La frecuencia principal de un horno de inducción varía en función de la aplicación, el material que se funde y la capacidad del horno.Suele oscilar entre la frecuencia de servicio (50 o 60 Hz) y 400 kHz o más.Los volúmenes de fusión más pequeños requieren frecuencias más altas debido al efecto de profundidad de la piel, que garantiza un calentamiento y una fusión eficaces.En la frecuencia también influyen factores como el efecto de agitación deseado, la eficacia de la fusión y las propiedades del material.Los hornos de inducción están diseñados para funcionar dentro de rangos de frecuencia específicos para optimizar el rendimiento, la eficiencia energética y la uniformidad en los procesos de fusión o calentamiento.
Explicación de los puntos clave:
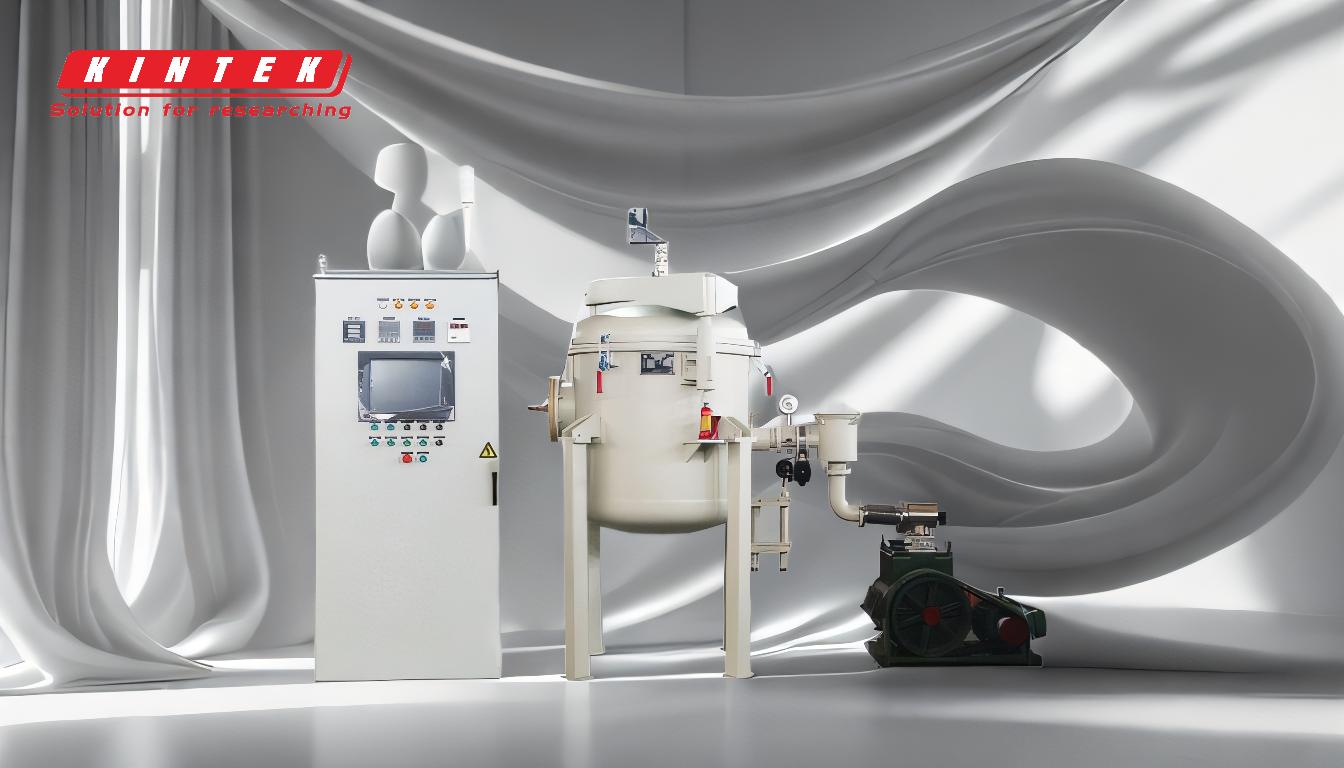
-
Gama de frecuencias de los hornos de inducción:
- Los hornos de inducción funcionan en una amplia gama de frecuencias, desde frecuencia de red (50 ó 60 Hz) a 400 kHz o superior .
- La elección de la frecuencia depende de la aplicación, el material y la capacidad del horno.
-
Factores que influyen en la selección de la frecuencia:
- Material que se funde:Los diferentes materiales tienen propiedades eléctricas y térmicas variables, que afectan a la frecuencia óptima.
- Capacidad del horno:Los hornos más pequeños suelen utilizar frecuencias más altas para garantizar un calentamiento y una fusión eficaces.
- Efecto de profundidad de la piel:Las frecuencias más altas dan lugar a una penetración menos profunda del campo electromagnético, lo que resulta ideal para volúmenes más pequeños.Las frecuencias más bajas se utilizan para volúmenes más grandes a fin de inducir agitación o turbulencia en el metal.
-
Ventajas de las frecuencias más altas:
- Eficiencia:Las frecuencias más altas permiten una mayor aplicación de potencia en hornos más pequeños, mejorando la eficacia de la fusión.
- Uniformidad:Las frecuencias más altas garantizan un calentamiento y una fusión uniformes gracias al efecto de profundidad de la piel.
- Turbulencia reducida:Las frecuencias más altas minimizan las turbulencias, lo que resulta beneficioso para determinados materiales y procesos.
-
Flexibilidad de diseño:
- La frecuencia de trabajo de los hornos de inducción de frecuencia media puede ajustarse cambiando el diseño de la bobina y condensador de compensación .
- Esta flexibilidad permite la personalización en función de factores como el material de fusión, la cantidad, el efecto de agitación, los niveles de ruido y la eficacia de la fusión.
-
Aplicaciones y capacidades de temperatura:
- Los hornos de inducción pueden alcanzar temperaturas de 1800°C o más lo que las hace adecuadas para fundir una amplia gama de materiales.
- La temperatura de calentamiento de la forja puede alcanzar 1250°C y la temperatura de fusión puede alcanzar 1650°C .
-
Características operativas:
- Exploración automática de frecuencias:Garantiza un funcionamiento suave y estable ajustando automáticamente la frecuencia.
- Control de potencia constante:Mantiene la tensión y la corriente constantes para un rendimiento óptimo.
- Sistemas de protección integral:Incluye mecanismos de sobretensión, sobrecorriente y otros mecanismos de seguridad para proteger el equipo.
-
Eficiencia energética y ventajas medioambientales:
- Los hornos de inducción de bajo consumo y respetuoso con el medio ambiente reduciendo los costes operativos.
- Garantizan una fundición uniforme y uniformidad de la composición mejora de la calidad del producto.
-
Consideraciones prácticas:
- Hornos pequeños:Suelen utilizar frecuencias más altas para una fusión eficaz de pequeñas cantidades.
- Hornos más grandes:Utilizar frecuencias más bajas para inducir la agitación y la turbulencia, lo que es beneficioso para volúmenes más grandes.
En resumen, la frecuencia principal de un horno de inducción es muy variable y depende de los requisitos específicos del proceso de fusión o calentamiento.Al comprender los factores que influyen en la selección de la frecuencia, los usuarios pueden optimizar el rendimiento del horno para sus aplicaciones específicas.
Tabla resumen:
Aspecto clave | Detalles |
---|---|
Gama de frecuencias | De 50/60 Hz a 400 kHz o más |
Factores que influyen en la elección | Material, capacidad del horno, efecto de profundidad de la piel, agitación y eficacia |
Ventajas de la alta frecuencia | Calentamiento eficaz, fusión uniforme, turbulencia reducida |
Flexibilidad de diseño | Ajustable mediante el diseño de la bobina y el condensador de compensación |
Capacidades de temperatura | Hasta 1800°C para fusión, 1250°C para forja |
Características operativas | Exploración automática de frecuencias, control de potencia constante, mecanismos de seguridad |
Eficiencia energética | Fundición uniforme, respetuosa con el medio ambiente y que ahorra energía |
¿Está listo para optimizar el rendimiento de su horno de inducción? Póngase en contacto con nuestros expertos para obtener soluciones a medida.