La sinterización en fase líquida (LPS) es un proceso muy utilizado en pulvimetalurgia y cerámica, en el que una fase líquida facilita la densificación y la unión de partículas sólidas. Aunque ofrece ventajas como una mejor densificación y la capacidad de producir formas complejas, también presenta varios inconvenientes. Entre ellos están los elevados costes debidos al costoso equipo y al consumo de energía, las dificultades para conseguir propiedades uniformes y los posibles defectos, como el alabeo o el pandeo. Además, el proceso puede requerir materiales especializados y un control preciso de los parámetros, lo que lo hace complejo y menos adecuado para la producción a gran escala o para aplicaciones que requieran una gran resistencia mecánica.
Explicación de los puntos clave:
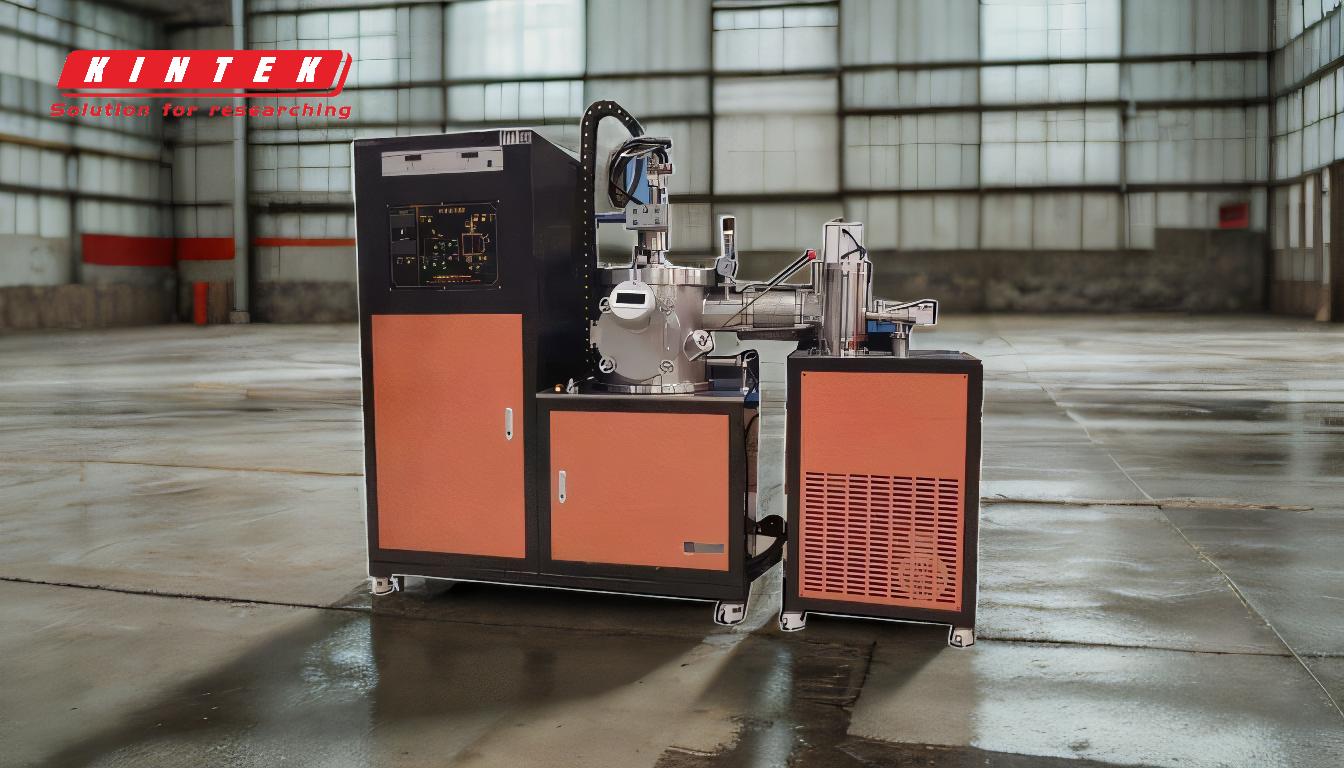
-
Costes operativos y de equipamiento elevados
- La sinterización en fase líquida suele requerir hornos especializados capaces de mantener temperaturas y atmósferas precisas, que son caros de adquirir y mantener.
- El proceso exige un importante consumo de energía, sobre todo para la sinterización a alta temperatura, lo que se traduce en mayores costes operativos.
- Para manejar y mantener el equipo se necesitan conocimientos profesionales, lo que aumenta los costes de mano de obra.
-
Limitaciones de materiales y procesos
- El proceso puede requerir materiales o aditivos específicos para formar la fase líquida, lo que puede aumentar los costes de material.
- Lograr una distribución uniforme de la fase líquida es un reto que puede dar lugar a propiedades incoherentes en el producto final.
- El proceso puede no ser adecuado para materiales sensibles a las altas temperaturas o propensos a una contracción excesiva.
-
Posibilidad de defectos
- El alabeo y el pandeo son problemas comunes durante la sinterización en fase líquida debido a la gravedad o a la fricción, lo que puede provocar imprecisiones dimensionales o defectos en la pieza final.
- Una contracción excesiva durante la sinterización puede complicar el proceso de diseño y producción, lo que exige una cuidadosa compensación durante las fases iniciales.
-
Limitaciones de tamaño y complejidad
- La sinterización en fase líquida puede tener limitaciones a la hora de producir piezas grandes o de formas complejas, de forma similar a otros procesos pulvimetalúrgicos.
- El proceso puede no alcanzar la misma resistencia mecánica o ductilidad que los métodos tradicionales de fundición o forja, lo que limita su uso en aplicaciones de alto rendimiento.
-
Baja productividad y rendimiento
- El proceso de sinterización suele requerir mucho tiempo, con ciclos largos que reducen la productividad global.
- La producción por horno suele ser pequeña, lo que la hace menos eficiente para la producción a gran escala en comparación con otros métodos de fabricación.
-
Complejidad técnica
- El proceso requiere un control preciso de parámetros como la temperatura, la presión y la atmósfera, lo que lo hace técnicamente exigente.
- Pueden ser necesarios ajustes para diferentes materiales, lo que añade complejidad a la operación y aumenta el riesgo de errores.
En resumen, aunque el sinterizado en fase líquida ofrece ventajas únicas, sus inconvenientes -como los elevados costes, la complejidad técnica y los posibles defectos- lo hacen menos adecuado para determinadas aplicaciones. Es esencial tener muy en cuenta estos factores a la hora de elegir este proceso para la fabricación.
Cuadro recapitulativo:
Drawback | Principales retos |
---|---|
Costes de equipamiento elevados | Hornos especializados caros, alto consumo de energía y costes de mano de obra. |
Limitaciones materiales | Requiere aditivos específicos, distribución desigual de la fase líquida y problemas de material. |
Posibles defectos | Alabeo, pandeo y contracción excesiva durante la sinterización. |
Límites de tamaño y complejidad | Capacidad limitada para producir piezas grandes o complejas con alta resistencia mecánica. |
Baja productividad | Proceso largo con poca producción por horno. |
Complejidad técnica | Se requiere un control preciso de la temperatura, la presión y la atmósfera. |
¿Necesita ayuda para superar los retos de la sinterización en fase líquida? Contacte hoy mismo con nuestros expertos soluciones a medida