Un molde es una herramienta crucial en procesos de fabricación como el moldeo por inyección, y su diseño influye directamente en la calidad y funcionalidad del producto final.En esencia, un molde consta de dos mitades principales: la cavidad y el núcleo.La cavidad forma la parte exterior del producto, mientras que el núcleo da forma a la parte interior o trasera.Estas mitades trabajan juntas para crear la pieza deseada.Además de estos componentes primarios, los moldes pueden incluir elementos adicionales como correderas, compuertas y pasadores eyectores para facilitar el flujo de material y la extracción de la pieza.Comprender las partes principales de un molde es esencial para garantizar una producción eficaz y unos resultados de alta calidad.
Explicación de los puntos clave:
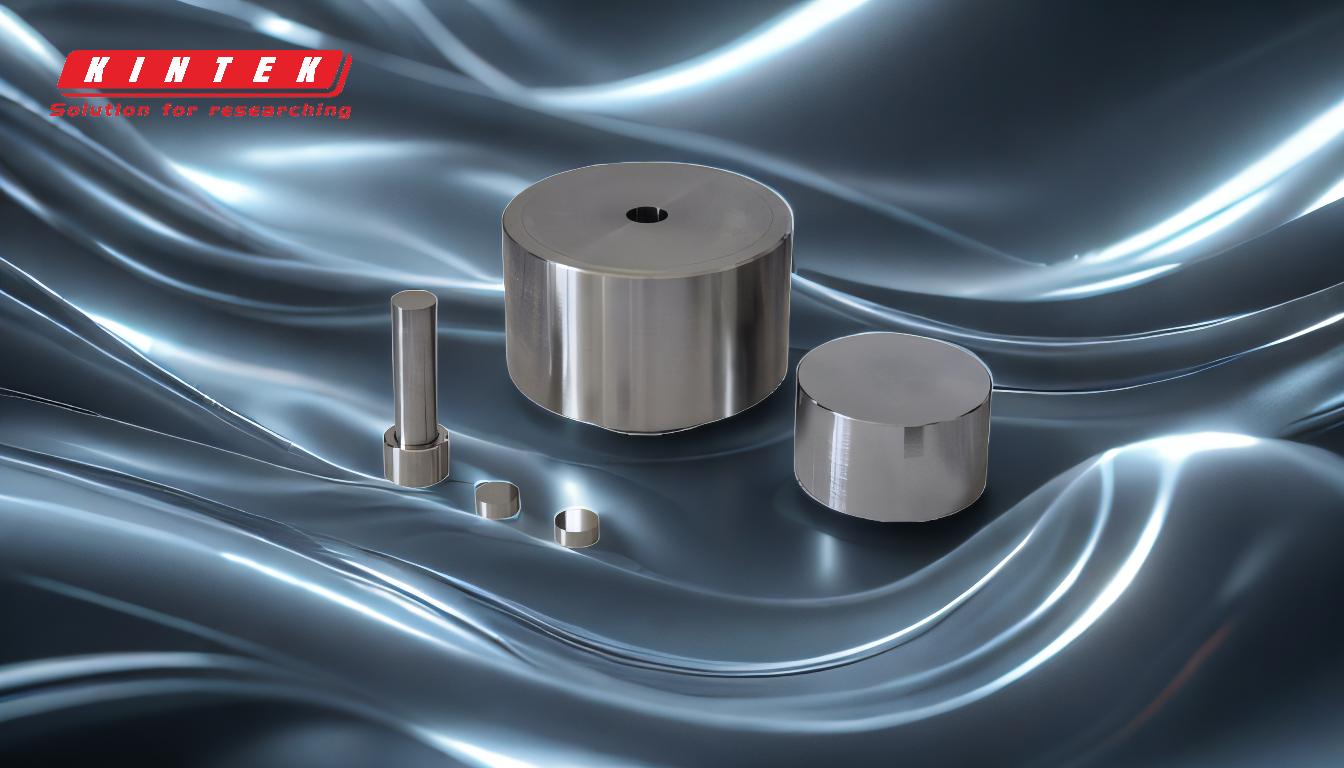
-
Cavidad y núcleo:
- La cavidad es la parte del molde que forma la superficie exterior del producto.Suele ser la cara A, que es la cara cosmética con mejor aspecto exterior.
- El núcleo es la parte que forma la cara interna o trasera del producto, conocida como cara B. Suele incluir características funcionales como nervaduras o resaltes.Suele incluir elementos funcionales como nervaduras o resaltes.
-
Placas metálicas:
- Los moldes se construyen a partir de dos placas metálicas que albergan la cavidad y el núcleo.Estas placas se mecanizan con precisión para adaptarlas a la forma deseada de la pieza acabada.
- Las placas deben soportar altas presiones y temperaturas durante el proceso de moldeo, por lo que suelen estar fabricadas con materiales duraderos como el acero o el aluminio.
-
Cavidades:
- Las cavidades son los espacios huecos dentro de las placas del molde donde se inyecta el material (por ejemplo, plástico o caucho) para formar el producto.
- El diseño de las cavidades influye directamente en las dimensiones, el acabado superficial y la integridad estructural del producto final.
-
Correderas y puertas:
- Las correderas son canales que guían el material fundido desde la boquilla de la máquina de moldeo por inyección hasta las cavidades.
- Las compuertas son los puntos de entrada por los que el material fluye hacia las cavidades.Su diseño afecta al caudal, la refrigeración y el aspecto final del producto.
-
Sistema eyector:
- Una vez solidificado el material, el sistema eyector ayuda a extraer la pieza acabada del molde.Este sistema suele incluir pasadores eyectores que empujan la pieza fuera de la cavidad.
- Una expulsión adecuada es fundamental para evitar dañar la pieza o el molde.
-
Sistema de refrigeración:
- Los moldes suelen incluir canales de refrigeración para regular la temperatura y garantizar un enfriamiento uniforme del material.Esto ayuda a evitar defectos como alabeos o marcas de hundimiento.
- Una refrigeración eficaz es esencial para mantener los tiempos de ciclo y la calidad del producto.
-
Características de alineación y soporte:
- Los moldes pueden incluir pasadores guía y casquillos para garantizar una alineación precisa de las mitades de la cavidad y el núcleo.
- Los elementos de soporte, como las bases de los moldes y las placas de sujeción, proporcionan estabilidad estructural durante el proceso de moldeo.
Al comprender estas partes principales de un molde, los fabricantes pueden optimizar sus diseños para obtener un mejor rendimiento, durabilidad y calidad del producto.Cada componente desempeña un papel vital en la funcionalidad general del molde, y su correcta integración es clave para el éxito de la producción.
Cuadro sinóptico:
Componente | Función |
---|---|
Cavidad | Forma la superficie exterior (cara A) del producto. |
Núcleo | Da forma a la parte interior o trasera (cara B) del producto. |
Placas metálicas | Aloja la cavidad y el núcleo; fabricadas con materiales duraderos como el acero o el aluminio. |
Canales y puertas | Canales y puntos de entrada para el flujo de material fundido. |
Sistema eyector | Extrae la pieza acabada del molde mediante pasadores eyectores. |
Sistema de refrigeración | Regula la temperatura para garantizar un enfriamiento uniforme y evitar defectos. |
Características de alineación | Garantiza una alineación precisa de las mitades de la cavidad y el núcleo. |
Optimice el diseño de sus moldes para mejorar la eficacia de la producción. contacte hoy mismo con nuestros expertos ¡!