Las piezas sinterizadas se fabrican mediante un proceso de varios pasos que transforma los materiales en polvo en componentes sólidos y duraderos.El proceso suele consistir en preparar una mezcla de polvo, compactarla para darle la forma deseada y, a continuación, sinterizarla a altas temperaturas para unir las partículas.Este método se utiliza ampliamente para metales, cerámicas y otros materiales, y ofrece un control preciso de las propiedades del material y de geometrías complejas.El proceso de sinterización garantiza que el producto final tenga integridad estructural, porosidad reducida y propiedades mecánicas mejoradas.A continuación se explican en detalle los pasos clave y su importancia.
Explicación de los puntos clave:
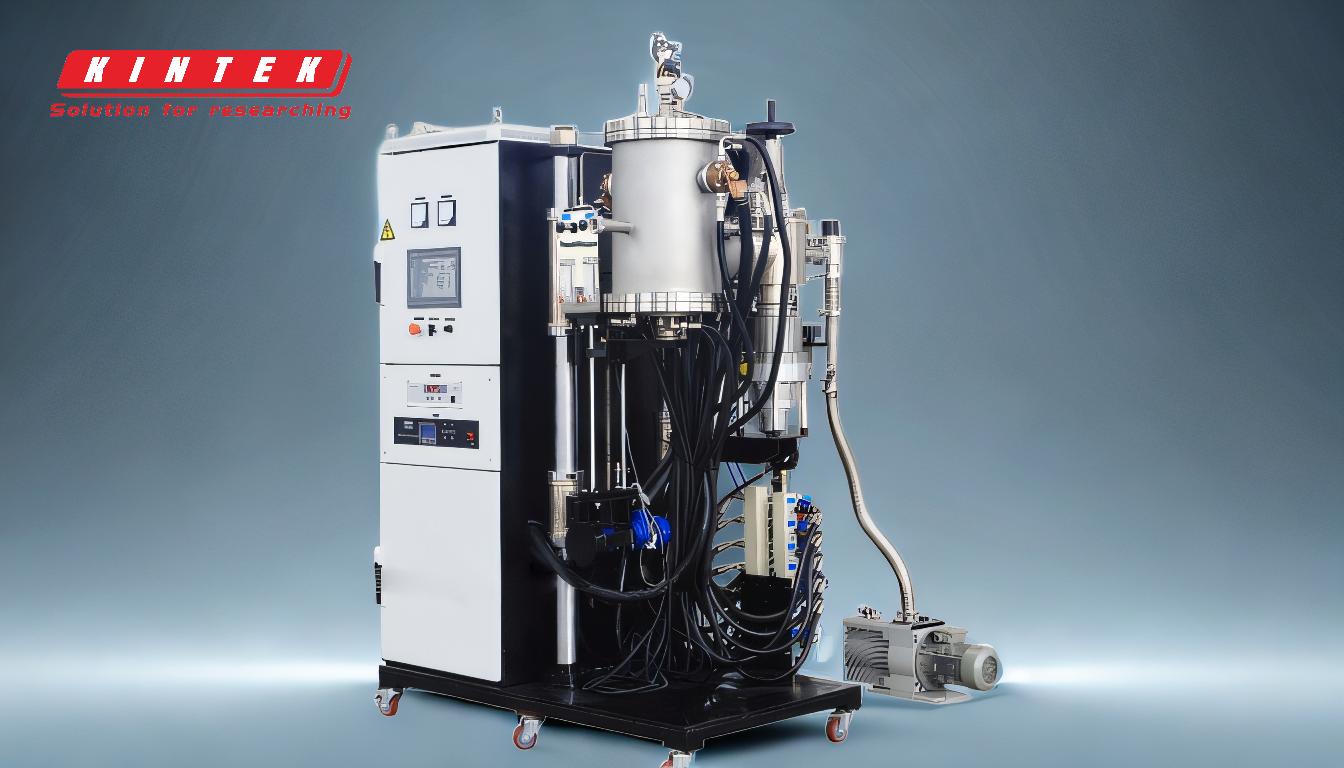
-
Preparación y mezcla del polvo
- El proceso comienza con la preparación de las materias primas en forma de polvo.Estos polvos se mezclan a menudo con aditivos como aglutinantes, lubricantes o agentes de acoplamiento para mejorar la fluidez, la compactación y el comportamiento de sinterización.
- En el caso de los metales, el polvo puede alearse o mezclarse para conseguir propiedades mecánicas o térmicas específicas.En cerámica, el polvo suele calibrarse para garantizar la uniformidad del tamaño de las partículas y la composición.
- Este paso es fundamental porque la calidad del polvo afecta directamente a la densidad, resistencia y precisión dimensional del producto final.
-
Compactación del polvo
- El polvo mezclado se compacta en un "cuerpo verde" utilizando herramientas de alta presión, como prensas hidráulicas o moldes.Este paso da al polvo la forma deseada, creando una estructura coherente pero frágil.
- El proceso de compactación puede realizarse a temperatura ambiente o con un ligero calentamiento, dependiendo del material.La presión aplicada garantiza que las partículas estén en estrecho contacto, lo que es esencial para una sinterización eficaz.
- Para formas complejas, pueden utilizarse técnicas como la soldadura en frío, el láser impreso en 3D o el prensado isostático para conseguir geometrías precisas.
-
Sinterización en atmósfera controlada
- El cuerpo verde se transfiere a un horno de sinterización, donde se calienta a una temperatura justo por debajo del punto de fusión del material.Este paso activa los mecanismos de difusión, haciendo que las partículas se adhieran y se densifiquen.
- En algunos casos, se emplea la sinterización en fase líquida (LPS), en la que se forma una pequeña cantidad de líquido en las interfaces de las partículas, lo que acelera la densificación y mejora las propiedades del material.
- La atmósfera de sinterización (por ejemplo, gas inerte, vacío o ambiente reductor) se controla cuidadosamente para evitar la oxidación o la contaminación y garantizar un calentamiento uniforme.
-
Enfriamiento y solidificación
- Tras la sinterización, el material se enfría gradualmente hasta alcanzar la temperatura ambiente.Este paso permite que los enlaces recién formados se estabilicen, dando lugar a una masa sólida y unificada con porosidad reducida y mayor resistencia mecánica.
- La velocidad de enfriamiento puede influir en la microestructura y las propiedades del material, como la dureza y la tenacidad.
-
Procesado posterior al sinterizado
- Dependiendo de la aplicación, las piezas sinterizadas pueden someterse a pasos adicionales como el mecanizado, el acabado superficial o el montaje.En el caso de la cerámica, suelen utilizarse herramientas de diamante o mecanizado por ultrasonidos para conseguir dimensiones precisas.
- En algunos casos, las piezas sinterizadas se metalizan o sueldan para unirlas a otros componentes, mejorando su funcionalidad en montajes complejos.
-
Control de calidad y pruebas
- A lo largo del proceso, parámetros como la temperatura, la presión y el tiempo de sinterización se controlan de cerca para garantizar que el producto final cumple las especificaciones.
- En las piezas sinterizadas se comprueban propiedades como la densidad, la porosidad, la resistencia y la precisión dimensional para garantizar que son adecuadas para el uso previsto.
Siguiendo estos pasos, los fabricantes pueden producir piezas sinterizadas con propiedades a medida para una amplia gama de aplicaciones, desde componentes de automoción hasta cerámica avanzada en electrónica y aeroespacial.El proceso de sinterización ofrece un método rentable y versátil para crear materiales de alto rendimiento con formas complejas y tolerancias precisas.
Tabla resumen:
Paso | Detalles clave |
---|---|
Preparación del polvo | Materias primas en polvo, mezcladas con aditivos para mejorar sus propiedades. |
Compactación del polvo | Las herramientas de alta presión dan forma al polvo en un "cuerpo verde" con una geometría precisa. |
Sinterización | Calentamiento por debajo del punto de fusión en atmósfera controlada para unir las partículas. |
Enfriamiento y solidificación | El enfriamiento gradual estabiliza las uniones, reduciendo la porosidad y mejorando la resistencia. |
Procesamiento posterior a la sinterización | Pasos adicionales como el mecanizado o el acabado superficial para obtener las dimensiones finales. |
Control de calidad | Pruebas de densidad, porosidad, resistencia y precisión dimensional. |
Descubra cómo las piezas sinterizadas pueden mejorar su proceso de fabricación. contacte con nuestros expertos hoy mismo ¡!