Un horno de inducción de acero es un tipo de horno eléctrico utilizado para fundir y calentar acero y otros metales.Funciona según el principio de inducción electromagnética, en el que una corriente alterna (CA) pasa a través de una bobina, generando un campo magnético que induce corrientes de Foucault dentro del metal.Estas corrientes de Foucault producen calor y funden el metal.El horno es conocido por su eficacia, su control preciso de la temperatura y su capacidad para producir composiciones uniformes.Los componentes clave son el inductor, el cuerpo del horno, la fuente de alimentación, el condensador y el sistema de control.Características avanzadas como horno de inducción IGBT mejoran el rendimiento, ofreciendo una mayor eficiencia energética y un mejor control.
Explicación de los puntos clave:
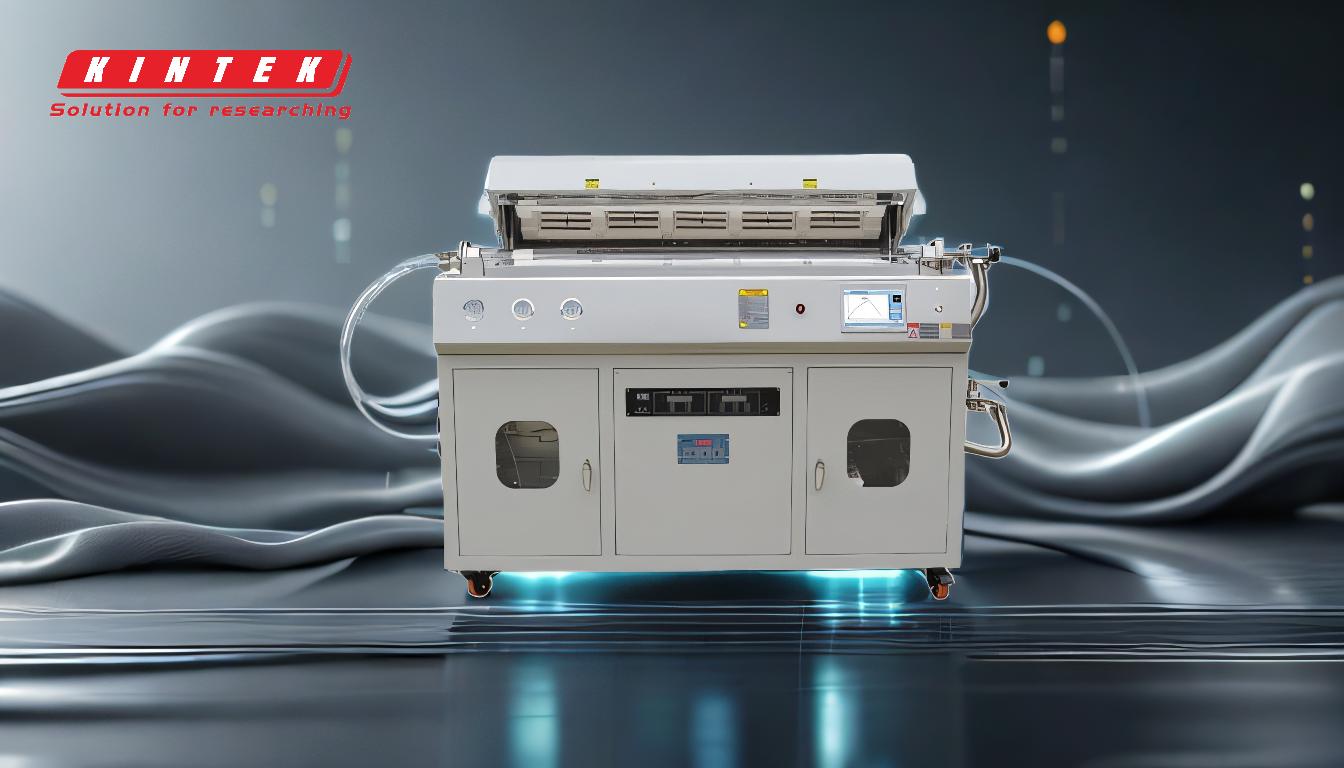
-
Principio de funcionamiento:
- El horno de inducción de acero funciona por inducción electromagnética.Una corriente alterna pasa a través de una bobina de inducción, creando un campo magnético.Este campo induce corrientes de Foucault dentro del metal, generando calor y fundiéndolo.Este método garantiza un calentamiento uniforme y un control preciso de la temperatura, lo que es crucial para producir acero de alta calidad.
-
Componentes clave:
- Inductor (Bobina):La bobina genera el campo magnético necesario para el calentamiento por inducción.Suele ser de cobre y está refrigerada por agua para evitar el sobrecalentamiento.
- Cuerpo del horno:Es la estructura que alberga el metal que se va a fundir.Está diseñada para soportar altas temperaturas y suele estar revestida de materiales refractarios.
- Alimentación eléctrica:Proporciona la corriente alterna necesaria para la inducción.Los hornos modernos suelen utilizar horno de inducción IGBT para mejorar la eficiencia y el control.
- Condensador:Ayuda a ajustar la fuente de alimentación a la frecuencia óptima para un calentamiento por inducción eficaz.
- Sistema de control:Gestiona el funcionamiento del horno, incluyendo el control de la temperatura, la regulación de la potencia y las funciones de seguridad.
-
Tipos de hornos de inducción:
- Horno de inducción sin núcleo:Comúnmente utilizado para fundir acero, no tiene núcleo y depende únicamente de la bobina de inducción para calentarse.
- Horno de inducción de canal:Dispone de un núcleo y se utiliza para mantener y sobrecalentar metal fundido.
- Horno de inducción de vacío:Funciona en condiciones de vacío, ideal para fundir metales y aleaciones de gran pureza.
-
Ventajas:
- Eficiencia:Los hornos de inducción son muy eficaces, ya que convierten la energía eléctrica directamente en calor con pérdidas mínimas.
- Precisión:Ofrecen un control preciso de la temperatura, esencial para producir acero de alta calidad con propiedades uniformes.
- Uniformidad:El proceso de inducción garantiza un calentamiento uniforme, dando lugar a una masa fundida homogénea.
- Beneficios medioambientales:Los hornos de inducción producen menos emisiones que los hornos tradicionales de combustible, por lo que son más respetuosos con el medio ambiente.
-
Aplicaciones:
- Producción de acero:Muy utilizado en la industria siderúrgica para fundir y refinar el acero.
- Fundiciones:Se utiliza para la fundición de diversas piezas y componentes metálicos.
- Producción de aleaciones:Ideal para producir aleaciones con composiciones precisas.
- Investigación y desarrollo:Se utiliza en los laboratorios para desarrollar nuevos materiales y comprobar las propiedades de los metales.
-
Mantenimiento y funcionamiento:
- Facilidad de mantenimiento:Los hornos de inducción modernos, especialmente aquellos con horno de inducción IGBT están diseñados para facilitar el mantenimiento.Componentes como la bobina de inducción y la fuente de alimentación son modulares y pueden sustituirse sin grandes tiempos de inactividad.
- Características de seguridad:Estos hornos vienen con sistemas de protección completos, que incluyen protecciones contra sobretensión, sobrecorriente y subtensión, lo que garantiza un funcionamiento seguro y fiable.
- Fácil de usar:Los diseños de circuitos integrados de alta simplifican la depuración, el funcionamiento y el aprendizaje, lo que facilita a los operarios la gestión del horno.
-
Avances tecnológicos:
- Tecnología IGBT:El uso de horno de inducción IGBT ha revolucionado los hornos de inducción, ofreciendo una mayor eficiencia energética, tiempos de respuesta más rápidos y un mejor control del proceso de fusión.
- Automatización:Los avanzados sistemas de control con exploración automática de frecuencias y funciones de arranque repetido garantizan un funcionamiento suave y estable, reduciendo la necesidad de intervención manual.
- Eficiencia energética:Los sistemas de control del circuito de potencia constante ajustan la tensión y la corriente automáticamente en función de la carga del horno, optimizando el uso de la energía y reduciendo los costes operativos.
En resumen, un horno de inducción para acero es una herramienta versátil y eficaz para fundir y calentar acero, que ofrece un control preciso, uniformidad y ventajas medioambientales.Con avances como horno de inducción IGBT la tecnología IGBT, estos hornos siguen evolucionando, proporcionando aún mayor eficiencia y facilidad de uso.
Cuadro sinóptico:
Aspecto | Detalles |
---|---|
Principio de funcionamiento | Inducción electromagnética con corrientes parásitas para un calentamiento uniforme. |
Componentes clave | Inductor, cuerpo del horno, fuente de alimentación, condensador, sistema de control. |
Tipos | Hornos de inducción sin núcleo, de canal y de vacío. |
Ventajas | Alta eficiencia, control preciso de la temperatura, uniformidad, respetuoso con el medio ambiente. |
Aplicaciones | Producción de acero, fundiciones, producción de aleaciones, I+D. |
Mantenimiento | Fácil mantenimiento, componentes modulares, funciones de seguridad avanzadas. |
Avances tecnológicos | Tecnología IGBT, automatización, mejoras de la eficiencia energética. |
¿Está preparado para mejorar su proceso de fusión de metales? Póngase en contacto con nosotros para obtener más información sobre los hornos de inducción de acero.