La sinterización de cerámica es un proceso de varios pasos que transforma materiales cerámicos en polvo en estructuras densas y sólidas mediante calor y presión sin fundir el material.El proceso consiste en preparar una mezcla de polvo cerámico, darle la forma deseada (cuerpo verde) y calentarla a altas temperaturas para fusionar las partículas.El resultado es un producto cerámico denso y de baja porosidad con mayor resistencia mecánica y durabilidad.El proceso es fundamental para crear cerámicas de alto rendimiento utilizadas en diversas industrias, como la electrónica, la aeroespacial y las aplicaciones médicas.
Explicación de los puntos clave:
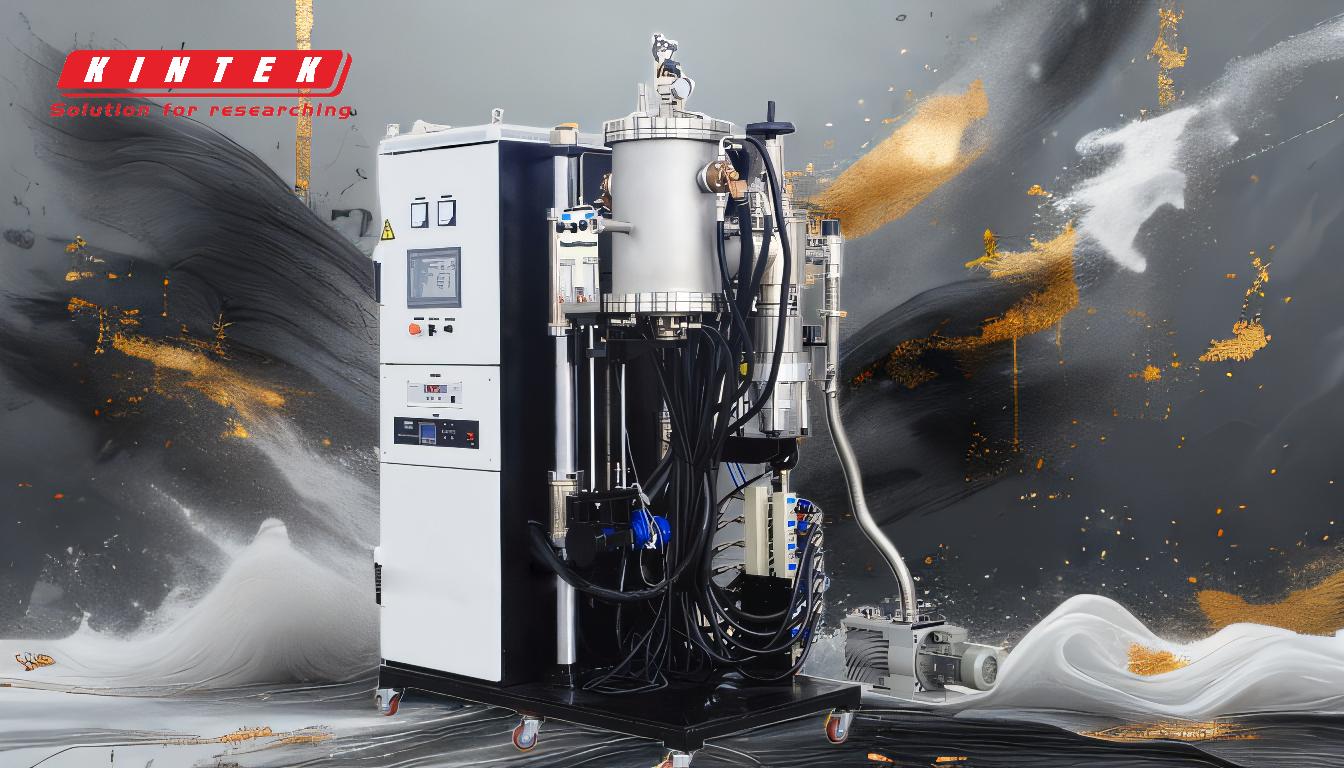
-
Composición y preparación del polvo:
- El proceso comienza con la preparación de una mezcla de polvo cerámico.Esto implica mezclar polvos cerámicos en bruto con aditivos como aglutinantes, defloculantes y agua para formar una pasta.Los aglutinantes ayudan a mantener unidas las partículas, mientras que los defloculantes evitan que se aglutinen.
- A continuación, la pasta se seca por pulverización para crear un polvo fluido más fácil de manipular y prensar en moldes.
-
Formación del cuerpo verde:
- El polvo secado por pulverización se prensa en un molde utilizando métodos mecánicos como el prensado en frío o en caliente.Este paso da forma al polvo en un "cuerpo verde", que es una estructura cerámica frágil y sin cocer.
- El cuerpo verde conserva la forma deseada, pero carece de la resistencia y densidad del producto final.Es crucial manipular el cuerpo verde con cuidado para evitar grietas o deformaciones.
-
Quemado del aglutinante:
- Antes de la sinterización, el cuerpo verde se calienta a baja temperatura para eliminar los aglutinantes orgánicos utilizados durante el proceso de conformado.Este paso, conocido como eliminación de aglutinantes, es esencial para evitar defectos en el producto final.
- La temperatura se controla cuidadosamente para garantizar la eliminación completa del aglutinante sin dañar el cuerpo verde.
-
Sinterización (cocción):
- A continuación, el cuerpo verde se calienta a una temperatura elevada, normalmente justo por debajo del punto de fusión del material cerámico, en una atmósfera controlada (por ejemplo, en un horno túnel o en un horno periódico).
- Durante la sinterización, las partículas cerámicas sufren difusión y movimiento de los límites de grano, lo que conduce a la densificación y fusión de las partículas.El resultado es un producto cerámico denso, de baja porosidad y con mejores propiedades mecánicas.
- El proceso de sinterización puede mejorarse utilizando técnicas como la sinterización en fase líquida (LPS), en la que una pequeña cantidad de fase líquida acelera la fusión de las partículas.
-
Enfriamiento y solidificación:
- Tras la sinterización, el producto cerámico se enfría gradualmente hasta alcanzar la temperatura ambiente.Este paso es fundamental para evitar tensiones térmicas y grietas.
- La velocidad de enfriamiento se controla para garantizar que el material se solidifique en una masa unificada y densa con la microestructura y las propiedades deseadas.
-
Factores que influyen en la sinterización:
- Temperatura y hora:La temperatura y la duración de la sinterización deben controlarse cuidadosamente para lograr una densificación óptima sin exceso de sinterización, lo que puede provocar un crecimiento del grano y una reducción de la resistencia.
- Atmósfera:La atmósfera de sinterización (por ejemplo, aire, vacío o gas inerte) afecta a las propiedades finales de la cerámica.Por ejemplo, la sinterización en una atmósfera reductora puede evitar la oxidación de determinados materiales.
- Características del polvo:El tamaño, la forma y la distribución de las partículas cerámicas influyen en el comportamiento de sinterización.Las partículas más finas suelen sinterizarse más fácilmente debido a su mayor energía superficial.
-
Aplicaciones de la cerámica sinterizada:
-
Las cerámicas sinterizadas se utilizan en una amplia gama de aplicaciones, como:
- Electrónica:Para sustratos, aislantes y condensadores.
- Aeroespacial:Para escudos térmicos y componentes de motores.
- Médico:Para implantes y prótesis dentales.
- Industrial:Para herramientas de corte, piezas resistentes al desgaste y filtros.
-
Las cerámicas sinterizadas se utilizan en una amplia gama de aplicaciones, como:
Al comprender y optimizar cada paso del proceso de sinterización, los fabricantes pueden producir materiales cerámicos de alta calidad adaptados a aplicaciones específicas.El proceso requiere un control preciso de parámetros como la temperatura, la presión y la atmósfera para conseguir las propiedades deseadas del material.
Cuadro recapitulativo:
Paso | Descripción |
---|---|
Preparación del polvo | Mezclar los polvos cerámicos con aglutinantes, defloculantes y agua para formar una pasta. |
Formar el cuerpo verde | Presione el polvo en un molde para crear una estructura cerámica frágil y sin cocer. |
Desmoldeo | Calentamiento para eliminar los aglutinantes, garantizando que no haya defectos en el producto final. |
Sinterización | Calentamiento a altas temperaturas para fusionar las partículas, creando un producto cerámico denso. |
Enfriamiento | Enfriar gradualmente para solidificar el material y evitar tensiones térmicas. |
Aplicaciones | Utilizado en los sectores electrónico, aeroespacial, médico e industrial. |
Optimice su proceso de sinterización de cerámica póngase en contacto con nuestros expertos para obtener soluciones a medida.