En la fabricación de aleaciones se utiliza una atmósfera inerte para evitar reacciones químicas no deseadas, como la oxidación o la contaminación, durante procesos como el tratamiento térmico, la sinterización o el prensado isostático en caliente. Al crear un entorno controlado con gases como el argón o el nitrógeno, los fabricantes pueden garantizar que la aleación mantenga las propiedades deseadas, como la resistencia, la durabilidad y la calidad de la superficie. Esto es especialmente importante en industrias como la aeroespacial, la automovilística y la petroquímica, donde la integridad del material es primordial. La atmósfera inerte también reduce riesgos como incendios, explosiones y contaminación, garantizando procesos de producción más seguros y eficaces.
Explicación de los puntos clave:
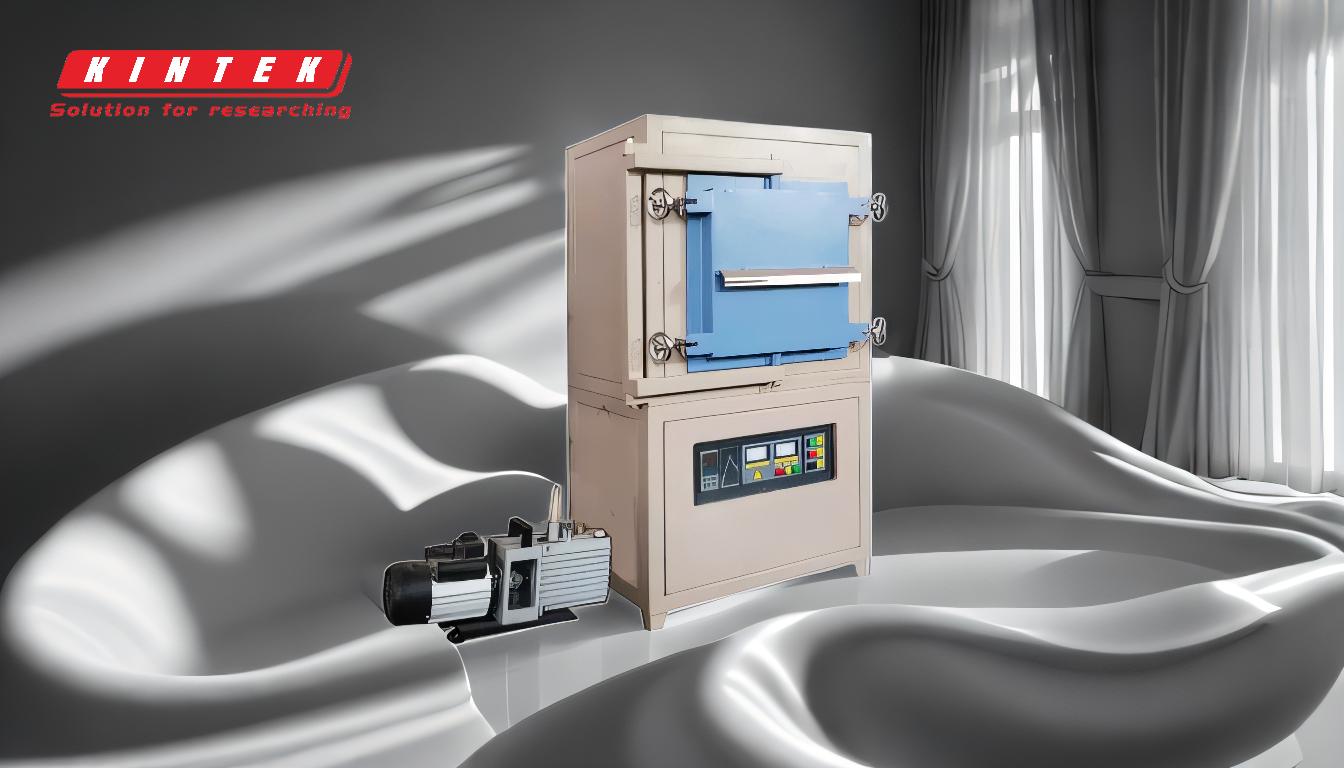
-
Prevención de la oxidación y la contaminación
- La oxidación se produce cuando los metales reaccionan con el oxígeno del aire, formando óxidos que pueden degradar la superficie de la aleación y sus propiedades mecánicas.
- Una atmósfera inerte, creada normalmente con gases como el argón o el nitrógeno, desplaza al oxígeno y otros gases reactivos, evitando la oxidación y la contaminación.
- Esto garantiza que la aleación conserve la composición química y la calidad superficial deseadas, lo que es fundamental para las aplicaciones que requieren alta precisión y durabilidad.
-
Mantenimiento de las propiedades de los materiales
- Durante los procesos de tratamiento térmico, como la sinterización, el recocido brillante o la carbonitruración, se controlan cuidadosamente la microestructura y las propiedades mecánicas de la aleación.
- Una atmósfera inerte garantiza que estos procesos se produzcan sin interferencias de factores externos, preservando la resistencia, dureza y otras propiedades críticas de la aleación.
- Por ejemplo, en la fabricación aeroespacial o automovilística, incluso pequeñas desviaciones en las propiedades de los materiales pueden provocar fallos catastróficos.
-
Control de procesos mejorado
- Una atmósfera inerte proporciona un entorno altamente controlado, reduciendo la variabilidad en el proceso de fabricación.
- Esto es especialmente importante en procesos como el prensado isostático en caliente (HIP) o las operaciones de vacío, donde se requiere un control preciso de la temperatura, la presión y la composición del gas.
- Al minimizar las reacciones no deseadas, los fabricantes pueden conseguir resultados uniformes y reducir los residuos.
-
Seguridad y reducción de riesgos
- Las atmósferas inertes reducen el riesgo de incendios y explosiones, especialmente cuando se trabaja con metales reactivos o procesos a alta temperatura.
- Al desplazar el oxígeno, la probabilidad de combustión disminuye significativamente, creando un entorno de trabajo más seguro.
- Esto es especialmente importante en industrias como la petroquímica, donde la seguridad es una prioridad absoluta.
-
Aplicaciones en industrias críticas
- Industrias como la aeroespacial, la automovilística y la petroquímica dependen de atmósferas inertes para producir aleaciones de alta calidad con especificaciones precisas.
- Por ejemplo, en el sector aeroespacial, las aleaciones deben soportar condiciones extremas, y cualquier contaminación u oxidación podría comprometer su rendimiento.
- Del mismo modo, en la fabricación de automóviles, componentes como las piezas del motor o los sistemas de transmisión requieren materiales con propiedades constantes para garantizar su fiabilidad y longevidad.
-
Coste y eficiencia
- Aunque crear una atmósfera inerte puede suponer costes adicionales, los beneficios a largo plazo suelen compensar la inversión inicial.
- Al reducir la oxidación y la contaminación, los fabricantes pueden minimizar el desperdicio de material y las repeticiones, lo que supone un ahorro de costes.
- Además, la mejora de la consistencia y la calidad de las aleaciones puede aumentar la eficacia general del proceso de fabricación.
En resumen, una atmósfera inerte es esencial en la fabricación de aleaciones para evitar la oxidación, mantener las propiedades de los materiales, garantizar el control de los procesos, mejorar la seguridad y cumplir los estrictos requisitos de las industrias críticas. Mediante el uso de gases inertes como el argón o el nitrógeno, los fabricantes pueden producir aleaciones de alta calidad con un rendimiento constante, por lo que es un componente vital de los procesos industriales modernos.
Cuadro recapitulativo:
Principales ventajas de la atmósfera inerte | Detalles |
---|---|
Evita la oxidación y la contaminación | Utiliza gases como el argón o el nitrógeno para desplazar el oxígeno, garantizando la integridad de la aleación. |
Mantiene las propiedades del material | Preserva la resistencia, dureza y durabilidad durante los procesos de tratamiento térmico. |
Mejora el control del proceso | Reduce la variabilidad, garantizando resultados uniformes en procesos como HIP o sinterización. |
Mejora la seguridad | Reduce los riesgos de incendio y explosión al desplazar el oxígeno en los procesos a alta temperatura. |
Aplicaciones industriales críticas | Esencial para la fabricación aeroespacial, automovilística y petroquímica. |
Ventajas de coste y eficiencia | Reduce los residuos y las repeticiones, mejorando la eficacia de la fabricación a largo plazo. |
Descubra cómo una atmósfera inerte puede optimizar su proceso de fabricación de aleaciones contacte hoy mismo con nuestros expertos ¡!