La sinterización es un proceso fundamental en la ciencia y la fabricación de materiales, que se utiliza para transformar materiales en polvo en cuerpos densos y sólidos aplicando calor y presión por debajo del punto de fusión del material.Este proceso se emplea ampliamente en industrias como la cerámica, la pulvimetalurgia y los plásticos.El proceso de sinterización suele dividirse en tres etapas principales: composición del polvo, compactación del polvo y sinterización o cocción.Cada etapa desempeña un papel fundamental a la hora de garantizar la integridad estructural, la densidad y el rendimiento del producto final.Comprender estas etapas es esencial para optimizar el proceso de sinterización y lograr resultados de alta calidad.
Explicación de los puntos clave:
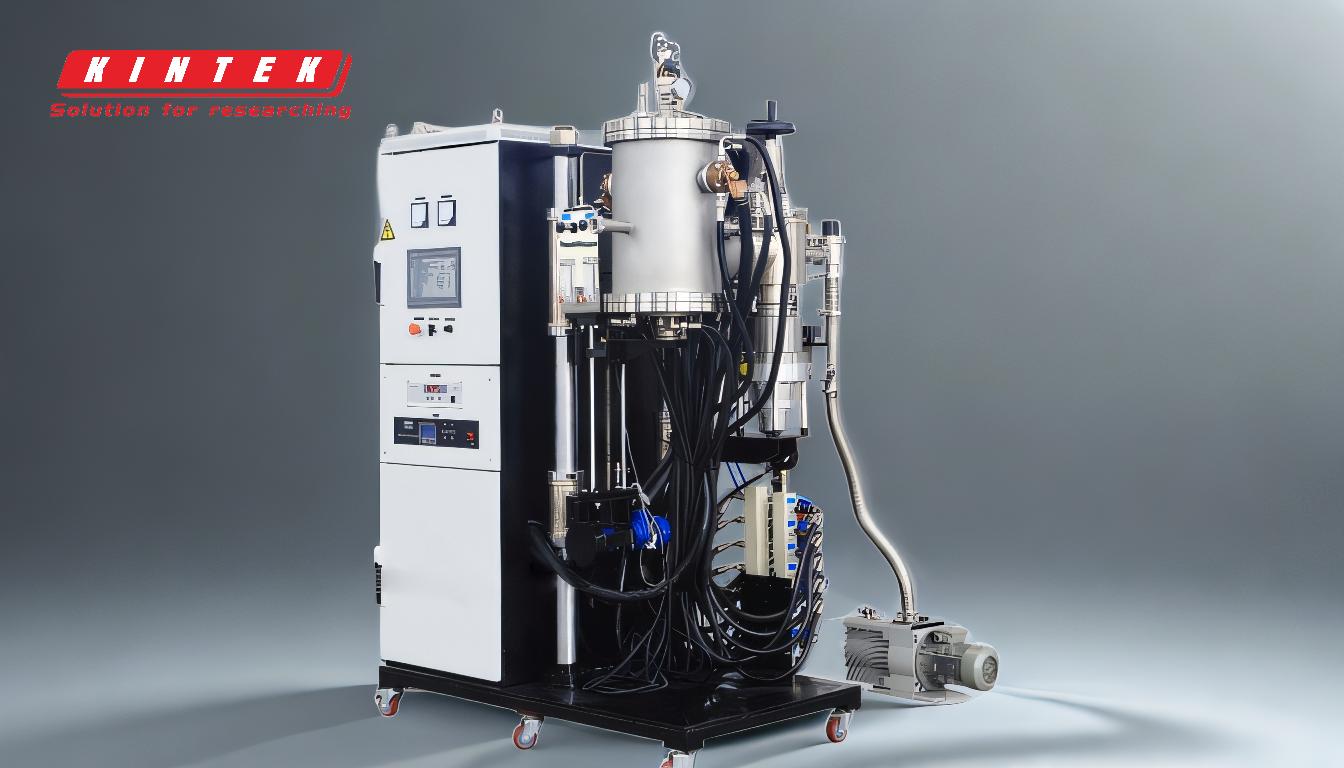
-
Composición de la pólvora:
- Definición:Esta es la etapa inicial en la que se preparan y mezclan las materias primas para crear una mezcla de polvo uniforme.
-
Proceso:
- El agua, el defloculante, el aglutinante y el polvo cerámico sin cocer se mezclan para formar una pasta.
- A continuación, la pasta se seca por pulverización para obtener un polvo fluido.
-
Objetivo:
- Garantiza la uniformidad del tamaño y la composición de las partículas.
- Prepara el material para la siguiente fase de compactación.
-
Consideraciones:
- La elección del aglutinante y el defloculante afecta a la fluidez y las propiedades de compactación del polvo.
- Una mezcla adecuada es crucial para evitar defectos en el producto final.
-
Compactación del polvo:
- Definición:Esta etapa consiste en la densificación mecánica del polvo para formar una pieza "verde", que es una forma presinterizada.
-
Proceso:
- El polvo se compacta mediante técnicas de prensado en molde frío o caliente.
- Se aplica presión para eliminar los huecos y conseguir la forma y densidad deseadas.
-
Propósito:
- Crea una pieza verde con suficiente resistencia para manipularla antes de la sinterización.
- Reduce la porosidad y aumenta la densidad, lo que es fundamental para las propiedades mecánicas del producto final.
-
Consideraciones:
- La presión aplicada debe controlarse cuidadosamente para evitar grietas o una densidad desigual.
- La pieza verde debe tener suficiente resistencia para soportar la manipulación y el transporte al horno de sinterización.
-
Sinterización o cocción:
- Definición:Etapa final en la que la pieza verde se calienta en un entorno controlado para fusionar las partículas.
-
Proceso:
- La pieza verde se introduce en un horno de sinterización, donde se calienta a una temperatura inferior al punto de fusión del material.
- Durante el calentamiento, las partículas sufren difusión, lo que provoca la formación de cuellos y la densificación.
- A continuación, el material se enfría para solidificarse en una estructura rígida y cohesiva.
-
Objetivo:
- Consigue la densidad final y las propiedades mecánicas del material.
- Une las partículas para formar una masa sólida sin fundir todo el material.
-
Consideraciones:
- El control de la temperatura es fundamental para evitar la sinterización excesiva o insuficiente.
- La atmósfera del horno (por ejemplo, reductora, oxidante o inerte) puede afectar a las propiedades finales del producto sinterizado.
- Las velocidades de enfriamiento deben controlarse para evitar tensiones térmicas que puedan provocar grietas.
-
Procesos posteriores a la sinterización:
- Definición:Tratamientos adicionales que pueden aplicarse después de la sinterización para mejorar las propiedades del producto final.
-
Proceso:
- Tratamiento térmico para mejorar las propiedades mecánicas.
- Acabado superficial (por ejemplo, esmerilado, pulido) para conseguir la calidad superficial deseada.
- Recubrimiento o impregnación para mejorar la resistencia al desgaste u otras propiedades.
-
Finalidad:
- Mejora aún más las propiedades mecánicas, térmicas o químicas del producto sinterizado.
- Garantiza que el producto cumple los requisitos específicos de la aplicación.
-
Consideraciones:
- La elección de los tratamientos posteriores al sinterizado depende del material y del uso previsto del producto.
- Estos procesos pueden añadir un valor significativo, pero también aumentar los costes de producción.
-
Aplicaciones y materiales:
-
Aplicaciones:
- La sinterización se utiliza en una amplia gama de industrias, como la automovilística, aeroespacial, electrónica y de dispositivos médicos.
- Los productos más comunes son engranajes, rodamientos, filtros y herramientas de corte.
-
Materiales:
- Metales (por ejemplo, hierro, cobre, wolframio).
- Cerámicas (por ejemplo, alúmina, circonio).
- Plásticos (por ejemplo, PTFE, PEEK).
-
Consideraciones:
- La elección del material depende de las propiedades deseadas del producto final (por ejemplo, resistencia, resistencia al desgaste, conductividad térmica).
- Los distintos materiales pueden requerir condiciones de sinterización específicas (por ejemplo, temperatura, atmósfera).
-
Aplicaciones:
En conclusión, el proceso de sinterización es un procedimiento complejo que consta de varias etapas y que transforma materiales pulverulentos en cuerpos densos y sólidos.Cada etapa -composición del polvo, compactación del polvo y sinterización- desempeña un papel crucial en la determinación de las propiedades y el rendimiento del producto final.Comprender estas etapas y sus matices es esencial para optimizar el proceso de sinterización y lograr resultados de alta calidad en diversas aplicaciones industriales.
Tabla resumen:
Etapa | Descripción | Consideraciones clave |
---|---|---|
Composición del polvo | Mezcla de materias primas para crear una mezcla de polvo uniforme. | Elección del aglutinante y el defloculante, mezcla adecuada para evitar defectos. |
Compactación del polvo | Densificación del polvo para formar una pieza "verde" presinterizada. | Presión controlada, resistencia de la pieza verde para su manipulación. |
Sinterización/cocción | Calentamiento de la pieza verde para fusionar las partículas sin fundirlas. | Control de la temperatura, atmósfera del horno, velocidad de enfriamiento para evitar el agrietamiento. |
Post-sinterización | Tratamientos adicionales (tratamiento térmico, acabado superficial, revestimiento). | Tratamientos específicos de materiales y aplicaciones, consideraciones sobre costes. |
Aplicaciones | Utilizadas en automoción, aeroespacial, electrónica y dispositivos médicos. | Elección del material (metales, cerámicas, plásticos) en función de las propiedades deseadas. |
Optimice su proceso de sinterización para obtener resultados de alta calidad. contacte hoy mismo con nuestros expertos ¡!