalmente en condiciones de alto vacío e implica múltiples pasos, como la generación de gas, el transporte, la reacción y la deposición.
Explicación de los puntos clave:
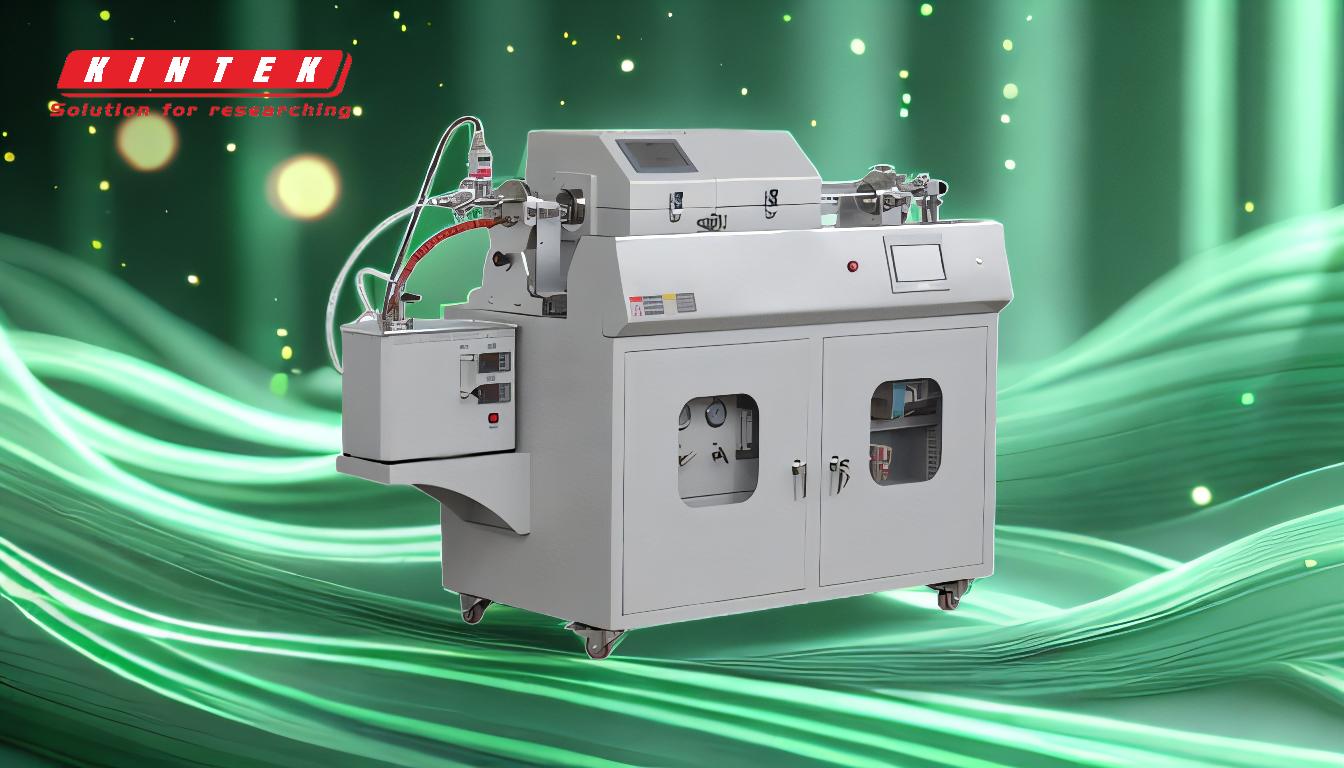
-
Vaporización del material de recubrimiento:
- El primer paso del proceso PVD es la vaporización del material de revestimiento.Esto puede conseguirse mediante métodos como la evaporación, el sputtering o la ablación por láser.En la evaporación, el material se calienta hasta que se convierte en vapor.En la pulverización catódica, iones de alta energía bombardean el material objetivo, desprendiendo átomos de su superficie y llevándolos a la fase de vapor.La ablación por láser utiliza un láser de alta potencia para vaporizar el material.
- La elección del método de vaporización depende del material depositado y de las propiedades deseadas del revestimiento final.Por ejemplo, el sputtering suele utilizarse para metales, mientras que la evaporación es más común para materiales con puntos de fusión más bajos.
-
Transporte del vapor al sustrato:
- Una vez vaporizado el material, los átomos, moléculas o iones son transportados a través de la cámara de vacío hasta el sustrato.Este transporte se produce en un entorno de alto vacío para minimizar las colisiones con otras partículas, lo que garantiza que el vapor llegue al sustrato con una contaminación mínima.
- Durante el transporte, el vapor puede sufrir colisiones con otras partículas, lo que provoca reacciones que pueden modificar la composición química del vapor.Esto es especialmente importante en los procesos de PVD reactivo, en los que se introduce un gas reactivo (como nitrógeno u oxígeno) para formar compuestos con el material vaporizado.
-
Condensación y deposición sobre el sustrato:
- La última etapa del proceso PVD es la condensación del vapor en el sustrato, donde forma una fina película.El sustrato suele mantenerse a una temperatura inferior a la del vapor, lo que favorece la condensación.Los átomos o moléculas del vapor se adhieren al sustrato, formando una capa sólida.
- Las propiedades de la película depositada, como el grosor, la uniformidad y la adherencia, dependen de factores como la temperatura del sustrato, la velocidad de deposición y las condiciones de vacío.Los revestimientos de alta calidad requieren un control preciso de estos parámetros.
-
PVD reactivo y formación de compuestos:
- En algunos procesos de PVD, se introduce un gas reactivo en la cámara de vacío para formar compuestos con el material vaporizado.Por ejemplo, al depositar nitruro de titanio (TiN), se vaporiza titanio y se introduce gas nitrógeno.Los átomos de titanio reaccionan con el nitrógeno para formar TiN, que se deposita sobre el sustrato.
- El PVD reactivo permite depositar una amplia gama de compuestos, como óxidos, nitruros y carburos, que pueden mejorar las propiedades del revestimiento, como la dureza, la resistencia al desgaste y la resistencia a la corrosión.
-
Ventajas del PVD:
- Los revestimientos PVD son conocidos por su gran pureza, densidad y adherencia, lo que los hace adecuados para aplicaciones que requieren revestimientos precisos y duraderos.El proceso puede utilizarse para depositar una amplia gama de materiales, como metales, cerámica y materiales compuestos.
- El PVD también es un proceso respetuoso con el medio ambiente, ya que no implica el uso de productos químicos peligrosos ni produce subproductos nocivos.El entorno de vacío garantiza que el proceso esté limpio y libre de contaminantes.
-
Aplicaciones del PVD:
- El PVD se utiliza ampliamente en varias industrias, incluidos los semiconductores, donde se emplea para depositar películas finas de materiales como el dióxido de silicio y el aluminio.En la industria óptica, el PVD se utiliza para crear revestimientos antirreflectantes y espejos.En la industria de herramientas, los revestimientos de PVD se aplican a las herramientas de corte para mejorar su resistencia al desgaste y su vida útil.
- La versatilidad del PVD lo hace adecuado para una amplia gama de aplicaciones, desde revestimientos decorativos en productos de consumo hasta revestimientos funcionales en dispositivos aeroespaciales y médicos.
En resumen, el proceso PVD es un método muy controlado y versátil para depositar películas finas de material sobre un sustrato.Implica la vaporización de un material sólido, el transporte del vapor al sustrato y la condensación del vapor para formar una película fina.El proceso puede mejorarse mediante el uso de gases reactivos para formar compuestos, y ofrece numerosas ventajas, como revestimientos de alta calidad y respeto por el medio ambiente.El PVD se utiliza en una amplia gama de industrias, desde semiconductores hasta recubrimientos de herramientas, lo que lo convierte en una tecnología fundamental en la fabricación moderna.
Cuadro sinóptico:
Aspecto clave | Detalles |
---|---|
Etapas del proceso | Vaporización → Transporte → Condensación y deposición |
Métodos de vaporización | Evaporación, pulverización catódica, ablación por láser |
Principales ventajas | Alta pureza, densidad, adherencia; respetuoso con el medio ambiente |
Aplicaciones | Semiconductores, óptica, revestimientos de herramientas, aeroespacial, dispositivos médicos |
PVD reactivo | Forma compuestos (por ejemplo, TiN) utilizando gases reactivos como el nitrógeno o el oxígeno. |
Descubra cómo el PVD puede mejorar su proceso de fabricación. contacte hoy con nuestros expertos ¡!