En el proceso de recubrimiento por deposición física de vapor (PVD), se utilizan varios gases en función de las propiedades de recubrimiento deseadas y de la técnica de PVD específica empleada.El argón es el gas inerte más utilizado debido a su naturaleza no reactiva, que garantiza la pureza del material de revestimiento durante la vaporización.También se utilizan gases reactivos como el oxígeno, el nitrógeno, el metano y el acetileno para formar revestimientos compuestos como óxidos, nitruros y carburos.La elección del gas depende del material de revestimiento, el sustrato y la aplicación prevista del producto revestido.
Explicación de los puntos clave:
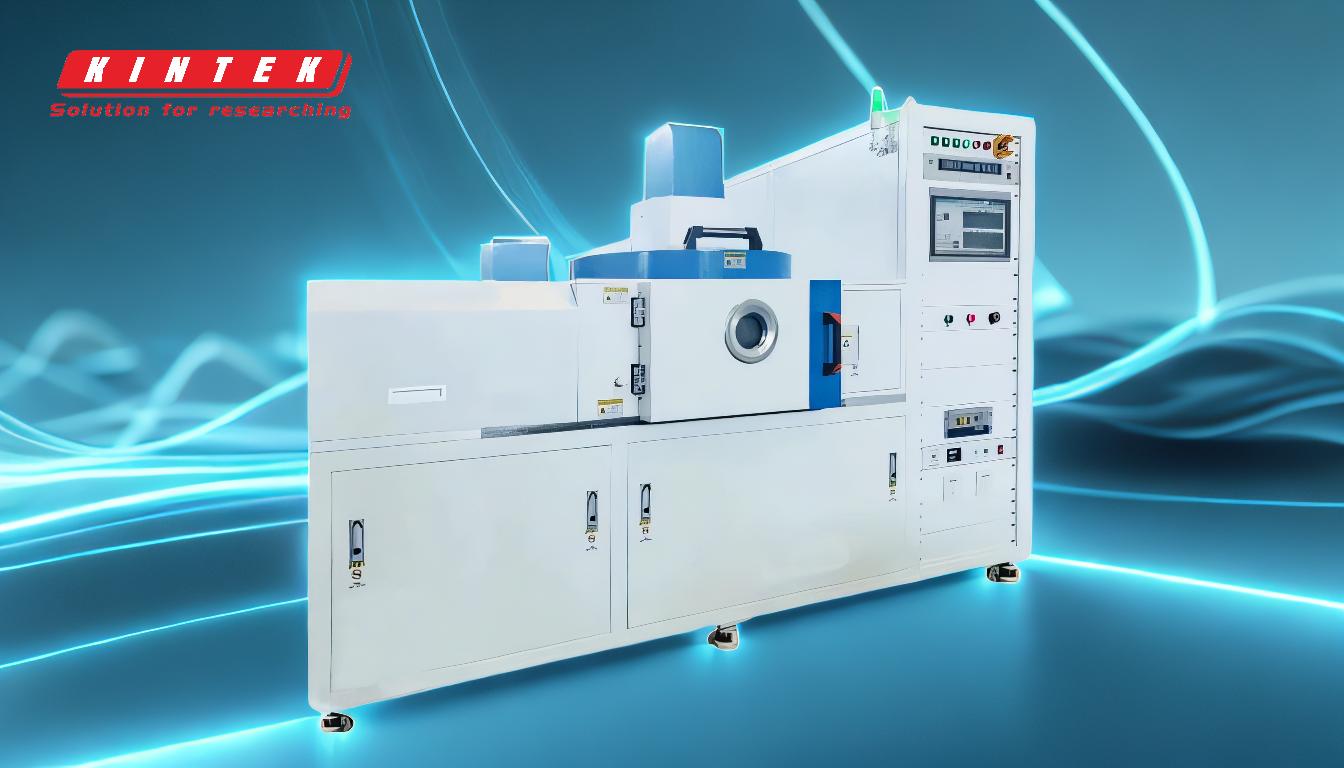
-
El argón como gas inerte primario:
- Papel:El argón se utiliza ampliamente en PVD porque es inerte, lo que significa que no reacciona químicamente con el material de revestimiento ni con el sustrato.Esto garantiza que el material de revestimiento permanezca puro durante las fases de vaporización y deposición.
- Proceso:Durante el sputtering por magnetrón o la evaporación por arco catódico, se utilizan iones de argón para bombardear el material objetivo, haciendo que se vaporice y forme un plasma.A continuación, el material vaporizado se deposita sobre el sustrato.
- Ventajas:La naturaleza inerte del argón lo hace ideal para crear revestimientos metálicos puros sin introducir impurezas.
-
Gases reactivos para revestimientos compuestos:
- Oxígeno (O2):Se utiliza para formar revestimientos de óxido metálico (por ejemplo, dióxido de titanio, óxido de aluminio).Estos revestimientos se utilizan a menudo por su dureza, resistencia al desgaste y propiedades ópticas.
- Nitrógeno (N2):Reacciona con átomos metálicos para formar nitruros (por ejemplo, nitruro de titanio, nitruro de cromo), conocidos por su dureza, resistencia a la corrosión y aspecto decorativo similar al oro.
- Metano (CH4) y acetileno (C2H2):Se utiliza para crear revestimientos de carburo (por ejemplo, carburo de titanio, carburo de silicio), que son extremadamente duros y resistentes al desgaste.El acetileno se utiliza especialmente para los revestimientos de carbono tipo diamante (DLC).
- Hexa-metil-disiloxano (HMDSO):Se utiliza en el depósito químico en fase vapor asistido por plasma (PACVD) para crear revestimientos que contienen silicio, que suelen emplearse por sus propiedades ópticas y de barrera.
-
Selección de gases en función de la técnica de PVD:
- Sputtering de magnetrón:El argón es el principal gas de pulverización catódica, pero pueden introducirse gases reactivos como el nitrógeno o el oxígeno para formar revestimientos compuestos.
- Evaporación por arco catódico:Se utiliza argón como gas primario, pero pueden añadirse gases reactivos para modificar las propiedades del revestimiento.
- Evaporación térmica o por haz de electrones:Normalmente se utiliza argón, pero pueden introducirse gases reactivos para formar revestimientos compuestos.
-
Sistema de entrada de gas de proceso:
- Suministro de gas:Los gases se suministran desde cilindros y se controlan mediante válvulas y contadores para garantizar caudales precisos.
- Cámara de vacío:Los gases se introducen en la cámara de vacío, donde interactúan con el material de revestimiento vaporizado para formar el revestimiento deseado.
-
Aplicaciones de los distintos gases:
- Revestimientos decorativos:El nitrógeno se utiliza a menudo para crear revestimientos similares al oro con fines decorativos.
- Revestimientos funcionales:El oxígeno y el metano se utilizan para crear revestimientos duros y resistentes al desgaste para aplicaciones industriales.
- Recubrimientos ópticos:El HMDSO se utiliza para crear revestimientos con propiedades ópticas específicas.
-
Importancia de la pureza del gas:
- Los gases de alta pureza son esenciales para evitar la contaminación y garantizar una calidad constante del revestimiento.Las impurezas en el gas pueden provocar defectos en el revestimiento, reduciendo su rendimiento y durabilidad.
Seleccionando cuidadosamente el gas o la mezcla de gases adecuados, los fabricantes pueden adaptar las propiedades del revestimiento PVD a los requisitos específicos de la aplicación, ya sea con fines decorativos, funcionales u ópticos.
Tabla resumen:
Tipo de gas | Papel en el recubrimiento PVD | Aplicaciones comunes |
---|---|---|
Argón (Ar) | Gas inerte para revestimientos metálicos puros, utilizado en procesos de sputtering y evaporación. | Recubrimientos metálicos puros, garantizando la ausencia de impurezas. |
Oxígeno (O2) | Forma recubrimientos de óxido metálico (por ejemplo, TiO2, Al2O3) para obtener dureza y resistencia al desgaste. | Recubrimientos duros y resistentes al desgaste para aplicaciones industriales. |
Nitrógeno (N2) | Crea nitruros (por ejemplo, TiN, CrN) para obtener dureza, resistencia a la corrosión y decoración. | Recubrimientos decorativos similares al oro y capas funcionales resistentes al desgaste. |
Metano (CH4) | Forma recubrimientos de carburo (por ejemplo, TiC, SiC) para una dureza y resistencia al desgaste extremas. | Aplicaciones industriales que requieren una gran durabilidad. |
Acetileno (C2H2) | Utilizado para revestimientos de carbono tipo diamante (DLC). | Recubrimientos de alto rendimiento para herramientas y maquinaria. |
HMDSO | Crea revestimientos que contienen silicio para propiedades ópticas y de barrera. | Recubrimientos ópticos y capas protectoras de barrera. |
¿Necesita ayuda para seleccionar los gases adecuados para su proceso de revestimiento PVD? Póngase en contacto hoy mismo con nuestros expertos para obtener soluciones a medida.