La soldadura fuerte es un proceso de unión que utiliza calor para fundir un metal de aportación, que luego fluye hacia la unión entre dos o más materiales estrechamente unidos. La elección de la fuente de calor es fundamental para el éxito del proceso de soldadura fuerte, ya que afecta la calidad, la eficiencia y la idoneidad de la aplicación de la unión. Tres fuentes de calor comúnmente utilizadas para la soldadura fuerte son la soldadura fuerte con soplete, la soldadura fuerte en horno y la soldadura fuerte por inducción. Cada método tiene sus ventajas únicas, lo que lo hace adecuado para aplicaciones y materiales específicos.
Puntos clave explicados:
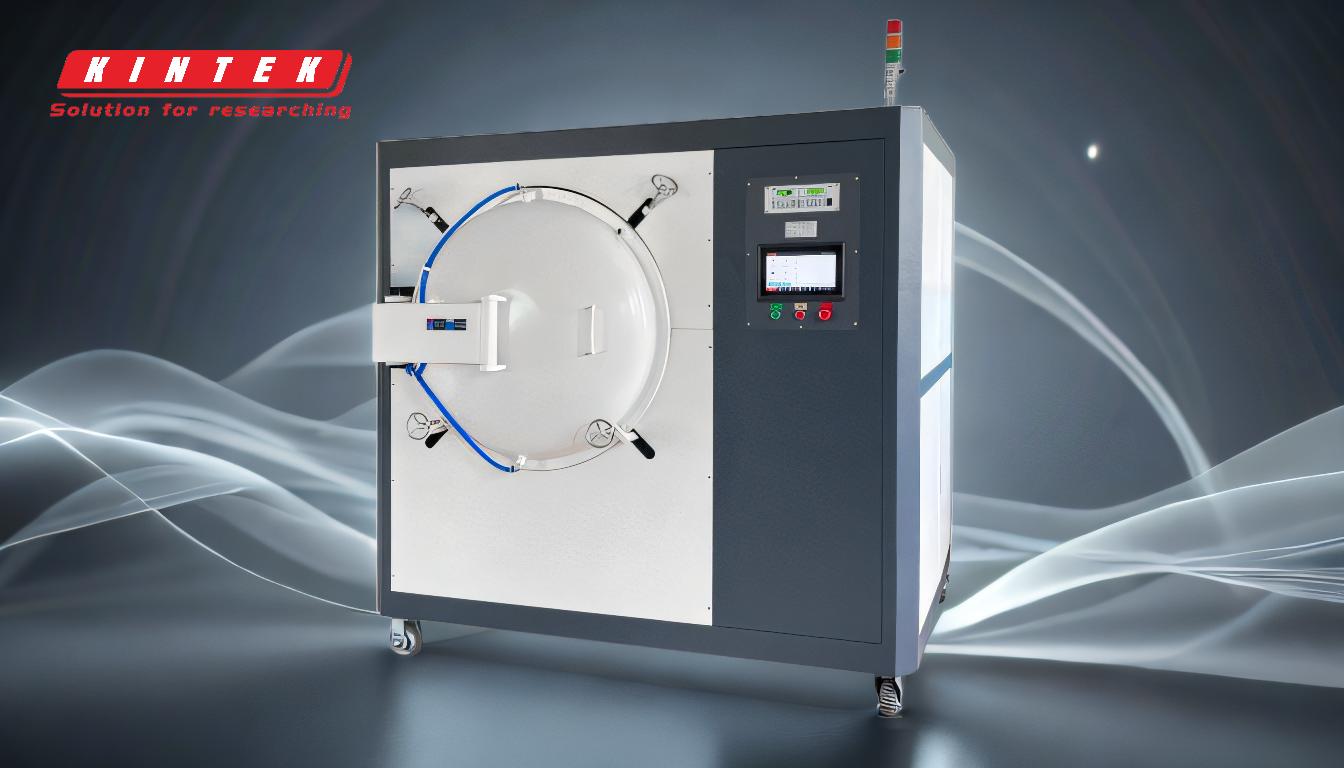
-
Soldadura con soplete:
- Descripción: La soldadura fuerte con soplete implica el uso de un soplete de gas para aplicar calor localizado al área de la unión. La antorcha puede operarse manualmente o automatizarse, según la aplicación.
-
Ventajas:
- Portabilidad: La soldadura fuerte con soplete es muy portátil, lo que la hace ideal para reparaciones in situ u operaciones a pequeña escala.
- Flexibilidad: Se puede utilizar en una amplia gama de materiales y configuraciones de juntas.
- Rentabilidad: Requiere equipo y configuración mínimos, lo que lo hace rentable para lotes pequeños o trabajos personalizados.
- Aplicaciones: Comúnmente utilizado en sistemas HVAC, plomería y reparaciones de automóviles.
-
Soldadura en horno:
- Descripción: La soldadura fuerte en horno implica calentar todo el conjunto en un horno, que puede controlarse para proporcionar una temperatura uniforme. Los hornos pueden funcionar en diversas atmósferas, incluidas exotérmicas, de hidrógeno, de argón y de vacío, para evitar la oxidación y la contaminación.
-
Ventajas:
- Calefacción uniforme: Garantiza una distribución uniforme del calor, lo cual es crucial para ensamblajes complejos o grandes.
- Producción de alto volumen: Adecuado para producción en masa debido a su capacidad para manejar múltiples piezas simultáneamente.
- Atmósfera controlada: Reduce la oxidación y mejora la calidad de las juntas.
- Aplicaciones: Ampliamente utilizado en las industrias aeroespacial, automotriz y electrónica para componentes como intercambiadores de calor, sensores y contactos eléctricos.
-
Soldadura por inducción:
- Descripción: La soldadura fuerte por inducción utiliza inducción electromagnética para generar calor directamente dentro de la pieza de trabajo. Una bobina de inducción crea un campo magnético alterno de alta frecuencia, que induce corrientes parásitas en los materiales conductores, calentándolos rápidamente.
-
Ventajas:
- Precisión: Proporciona un calentamiento preciso y localizado, minimizando las zonas afectadas por el calor.
- Velocidad: Los ciclos de calentamiento rápidos aumentan la eficiencia de la producción.
- Eficiencia Energética: El calentamiento directo de la pieza de trabajo reduce la pérdida de energía.
- Aplicaciones: Ideal para aplicaciones de alta precisión como dispositivos médicos, joyería y pequeños componentes electrónicos.
Estas tres fuentes de calor (soldadura con soplete, soldadura en horno y soldadura por inducción) se utilizan ampliamente en diversas industrias debido a sus capacidades únicas. La elección de la fuente de calor depende de factores como los materiales que se unen, la complejidad del ensamblaje, el volumen de producción y los requisitos específicos de la aplicación. Comprender estos métodos ayuda a seleccionar la técnica de soldadura más adecuada para obtener resultados óptimos.
Tabla resumen:
Fuente de calor | Ventajas | Aplicaciones |
---|---|---|
Soldadura con soplete | Portátil, flexible y rentable | Sistemas HVAC, fontanería, reparaciones de automóviles. |
Soldadura en horno | Calentamiento uniforme, producción de alto volumen, atmósfera controlada | Aeroespacial, automoción, electrónica (intercambiadores de calor, sensores, contactos eléctricos) |
Soldadura por inducción | Precisión, velocidad, eficiencia energética | Dispositivos médicos, joyas, pequeños componentes electrónicos. |
¿Necesita ayuda para elegir el método de soldadura adecuado para su proyecto? Póngase en contacto con nuestros expertos hoy !