La sinterización es un proceso crítico en la fabricación que consiste en calentar polvos metálicos o cerámicos comprimidos para formar piezas estructurales complejas.Para garantizar la calidad y consistencia de los productos sinterizados, se utilizan gases protectores para crear una atmósfera inerte que evite la oxidación y la descarburación.Los gases más utilizados en la sinterización son el hidrógeno, el nitrógeno y el monóxido de carbono.Estos gases ayudan a mantener la presión atmosférica, controlar el entorno de sinterización y garantizar un rendimiento constante.El nitrógeno es especialmente eficaz para evitar la oxidación en zonas de alto calor, mientras que el hidrógeno y el monóxido de carbono se utilizan por sus propiedades reductoras.La elección del gas depende del material a sinterizar y de los resultados deseados.
Explicación de los puntos clave:
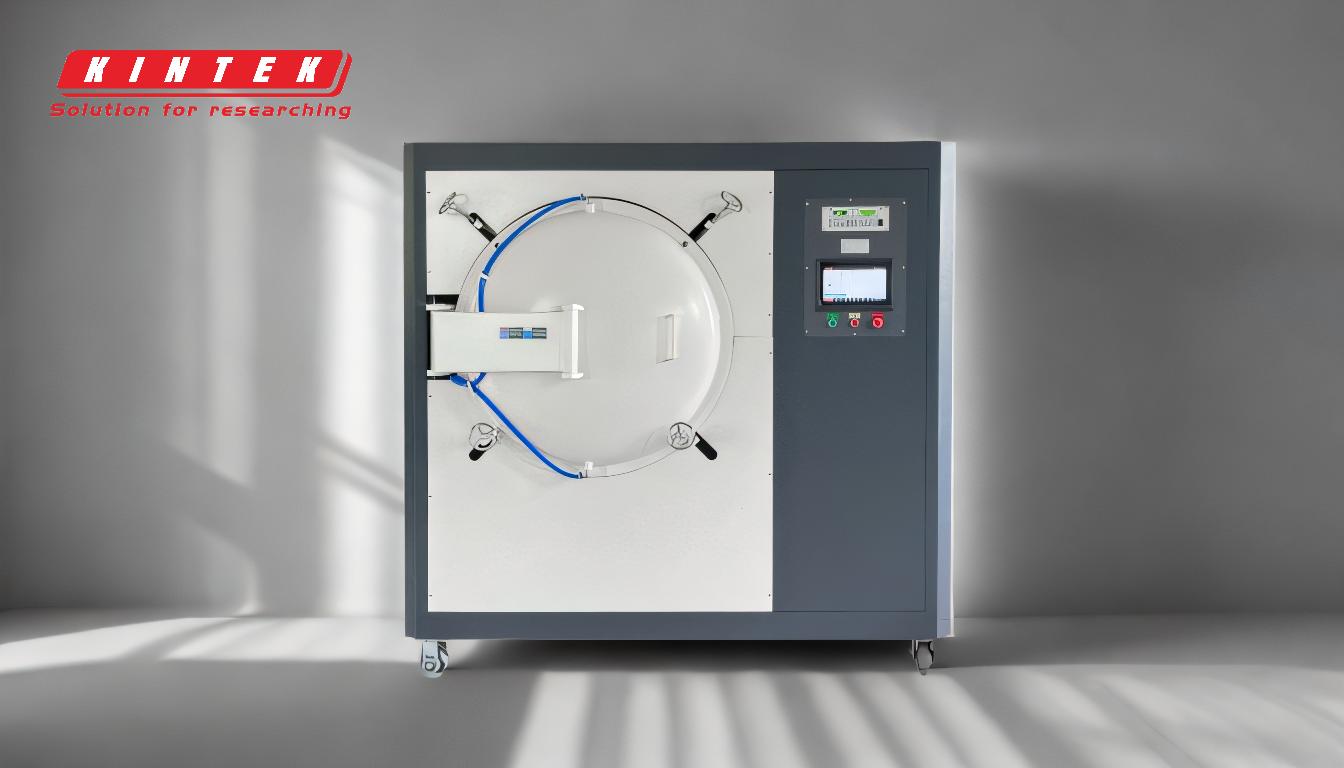
-
Finalidad de los gases protectores en la sinterización:
- Prevenir la oxidación: Los gases protectores crean una atmósfera inerte que impide que los metales calientes reaccionen con el oxígeno, lo que puede provocar la oxidación y degradación del material.
- Prevención de la descarburación: En el caso de materiales que contienen carbono, los gases protectores ayudan a evitar la pérdida de carbono, que puede debilitar el material.
- Mantenimiento de la presión atmosférica: Estos gases ayudan a mantener la presión necesaria dentro del horno de sinterización, asegurando unas condiciones de sinterización consistentes.
-
Gases de uso común en la sinterización:
-
Hidrógeno (H₂):
- Propiedades: El hidrógeno es un gas altamente reductor, lo que significa que puede eliminar el oxígeno de los óxidos metálicos, evitando la oxidación.
- Aplicaciones: Suele utilizarse en procesos de sinterización en los que se requieren condiciones reductoras, como en la sinterización de acero inoxidable u otras aleaciones.
- Ventajas: Las atmósferas a base de hidrógeno pueden dar lugar a un rendimiento más constante y a una mejor calidad superficial.
- Desventajas: El hidrógeno es altamente inflamable, por lo que requiere una manipulación cuidadosa y medidas de seguridad.
-
Nitrógeno (N₂):
- Propiedades: El nitrógeno es un gas inerte, lo que significa que no reacciona con la mayoría de los materiales, por lo que es ideal para crear una atmósfera inerte.
- Aplicaciones: Se utiliza habitualmente en las zonas de alto calor de los hornos de sinterización para evitar la oxidación.El nitrógeno se inyecta a través de puertos ajustados angularmente o en forma de chorros laminares transversales.
- Ventajas: El nitrógeno es rentable, fácil de conseguir y seguro de usar.
- Desventajas: Aunque es eficaz para evitar la oxidación, el nitrógeno no tiene propiedades reductoras, por lo que puede no ser adecuado para todos los materiales.
-
Monóxido de carbono (CO):
- Propiedades: El monóxido de carbono es un gas reductor que también puede actuar como agente carburante, añadiendo carbono al material que se sinteriza.
- Aplicaciones: Se utiliza en procesos de sinterización en los que se desean tanto efectos reductores como carburizantes, como en la sinterización de materiales a base de hierro.
- Ventajas: El monóxido de carbono puede mejorar las propiedades mecánicas del material sinterizado al aumentar su contenido en carbono.
- Desventajas: El monóxido de carbono es tóxico y requiere una manipulación y ventilación cuidadosas.
-
-
Selección de gases en función de los requisitos del material y del proceso:
- Consideraciones sobre el material: La elección del gas depende del material a sinterizar.Por ejemplo, el hidrógeno suele utilizarse para el acero inoxidable, mientras que el nitrógeno es preferible para los materiales no reactivos.
- Requisitos del proceso: El resultado deseado del proceso de sinterización también influye en la elección del gas.Por ejemplo, si se requiere carburación, el monóxido de carbono puede ser la mejor opción.
- Seguridad y coste: La seguridad y el coste también son factores importantes.El nitrógeno suele ser más seguro y rentable que el hidrógeno o el monóxido de carbono.
-
Métodos de inyección para gases protectores:
- Puertos ajustados angularmente: El nitrógeno suele inyectarse en el horno a través de puertos ajustados angularmente, lo que garantiza una distribución uniforme y una cobertura eficaz del material de sinterización.
- Chorros laminares transversales: Este método consiste en inyectar el gas en un patrón de flujo laminar, lo que ayuda a crear una atmósfera inerte uniforme y evita la oxidación localizada.
-
Impacto de la selección del gas en el rendimiento de la sinterización:
- Consistencia: El uso de gases protectores adecuados puede conducir a resultados de sinterización más consistentes, con menos defectos y mejores propiedades mecánicas.
- Calidad superficial: Las atmósferas a base de hidrógeno, en particular, pueden mejorar la calidad superficial de las piezas sinterizadas al reducir los óxidos superficiales.
- Propiedades mecánicas: La elección del gas también puede afectar a las propiedades mecánicas del material sinterizado, como la dureza, la resistencia y la tenacidad.
En resumen, la selección de gases en la sinterización es un factor crítico que influye en la calidad, la consistencia y el rendimiento del producto final.El hidrógeno, el nitrógeno y el monóxido de carbono son los gases más utilizados, cada uno de los cuales ofrece ventajas y retos únicos.La elección del gas debe basarse en el material que se va a sinterizar, los resultados deseados y las consideraciones de seguridad.También son esenciales unos métodos de inyección y una gestión del gas adecuados para garantizar una sinterización eficaz y unos resultados de alta calidad.
Cuadro sinóptico:
Gas | Propiedades | Aplicaciones | Ventajas | Desventajas |
---|---|---|---|---|
Hidrógeno (H₂) | Gas altamente reductor, evita la oxidación eliminando el oxígeno de los óxidos metálicos | Sinterización de acero inoxidable y aleaciones | Rendimiento constante, mejor calidad superficial | Altamente inflamable, requiere una manipulación cuidadosa |
Nitrógeno (N₂) | Gas inerte, no reacciona con la mayoría de los materiales | Zonas de alto calor para evitar la oxidación | Económico, fácil de conseguir, seguro de usar | Sin propiedades reductoras, puede no ser adecuado para todos los materiales |
Monóxido de carbono (CO) | Gas reductor, actúa como agente de carburación | Sinterización de materiales a base de hierro en los que es necesaria la carburación | Mejora las propiedades mecánicas al aumentar el contenido de carbono | Tóxico, requiere una manipulación y ventilación cuidadosas |
¿Necesita ayuda para seleccionar el gas adecuado para su proceso de sinterización? Póngase en contacto con nuestros expertos hoy mismo ¡!