La soldadura por inducción, si bien es ventajosa en muchas aplicaciones industriales, tiene varias desventajas notables. Estos incluyen altos costos iniciales, complejidad en la operación, limitaciones de materiales y desafíos relacionados con el refinamiento y el mantenimiento de la composición del material. A continuación, exploramos estas desventajas en detalle, brindando una comprensión integral de las limitaciones asociadas con la soldadura por inducción.
Puntos clave explicados:
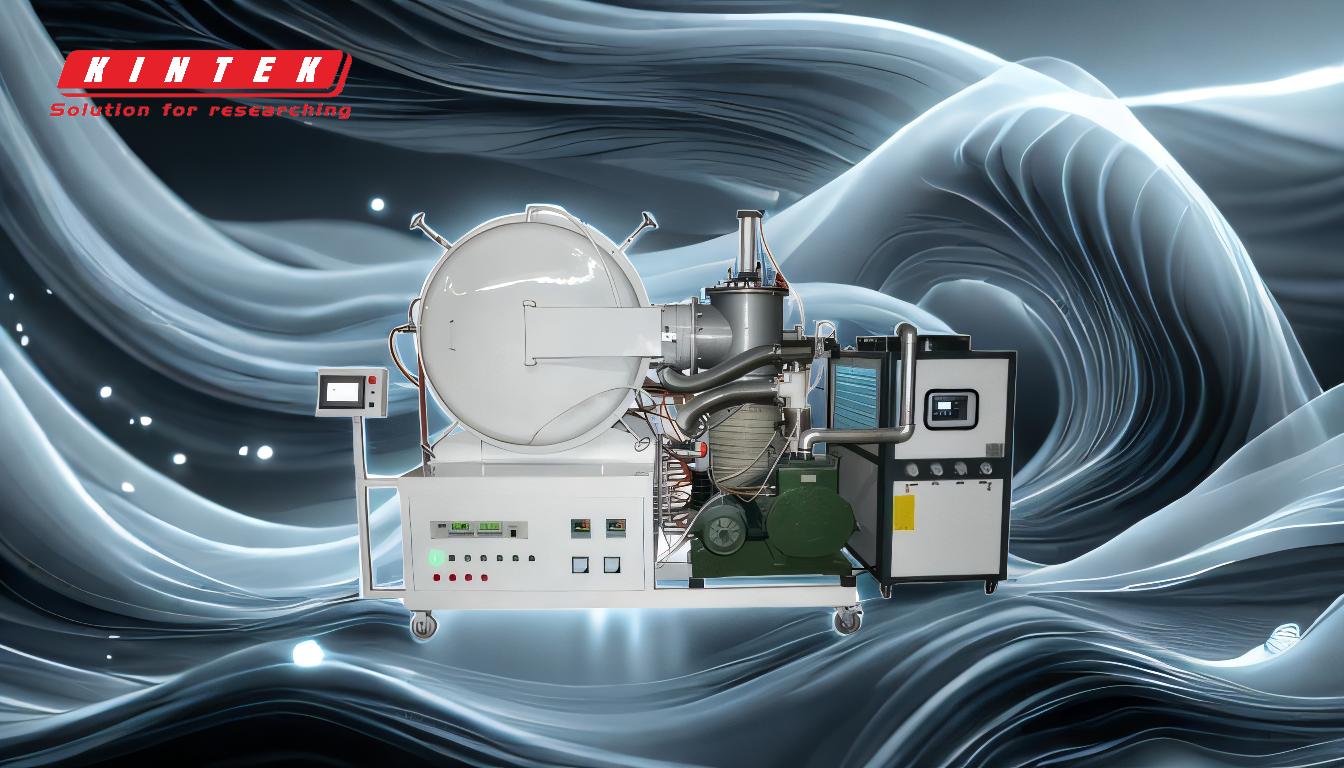
-
Alto costo inicial
- Los equipos de soldadura por inducción son significativamente más caros en comparación con los métodos de soldadura tradicionales.
- El costo incluye no sólo la máquina en sí, sino también la infraestructura asociada, como fuentes de alimentación y sistemas de refrigeración.
- Para operaciones de pequeña escala o empresas con presupuestos limitados, esta elevada inversión inicial puede ser una barrera importante para la adopción.
-
Proceso y operación complejos
- La soldadura por inducción requiere conocimientos y formación especializados para funcionar de forma eficaz.
- El proceso implica un control preciso de parámetros como la frecuencia, la potencia y el tiempo de calentamiento, lo que puede resultar un desafío para los operadores sin experiencia.
- El mantenimiento del equipo también exige experiencia técnica, lo que aumenta la complejidad operativa.
-
Limitaciones de materiales
- La soldadura por inducción no es adecuada para todos los materiales. Funciona mejor con metales conductores como cobre, latón y acero.
- Es posible que los materiales no conductores o aquellos con mala conductividad térmica no se calienten de manera uniforme o eficiente, lo que genera resultados inconsistentes.
- Ciertos materiales también pueden degradarse u oxidarse bajo las altas temperaturas generadas por el calentamiento por inducción.
-
Falta de capacidad de refinación
- La soldadura por inducción no tiene la capacidad de refinar o purificar materiales durante el proceso.
- Los materiales utilizados deben estar previamente libres de óxidos y contaminantes, ya que estos pueden afectar negativamente a la calidad de la unión soldada.
- Esta limitación requiere pasos de preprocesamiento adicionales, lo que aumenta el tiempo y el costo.
-
Oxidación y pérdida de elementos de aleación
- Las altas temperaturas durante la soldadura por inducción pueden provocar la oxidación de ciertos materiales, particularmente aquellos con elementos de aleación reactivos.
- La oxidación puede provocar la pérdida de elementos de aleación críticos, que tal vez sea necesario volver a agregarlos para mantener las propiedades deseadas del material.
- Este problema puede comprometer la integridad y el rendimiento del producto final.
-
Consumo y eficiencia energética
- Los sistemas de soldadura por inducción pueden consumir mucha energía, especialmente cuando funcionan a altas frecuencias o niveles de potencia.
- Si bien el calentamiento por inducción es generalmente eficiente, el consumo total de energía puede ser aún mayor en comparación con otros métodos de soldadura, según la aplicación.
-
Flexibilidad limitada para piezas pequeñas o complejas
- La soldadura por inducción es menos eficaz para piezas pequeñas, intrincadas o de forma irregular debido a las dificultades para lograr un calentamiento uniforme.
- Es posible que se requieran diseños de bobinas personalizados para aplicaciones específicas, lo que aumenta la complejidad y el costo.
-
Preocupaciones de seguridad
- Las altas temperaturas y los campos electromagnéticos generados durante la soldadura por inducción plantean riesgos de seguridad para los operadores.
- Para mitigar estos riesgos son necesarias medidas de seguridad adecuadas, como blindajes y equipos de protección.
En resumen, si bien la soldadura por inducción ofrece ventajas como velocidad, precisión y calentamiento localizado, sus desventajas (incluidos los altos costos, las limitaciones de materiales y la complejidad operativa) deben considerarse cuidadosamente. Estos factores lo hacen menos adecuado para determinadas aplicaciones o empresas con recursos limitados. Comprender estas limitaciones es crucial para tomar decisiones informadas sobre si la soldadura por inducción es la opción correcta para un caso de uso específico.
Tabla resumen:
Desventaja | Detalles |
---|---|
Alto costo inicial | Equipos e infraestructura costosos; barrera para operaciones a pequeña escala. |
Proceso y operación complejos | Requiere formación especializada y control preciso de parámetros. |
Limitaciones de materiales | Lo mejor para metales conductores; Desafíos con materiales no conductores. |
Falta de capacidad de refinación | Sin purificación de material durante el proceso; Se requiere procesamiento previo. |
Pérdida por oxidación y aleación | Las altas temperaturas provocan oxidación y pérdida de elementos de aleación críticos. |
Consumo de energía | Puede consumir mucha energía, especialmente a altas frecuencias. |
Flexibilidad limitada | Menos eficaz para piezas pequeñas o complejas; Es posible que se necesiten bobinas personalizadas. |
Preocupaciones de seguridad | Las altas temperaturas y los campos electromagnéticos suponen riesgos para los operadores. |
¿Necesita ayuda para decidir si la soldadura por inducción es adecuada para su aplicación? Póngase en contacto con nuestros expertos hoy para asesoramiento personalizado!