El depósito físico en fase vapor (PVD) es un proceso utilizado para depositar películas finas de material sobre un sustrato mediante la transición del material de una fase sólida a una fase vapor y su posterior condensación en forma sólida sobre el sustrato.Este proceso suele llevarse a cabo en una cámara de vacío para minimizar la contaminación y garantizar un entorno controlado.El PVD se utiliza ampliamente en industrias como la electrónica, la óptica y la fabricación debido a su capacidad para producir revestimientos muy duraderos, resistentes a la corrosión y tolerantes a la temperatura.El proceso consta de varios pasos clave: vaporización del material objetivo, transporte del vapor a través de la cámara y condensación en el sustrato.Los métodos de PVD incluyen la evaporación térmica, el sputtering y la descarga de arco, cada uno de los cuales ofrece ventajas únicas en función de la aplicación.
Explicación de los puntos clave:
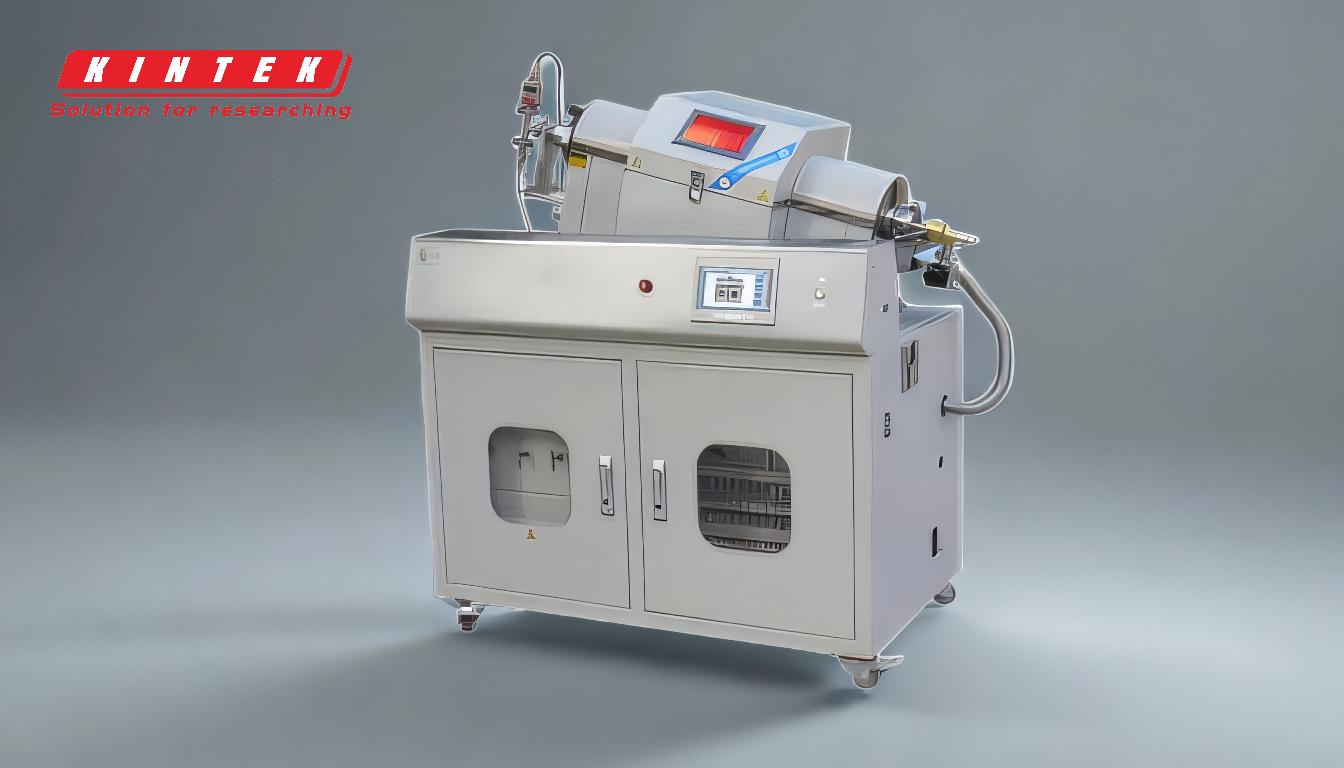
-
Transición de la fase sólida a la fase vapor:
- El principio básico del PVD es la conversión de un material objetivo sólido en una fase de vapor.Esto se consigue mediante diversos métodos, como la evaporación térmica, la pulverización catódica o la descarga de arco.El material objetivo suele ser un metal o una cerámica, elegido en función de las propiedades deseadas del revestimiento final.
- Evaporación térmica:Consiste en calentar el material objetivo hasta que se evapora.Este método suele utilizarse para materiales con puntos de fusión relativamente bajos.
- Pulverización catódica:Utiliza partículas de alta energía (normalmente iones de argón) para desprender átomos del material objetivo, creando un vapor.Este método es adecuado para materiales con puntos de fusión elevados.
- Descarga por arco:Consiste en crear un arco eléctrico que vaporiza el material objetivo.Este método es especialmente eficaz para depositar revestimientos duros como el nitruro de titanio.
-
Transporte de vapor en una cámara de vacío:
- Una vez vaporizado el material objetivo, el vapor se transporta a través de una cámara de vacío.El entorno de vacío es crucial, ya que minimiza la presencia de contaminantes y garantiza que el vapor se desplace en línea recta (línea de visión) hasta el sustrato.
- La cámara de vacío suele mantenerse a una temperatura de entre 50 y 600 grados Celsius, en función de los requisitos específicos del proceso de revestimiento.
-
Condensación en el sustrato:
- El material vaporizado se desplaza por la cámara y se condensa sobre el sustrato, formando una fina película.El sustrato puede estar hecho de diversos materiales, como metales, cerámica o polímeros, en función de la aplicación.
- El proceso de condensación da como resultado un recubrimiento muy adherente y uniforme.Las películas finas producidas por PVD suelen tener un grosor de sólo unos nanómetros o micrómetros, lo que las hace ideales para aplicaciones que requieren precisión y durabilidad.
-
Tipos de métodos PVD:
- Evaporación térmica:Este método consiste en calentar el material objetivo hasta que se evapora.A continuación, el vapor se condensa en el sustrato.Se suele utilizar para depositar metales como el aluminio y el oro.
- Pulverización catódica:En este método, partículas de alta energía bombardean el material objetivo, provocando la expulsión de átomos que se depositan sobre el sustrato.El sputtering es versátil y puede utilizarse con una amplia gama de materiales, como metales, aleaciones y cerámicas.
- Descarga por arco:Este método utiliza un arco eléctrico para vaporizar el material objetivo.Es especialmente eficaz para depositar revestimientos duros como el nitruro de titanio, que se utiliza en herramientas de corte y aplicaciones resistentes al desgaste.
-
Ventajas del PVD:
- Alta adherencia:Los revestimientos PVD son conocidos por su excelente adherencia al sustrato, que es crucial para aplicaciones que requieren durabilidad y resistencia al desgaste.
- Versatilidad de materiales:El PVD puede utilizarse para depositar una amplia gama de materiales, como metales, cerámicas e incluso algunos polímeros.Esto la convierte en una técnica versátil para diversas aplicaciones industriales.
- Resistencia a altas temperaturas:Los revestimientos de PVD pueden soportar altas temperaturas, lo que los hace adecuados para su uso en entornos difíciles, como en aplicaciones aeroespaciales o de automoción.
- Resistencia a la corrosión:Los revestimientos producidos por PVD son muy resistentes a la corrosión, lo que resulta esencial para aplicaciones expuestas a entornos corrosivos, como las industrias naval o de procesamiento químico.
-
Aplicaciones del PVD:
- Electrónica:El PVD se utiliza para depositar películas finas en la fabricación de semiconductores, paneles solares y pantallas.La precisión y uniformidad de los revestimientos PVD son fundamentales para el rendimiento de los componentes electrónicos.
- Óptica:El PVD se emplea para crear revestimientos reflectantes y antirreflectantes en lentes, espejos y otros componentes ópticos.Estos revestimientos mejoran el rendimiento y la durabilidad de los dispositivos ópticos.
- Fabricación:El PVD se utiliza ampliamente en la producción de herramientas de corte, moldes y componentes resistentes al desgaste.Los recubrimientos duros producidos por PVD prolongan la vida útil de estas herramientas y mejoran su rendimiento.
-
Retos y consideraciones:
- Complejidad del proceso:El PVD requiere equipos especializados y un entorno controlado, lo que puede resultar costoso y complejo de configurar y mantener.
- Limitaciones de los materiales:Aunque el PVD es versátil, no todos los materiales son adecuados para la deposición mediante este método.Algunos materiales pueden requerir condiciones específicas o técnicas de deposición alternativas.
- Control de uniformidad y espesor:Conseguir revestimientos uniformes con espesores precisos puede ser todo un reto, especialmente en el caso de geometrías complejas o sustratos de gran tamaño.A menudo son necesarios sistemas y técnicas de control avanzados para garantizar resultados uniformes.
En resumen, el depósito físico en fase vapor (PVD) es una técnica sofisticada y versátil para depositar películas finas de material sobre sustratos.Consiste en la conversión de un material sólido en una fase de vapor, el transporte del vapor en una cámara de vacío y la condensación en el sustrato para formar una película fina.El PVD ofrece numerosas ventajas, como una gran adherencia, versatilidad de materiales y resistencia a altas temperaturas y a la corrosión.Sin embargo, también presenta retos como la complejidad del proceso y la necesidad de un control preciso de la uniformidad y el grosor del revestimiento.A pesar de estos retos, el PVD sigue siendo una tecnología fundamental en sectores que van desde la electrónica a la fabricación, donde los revestimientos de alto rendimiento son esenciales.
Tabla resumen:
Aspecto | Detalles |
---|---|
Proceso | Convierte el material sólido en vapor, transporta en vacío, condensa en el sustrato. |
Métodos | Evaporación térmica, pulverización catódica, descarga de arco. |
Ventajas | Alta adherencia, versatilidad de materiales, resistencia a la temperatura y a la corrosión. |
Aplicaciones | Electrónica, óptica, fabricación (herramientas de corte, revestimientos resistentes al desgaste). |
Retos | Complejidad del proceso, limitaciones de los materiales, control de la uniformidad. |
Descubra cómo el PVD puede mejorar sus productos póngase en contacto con nuestros expertos para obtener soluciones a medida.