La pérdida por fusión de un horno de inducción se refiere a la reducción del peso del metal durante el proceso de fusión debido a factores como la oxidación, la evaporación y la formación de escoria. Esta pérdida está influenciada por varias variables, incluida la velocidad de fusión, la configuración de energía, la limpieza de la carga, el diseño del horno y los materiales refractarios utilizados. Una carga limpia, una longitud adecuada del bloque del horno y crisoles adecuados, como los crisoles de cuarzo, pueden minimizar la pérdida de fusión al mejorar la eficiencia y reducir el consumo de transferencia de calor. Además, el sobrecalentamiento debido a un flujo de agua inadecuado, dimensiones del revestimiento del horno o material refractario puede exacerbar la pérdida de fusión. Comprender estos factores ayuda a optimizar las operaciones del horno y reducir el desperdicio de material.
Puntos clave explicados:
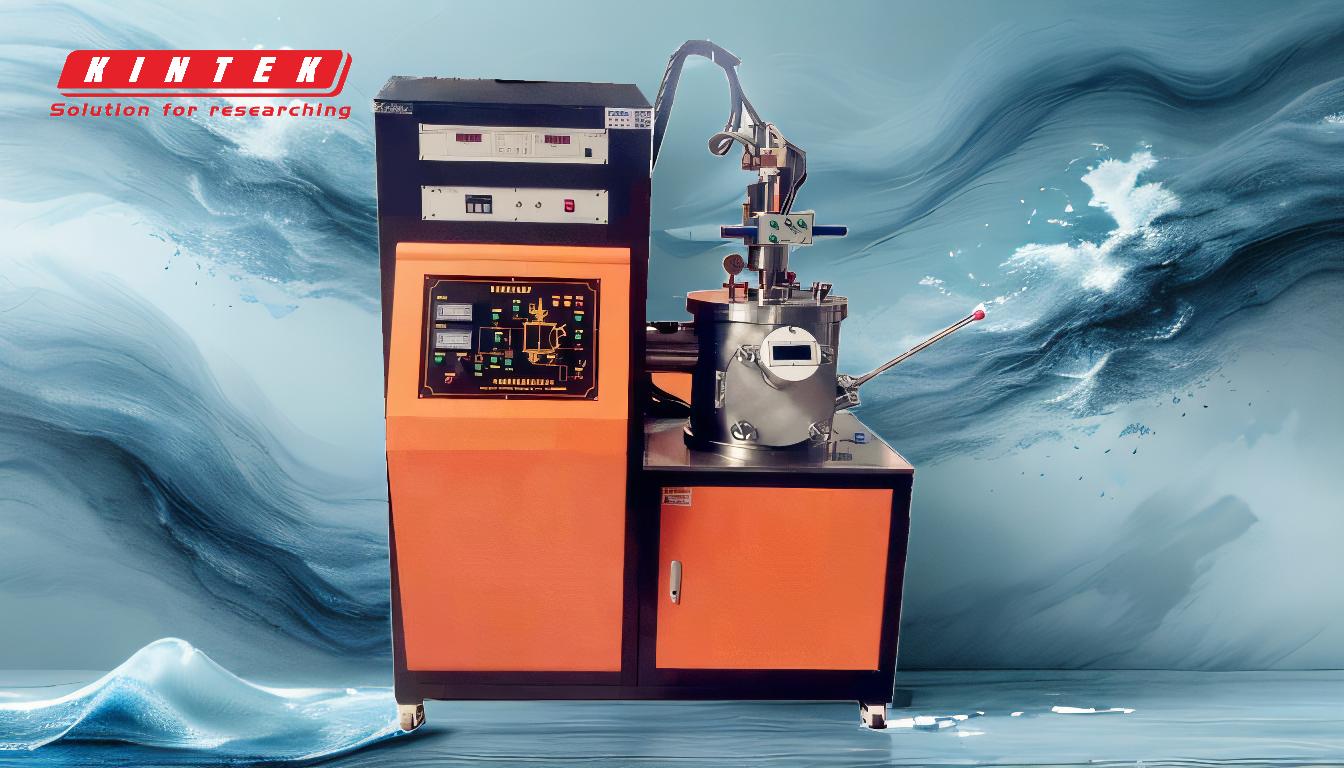
-
Definición de pérdida por fusión:
- La pérdida por fusión se refiere a la reducción del peso del metal durante el proceso de fusión en un horno de inducción. Esta pérdida se produce debido a la oxidación, evaporación y formación de escoria, que son inherentes al proceso de fusión.
-
Factores que influyen en la pérdida de fusión:
- Velocidad de fusión y configuración de potencia: La tasa de fusión, calculada como (Potencia en kW) / (Consumo de energía estándar en kWh/tonelada), impacta directamente en la pérdida de fusión. Las configuraciones de potencia más altas pueden reducir el tiempo de fusión, pero pueden aumentar la oxidación y la evaporación si no se controlan.
- Limpieza y tamaño de la carga: Una carga limpia con impurezas mínimas reduce la formación de escoria y la oxidación, minimizando así la pérdida por fusión. El tamaño de la carga también afecta la uniformidad de la fusión y la distribución del calor.
- Materiales refractarios y crisoles: El tipo de materiales refractarios y crisoles utilizados, como los crisoles de cuarzo, desempeña un papel importante a la hora de reducir la pérdida de transferencia de calor y mejorar la eficiencia general.
- Diseño y revestimiento de hornos: Las dimensiones adecuadas del revestimiento del horno y suficiente material refractario evitan el sobrecalentamiento y daños al serpentín, que de otro modo pueden provocar una mayor pérdida de fusión.
-
Sobrecalentamiento y su impacto:
- El sobrecalentamiento del serpentín del horno, causado por restricciones en la ruta del flujo de agua o por un diseño inadecuado del horno, puede provocar una mayor pérdida de fusión. El sobrecalentamiento acelera la oxidación y la evaporación, lo que contribuye a un mayor desperdicio de material.
-
Cálculo de la velocidad y el tiempo de fusión:
- La velocidad de fusión se calcula mediante la fórmula: (Potencia en kW) / (Consumo de energía estándar en kWh/tonelada) = (Peso del metal en kg) / (1000 kg). Por ejemplo, a 325 kW, la velocidad de fusión es de 520 kg/hora.
- El tiempo de fusión se calcula mediante la fórmula: (Potencia en kW * Tiempo en horas) / (Peso del metal en kg) = (Consumo de energía estándar en kWh/tonelada * 1 hora) / (1000 kg). Para un horno de 550 kg con una potencia de 325 kW, el tiempo de fusión es de 1,06 horas (64 minutos).
-
Estrategias de optimización:
- Carga limpia: Garantizar que la carga esté libre de impurezas y contaminantes reduce la formación de escoria y la oxidación.
- Diseño adecuado del horno: Mantener la longitud adecuada del bloque del horno y las dimensiones del revestimiento evita el sobrecalentamiento y mejora la eficiencia.
- Crisoles adecuados: El uso de crisoles como los de cuarzo reduce la pérdida de transferencia de calor y mejora la eficiencia de la fusión.
- Mantenimiento regular: La inspección y el mantenimiento periódicos de las rutas de flujo de agua, los intercambiadores de calor y los cables de alimentación evitan el sobrecalentamiento y garantizan un rendimiento constante.
Al comprender y abordar estos factores, los operadores pueden minimizar la pérdida de fusión, mejorar la eficiencia del horno y reducir el desperdicio de material en las operaciones de los hornos de inducción.
Tabla resumen:
Factor clave | Impacto en la pérdida por fusión |
---|---|
Tasa de fusión y potencia | Una potencia más alta reduce el tiempo de fusión pero puede aumentar la oxidación y la evaporación. |
Limpieza y tamaño de la carga | Las cargas limpias minimizan la formación de escoria y la oxidación, reduciendo la pérdida por fusión. |
Materiales refractarios | Los materiales adecuados, como los crisoles de cuarzo, reducen la pérdida de transferencia de calor y mejoran la eficiencia. |
Diseño y revestimiento de hornos | Las dimensiones adecuadas evitan el sobrecalentamiento y el daño del serpentín, lo que reduce el desperdicio de material. |
Calentamiento excesivo | El sobrecalentamiento acelera la oxidación y la evaporación, aumentando la pérdida por fusión. |
Optimice las operaciones de su horno de inducción y reduzca las pérdidas por fusión. contacte a nuestros expertos hoy ¡Para soluciones personalizadas!