El horno de inducción es un equipo fundamental en la fabricación de acero, sobre todo para fundir acero y producir aleaciones con composiciones precisas. Funciona utilizando energía eléctrica para generar calor mediante inducción electromagnética, eliminando la necesidad de combustión externa o gases. El proceso consiste en cargar acero en un crisol rodeado por un electroimán de cobre en espiral. Cuando recibe energía, la bobina crea un campo magnético inverso que induce corrientes de Foucault en el metal. Estas corrientes generan calor y funden el acero al tiempo que lo agitan. Una vez que el acero alcanza la temperatura deseada (alrededor de 1650°C), se introduce en una cuchara para su posterior procesamiento. Este método es eficaz, limpio y permite un control preciso del proceso de fusión.
Explicación de los puntos clave:
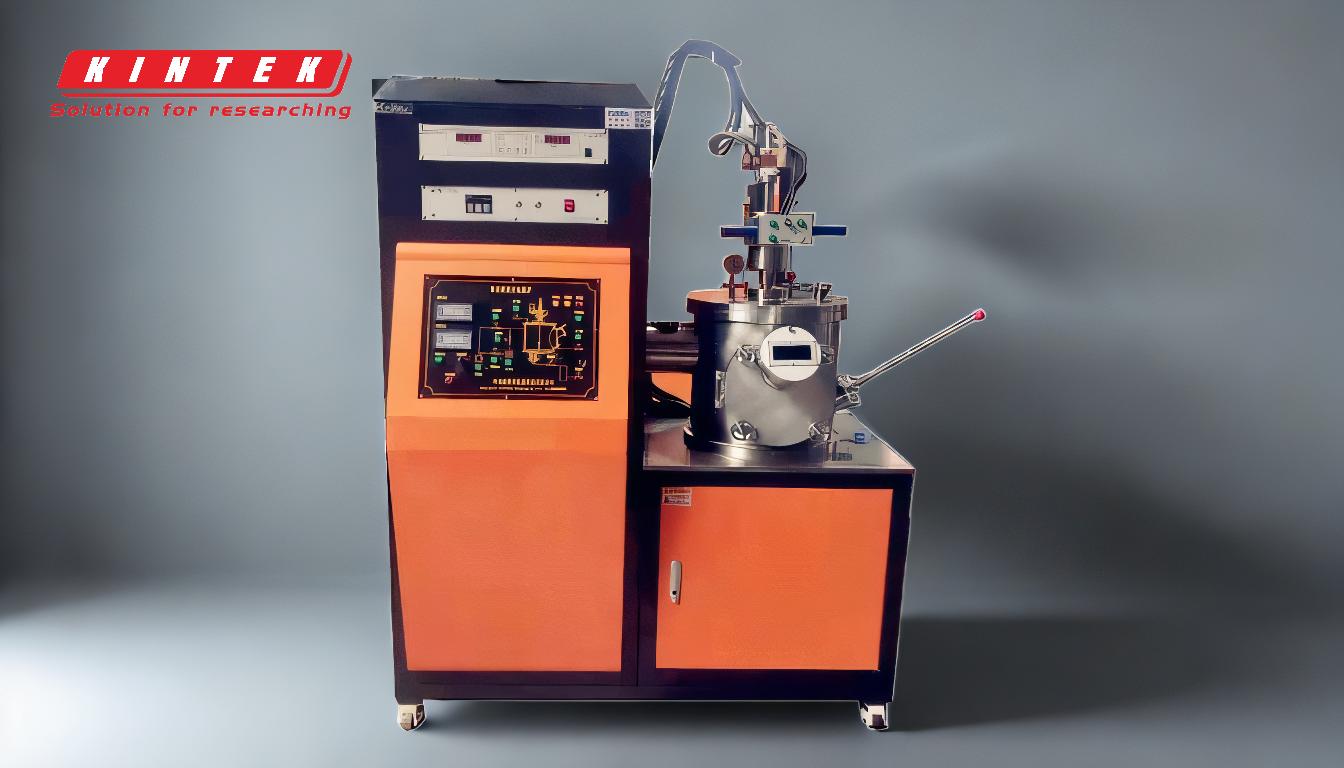
-
Funcionamiento básico de un horno de inducción:
- El horno de inducción utiliza la inducción electromagnética para generar calor. Una fuente eléctrica de alta tensión alimenta una bobina primaria, que induce un flujo de baja tensión y alta corriente en el metal (bobina secundaria).
- La corriente alterna en la bobina crea un campo magnético inverso que induce corrientes de Foucault en la carga metálica. Estas corrientes generan calor debido a la resistencia del metal, fundiéndolo eficazmente.
-
Componentes de un horno de inducción:
- Crisol: Recipiente de material refractario que contiene la carga metálica durante la fusión.
- Bobina de cobre: Rodea el crisol y transporta corriente alterna para crear el campo magnético.
- Fuente de alimentación: Proporciona la corriente alterna de alta frecuencia necesaria para el calentamiento por inducción.
- Sistema de refrigeración: Garantiza que la bobina y otros componentes no se sobrecalienten durante el funcionamiento.
-
Proceso de fusión:
- La carga de acero se carga en el crisol.
- La bobina de inducción se alimenta, creando un campo magnético que induce corrientes de Foucault en el metal.
- Las corrientes de Foucault generan calor, fundiendo el acero. El campo magnético también provoca la autoagitación, lo que garantiza la uniformidad de la temperatura y la composición.
- El proceso continúa hasta que el acero alcanza la temperatura deseada (normalmente alrededor de 1650°C).
-
Ventajas de los hornos de inducción:
- Eficiencia energética: Los hornos de inducción convierten la energía eléctrica directamente en calor con pérdidas mínimas.
- Precisión: El proceso permite un control preciso de la temperatura y la composición, por lo que es ideal para producir aleaciones de alta calidad.
- Funcionamiento limpio: No requiere gases de combustión ni oxígeno, lo que reduce las emisiones y la contaminación.
- Diseño compacto: Los hornos de inducción son relativamente pequeños en comparación con otros hornos de fusión, lo que los hace adecuados para fundiciones con espacio limitado.
-
Aplicaciones en la fabricación de acero:
- Los hornos de inducción se utilizan mucho en las fundiciones para fundir acero y producir aleaciones.
- Son especialmente útiles para la producción a pequeña y mediana escala, donde la precisión y la flexibilidad son fundamentales.
- La capacidad de producir acero limpio y de alta calidad hace que los hornos de inducción sean ideales para aplicaciones especializadas, como las industrias aeroespacial y automovilística.
-
Comparación con otros procesos siderúrgicos:
- Horno eléctrico de arco (EAF): A diferencia de los hornos de inducción, los EAF utilizan un arco eléctrico para generar calor. Mientras que los EAF son adecuados para la producción a gran escala, los hornos de inducción ofrecen una mayor precisión y son más eficientes para lotes más pequeños.
- Alto horno: Los altos hornos se basan en la combustión y se utilizan principalmente para la producción de hierro a gran escala. Los hornos de inducción, en cambio, son más versátiles y respetuosos con el medio ambiente.
-
Retos y limitaciones:
- Coste inicial: Los hornos de inducción requieren una importante inversión inicial en equipos y suministro eléctrico.
- Mantenimiento: El crisol y la bobina requieren un mantenimiento regular para garantizar un funcionamiento eficaz.
- Escalabilidad: Aunque son ideales para la producción a pequeña y mediana escala, los hornos de inducción pueden no ser rentables para la fabricación de acero a muy gran escala.
En resumen, el horno de inducción es una herramienta muy eficaz y precisa para la fabricación de acero, que ofrece numerosas ventajas en términos de eficiencia energética, limpieza y control. Su capacidad para producir acero y aleaciones de alta calidad lo hace indispensable en las fundiciones modernas, sobre todo para aplicaciones especializadas. Sin embargo, es esencial tener en cuenta los costes iniciales y los requisitos de mantenimiento a la hora de elegir esta tecnología.
Cuadro recapitulativo:
Aspecto | Detalles |
---|---|
Operación | Utiliza la inducción electromagnética para generar calor para fundir acero. |
Componentes | Crisol, bobina de cobre, fuente de alimentación, sistema de refrigeración. |
Proceso de fusión | El acero se calienta a ~1650°C, con autoagitación para una composición uniforme. |
Ventajas | Eficiente energéticamente, precisa, limpia y compacta. |
Aplicaciones | Ideal para la producción de acero y aleaciones a pequeña y mediana escala. |
Desafíos | Coste inicial elevado, requisitos de mantenimiento, escalabilidad limitada. |
Descubra cómo un horno de inducción puede mejorar su proceso de fabricación de acero contacte con nosotros para obtener asesoramiento experto