La galvanoplastia y el depósito físico en fase vapor (PVD) son dos técnicas distintas de recubrimiento de superficies que se utilizan para mejorar las propiedades de los materiales, como la resistencia a la corrosión, la dureza y el atractivo estético.La galvanoplastia consiste en la deposición electroquímica de una capa metálica sobre un sustrato utilizando una solución electrolítica, mientras que el PVD utiliza procesos físicos como la evaporación o el sputtering para depositar películas finas en un entorno de vacío.El PVD ofrece ventajas como una mayor resistencia a la corrosión, mejor adherencia y seguridad medioambiental, ya que no depende de productos químicos tóxicos.La galvanoplastia, en cambio, suele ser más rentable y adecuada para revestimientos más gruesos, pero puede implicar el uso de productos químicos peligrosos y producir acabados menos duraderos.
Explicación de los puntos clave:
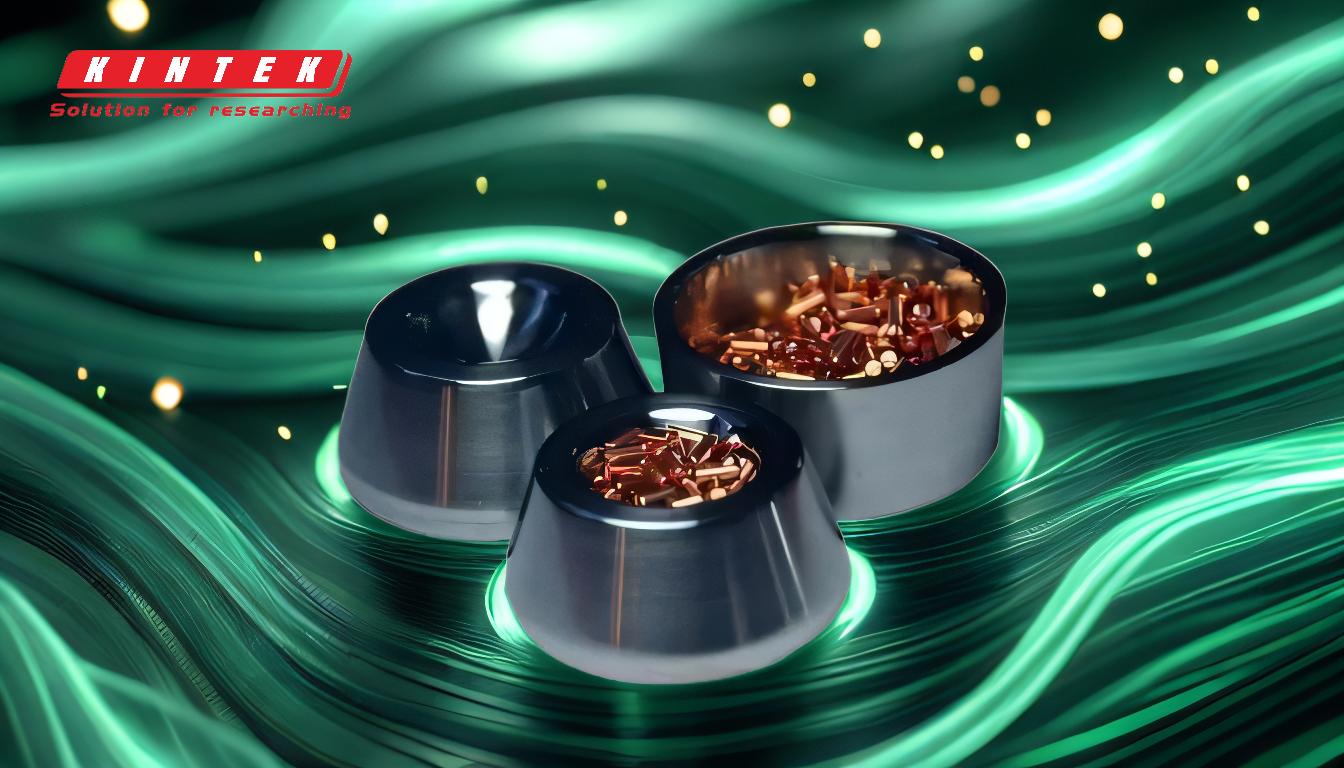
-
Mecanismo del proceso:
- Galvanoplastia:Se trata de un proceso electroquímico en el que se utiliza una solución de iones metálicos (electrolito) para depositar una capa de metal sobre un sustrato.Una corriente eléctrica reduce los iones metálicos del electrolito y hace que se adhieran al sustrato.
- PVD:El PVD es un proceso físico que consiste en vaporizar un material sólido (blanco) en una cámara de vacío.Los átomos o moléculas vaporizados se condensan en el sustrato para formar un revestimiento fino y uniforme.Se suelen utilizar técnicas como la pulverización catódica y la evaporación.
-
Espesor y uniformidad del revestimiento:
- Galvanoplastia:Normalmente produce revestimientos más gruesos, que pueden oscilar entre unos pocos micrómetros y varios milímetros.Sin embargo, conseguir un grosor uniforme, especialmente en geometrías complejas, puede ser todo un reto.
- PVD:Crea revestimientos mucho más finos, a menudo en el rango de nanómetros a micrómetros.Los revestimientos PVD son muy uniformes y pueden adaptarse a formas complejas gracias al proceso de deposición en línea recta.
-
Adherencia y durabilidad:
- Galvanoplastia:La adherencia de los revestimientos galvánicos depende de la preparación de la superficie y de las condiciones electroquímicas.Aunque duraderos, estos revestimientos pueden ser propensos a pelarse o descascarillarse bajo tensión.
- PVD:Ofrece una adherencia superior gracias a la unión a nivel atómico entre el revestimiento y el sustrato.Los revestimientos de PVD son muy duraderos y resistentes al desgaste, la corrosión y la oxidación.
-
Consideraciones medioambientales y de seguridad:
- Galvanoplastia:A menudo implica el uso de productos químicos peligrosos, como cianuros y ácidos, que requieren una manipulación y eliminación cuidadosas.El proceso puede generar residuos tóxicos y plantear riesgos medioambientales.
- PVD:Generalmente se considera más seguro y respetuoso con el medio ambiente, ya que no utiliza productos químicos tóxicos.El proceso se realiza al vacío, lo que minimiza la exposición a sustancias peligrosas.
-
Aplicaciones:
- Galvanoplastia:Comúnmente utilizado en industrias que requieren revestimientos gruesos, decorativos o funcionales, como la automoción (cromado), la electrónica (chapado en oro) y la joyería.
- PVD:Preferido para aplicaciones que requieren revestimientos de alto rendimiento, como herramientas de corte, dispositivos médicos y componentes aeroespaciales, donde la durabilidad, la resistencia a la corrosión y la precisión son fundamentales.
-
Coste y escalabilidad:
- Galvanoplastia:Generalmente es más rentable para la producción a gran escala y los revestimientos más gruesos.Se utiliza mucho en la producción en serie debido a su coste relativamente bajo y su alto rendimiento.
- PVD:Más caro debido a la necesidad de equipos de vacío y procesos especializados.Sin embargo, es altamente escalable para aplicaciones de precisión y ofrece ventajas económicas a largo plazo debido a la durabilidad de los revestimientos.
-
Compatibilidad de materiales:
- Galvanoplastia:Limitado a metales que pueden depositarse electroquímicamente.Los sustratos no conductores requieren un pretratamiento conductor.
- PVD:Puede depositar una amplia gama de materiales, incluidos metales, cerámicas y compuestos, tanto en sustratos conductores como no conductores.
-
Acabado superficial y estética:
- Galvanoplastia:Proporciona un acabado brillante y reflectante, por lo que es ideal para aplicaciones decorativas.Sin embargo, el acabado puede degradarse con el tiempo debido a la exposición ambiental.
- PVD:Ofrece un acabado mate o satinado, que puede adaptarse a requisitos estéticos específicos.Los revestimientos de PVD son más resistentes a la decoloración y el deslustre.
Al conocer estas diferencias clave, los compradores pueden tomar decisiones informadas basadas en los requisitos específicos de su aplicación, como la durabilidad, el impacto medioambiental y las consideraciones de coste.
Cuadro sinóptico:
Aspecto | Galvanoplastia | PVD |
---|---|---|
Mecanismo del proceso | Deposición electroquímica utilizando una solución electrolítica. | Vaporización física en un entorno de vacío. |
Espesor del revestimiento | Recubrimientos más gruesos (de micrómetros a milímetros). | Recubrimientos más finos (nanómetros a micrómetros). |
Adherencia y durabilidad | Durable pero puede pelarse o descascarillarse bajo tensión. | Adherencia superior, muy duradera y resistente al desgaste y la corrosión. |
Impacto medioambiental | Utiliza productos químicos peligrosos; genera residuos tóxicos. | Respetuoso con el medio ambiente; no utiliza productos químicos tóxicos. |
Aplicaciones | Automoción, electrónica, joyería (revestimientos gruesos y decorativos). | Herramientas de corte, dispositivos médicos, aeroespacial (revestimientos de alto rendimiento). |
Coste | Rentable para la producción a gran escala. | Coste inicial más elevado pero ventajas de durabilidad a largo plazo. |
Compatibilidad de materiales | Limitada a metales; los sustratos no conductores requieren tratamiento previo. | Compatible con metales, cerámica y materiales compuestos. |
Acabado superficial | Acabado brillante y reflectante; puede degradarse con el tiempo. | Acabado mate o satinado; resistente a la decoloración y el deslustre. |
¿Aún no sabe qué técnica de revestimiento es la adecuada para su proyecto? Póngase en contacto con nuestros expertos para un asesoramiento personalizado.