La tecnología de capa fina, aunque muy prometedora para aplicaciones en electrónica, óptica y revestimientos, se enfrenta a varios retos importantes. Estos retos se derivan de los intrincados procesos que intervienen en la deposición, el enfriamiento y el escalado. Entre los principales problemas se encuentran las limitaciones de temperatura durante la deposición, las tensiones indeseables generadas durante el enfriamiento y la necesidad de optimizar las velocidades de deposición al tiempo que se mejoran las propiedades mecánicas y tribológicas. Además, lograr la uniformidad, garantizar una adhesión adecuada, minimizar la contaminación y equilibrar el coste y la escalabilidad son obstáculos críticos. Abordar estos retos exige un enfoque multidisciplinar que combine la ciencia de los materiales, la ingeniería y la optimización de procesos para garantizar el éxito de la aplicación de la tecnología de capa fina en diversas industrias.
Explicación de los puntos clave:
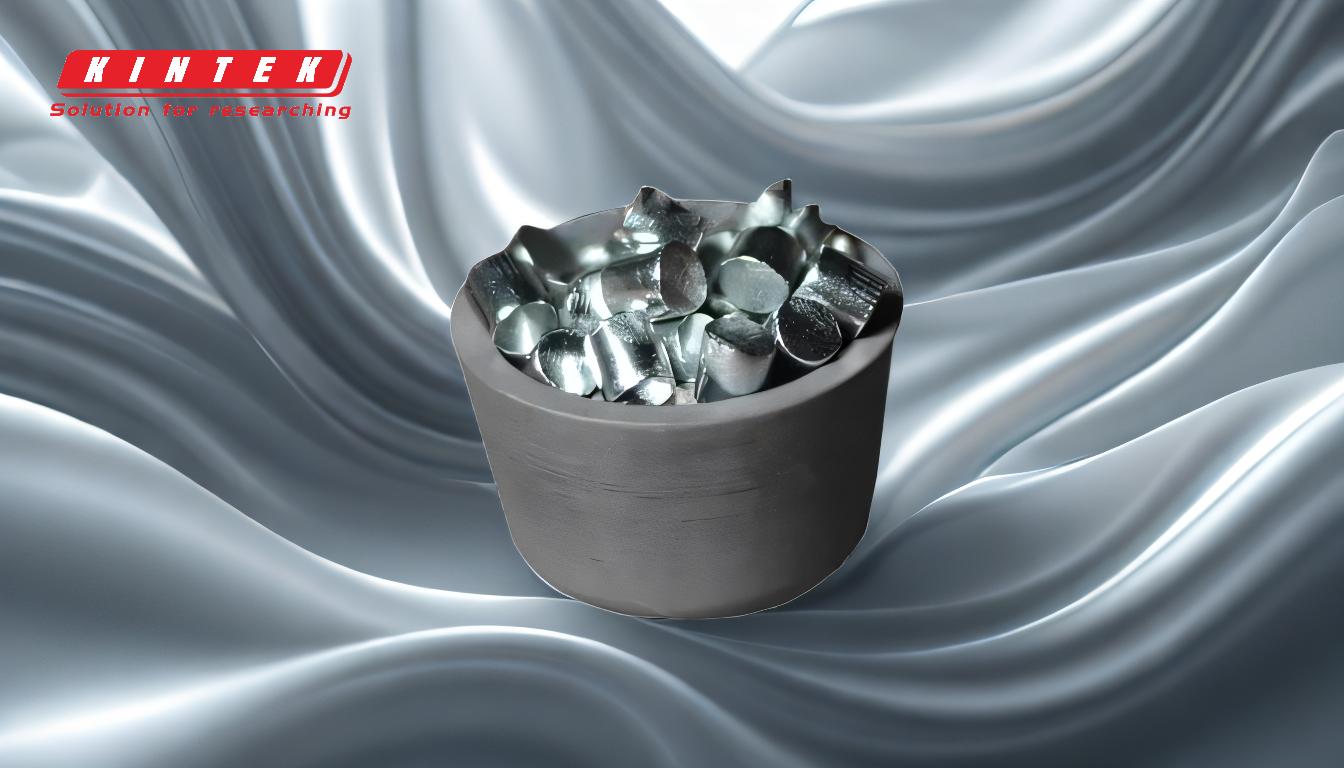
-
Limitaciones de temperatura durante la deposición:
- Los procesos de deposición de películas finas, como la deposición química en fase vapor (CVD) y la deposición física en fase vapor (PVD), suelen requerir altas temperaturas para conseguir las propiedades deseadas de la película.
- Las altas temperaturas pueden dañar los sustratos, sobre todo en el caso de materiales sensibles a la temperatura, como los polímeros o determinados semiconductores.
- La gestión de los gradientes de temperatura es crucial para evitar el estrés térmico y garantizar el crecimiento uniforme de la película.
-
Tensiones indeseables generadas durante el enfriamiento:
- Tras la deposición, el enfriamiento puede inducir tensiones térmicas debido a las diferencias en los coeficientes de expansión térmica entre la película y el sustrato.
- Estas tensiones pueden provocar grietas en la película, delaminación u otros fallos mecánicos.
- A menudo se emplean técnicas como el recocido de alivio de tensiones o el uso de capas intermedias con propiedades térmicas adecuadas para mitigar estos problemas.
-
Optimización de las tasas de deposición y mejora de las propiedades mecánicas y tribológicas:
- Alcanzar altas velocidades de deposición es esencial para la escalabilidad industrial, pero a menudo compromete la calidad de la película, como la uniformidad y las propiedades mecánicas.
- Equilibrar la velocidad de deposición con la necesidad de obtener películas de alta calidad exige un control preciso de los parámetros del proceso, como la presión, la temperatura y el caudal de gas.
- Mejorar las propiedades mecánicas (p. ej., dureza, resistencia al desgaste) y el rendimiento tribológico (p. ej., fricción, lubricación) es fundamental para las aplicaciones en revestimientos y capas protectoras.
-
Garantizar la uniformidad y el control del espesor:
- La uniformidad del grosor de la película es vital para un rendimiento constante, especialmente en aplicaciones ópticas y electrónicas.
- Las variaciones de grosor pueden provocar defectos, como agujeros de alfiler o una conductividad eléctrica desigual.
- Las técnicas de deposición avanzadas, como la deposición de capas atómicas (ALD), ofrecen un mejor control, pero pueden ser más lentas y caras.
-
Conseguir una adhesión adecuada y evitar la delaminación:
- Una fuerte adhesión entre la película y el sustrato es esencial para evitar la delaminación, que puede comprometer la funcionalidad y durabilidad de la película.
- La preparación de la superficie, como la limpieza y la rugosidad, y el uso de capas que favorecen la adhesión son estrategias habituales para mejorar la adhesión.
- La delaminación también puede deberse a tensiones mecánicas, ciclos térmicos o factores ambientales como la humedad.
-
Minimizar la contaminación:
- Los contaminantes, como el polvo, los gases o las impurezas, pueden degradar la calidad y el rendimiento de la película.
- Para minimizar la contaminación es necesario mantener un entorno de deposición limpio, utilizar materiales de gran pureza y aplicar protocolos de limpieza rigurosos.
- La contaminación puede provocar defectos, reducir la conductividad eléctrica o comprometer las propiedades ópticas.
-
Garantizar la compatibilidad del sustrato:
- La elección del material del sustrato es fundamental, ya que debe ser compatible con el proceso de deposición y la aplicación prevista.
- Los desajustes en los coeficientes de dilatación térmica, la reactividad química o las propiedades mecánicas pueden provocar el fallo de la película.
- Pueden ser necesarios tratamientos superficiales o capas intermedias para mejorar la compatibilidad.
-
Mantener la pureza y composición de la película:
- La alta pureza y el control preciso de la composición de las películas son esenciales para las aplicaciones en semiconductores, óptica y revestimientos.
- Las impurezas o las desviaciones en la composición pueden alterar las propiedades eléctricas, ópticas o mecánicas.
- Se utilizan técnicas como el sputtering o la epitaxia de haces moleculares (MBE) para conseguir películas de gran pureza con un control preciso de la composición.
-
Equilibrio entre costes y escalabilidad:
- Los procesos de deposición de películas finas deben ser rentables y escalables para las aplicaciones industriales.
- Las técnicas de alto coste, como ALD o MBE, pueden no ser viables para la producción a gran escala.
- El desarrollo de métodos de deposición rentables, la optimización de los parámetros del proceso y la reducción del desperdicio de material son fundamentales para lograr la escalabilidad.
-
Lograr la normalización:
- La normalización de los procesos de deposición, los materiales y los métodos de caracterización es esencial para obtener una calidad y un rendimiento uniformes.
- La falta de normalización puede provocar variabilidad en las propiedades de las películas y dificultar la adopción de la tecnología de película fina en la industria.
- Se necesitan esfuerzos de colaboración entre investigadores, fabricantes y organismos de normalización para establecer las mejores prácticas y directrices.
Al abordar estos retos mediante materiales innovadores, técnicas de deposición avanzadas y un riguroso control de los procesos, se puede aprovechar plenamente el potencial de la tecnología de capa fina en una amplia gama de aplicaciones.
Cuadro recapitulativo:
Desafío | Cuestiones clave | Soluciones |
---|---|---|
Limitaciones de temperatura | Las altas temperaturas pueden dañar los sustratos; el estrés térmico afecta a la uniformidad. | Controlar los gradientes de temperatura; utilizar materiales compatibles. |
Tensiones indeseables durante el enfriamiento | Las tensiones térmicas provocan grietas o delaminación. | Recocido de alivio de tensiones; uso de capas intermedias. |
Optimización de la tasa de deposición | Unas tasas elevadas pueden comprometer la calidad de la película. | Equilibrar los parámetros del proceso (presión, temperatura, caudal de gas). |
Uniformidad y control del espesor | Las variaciones provocan defectos como agujeros de alfiler. | Utilizar técnicas avanzadas como ALD para un mejor control. |
Adherencia y deslaminación | Una mala adherencia compromete la durabilidad. | Preparación de la superficie; capas que favorecen la adherencia. |
Contaminación | Las impurezas degradan la calidad de la película. | Mantener entornos limpios; utilizar materiales de gran pureza. |
Compatibilidad del sustrato | Las propiedades desiguales provocan el fallo de la película. | Tratamientos superficiales; capas intermedias. |
Pureza y composición de la película | Las impurezas alteran las propiedades eléctricas u ópticas. | Utilizar sputtering o MBE para películas de gran pureza. |
Coste y escalabilidad | El elevado coste de las técnicas dificulta la producción a gran escala. | Optimizar los procesos; reducir los residuos de material. |
Normalización | La falta de normalización genera variabilidad. | Colaborar con investigadores y fabricantes para obtener las mejores prácticas. |
¿Preparado para afrontar los retos de la capa fina? Contacte hoy mismo con nuestros expertos soluciones a medida