El proceso de sinterización es un método complejo de tratamiento térmico que se utiliza para unir partículas en una masa sólida y su resultado está influenciado por una variedad de factores. Estos factores incluyen la atmósfera de sinterización, la temperatura, la velocidad de enfriamiento, la presión aplicada, el tamaño de las partículas, la composición, la velocidad de calentamiento y parámetros específicos del proceso, como el espesor de la capa, la velocidad de la máquina y el volumen de aire. Cada una de estas variables juega un papel fundamental en la determinación de las propiedades finales del producto sinterizado, como la resistencia a la tracción, la resistencia a la fatiga por flexión y la energía de impacto. Comprender y controlar estos factores es esencial para optimizar el proceso de sinterización y lograr las características deseadas del material.
Puntos clave explicados:
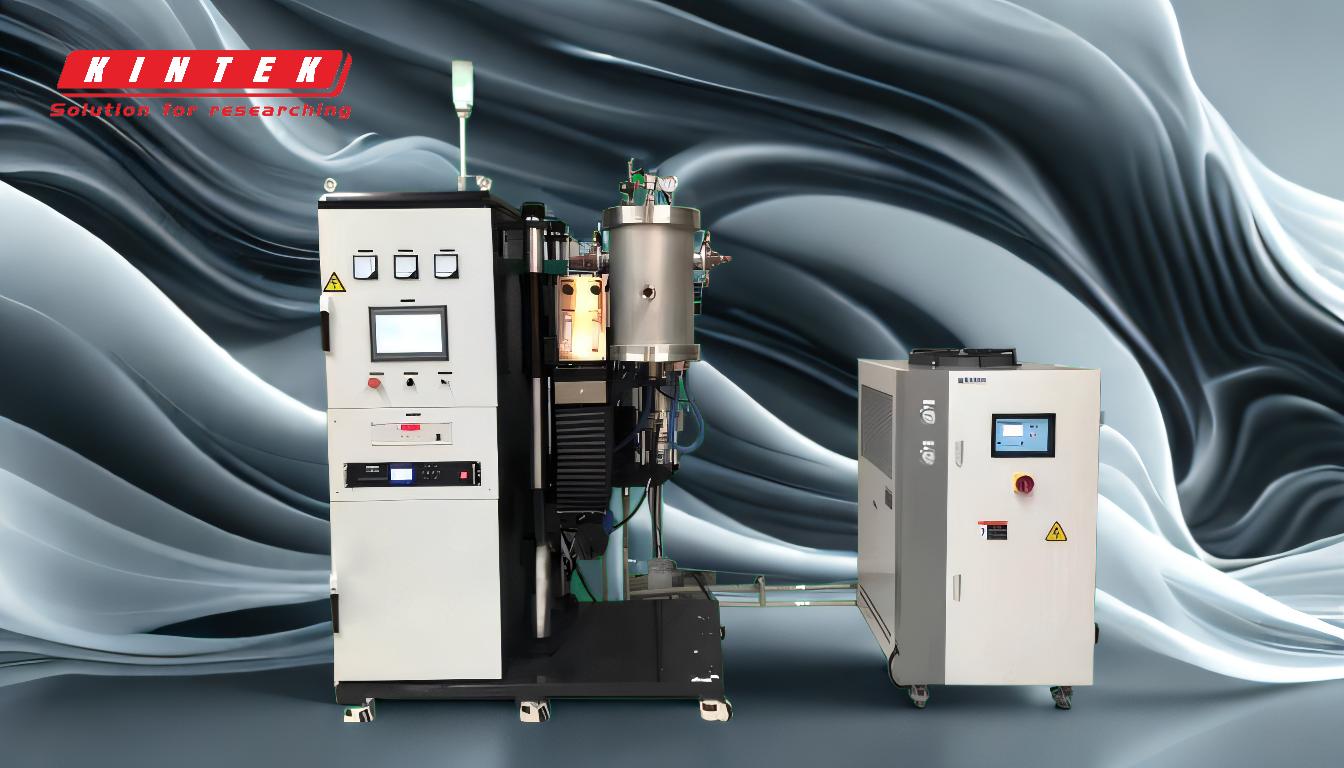
-
Atmósfera de sinterización:
- La atmósfera en la que se produce la sinterización (por ejemplo, aire, vacío, argón o nitrógeno) afecta significativamente el proceso. Por ejemplo, un vacío o una atmósfera inerte pueden prevenir la oxidación y la contaminación, lo cual es crucial para materiales sensibles al oxígeno u otros gases reactivos.
- La elección de la atmósfera también puede afectar a la cinética de sinterización y a las propiedades finales del material, como la densidad y la resistencia mecánica.
-
Temperatura:
- La temperatura es uno de los factores más críticos en la sinterización. Las temperaturas más altas generalmente aumentan la velocidad de difusión, lo que conduce a una mejor unión y densificación de las partículas.
- Sin embargo, temperaturas excesivamente altas pueden provocar un crecimiento de grano no deseado o la formación de fases no deseadas, que pueden degradar las propiedades del material.
- La temperatura de sinterización óptima depende del material a procesar y de las propiedades finales deseadas.
-
Tasa de enfriamiento:
- La velocidad de enfriamiento después de la sinterización puede influir en la microestructura y las propiedades mecánicas del material. El enfriamiento rápido puede dar como resultado una estructura de grano más fina, lo que puede mejorar la resistencia y la tenacidad.
- Por el contrario, velocidades de enfriamiento más lentas pueden permitir transformaciones de fase más controladas, lo que puede ser beneficioso para ciertos materiales.
-
Presión aplicada:
- La presión aplicada durante la sinterización (como en el prensado en caliente o la sinterización por plasma por chispa) puede mejorar la densificación al promover la reorganización de las partículas y reducir la porosidad.
- El uso de presión también puede permitir temperaturas de sinterización más bajas, lo que puede resultar ventajoso para materiales sensibles a las altas temperaturas.
-
Tamaño y composición de partículas:
- Los tamaños de partículas más pequeños generalmente conducen a una mejor densificación porque tienen una relación superficie-volumen más alta, lo que mejora la difusión y la unión.
- La composición de las partículas, incluida la presencia de aditivos o impurezas, también puede afectar el comportamiento de sinterización. Las composiciones homogéneas tienden a promover una densificación más uniforme.
-
Tasa de calentamiento:
- La velocidad a la que se calienta el material puede influir en el proceso de sinterización. Una velocidad de calentamiento más lenta puede permitir una distribución de temperatura más uniforme y reducir las tensiones térmicas, mientras que una velocidad de calentamiento más rápida puede ser beneficiosa para ciertos materiales que requieren una densificación rápida.
-
Parámetros del proceso:
- Los parámetros específicos del proceso, como el espesor de la capa, la velocidad de la máquina, el volumen de aire y el nivel de vacío, son críticos en los procesos de sinterización industrial. Por ejemplo, el espesor de la capa (normalmente 250-500 mm) y la velocidad de la máquina (1,5-4 m/min) deben controlarse cuidadosamente para garantizar que la alimentación de sinterización se queme en el punto final programado.
- El volumen de aire (normalmente 3200 m³ por tonelada de mineral de sinterización) y el nivel de vacío también son importantes, ya que afectan la eficiencia del proceso de sinterización y la calidad del producto final.
-
Control del punto final de sinterización:
- El punto final del proceso de sinterización debe controlarse cuidadosamente para garantizar que el material alcance el nivel deseado de densificación sin sinterizar excesivamente, lo que puede provocar defectos o reducir las propiedades mecánicas.
- Factores como el área de sinterización (calculada como 70-90 m³/(cm²·min)) y la capacidad del ventilador, la resistencia del aire, la permeabilidad del aire y la pérdida por fuga de aire desempeñan un papel en la determinación del punto final de sinterización óptimo.
En resumen, el proceso de sinterización se rige por una compleja interacción de factores, cada uno de los cuales debe controlarse cuidadosamente para lograr las propiedades deseadas del material. Al comprender y optimizar estos factores, los fabricantes pueden producir productos sinterizados de alta calidad con propiedades físicas y mecánicas personalizadas.
Tabla resumen:
Factor | Impacto en el proceso de sinterización |
---|---|
Atmósfera de sinterización | Afecta la oxidación, la contaminación y las propiedades finales del material (p. ej., densidad, resistencia). |
Temperatura | Las temperaturas más altas mejoran la difusión y la unión; Las temperaturas excesivas pueden provocar crecimiento o defectos del grano. |
Tasa de enfriamiento | Influye en la microestructura; el enfriamiento rápido mejora la resistencia, el enfriamiento más lento ayuda al control de fase. |
Presión aplicada | Mejora la densificación, reduce la porosidad y permite temperaturas de sinterización más bajas. |
Tamaño de partícula | Las partículas más pequeñas mejoran la densificación debido a una mayor relación superficie-volumen. |
Composición | Las composiciones homogéneas favorecen una densificación uniforme. |
Tasa de calentamiento | Afecta la distribución de la temperatura y las tensiones térmicas; ritmos más lentos reducen el estrés. |
Parámetros del proceso | El espesor de la capa, la velocidad de la máquina, el volumen de aire y el nivel de vacío afectan la eficiencia y la calidad. |
Control de punto final | Garantiza una densificación óptima sin defectos ni propiedades mecánicas reducidas. |
¿Listo para optimizar su proceso de sinterización? Póngase en contacto con nuestros expertos hoy ¡Para soluciones personalizadas!