La temperatura más adecuada para quemar cemento en un horno rotatorio suele oscilar entre 1400°C a 1500°C . Este rango de temperaturas garantiza la correcta formación del clínker, que es el producto intermedio en la fabricación del cemento. Por debajo de este intervalo, las reacciones químicas necesarias para la formación de clínker pueden ser incompletas, mientras que las temperaturas por encima de este intervalo pueden provocar un consumo excesivo de energía y posibles daños en el revestimiento del horno. El proceso consiste en calentar las materias primas (piedra caliza, arcilla y otros aditivos) a este rango de temperatura para facilitar las reacciones químicas que producen el clínker de cemento.
Explicación de los puntos clave:
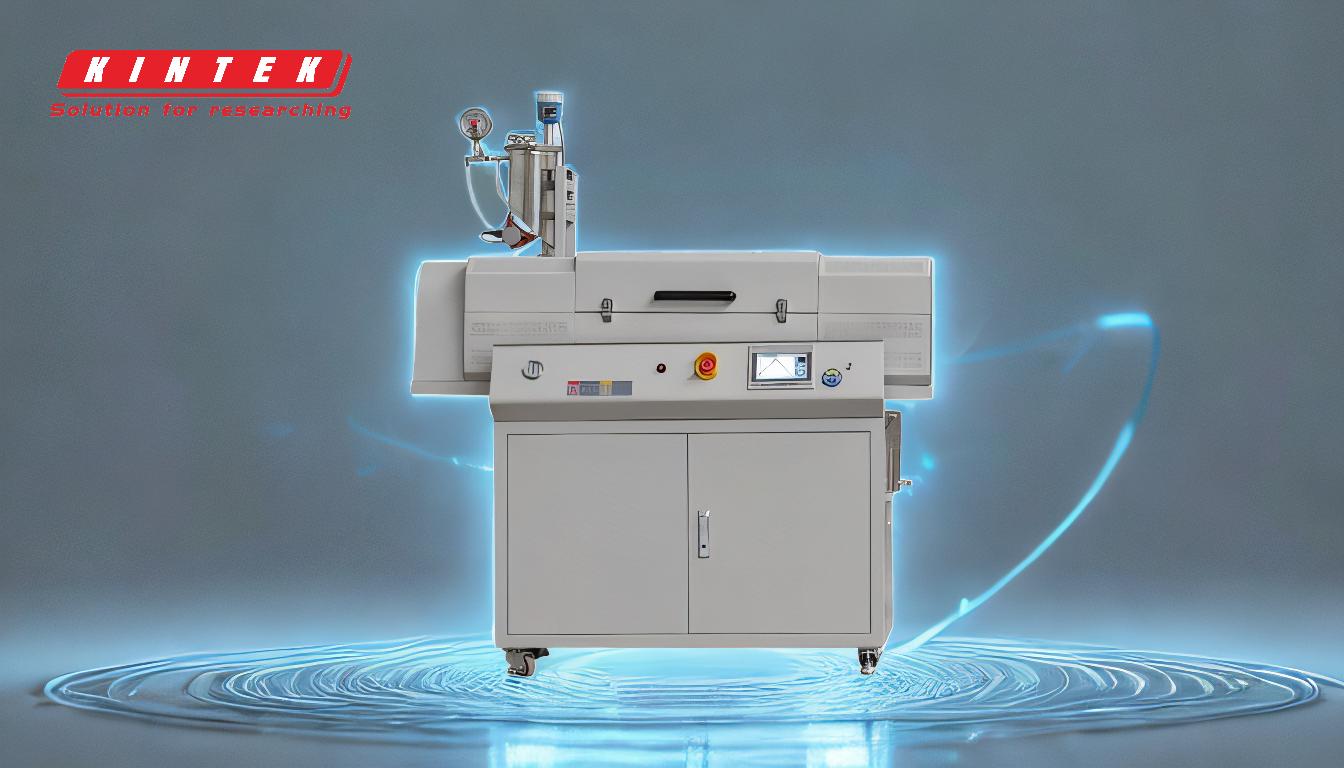
-
Rango óptimo de temperatura para la cocción del cemento:
- El intervalo de temperatura ideal para quemar cemento en un horno rotatorio es de 1400°C a 1500°C . Este intervalo es crítico para la formación de clínker, que es el componente principal del cemento.
- A esta temperatura, las materias primas sufren una serie de reacciones químicas, como la calcinación (descomposición de la piedra caliza en cal) y la sinterización (formación de compuestos del clínker como la alita y la belita).
-
Por qué de 1400°C a 1500°C es adecuado:
- Reacciones químicas: A temperaturas inferiores a 1400°C, las reacciones químicas necesarias para la formación de clínker pueden no llegar a completarse, dando lugar a un clínker de mala calidad. Por encima de 1500°C, las reacciones pueden llegar a ser demasiado intensas, provocando un exceso de combustión e ineficiencia energética.
- Eficiencia energética: Mantener la temperatura dentro de este rango garantiza un uso eficiente de la energía. Las temperaturas excesivas provocan un mayor consumo de combustible y un aumento de los costes operativos.
- Protección del revestimiento del horno: La exposición prolongada a temperaturas superiores a 1500°C puede dañar el revestimiento refractario del horno, reduciendo su vida útil y aumentando los costes de mantenimiento.
-
Comparación con otros tipos de hornos:
- Hornos Rotativos Indirectos: Estos hornos funcionan normalmente a temperaturas más bajas (1200-1300°C para el tubo del horno y menos de 1150°C para el material). No son adecuados para la producción de cemento, ya que no pueden alcanzar las temperaturas necesarias para la formación de clínker.
- Hornos rotatorios eléctricos: Con una temperatura máxima de trabajo de 1100°C, los hornos rotatorios eléctricos tampoco son adecuados para la producción de cemento debido a su incapacidad para alcanzar las temperaturas necesarias para la formación del clínker.
-
Factores que influyen en la selección de la temperatura:
- Composición de la materia prima: La composición química de las materias primas puede influir en la temperatura de combustión requerida. Por ejemplo, las materias primas con mayor contenido en sílice pueden requerir temperaturas ligeramente superiores.
- Diseño del horno: El diseño del horno rotatorio, incluida su longitud, diámetro y revestimiento refractario, puede afectar a la distribución de la temperatura y a la eficacia de la transferencia de calor.
- Tipo de combustible: El tipo de combustible utilizado (por ejemplo, carbón, gas natural o combustibles alternativos) puede influir en la temperatura de combustión y, en consecuencia, en la temperatura global del horno.
-
Consideraciones prácticas:
- Control de la temperatura: El control preciso de la temperatura es esencial para mantener las condiciones óptimas de combustión. Esto se consigue normalmente mediante sistemas de control avanzados que supervisan y ajustan el suministro de combustible y aire.
- Proceso de enfriamiento: Una vez formado el clínker, debe enfriarse rápidamente para preservar su calidad. Esto suele hacerse en un enfriador adosado al horno, donde el clínker se enfría desde unos 1400°C hasta menos de 200°C.
-
Impacto de la temperatura en la calidad del cemento:
- Calidad del clínker: La temperatura afecta directamente a la calidad del clínker, que a su vez influye en la resistencia y durabilidad del producto final de cemento.
- Consumo de energía: Operar dentro del rango óptimo de temperatura minimiza el consumo de energía, haciendo que el proceso sea más rentable y respetuoso con el medio ambiente.
- Consideraciones medioambientales: Mantener la temperatura correcta ayuda a reducir las emisiones de contaminantes como los óxidos de nitrógeno (NOx) y el dióxido de azufre (SO2), que son subproductos de la combustión a alta temperatura.
En resumen, la temperatura más adecuada para la combustión de cemento en un horno rotatorio se sitúa entre 1400°C y 1500°C. Este intervalo garantiza una formación eficaz del clínker, la eficiencia energética y la protección del revestimiento del horno, al tiempo que contribuye a la producción de cemento de alta calidad.
Tabla resumen:
Aspecto | Detalles |
---|---|
Temperatura óptima | 1400°C a 1500°C |
Finalidad | Garantiza la correcta formación del clínker y la eficiencia energética |
Reacciones químicas | La calcinación y la sinterización se producen en este rango |
Eficiencia energética | Minimiza el consumo de combustible y los costes operativos |
Protección del revestimiento del horno | Evita daños en el revestimiento refractario |
Calidad del cemento | El clínker de alta calidad da lugar a un cemento duradero y resistente |
Impacto medioambiental | Reduce las emisiones de NOx y SO2 |
¿Necesita asesoramiento experto para optimizar su horno rotatorio para la producción de cemento? Póngase en contacto con nosotros para obtener más información.