Los gases de protección desempeñan un papel fundamental en los procesos de soldadura fuerte, ya que evitan la oxidación y garantizan un acabado limpio y de alta calidad. La elección del gas de protección depende del método de soldadura fuerte y de los materiales utilizados. Los gases de protección más comunes son el hidrógeno, el amoníaco disociado y el nitrógeno. En la soldadura fuerte al vacío, el oxígeno se elimina por completo, mientras que la soldadura fuerte con gas de protección se basa en el nitrógeno y el fundente para lograr resultados similares. La selección de materiales, como las aleaciones que contienen magnesio para la soldadura fuerte en vacío o las aleaciones que dependen del fundente para la soldadura fuerte con gas de protección, influye aún más en la eficacia del gas de protección. Comprender estos factores es esencial para optimizar los resultados de la soldadura fuerte.
Explicación de los puntos clave:
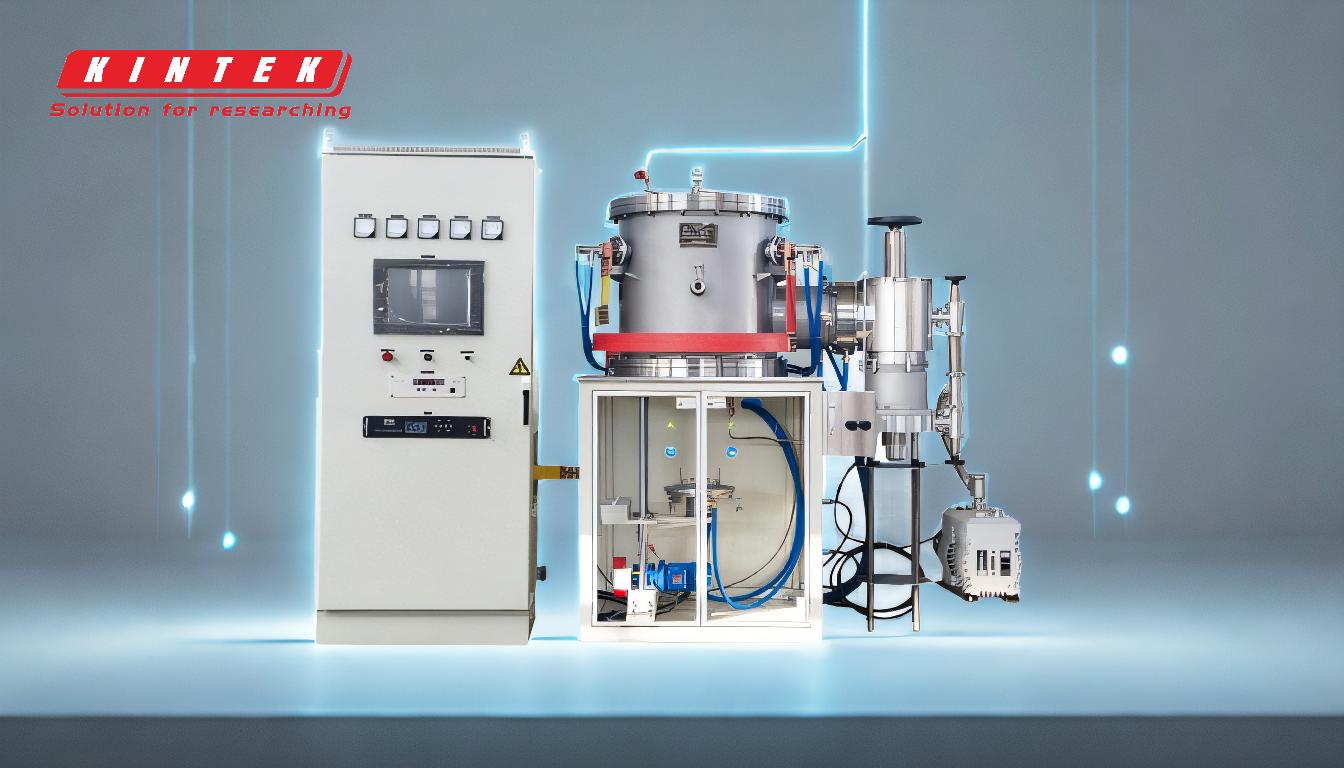
-
Finalidad de los gases de protección en la soldadura fuerte
- Los gases de protección se utilizan para crear una atmósfera inerte que evite la oxidación, la formación de incrustaciones y la acumulación de carbono (hollín) durante la soldadura fuerte.
- Garantizan un acabado limpio y brillante de la pieza, lo que es fundamental para conseguir uniones soldadas de alta calidad.
-
Gases de protección comunes
- Hidrógeno: A menudo se utiliza en la soldadura fuerte debido a su capacidad para reducir los óxidos y crear una superficie limpia.
- Amoníaco disociado: Mezcla de hidrógeno y nitrógeno, utilizada habitualmente por su rentabilidad y su capacidad para evitar la oxidación.
- Nitrógeno: Se utiliza con frecuencia en la soldadura fuerte con gas de protección para proteger la pieza de la oxidación.
-
Soldadura fuerte en vacío frente a soldadura fuerte con gas protector
-
Soldadura al vacío:
- Consiste en evacuar el horno para eliminar el oxígeno y otros gases reactivos.
- No requiere fundente, ya que el entorno de vacío elimina el riesgo de oxidación.
- Utiliza materiales como el doble compuesto 4104/****/4104, que contiene un 1,5% de magnesio para romper la capa de AL203 de la superficie de la pieza.
-
Soldadura con gas de protección:
- Depende del nitrógeno como gas de protección para proteger la pieza de trabajo.
- Requiere la aplicación de fundente para romper la capa de AL203, ya que los materiales utilizados (por ejemplo, 4343/****/4343 doble compuesto) no contienen magnesio.
-
Soldadura al vacío:
-
Consideraciones materiales
- Aleaciones que contienen magnesio (por ejemplo, 4104/****/4104): Utilizado en la soldadura fuerte al vacío, el magnesio ayuda a romper la capa de AL203, garantizando una unión adecuada.
- Aleaciones que no sean de magnesio (por ejemplo, 4343/****/4343): Utilizados en la soldadura fuerte con gas de protección, estos materiales dependen del fundente para conseguir el mismo efecto.
-
Diferencias de proceso
-
Soldadura al vacío:
- Implica una fase de aislamiento más larga (unas 4 horas por horno) para garantizar una distribución uniforme de la temperatura.
- No es necesario ningún proceso de enfriamiento tras la soldadura.
-
Soldadura con gas de protección:
- Funciona de forma continua a una velocidad de 350 mm/min.
- No requiere vacío ni proceso de enfriamiento, lo que la hace más rápida y eficaz para determinadas aplicaciones.
-
Soldadura al vacío:
-
Ventajas de los gases de protección
- Mejora de la calidad de las articulaciones: Los gases de protección evitan la oxidación, lo que da lugar a uniones soldadas más fuertes y fiables.
- Estética mejorada: El uso de gases inertes permite obtener un acabado limpio y brillante de la pieza.
- Versatilidad: Los distintos gases y métodos (vacío frente a gas protegido) permiten abordar con flexibilidad los diversos retos de la soldadura fuerte.
-
Factores que influyen en la selección del gas
- Tipo de material: La elección del gas de protección depende de la aleación que se vaya a soldar y de sus requisitos específicos (por ejemplo, contenido de magnesio).
- Método de soldadura: La soldadura fuerte al vacío y la soldadura fuerte con protección de gas tienen requisitos de gas distintos.
- Coste y eficacia: El amoníaco disociado suele elegirse por su rentabilidad, mientras que el nitrógeno se prefiere por su disponibilidad y facilidad de uso en la soldadura fuerte con protección de gas.
Al comprender el papel de los gases de protección y su aplicación en los distintos procesos de soldadura fuerte, los fabricantes pueden optimizar sus operaciones para lograr resultados superiores. La elección del gas, el material y el método debe ajustarse a los requisitos específicos de la pieza y al resultado deseado.
Cuadro recapitulativo:
Aspecto | Soldadura al vacío | Soldadura con gas de protección |
---|---|---|
Gas de protección | Eliminación total del oxígeno; no se necesita gas de protección | Nitrógeno utilizado como gas de protección |
Requisito de flujo | No necesita fundente | Fundente necesario para romper la capa de AL203 |
Material utilizado | Aleaciones que contienen magnesio (por ejemplo, 4104/****/4104) | Aleaciones que no sean de magnesio (por ejemplo, 4343/****/4343) |
Duración del proceso | Fase de aislamiento más larga (~4 horas por horno) | Funcionamiento continuo a 350 mm/min |
Proceso de enfriamiento | No necesita refrigeración | No necesita refrigeración |
Ventajas | Juntas limpias y sin oxidación; sin residuos de fundente | Más rápido y eficaz para determinadas aplicaciones |
¿Está listo para optimizar su proceso de soldadura? Contacte hoy mismo con nuestros expertos soluciones a medida