El calentamiento por horno de inducción es un método altamente eficiente y preciso para fundir y calentar metales conductores. El proceso se basa en la inducción electromagnética, donde una corriente alterna genera un campo magnético dentro de una bobina de cobre, induciendo corrientes parásitas en la carga metálica. Estas corrientes parásitas generan calor mediante calentamiento Joule, derritiendo el metal interna y uniformemente. El proceso es limpio, energéticamente eficiente y permite un control preciso de la temperatura, lo que lo hace ideal para aplicaciones como fundición de metales y producción de aleaciones. La frecuencia de la corriente alterna determina la profundidad de la penetración del calor y el efecto de agitación de las corrientes parásitas garantiza una mezcla uniforme del metal fundido.
Puntos clave explicados:
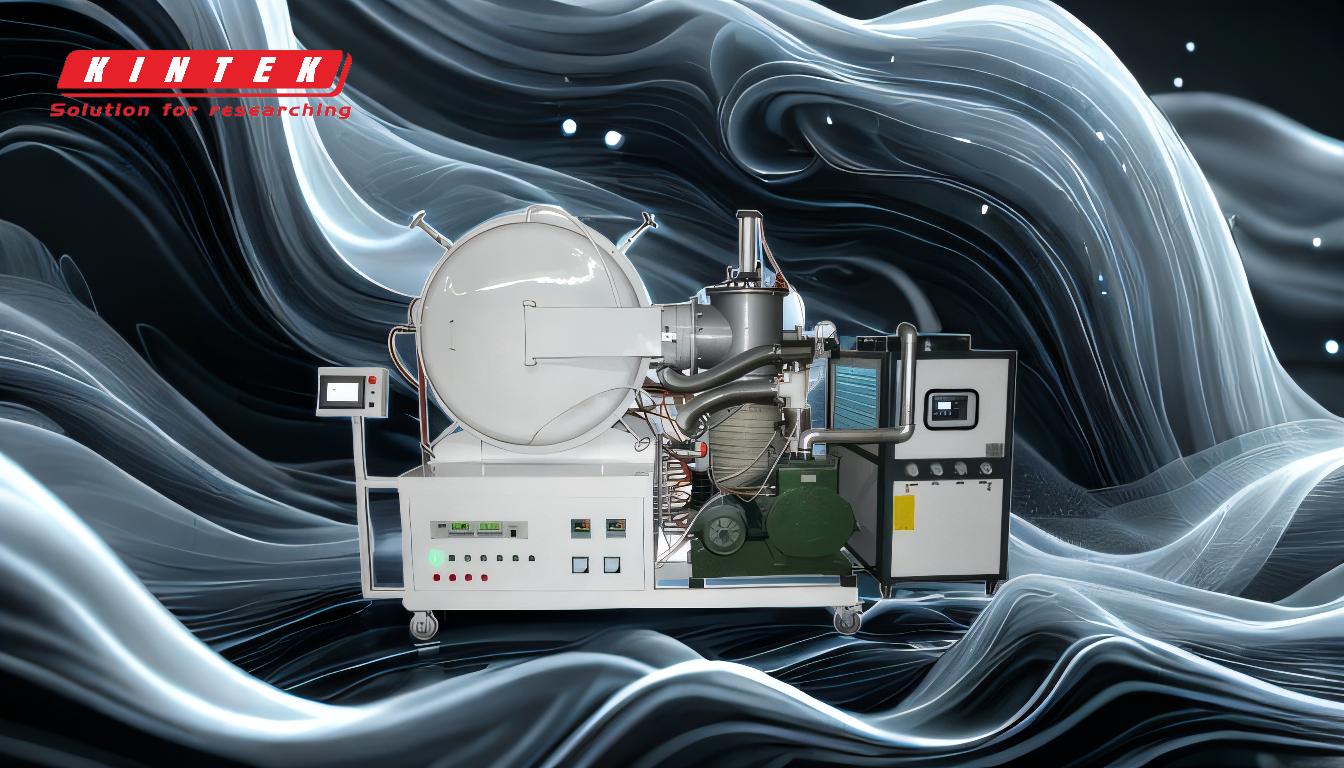
-
Principio de inducción electromagnética:
- Un horno de inducción funciona según el principio de inducción electromagnética. Se hace pasar una corriente alterna (CA) a través de una bobina de cobre hueca, creando un campo magnético que se invierte rápidamente.
- Cuando se coloca una carga metálica conductora dentro de este campo magnético, se inducen corrientes parásitas dentro del metal. Estas corrientes fluyen a través de la resistencia eléctrica del metal, generando calor mediante calentamiento Joule.
- El calor se produce directamente dentro del metal, lo que garantiza un calentamiento eficiente y uniforme sin una pérdida significativa de calor hacia la estructura del horno.
-
Componentes de un horno de inducción:
- Bobina de cobre: La bobina, a menudo hecha de cobre debido a su alta conductividad, transporta la corriente alterna y genera el campo magnético.
- Fuente de alimentación: La unidad de potencia convierte CA trifásica estándar en una corriente de frecuencia media (150 Hz–8000 Hz) adecuada para calentamiento por inducción.
- Crisol: El recipiente que contiene la carga metálica suele estar hecho de materiales refractarios para soportar altas temperaturas.
- Sistema de enfriamiento: Es posible que sea necesario enfriar el serpentín y otros componentes para evitar el sobrecalentamiento durante el funcionamiento.
-
Proceso de calentamiento:
- La corriente alterna en la bobina crea un campo magnético que penetra la carga metálica.
- Las corrientes parásitas inducidas en el metal generan calor internamente, elevando rápidamente la temperatura hasta el punto de fusión.
- La frecuencia de la corriente alterna determina la profundidad de la penetración del calor. Las frecuencias más altas dan como resultado una penetración más superficial, mientras que las frecuencias más bajas permiten un calentamiento más profundo.
-
Ventajas del calentamiento por inducción:
- Eficiencia: El calor se genera directamente dentro del metal, minimizando la pérdida de energía.
- Precisión: El proceso permite un control preciso de la temperatura, esencial para crear aleaciones con composiciones exactas.
- Limpieza: El calentamiento por inducción no implica combustión, lo que lo convierte en un proceso más limpio en comparación con los hornos tradicionales.
- Calefacción uniforme: El efecto de agitación de las corrientes parásitas garantiza una distribución uniforme de la temperatura y la mezcla del metal fundido.
-
Aplicaciones de los hornos de inducción:
- Fundición de metales: Los hornos de inducción se utilizan ampliamente en fundiciones para fundir metales como acero, hierro y aleaciones no ferrosas.
- Producción de aleaciones: El control preciso de la temperatura hace que los hornos de inducción sean ideales para crear aleaciones con propiedades específicas.
- Tratamiento térmico: El calentamiento por inducción también se utiliza para el endurecimiento de superficies y otros procesos de tratamiento térmico.
-
Consideraciones de temperatura y frecuencia:
- La temperatura alcanzada depende del metal que se está fundiendo. Por ejemplo, el acero requiere temperaturas de hasta 1370°C (2500°F).
- La frecuencia de la corriente alterna se elige en función de la profundidad deseada de penetración del calor y del tipo de metal que se procesa.
-
Efecto de agitación:
- Las corrientes parásitas no sólo generan calor sino que también crean un movimiento de agitación dentro del metal fundido. Esto garantiza la homogeneidad en la masa fundida, lo cual es fundamental para producir aleaciones y piezas fundidas de alta calidad.
Al aprovechar estos principios y componentes, los hornos de inducción proporcionan un método confiable y eficiente para calentar y fundir metales, lo que los hace indispensables en los procesos metalúrgicos modernos.
Tabla resumen:
Aspecto | Detalles |
---|---|
Principio | La inducción electromagnética genera corrientes parásitas para el calentamiento interno. |
Componentes clave | Bobina de cobre, fuente de alimentación, crisol, sistema de refrigeración. |
Proceso de calentamiento | La corriente alterna induce calor directamente en el metal para una fusión uniforme. |
Ventajas | Alta eficiencia, control preciso de temperatura, limpieza, calentamiento uniforme. |
Aplicaciones | Fundición de metales, producción de aleaciones, tratamiento térmico. |
Rango de temperatura | Hasta 1370°C (2500°F) para acero. |
Impacto de frecuencia | Determina la profundidad de penetración del calor y el efecto de agitación. |
Descubra cómo el calentamiento por horno de inducción puede revolucionar su procesamiento de metales. contacte a nuestros expertos hoy !