La temperatura y el tiempo de mantenimiento de la sinterización son parámetros críticos que dependen del material procesado, de las propiedades deseadas del producto final y de la técnica de sinterización utilizada. Las temperaturas de sinterización suelen oscilar entre el 70% y el 90% del punto de fusión del material, y el tiempo de mantenimiento puede variar entre milisegundos y más de 24 horas. Estos parámetros influyen en la porosidad, densidad, resistencia y dureza del cuerpo sinterizado. Las temperaturas elevadas y los tiempos de mantenimiento prolongados pueden reducir la porosidad y aumentar la densidad, pero también pueden provocar defectos o crecimiento de grano, mientras que una sinterización insuficiente puede degradar las propiedades del material. La elección de las condiciones de sinterización debe equilibrar estos factores para conseguir las características deseadas del producto.
Explicación de los puntos clave:
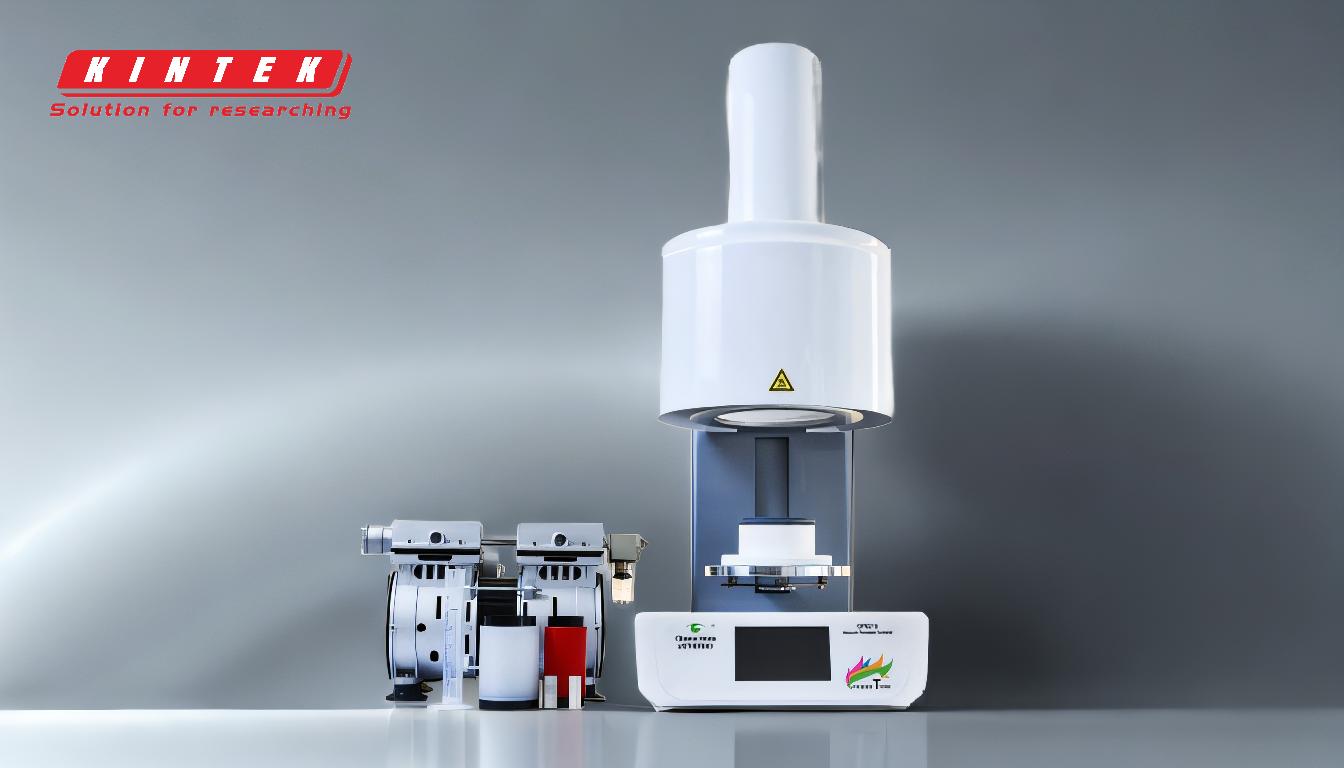
-
Dependencia del material y de las propiedades deseadas:
- La temperatura de sinterización y el tiempo de mantenimiento se adaptan al material específico y a la densidad, resistencia y dureza requeridas de la pieza final.
- Por ejemplo, metales como el acero o el titanio pueden requerir temperaturas más elevadas (por ejemplo, de 1000°C a 1400°C) en comparación con la cerámica o los polímeros.
-
Temperatura típica:
- Las temperaturas de sinterización suelen oscilar entre el 70% y el 90% del punto de fusión del material.
- Por ejemplo, si un material tiene un punto de fusión de 1500°C, la temperatura de sinterización podría oscilar entre 1050°C y 1350°C.
-
Variabilidad del tiempo de retención:
- Los tiempos de retención pueden oscilar entre milisegundos (en técnicas como el sinterizado por plasma de chispa) y varias horas (en el sinterizado tradicional en horno).
- Los tiempos de mantenimiento más largos suelen utilizarse para materiales que requieren una alta densificación, mientras que los tiempos más cortos pueden ser suficientes para materiales con puntos de fusión más bajos o cuando se utilizan técnicas avanzadas.
-
Influencia en las propiedades del material:
- Alta temperatura y largo tiempo de mantenimiento: Puede reducir la porosidad y aumentar la densidad, pero puede causar crecimiento de grano, defectos o propiedades mecánicas reducidas.
- Temperatura baja o tiempo de mantenimiento corto: Puede dar lugar a una densificación insuficiente, con las consiguientes propiedades mecánicas deficientes y mayor porosidad.
-
Papel de la atmósfera de sinterización:
- La atmósfera de sinterización (por ejemplo, aire, vacío, argón o nitrógeno) puede afectar al proceso impidiendo la oxidación o controlando las velocidades de difusión.
- Por ejemplo, la sinterización en vacío se utiliza a menudo para materiales propensos a la oxidación, como el titanio.
-
Impacto del tamaño y la composición de las partículas:
- Los tamaños de partícula más pequeños y las composiciones homogéneas favorecen una mejor densificación y una sinterización más rápida.
- Las partículas más grandes o las composiciones heterogéneas pueden requerir temperaturas más altas o tiempos de mantenimiento más largos.
-
Técnicas avanzadas de sinterización:
- Técnicas como el sinterizado selectivo por láser (SLS) o el sinterizado asistido por campo (FAST) pueden reducir considerablemente los tiempos de sinterización.
- Por ejemplo, FAST puede lograr una densificación completa en cuestión de minutos, frente a las horas de los hornos tradicionales.
-
Compromisos en los parámetros de sinterización:
- Aumentar la temperatura o el tiempo de mantenimiento puede mejorar la densidad y la resistencia, pero también puede aumentar el riesgo de defectos o crecimiento del grano.
- Las técnicas de sinterización más rápidas pueden reducir el tiempo de procesamiento, pero podrían dar lugar a porosidad residual o densificación desigual.
-
Importancia de la tasa de enfriamiento:
- La velocidad de enfriamiento tras la sinterización puede influir en la microestructura y las propiedades finales.
- El enfriamiento controlado se utiliza a menudo para evitar tensiones térmicas o transformaciones de fase que podrían degradar el rendimiento del material.
-
Optimización para aplicaciones específicas:
- La elección de los parámetros de sinterización depende de los requisitos de la aplicación, como alta resistencia, resistencia al desgaste o conductividad térmica.
- Por ejemplo, las condiciones de sinterización para componentes aeroespaciales pueden dar prioridad a la solidez y la resistencia a la fatiga, mientras que las de los implantes biomédicos pueden centrarse en la biocompatibilidad y la resistencia a la corrosión.
Si se equilibran cuidadosamente estos factores, los fabricantes pueden conseguir las propiedades deseadas en los materiales sinterizados minimizando al mismo tiempo los defectos y los costes de procesamiento. El proceso de sinterización óptimo es un compromiso entre las características del material, las técnicas de procesamiento y los requisitos de la aplicación.
Cuadro recapitulativo:
Factor | Impacto en la sinterización |
---|---|
Tipo de material | Determina la temperatura y el tiempo de mantenimiento necesarios (por ejemplo, metales frente a cerámica). |
Temperatura | Normalmente entre el 70% y el 90% del punto de fusión del material. |
Tiempo de espera | Oscila entre milisegundos (sinterización por plasma de chispa) y horas (sinterización tradicional). |
Atmósfera de sinterización | Evita la oxidación o controla la difusión (por ejemplo, el vacío para el titanio). |
Tamaño de las partículas | Las partículas más pequeñas favorecen una densificación más rápida y mejor. |
Técnicas avanzadas | FAST o SLS reducen significativamente el tiempo de sinterización. |
Tasa de enfriamiento | Influye en la microestructura y evita las tensiones térmicas. |
Requisitos de solicitud | Adaptados a la solidez, la resistencia al desgaste o la biocompatibilidad (por ejemplo, aeroespacial frente a biomédica). |
¿Necesita ayuda para optimizar su proceso de sinterización? Contacte hoy mismo con nuestros expertos soluciones a medida