El revestimiento PVD (deposición física de vapor) es un sofisticado proceso utilizado para aplicar revestimientos finos, muy adherentes y duraderos a diversos sustratos.El proceso implica varios pasos clave, como la limpieza y el pretratamiento del sustrato, la vaporización del material objetivo, el transporte de los átomos vaporizados, la reacción con gases (si es necesario) y la deposición sobre el sustrato.El resultado es una capa de micras de espesor que se interpenetra con el material subyacente, proporcionando una excelente adherencia y resistencia a la descamación o el desconchado.El proceso se lleva a cabo en un entorno de vacío que utiliza gases inertes como el argón para garantizar una atmósfera químicamente no reactiva, lo que mejora la calidad y la durabilidad del revestimiento.
Explicación de los puntos clave:
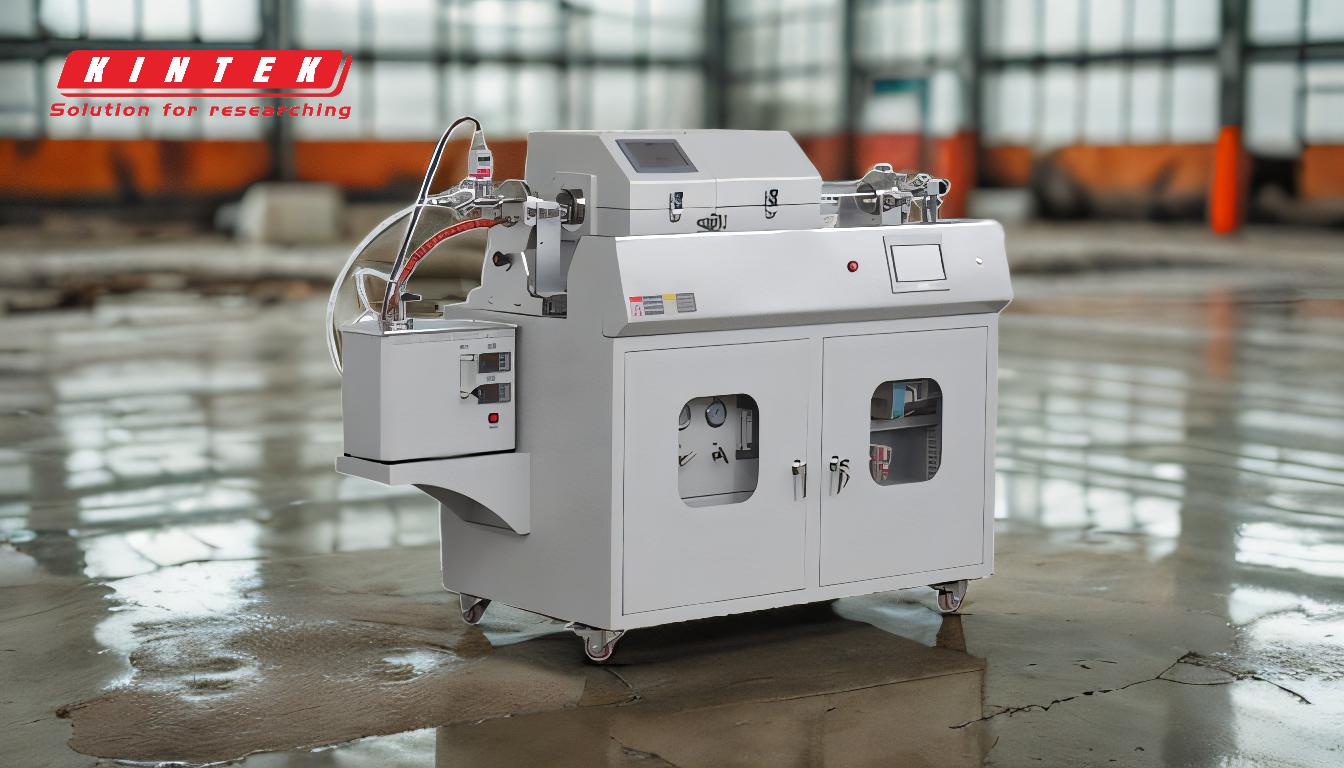
-
Limpieza y pretratamiento del sustrato:
- Limpieza: El sustrato debe limpiarse a fondo para eliminar cualquier contaminante como aceites, polvo u óxidos.Esto es crucial porque cualquier impureza en la superficie puede afectar negativamente a la adherencia y la calidad del revestimiento.Los métodos de limpieza pueden incluir la limpieza por ultrasonidos, la limpieza química o la limpieza por plasma.
- Pretratamiento: Tras la limpieza, el sustrato suele someterse a procesos de pretratamiento para mejorar la adherencia del revestimiento.Esto puede implicar el desbastado de la superficie, el bombardeo iónico o la aplicación de una capa de imprimación.El pretratamiento garantiza que la superficie esté química y físicamente preparada para recibir el revestimiento.
-
Vaporización del material objetivo:
- Evaporación/Ablación: El material objetivo, que es la fuente del revestimiento, se coloca en una cámara de vacío.Se utilizan fuentes de alta energía, como electrones, iones o láseres, para bombardear el material objetivo y provocar su vaporización.Este proceso convierte el material sólido en una fase de vapor.
- Transporte: A continuación, los átomos o moléculas vaporizados se transportan a través de la cámara de vacío hacia el sustrato.El entorno de vacío garantiza que las partículas vaporizadas se desplacen sin interferencias de las moléculas de aire, lo que permite una deposición más controlada y uniforme.
-
Reacción con gases (si es necesario):
- Reacción: En algunos casos, los átomos vaporizados reaccionan con gases seleccionados (como nitrógeno, oxígeno o metano) introducidos en la cámara.Esta reacción forma compuestos como óxidos metálicos, nitruros o carburos, que determinan las propiedades finales del revestimiento, como la dureza, el color y la resistencia química.
- Control de las condiciones de reacción: Las condiciones de reacción, incluida la composición del gas, la presión y la temperatura, se controlan cuidadosamente para conseguir las propiedades de revestimiento deseadas.Por ejemplo, la introducción de gas nitrógeno puede dar lugar a la formación de nitruros metálicos, conocidos por su dureza y resistencia al desgaste.
-
Deposición sobre el sustrato:
- Condensación: Los átomos o moléculas vaporizados se condensan en la superficie del sustrato, formando una fina película.El proceso de deposición se controla para garantizar una cobertura y un grosor uniformes.El revestimiento se acumula capa a capa, adhiriéndose fuertemente al sustrato.
- Adhesión: El revestimiento se interpenetra con el material subyacente, creando una fuerte unión que evita que se desconche o astille.Esta es una de las principales ventajas de los revestimientos PVD, ya que proporcionan una excelente adherencia y durabilidad.
-
Control de calidad y acabado:
- Control de calidad: Tras la deposición, el sustrato revestido se somete a comprobaciones de control de calidad para garantizar que el revestimiento cumple las especificaciones requeridas.Esto puede incluir mediciones del grosor, la dureza, la adherencia y la rugosidad de la superficie.Se identifican y tratan todos los defectos o incoherencias.
- Acabado: En función de la aplicación, el sustrato revestido puede someterse a procesos de acabado adicionales para mejorar su aspecto o sus prestaciones.Esto podría incluir el pulido, el recocido o la aplicación de una capa de acabado para mejorar la resistencia a la corrosión o el aspecto estético.
-
Uso de gases inertes:
- Atmósfera inerte: A lo largo del proceso de PVD, se utilizan gases inertes como el argón para crear una atmósfera químicamente no reactiva.Esto evita reacciones no deseadas entre el material de revestimiento y el entorno, garantizando la pureza y calidad del revestimiento.El gas inerte también ayuda a eliminar los vapores residuales de la cámara una vez finalizado el proceso de deposición.
-
Entorno de vacío:
-
Condiciones de alto vacío:
Todo el proceso de PVD tiene lugar en un entorno de alto vacío.Esto es esencial por varias razones:
- Minimización de la contaminación: El vacío reduce la presencia de contaminantes que podrían interferir en el proceso de recubrimiento.
- Deposición controlada: El vacío permite un control preciso del proceso de deposición, garantizando revestimientos uniformes y de alta calidad.
- Eficiencia energética: El entorno de vacío minimiza las pérdidas de energía, haciendo que el proceso sea más eficiente.
-
Condiciones de alto vacío:
Todo el proceso de PVD tiene lugar en un entorno de alto vacío.Esto es esencial por varias razones:
-
Aplicaciones y ventajas:
- Amplia gama de aplicaciones: Los revestimientos PVD se utilizan en diversas industrias, como la automovilística, la aeroespacial, la de dispositivos médicos y la de electrónica de consumo.Se valoran por su capacidad para mejorar el rendimiento, la durabilidad y la estética de los componentes.
- Ventajas: Los revestimientos de PVD ofrecen numerosas ventajas, como alta dureza, resistencia al desgaste, resistencia a la corrosión y la posibilidad de crear acabados decorativos.También son respetuosos con el medio ambiente, ya que no utilizan productos químicos nocivos ni producen residuos peligrosos.
En resumen, el proceso de revestimiento PVD es un método muy controlado y preciso para aplicar revestimientos finos, duraderos y adherentes a una amplia gama de sustratos.Al comprender cada paso del proceso, desde la limpieza y el pretratamiento hasta la deposición y el control de calidad, se puede apreciar la complejidad y sofisticación que implica la creación de revestimientos PVD de alto rendimiento.
Tabla resumen:
Paso | Descripción |
---|---|
Limpieza y Pretratamiento | Elimina los contaminantes y prepara el sustrato para una mejor adherencia. |
Vaporización | El material objetivo se vaporiza utilizando fuentes de alta energía en una cámara de vacío. |
Reacción con los gases | Los átomos vaporizados reaccionan con los gases para formar compuestos como nitruros o carburos. |
Deposición | Los átomos vaporizados se condensan sobre el sustrato, formando un revestimiento fino y duradero. |
Control de calidad | Garantiza que el revestimiento cumple las especificaciones de espesor, dureza y adherencia. |
Gases inertes | El argón u otros gases inertes crean una atmósfera químicamente no reactiva para revestimientos de alta calidad. |
Entorno de vacío | Las condiciones de alto vacío minimizan la contaminación y garantizan una deposición precisa y uniforme. |
Aplicaciones | Se utiliza en automoción, aeroespacial, dispositivos médicos y electrónica de consumo para mejorar el rendimiento. |
Ventajas | Alta dureza, resistencia al desgaste, resistencia a la corrosión y acabados decorativos. |
¿Está listo para mejorar sus componentes con revestimientos PVD? Póngase en contacto con nosotros para obtener más información.