La pérdida de fusión en un horno de inducción se refiere a la reducción de la cantidad de metal durante el proceso de fusión, debido principalmente a factores como la oxidación, la evaporación y la formación de escoria.Sin embargo, los hornos de inducción, en particular los que utilizan horno de inducción IGBT están diseñados para minimizar estas pérdidas.Lo consiguen mediante un calentamiento eficaz, entornos controlados y una automatización avanzada.El proceso garantiza un calentamiento rápido, una oxidación reducida y una contaminación mínima, lo que convierte a los hornos de inducción en una solución rentable y eficaz para la fusión de metales.
Explicación de los puntos clave:
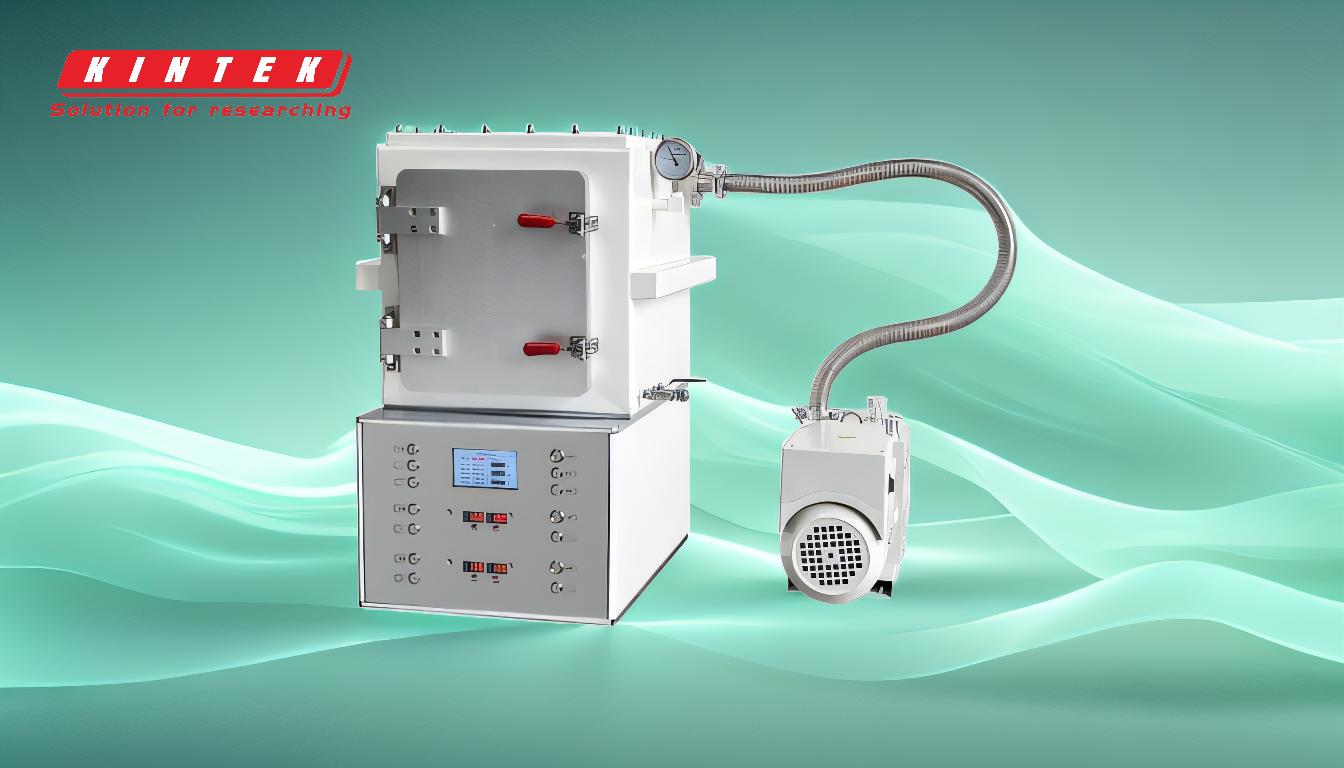
-
¿Qué es la pérdida por fusión?
- La pérdida por fusión se refiere a la reducción de la cantidad de metal durante el proceso de fusión.Puede producirse por oxidación, evaporación o formación de escoria.En los métodos de fusión tradicionales, como los que utilizan hornos eléctricos, estas pérdidas pueden ser significativas debido a la exposición prolongada a altas temperaturas y a contaminantes como las barras de carbono.
-
Cómo minimizan las pérdidas los hornos de inducción:
-
Los hornos de inducción, especialmente los que utilizan
horno de inducción IGBT
están diseñados para minimizar las pérdidas por fusión.Lo consiguen mediante
- Calentamiento rápido: El uso de corrientes de alta frecuencia garantiza un calentamiento rápido del metal, reduciendo el tiempo de exposición a altas temperaturas y minimizando la oxidación.
- Entorno controlado: La bobina de tubo hueco de cobre de gran calibre con doble aislamiento y circulación de agua fría evita el sobrecalentamiento y mantiene una temperatura estable, reduciendo aún más la oxidación y la evaporación.
- Sin varillas de carbono: A diferencia de los métodos tradicionales, los hornos de inducción no requieren varillas de carbono, que pueden causar contaminación y pérdida adicional de metal.
-
Los hornos de inducción, especialmente los que utilizan
horno de inducción IGBT
están diseñados para minimizar las pérdidas por fusión.Lo consiguen mediante
-
Factores que influyen en la pérdida por fusión:
-
Varios factores pueden influir en la magnitud de la pérdida por fusión en cualquier horno, entre ellos:
- La temperatura: Las temperaturas más altas pueden aumentar la velocidad de oxidación y evaporación.
- La presión: La presión dentro del horno puede afectar a la velocidad de pérdida de metal.
- Impurezas y escorias: La presencia de impurezas puede dar lugar a la formación de escorias, que pueden atrapar parte del metal, dando lugar a pérdidas.
- Oxidantes: La presencia de oxidantes puede acelerar el proceso de oxidación, provocando una mayor pérdida de metal.
-
Varios factores pueden influir en la magnitud de la pérdida por fusión en cualquier horno, entre ellos:
-
Ventajas de los hornos de inducción en la reducción de la pérdida por fusión:
- Eficacia: Los hornos de inducción son altamente eficientes, con ciclos rápidos de calentamiento y enfriamiento que reducen el tiempo de exposición del metal a altas temperaturas.
- Pureza: La agitación automática garantiza que el metal permanezca puro y libre de contaminantes, reduciendo la formación de escoria y otros productos de desecho.
- Rentabilidad: Al reducir el consumo de energía y minimizar los productos de desecho, los hornos de inducción disminuyen el coste global de funcionamiento.
-
Comparación con los métodos tradicionales:
- Los métodos de fusión tradicionales, como los que utilizan hornos eléctricos, suelen dar lugar a mayores pérdidas por fusión debido a la exposición prolongada a altas temperaturas y al uso de barras de carbono.Los hornos de inducción, en cambio, ofrecen un entorno más controlado, lo que reduce significativamente estas pérdidas.
En resumen, la pérdida por fusión en un horno de inducción, en particular los que utilizan horno de inducción IGBT es significativamente inferior en comparación con los métodos tradicionales.El calentamiento rápido, el entorno controlado y la ausencia de contaminantes como las varillas de carbono garantizan que el metal se mantenga puro y se minimicen las pérdidas.Esto convierte a los hornos de inducción en la opción preferida de las industrias que buscan reducir costes y mejorar la eficacia en los procesos de fusión de metales.
Cuadro resumen:
Aspecto clave | Detalles |
---|---|
¿Qué es la pérdida por fusión? | Reducción de la cantidad de metal debido a la oxidación, evaporación o formación de escoria. |
Cómo ayudan los hornos de inducción | El calentamiento rápido, los entornos controlados y la ausencia de barras de carbono minimizan las pérdidas. |
Factores que influyen en las pérdidas | La temperatura, la presión, las impurezas y los oxidantes afectan a la pérdida por fusión. |
Ventajas | Eficacia, pureza y rentabilidad en la reducción de la pérdida por fusión. |
Comparación con los métodos tradicionales | Los hornos de inducción ofrecen menores pérdidas que los hornos eléctricos. |
Descubra cómo los hornos de inducción pueden optimizar su proceso de fusión de metales. contacte con nuestros expertos hoy mismo ¡!