La pulvimetalurgia (PM) es un proceso de fabricación versátil que ofrece numerosas ventajas, como alta eficiencia, escaso desperdicio de material y capacidad para producir piezas uniformes con tolerancias ajustadas.Sin embargo, también presenta varios inconvenientes que pueden limitar su aplicación en determinados escenarios.Entre ellas se encuentran las limitaciones en el tamaño y la complejidad de las piezas, la reducción de la resistencia mecánica debido a la porosidad y las dificultades para producir piezas que igualen la resistencia y la ductilidad de los componentes fundidos o forjados.A continuación analizamos estas desventajas en detalle.
Explicación de los puntos clave:
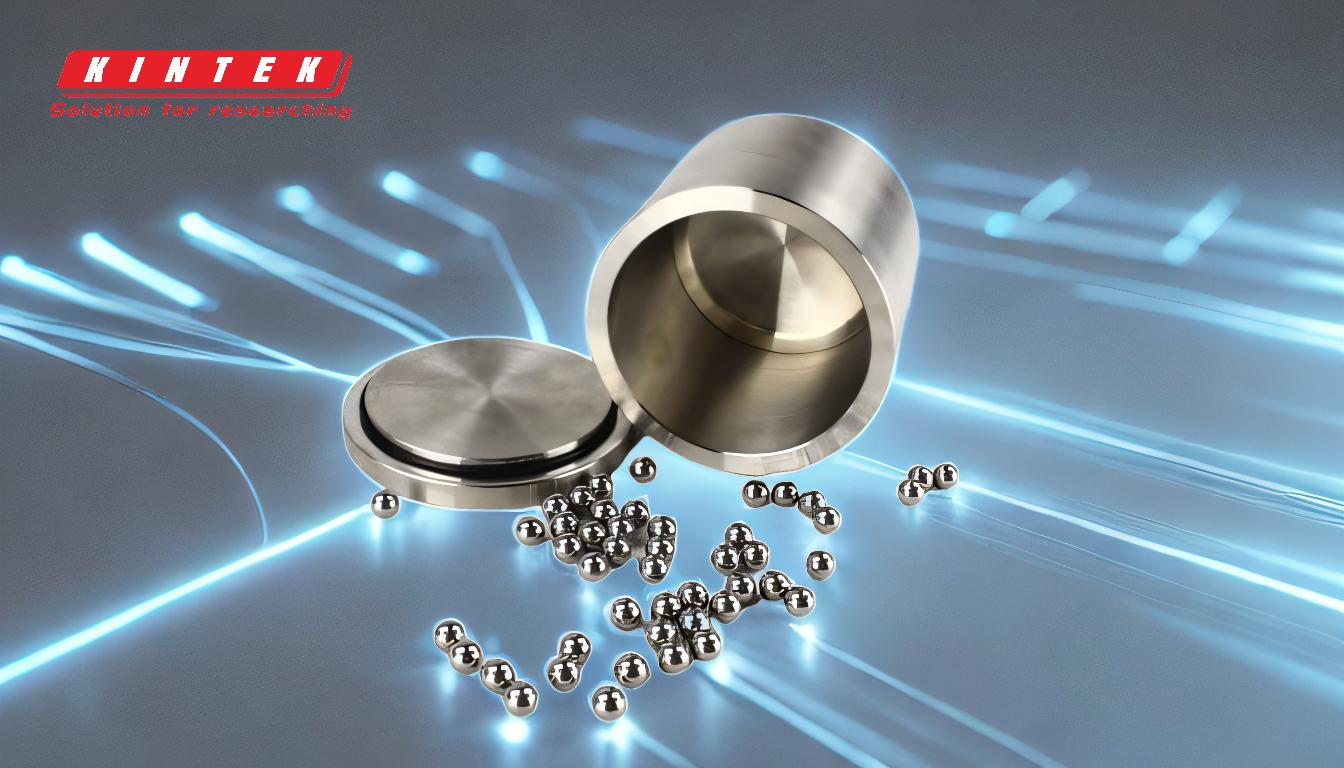
-
Limitaciones de tamaño:
- La pulvimetalurgia se ve limitada por el tamaño de las prensas utilizadas en el proceso.Las prensas más grandes del sector suelen rondar las 1.500 toneladas, lo que limita el tamaño práctico de las piezas a aproximadamente 40-50 pulgadas cuadradas de superficie plana.Esto hace que la PM no sea adecuada para producir componentes muy grandes, que pueden requerir métodos de fabricación alternativos como la fundición o la forja.
-
Piezas de formas complejas:
- Aunque la PM puede producir piezas con geometrías intrincadas, existen limitaciones en cuanto a la complejidad de las formas que pueden conseguirse.Las piezas de formas complejas suelen requerir utillaje avanzado y fabricantes cualificados para superar los retos que plantean el prensado de polvo y la sinterización.Esto puede aumentar los costes de producción y los plazos de entrega, haciendo que la PM sea menos competitiva para diseños muy complejos.
-
Porosidad y resistencia mecánica reducida:
- Uno de los inconvenientes inherentes a la PM es la presencia de porosidad en las piezas sinterizadas.La porosidad se produce debido a los espacios entre las partículas de polvo que permanecen incluso después de la compactación y la sinterización.Esta porosidad reduce la densidad de la pieza final, lo que conlleva una menor resistencia mecánica en comparación con las piezas fundidas o forjadas.Como resultado, las piezas de PM pueden no ser adecuadas para aplicaciones que requieran una gran resistencia o durabilidad.
-
Menor ductilidad:
- Las piezas PM suelen presentar una ductilidad menor que las producidas por fundición o forja.La ductilidad es la capacidad de un material para deformarse bajo tensión de tracción, y su reducción en las piezas de PM puede limitar su uso en aplicaciones en las que la flexibilidad o la resistencia al impacto son críticas.
-
Limitaciones del material:
- No todos los materiales son adecuados para la pulvimetalurgia.Algunas aleaciones o materiales pueden no compactarse o sinterizarse eficazmente, lo que limita la gama de materiales que pueden utilizarse.Además, conseguir propiedades específicas de los materiales, como alta resistencia o resistencia a la corrosión, puede ser más difícil con la PM en comparación con otros métodos de fabricación.
-
Coste del utillaje:
- El coste inicial del utillaje para la PM puede ser elevado, sobre todo en el caso de piezas personalizadas o complejas.Aunque la PM es rentable para la producción de grandes volúmenes, la inversión inicial en utillaje puede no estar justificada para series de producción de bajo volumen o prototipos.
-
Piezas finales incompletas:
- Debido a las limitaciones del prensado de polvo y la sinterización, algunas piezas de uso final pueden quedar incompletas o requerir operaciones secundarias para conseguir la forma o las propiedades deseadas.Esto puede aumentar el coste global y la complejidad de la producción.
-
Opciones limitadas de acabado superficial:
- Las piezas PM suelen tener un acabado superficial más rugoso que las piezas mecanizadas o forjadas.Aunque operaciones secundarias como el mecanizado o el revestimiento pueden mejorar el acabado superficial, estos pasos adicionales aumentan el tiempo y el coste de producción.
-
Preocupaciones medioambientales y de seguridad:
- Aunque en general se considera que el polvo metálico es respetuoso con el medio ambiente porque los residuos de material son mínimos, su manipulación puede plantear riesgos para la salud y la seguridad, como problemas respiratorios o peligro de incendio.Para mitigar estos riesgos se requieren medidas y equipos de seguridad adecuados.
-
Dependencia de las características del polvo:
- La calidad de las piezas de PM depende en gran medida de las características del polvo metálico utilizado, como el caudal, la densidad, la compresibilidad y la resistencia.Las variaciones en las propiedades del polvo pueden provocar incoherencias en el producto final, lo que exige estrictas medidas de control de calidad.
En resumen, aunque la pulvimetalurgia ofrece ventajas significativas en términos de eficiencia y utilización del material, sus desventajas -como las limitaciones de tamaño, la porosidad, las propiedades mecánicas reducidas y los retos que plantean las formas complejas- deben tenerse muy en cuenta a la hora de seleccionar un proceso de fabricación.Estas limitaciones hacen que la PM sea más adecuada para aplicaciones específicas en las que sus ventajas superan a sus inconvenientes.
Cuadro sinóptico:
Desventaja | Descripción |
---|---|
Limitaciones de tamaño | Limitado a piezas con áreas planas de 40-50 pulgadas cuadradas debido a las restricciones de la prensa. |
Piezas de formas complejas | Se requiere utillaje avanzado y mano de obra cualificada, lo que aumenta los costes y los plazos de entrega. |
Porosidad y resistencia reducida | La porosidad en las piezas sinterizadas reduce la resistencia mecánica y la durabilidad. |
Menor ductilidad | Menor flexibilidad y resistencia al impacto en comparación con las piezas fundidas o forjadas. |
Limitaciones de los materiales | Gama limitada de materiales aptos para PM; dificultades para conseguir propiedades. |
Coste del utillaje | Elevados costes iniciales de utillaje, especialmente para piezas personalizadas o complejas. |
Piezas de uso final incompletas | Pueden requerir operaciones secundarias, lo que aumenta los costes de producción y la complejidad. |
Opciones limitadas de acabado superficial | Acabado superficial más rugoso; se necesitan pasos adicionales para mejorarlo. |
Preocupaciones medioambientales y de seguridad | Riesgos para la salud derivados de los polvos metálicos finos; requiere medidas de seguridad. |
Dependencia de las características del polvo | La calidad del producto final depende de las propiedades del polvo, lo que exige controles estrictos. |
¿Necesita ayuda para elegir el proceso de fabricación adecuado? Póngase en contacto con nuestros expertos para un asesoramiento personalizado.