El endurecimiento de superficies es un proceso crítico en la ingeniería de materiales destinado a mejorar la durabilidad y el rendimiento de los componentes metálicos. Implica alterar la capa superficial de un metal para mejorar su dureza manteniendo al mismo tiempo la tenacidad del material del núcleo. Este proceso es esencial en industrias donde los componentes están sujetos a un alto desgaste, fatiga o impacto, como la automoción, la aeroespacial y la manufactura. El endurecimiento de la superficie no sólo prolonga la vida útil de las piezas, sino que también reduce los costos de mantenimiento y mejora la eficiencia general. Las técnicas utilizadas para el endurecimiento de superficies varían según el material y la aplicación, pero todas comparten el objetivo común de crear una superficie dura y resistente al desgaste sin comprometer la integridad estructural del componente.
Puntos clave explicados:
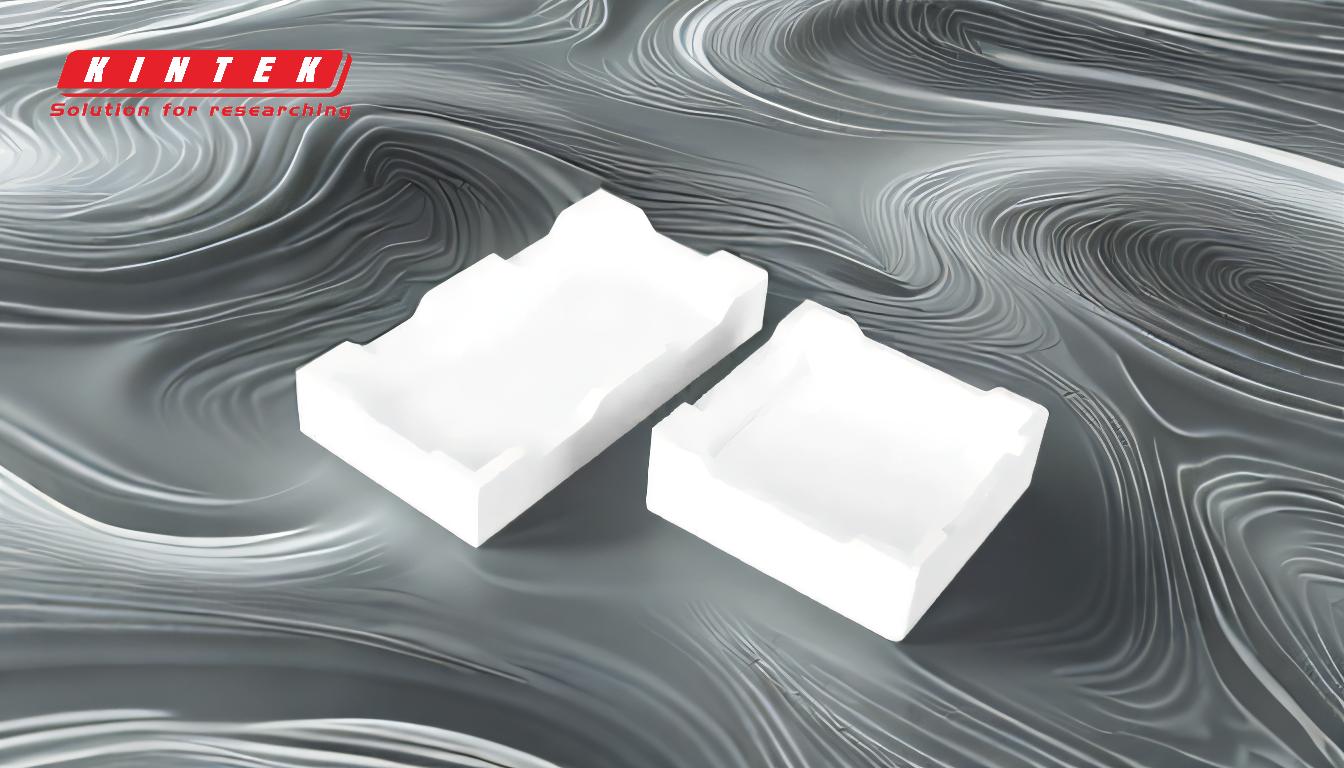
-
Resistencia al desgaste mejorada:
- El endurecimiento de la superficie aumenta significativamente la dureza de la capa exterior de un componente metálico, haciéndolo más resistente al desgaste y la abrasión. Esto es particularmente importante para piezas que están en contacto constante con otras superficies, como engranajes, cojinetes y herramientas de corte. Al endurecer la superficie, el componente puede resistir las tensiones mecánicas y la fricción que encuentra durante el funcionamiento, reduciendo así la tasa de desgaste y extendiendo su vida útil.
-
Resistencia a la fatiga mejorada:
- La falla por fatiga ocurre cuando un material se somete a tensiones cíclicas repetidas, lo que lleva a la formación de grietas y eventualmente falla. Procesos de endurecimiento de superficies, como endurecimiento de caso o nitruración, introducen tensiones residuales de compresión en la superficie del material. Estas tensiones contrarrestan las tensiones de tracción que provocan grietas por fatiga, mejorando así la resistencia a la fatiga del componente. Esto es crucial para piezas que sufren cargas cíclicas, como resortes, ejes y componentes estructurales.
-
Dureza central mantenida:
- Una de las ventajas clave del endurecimiento superficial es que permite que el núcleo del material conserve su dureza y ductilidad originales. Si bien la superficie se vuelve dura y resistente al desgaste, el núcleo sigue siendo resistente y capaz de absorber la energía del impacto sin fracturarse. Esta combinación de una superficie dura y un núcleo resistente es ideal para componentes que necesitan resistir tanto el desgaste como el impacto, como engranajes, cigüeñales y árboles de levas.
-
Resistencia a la corrosión:
- Ciertas técnicas de endurecimiento de superficies, como nitruración y cementación, también pueden mejorar la resistencia a la corrosión de los componentes metálicos. Estos procesos crean una capa superficial endurecida que es menos susceptible a la corrosión, lo que hace que el componente sea más duradero en entornos hostiles. Esto es particularmente beneficioso para piezas expuestas a sustancias corrosivas, como las utilizadas en procesos químicos o aplicaciones marinas.
-
Rentabilidad:
- El endurecimiento de superficies es una solución rentable para mejorar el rendimiento de los componentes metálicos. En lugar de utilizar costosos materiales de alta aleación en todo el componente, el endurecimiento de la superficie permite a los fabricantes utilizar materiales base menos costosos y al mismo tiempo lograr las propiedades superficiales deseadas. Esto reduce los costes de material y hace que el proceso de producción sea más económico.
-
Versatilidad en aplicaciones:
- Las técnicas de endurecimiento de superficies son versátiles y se pueden aplicar a una amplia gama de materiales y componentes. Ya sea que se trate de una pequeña pieza de precisión o de un gran componente industrial, el endurecimiento de la superficie se puede adaptar para cumplir requisitos específicos. Esta versatilidad lo convierte en un proceso valioso en diversas industrias, incluida la automotriz, aeroespacial, de fabricación de herramientas y más.
-
Beneficios ambientales:
- Al extender la vida útil de los componentes y reducir la necesidad de reemplazos frecuentes, el endurecimiento de la superficie contribuye a la sostenibilidad ambiental. Menos reemplazos significan menos desperdicio de material y menor consumo de energía asociado con la fabricación de piezas nuevas. Además, algunos procesos de endurecimiento superficial, como endurecimiento por inducción , son energéticamente eficientes y producen un mínimo de residuos, lo que mejora aún más sus beneficios medioambientales.
En resumen, el endurecimiento de superficies es un proceso vital que mejora el rendimiento, la durabilidad y la rentabilidad de los componentes metálicos. Al mejorar la resistencia al desgaste, la fatiga y la corrosión mientras se mantiene la tenacidad del núcleo, el endurecimiento de la superficie garantiza que los componentes puedan soportar las exigentes condiciones de las aplicaciones industriales modernas. Su versatilidad y beneficios medioambientales la convierten en una técnica indispensable en la ingeniería de materiales.
Tabla resumen:
Beneficio clave | Descripción |
---|---|
Resistencia al desgaste mejorada | Aumenta la dureza de la superficie, reduciendo el desgaste y extendiendo la vida útil de los componentes. |
Resistencia a la fatiga mejorada | Introduce tensiones de compresión para evitar grietas por fatiga bajo cargas cíclicas. |
Dureza central mantenida | Mantiene el núcleo resistente y dúctil mientras endurece la superficie. |
Resistencia a la corrosión | Ciertas técnicas mejoran la resistencia a la corrosión en entornos hostiles. |
Rentabilidad | Reduce los costos de materiales al utilizar materiales base menos costosos. |
Versatilidad en aplicaciones | Aplicable a una amplia gama de materiales y componentes en todas las industrias. |
Beneficios ambientales | Extiende la vida útil de los componentes, reduciendo el desperdicio y el consumo de energía. |
Optimice sus componentes metálicos con endurecimiento de superficies: contacte a nuestros expertos hoy para aprender más!