La pulverización catódica es una técnica versátil de deposición de películas finas muy utilizada en sectores como los semiconductores, la óptica y el almacenamiento de datos.Consiste en bombardear un material objetivo con iones de alta energía en una cámara de vacío, lo que provoca la expulsión de átomos que se depositan sobre un sustrato.Este método es muy controlable y puede producir películas uniformes y de alta calidad con espesores que oscilan entre nanómetros y micrómetros.El sputtering se utiliza para aplicaciones como revestimientos antirreflectantes, metalización de semiconductores y revestimientos de herramientas resistentes al desgaste.El proceso es preciso, repetible y capaz de depositar una amplia gama de materiales, incluidos metales, aleaciones y compuestos, lo que lo convierte en una piedra angular de la fabricación y la tecnología modernas.
Explicación de los puntos clave:
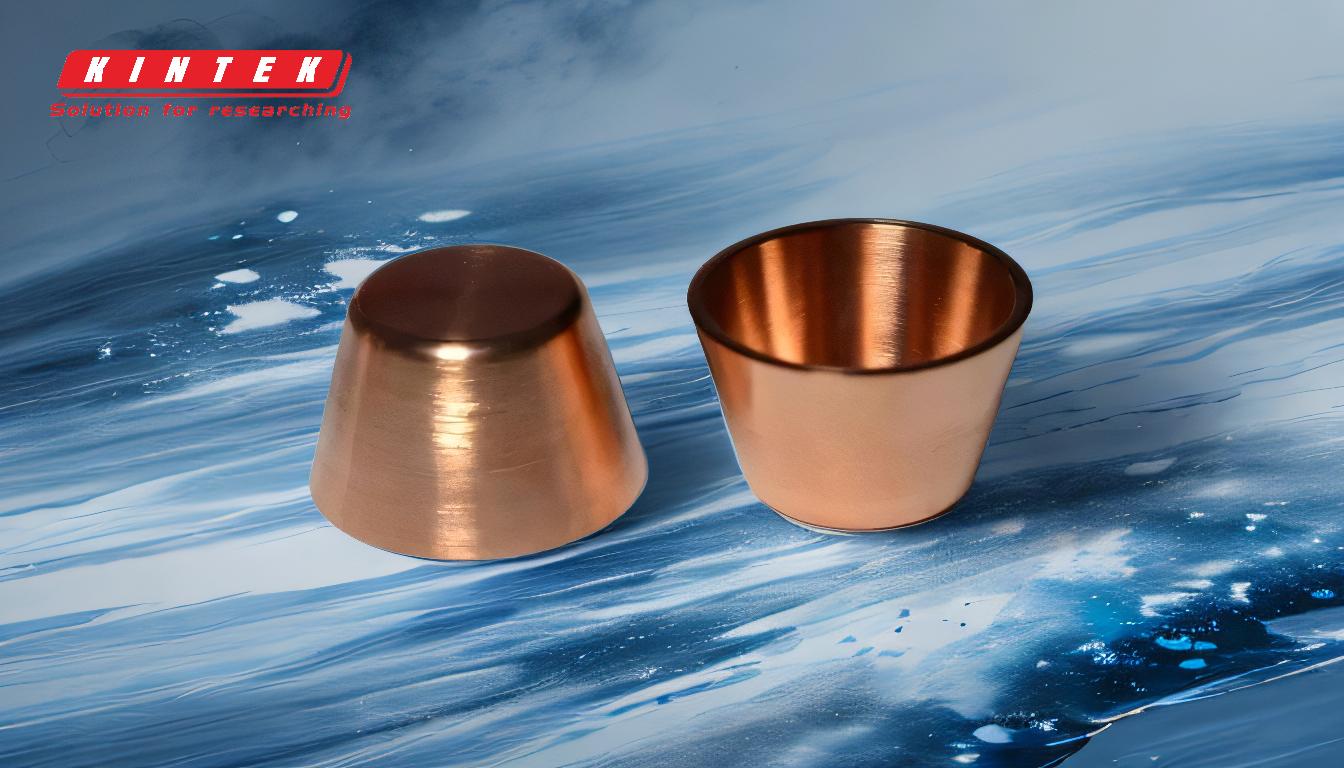
-
Definición de sputtering
- El sputtering es una técnica de deposición física de vapor (PVD) en la que los átomos son expulsados de un material objetivo sólido debido al bombardeo de iones de alta energía en un entorno de vacío.
- Los átomos expulsados forman una corriente de vapor que se deposita sobre un sustrato, creando una fina película.
- Este proceso es altamente controlable y puede producir películas de espesor y composición precisos.
-
Mecanismo del sputtering
- Se introduce un gas controlado, normalmente argón, en una cámara de vacío.
- Se aplica energía eléctrica a un cátodo para generar un plasma que ioniza los átomos de gas.
- Los iones cargados positivamente se aceleran hacia el material objetivo, desprendiendo átomos o moléculas al impactar.
- Estos átomos desalojados forman una corriente de vapor que se deposita sobre el sustrato, formando una fina película.
-
Aplicaciones de la deposición por pulverización catódica
- Industria de semiconductores:Se utiliza para depositar películas finas en circuitos integrados, como capas de metalización y metales de contacto en transistores de película fina.
- Óptica y vidrio:Aplicado para revestimientos antirreflectantes, revestimientos de baja emisividad y películas de alta emisividad sobre vidrio.
- Almacenamiento de datos:Utilizado en la producción de discos duros de ordenador, CD y DVD.
- Recubrimientos para herramientas:Deposita revestimientos resistentes al desgaste, como el nitruro de titanio, en las herramientas de corte.
- Células solares:Utilizado en la fabricación de células solares fotovoltaicas.
- Revestimientos decorativos y funcionales:Se aplica para revestimientos reflectantes sobre polímeros, lubricantes de película seca y acabados decorativos.
-
Ventajas del sputtering
- Uniformidad:Produce películas muy uniformes y densas.
- Versatilidad:Puede depositar una amplia gama de materiales, incluidos metales, aleaciones y compuestos.
- Precisión:Permite controlar con precisión el espesor y la composición de la película.
- Adhesión:Garantiza una fuerte adherencia de la película al sustrato.
- Escalabilidad:Adecuado para la producción industrial a gran escala.
-
Tipos de técnicas de sputtering
- Sputtering DC:Utiliza corriente continua para generar plasma, adecuado para materiales conductores.
- Pulverización catódica por RF:Utiliza la radiofrecuencia para ionizar el gas, lo que permite la deposición de materiales no conductores.
- Pulverización catódica por magnetrón:Incorpora campos magnéticos para aumentar la densidad del plasma, mejorando la velocidad de deposición y la calidad de la película.
- Pulverización catódica reactiva:Introduce gases reactivos (por ejemplo, nitrógeno u oxígeno) para formar películas compuestas como óxidos o nitruros.
-
Componentes clave de un sistema de sputtering
- Cámara de vacío:Mantiene un entorno controlado para el proceso.
- Material objetivo:Fuente de los átomos que se depositarán.
- Sustrato:La superficie sobre la que se deposita la película fina.
- Fuente de alimentación:Proporciona energía para generar plasma.
- Sistema de suministro de gas:Introduce y controla el flujo de gas de sputtering.
-
Retos y consideraciones
- Coste:Elevada inversión inicial en equipos y mantenimiento.
- Complejidad:Requiere un control preciso de parámetros como la presión, la potencia y el caudal de gas.
- Limitaciones del material:Algunos materiales pueden ser difíciles de bombardear debido a su bajo rendimiento o a sus altos puntos de fusión.
- Contaminación:Requiere una manipulación cuidadosa para evitar impurezas en la película depositada.
-
Tendencias futuras de la tecnología de sputtering
- Materiales avanzados:Desarrollo de nuevos materiales diana para aplicaciones especializadas.
- Sostenibilidad:Centrarse en reducir el consumo de energía y el impacto medioambiental.
- Automatización:Integración de IA y aprendizaje automático para la optimización de procesos.
- Miniaturización:Adaptación a la nanotecnología y la microelectrónica.
En resumen, el sputtering es una técnica fundamental en la fabricación moderna, que permite la deposición de películas finas de alta calidad para una amplia gama de aplicaciones.Su precisión, versatilidad y escalabilidad la hacen indispensable en industrias como la de los semiconductores, la óptica y la energía.
Cuadro sinóptico:
Aspecto | Detalles |
---|---|
Definición | Técnica de deposición física de vapor (PVD) que utiliza iones de alta energía. |
Mecanismo | Bombardeo del material objetivo en una cámara de vacío para depositar películas finas. |
Aplicaciones | Semiconductores, óptica, almacenamiento de datos, revestimientos de herramientas, células solares, etc. |
Ventajas | Uniformidad, versatilidad, precisión, fuerte adhesión y escalabilidad. |
Técnicas | CC, RF, magnetrón y sputtering reactivo. |
Componentes | Cámara de vacío, material objetivo, sustrato, fuente de alimentación, suministro de gas. |
Desafíos | Coste elevado, complejidad, limitaciones de material y riesgos de contaminación. |
Tendencias futuras | Materiales avanzados, sostenibilidad, automatización y miniaturización. |
Descubra cómo el sputtering puede mejorar su proceso de fabricación. contacte con nuestros expertos hoy mismo ¡!