Los revestimientos PVD (deposición física de vapor) se aplican a una amplia gama de metales, aleaciones y sustratos, en función de las propiedades y aplicaciones deseadas.Entre los metales comunes que se someten a revestimiento PVD se encuentran el acero inoxidable, el titanio, el circonio, el aluminio y el cobre, así como aleaciones especializadas como aceros para herramientas y aleaciones de titanio.Estos revestimientos se utilizan para mejorar propiedades como la dureza, la resistencia al desgaste, la estabilidad química y el aspecto estético.Los revestimientos PVD suelen aplicarse a materiales que pueden soportar altas temperaturas (hasta 800 ºF) y son compatibles con los procesos de deposición al vacío.La técnica es versátil y puede utilizarse en metales, cerámicas e incluso algunos polímeros, por lo que es adecuada para industrias que van desde la aeroespacial y la automoción hasta la médica y la electrónica.
Explicación de los puntos clave:
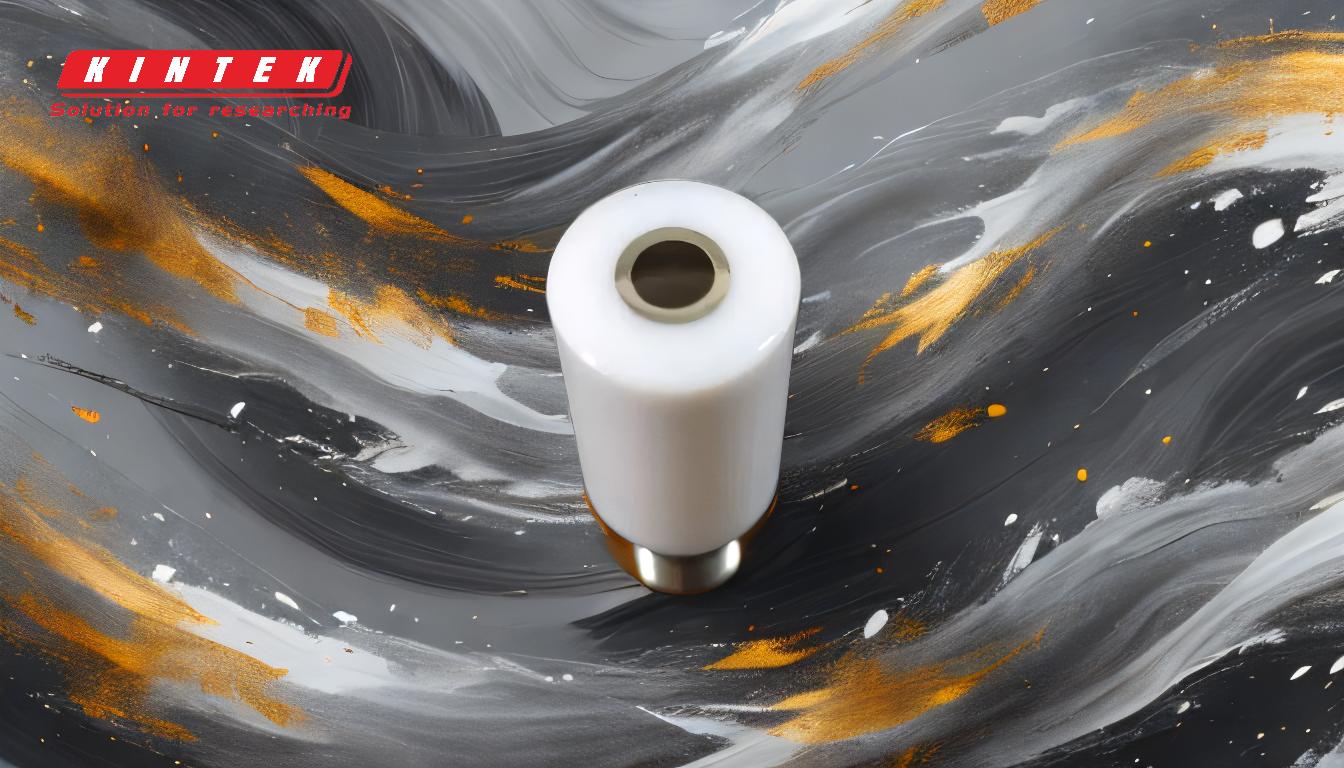
-
Metales comunes para recubrimiento PVD:
- Acero inoxidable:Los aceros inoxidables más utilizados son el 303, el 440C y el 17-4. Suelen elegirse por su durabilidad y resistencia a la corrosión.Suelen elegirse por su durabilidad y resistencia a la corrosión, lo que los hace ideales para aplicaciones médicas e industriales.
- Titanio y aleaciones de titanio:El titanio es ligero, resistente y biocompatible, lo que lo convierte en una opción popular para la industria aeroespacial, los implantes médicos y las aplicaciones de alto rendimiento.
- Aluminio:Aunque es menos común debido a su bajo punto de fusión, el aluminio puede recubrirse con PVD para aplicaciones específicas en las que la reducción de peso es fundamental.
- Cobre:Se utiliza en electrónica y aeronáutica por su excelente conductividad eléctrica y sus propiedades térmicas.
- Circonio:A menudo se utiliza en revestimientos especializados por su alta resistencia a la corrosión y biocompatibilidad.
-
Compatibilidad del sustrato:
- Los revestimientos PVD pueden aplicarse a diversos sustratos, como metales, cerámica y algunos polímeros.El sustrato debe poder soportar las altas temperaturas (normalmente hasta 800 ºF) y las condiciones de vacío del proceso de PVD.
-
Recubrimientos especializados:
- Carburos, nitruros y boruros:Estos revestimientos se utilizan para satisfacer requisitos de rendimiento específicos, como una mayor dureza, resistencia al desgaste o estabilidad térmica.Algunos ejemplos son el nitruro de titanio (TiN) y el nitruro de circonio (ZrN), que se utilizan habitualmente en herramientas de corte y componentes de automoción.
- Oro y otros metales preciosos:El oro se solicita con frecuencia para la electrónica aeroespacial debido a su excelente conductividad y resistencia a la corrosión.
-
Condiciones del proceso:
- El revestimiento PVD se realiza en una cámara de vacío a temperaturas de entre 50 y 600 grados Celsius.El proceso consiste en vaporizar el material de revestimiento (blanco) y depositarlo sobre el sustrato (pieza de trabajo) en un entorno controlado.Pueden introducirse gases reactivos como nitrógeno, acetileno u oxígeno para crear revestimientos compuestos con propiedades a medida.
-
Aplicaciones de los revestimientos PVD:
- Aeroespacial:Se utiliza para componentes que requieren alta resistencia, resistencia al desgaste y estabilidad térmica.
- Médico:Aplicado a implantes e instrumentos quirúrgicos por su biocompatibilidad y resistencia a la corrosión.
- Automoción:Mejora la durabilidad y el rendimiento de las piezas del motor, las herramientas de corte y los elementos decorativos.
- Electrónica:Proporciona revestimientos conductores y protectores para componentes como conectores y placas de circuitos.
-
Ventajas de los revestimientos PVD:
- Fino y duradero:Los revestimientos PVD son extremadamente finos (0,5 - 5 μm) pero ofrecen mejoras significativas en la dureza superficial, la resistencia al desgaste y la estabilidad química.
- Versatilidad estética:El proceso permite una amplia gama de colores y acabados, lo que lo hace adecuado para aplicaciones decorativas.
- Adhesión fuerte:Los revestimientos forman una fuerte unión con el sustrato, lo que garantiza un rendimiento duradero.
Al conocer los metales y sustratos adecuados para el revestimiento PVD, así como las condiciones del proceso y las aplicaciones, los compradores pueden tomar decisiones informadas a la hora de seleccionar materiales y revestimientos para sus necesidades específicas.
Tabla resumen:
Categoría | Detalles |
---|---|
Metales comunes | Acero inoxidable, titanio, circonio, aluminio, cobre, aceros para herramientas, aleaciones de titanio |
Compatibilidad de sustratos | Metales, cerámicas y algunos polímeros que soportan altas temperaturas y condiciones de vacío |
Recubrimientos especializados | Carburos, nitruros, boruros, oro y otros metales preciosos |
Condiciones del proceso | Cámara de vacío, 50-600°C, gases reactivos (nitrógeno, acetileno, oxígeno) |
Aplicaciones | Aeroespacial, médica, automoción, electrónica |
Ventajas | Fino, duradero, resistente al desgaste, químicamente estable, versatilidad estética |
¿Está preparado para mejorar sus materiales con recubrimientos PVD? Póngase en contacto con nuestros expertos para obtener soluciones a medida.