La vida útil de un revestimiento, como el revestimiento PVD (deposición física de vapor), varía significativamente en función de varios factores. Entre ellos, el tipo de material del sustrato, el grosor del revestimiento, la fuerza de adherencia entre el revestimiento y el sustrato, y las condiciones ambientales, como la exposición a altas temperaturas y el desgaste. Comprender estos factores puede ayudar a predecir la durabilidad y el rendimiento del revestimiento en aplicaciones específicas.
Explicación de los puntos clave:
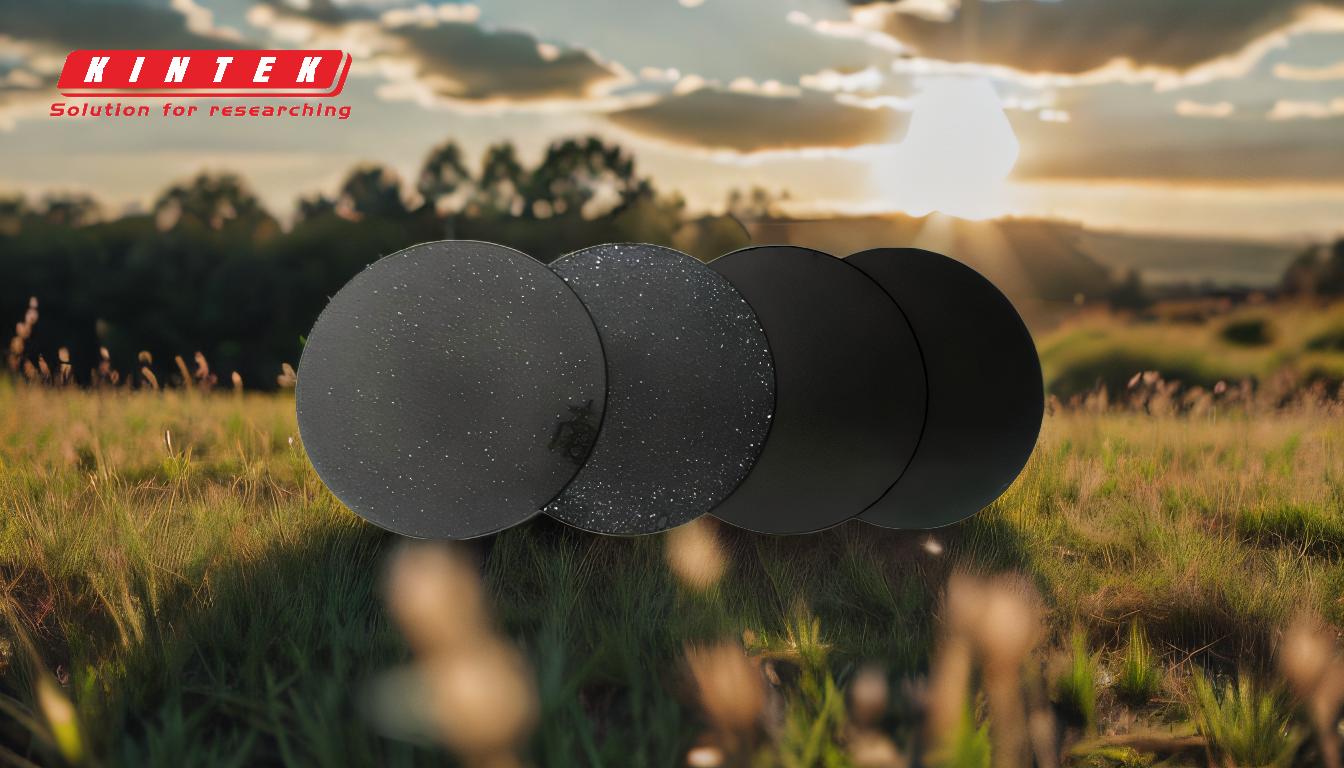
-
Tipo de sustrato:
- Explicación: El material sobre el que se aplica el revestimiento desempeña un papel crucial a la hora de determinar su vida útil. Los distintos sustratos tienen diferentes energías superficiales y composiciones químicas, lo que puede afectar a la adherencia del revestimiento y a su rendimiento a lo largo del tiempo.
- Impacto: Por ejemplo, los revestimientos de metales como el acero inoxidable pueden durar más que los de materiales más blandos gracias a su mayor adherencia y resistencia al desgaste.
-
Espesor del revestimiento:
- Explicación: El grosor del revestimiento es directamente proporcional a su durabilidad. Los revestimientos más gruesos suelen ofrecer mejor protección contra el desgaste y la corrosión.
- Impacto: Sin embargo, los revestimientos excesivamente gruesos pueden provocar problemas como grietas o delaminación, especialmente bajo tensión mecánica o ciclos térmicos.
-
Fuerza de adherencia entre el revestimiento y el sustrato:
- Explicación: La fuerza de adhesión entre el revestimiento y el sustrato es fundamental para la longevidad del revestimiento. Unas uniones más fuertes garantizan que el revestimiento permanezca intacto bajo tensión mecánica y exposición ambiental.
- Impacto: Técnicas como la preparación de la superficie (limpieza, grabado) y el uso de capas intermedias pueden mejorar la fuerza de adherencia, prolongando así la vida útil del revestimiento.
-
Exposición a altas temperaturas:
- Explicación: Las altas temperaturas pueden provocar dilataciones térmicas y tensiones en la interfaz entre el revestimiento y el sustrato, lo que puede provocar grietas o desprendimientos.
- Impacto: Los revestimientos diseñados para soportar altas temperaturas, como los utilizados en aplicaciones aeroespaciales o de automoción, están formulados para mantener la integridad bajo estrés térmico.
-
Exposición al desgaste:
- Explicación: El entorno operativo, incluidos factores como la fricción, la abrasión y el impacto, afecta significativamente a la durabilidad del revestimiento. Los revestimientos en entornos de alto desgaste deben tener una gran dureza y resistencia al desgaste.
- Impacto: Por ejemplo, los revestimientos de herramientas de corte o piezas de maquinaria industrial suelen estar sometidos a un intenso desgaste, lo que exige el uso de materiales muy duraderos como el nitruro de titanio (TiN) o el carbono diamante (DLC).
Comprender estos factores y cómo interactúan es esencial para seleccionar el revestimiento adecuado para una aplicación específica, garantizando un rendimiento y una longevidad óptimos. Teniendo en cuenta el tipo de sustrato, el grosor del revestimiento, la fuerza de adherencia y las exposiciones ambientales, se pueden tomar decisiones informadas que mejoren la durabilidad y la eficacia del revestimiento.
Cuadro recapitulativo:
Factor | Explicación | Impacto |
---|---|---|
Tipo de sustrato | Las propiedades del material afectan a la adherencia y al rendimiento. | Los revestimientos de metales como el acero inoxidable duran más gracias a su mayor adherencia y resistencia al desgaste. |
Espesor del revestimiento | Los revestimientos más gruesos ofrecen mayor protección, pero pueden agrietarse bajo tensión. | El grosor óptimo garantiza la durabilidad sin comprometer la integridad. |
Fuerza de adhesión | La fuerte adherencia evita la delaminación bajo tensión. | La preparación de la superficie y las capas intermedias mejoran la fuerza de adherencia. |
Altas temperaturas | El estrés térmico puede causar grietas o delaminación. | Los revestimientos resistentes a altas temperaturas mantienen la integridad en aplicaciones exigentes. |
Exposición al desgaste | La fricción, la abrasión y los impactos reducen la vida útil del revestimiento. | Los materiales duraderos como el TiN o el DLC se utilizan en entornos de alto desgaste. |
Optimice el rendimiento de su revestimiento contacte con nosotros para obtener asesoramiento experto