Los recubrimientos de tipo diamante (DLC) se aplican mediante técnicas de deposición avanzadas, principalmente deposición física de vapor (PVD) y deposición química de vapor (CVD).Estos métodos consisten en crear una capa fina y duradera de carbono tipo diamante (DLC) sobre la superficie de herramientas o componentes.El PVD consiste en evaporar un material original y dejar que se condense en la herramienta, formando una monocapa de DLC de 0,5 a 2,5 micras de grosor.El CVD, por su parte, utiliza gases de hidrógeno y metano en una cámara, donde hilos de tungsteno calentados a más de 2.300°C descomponen los gases, permitiendo que los átomos de carbono se recombinen y formen una película de diamante puro sobre la superficie de la herramienta.Ambos métodos requieren un control preciso de la temperatura, la presión y la composición de los gases para lograr resultados óptimos.
Explicación de los puntos clave:
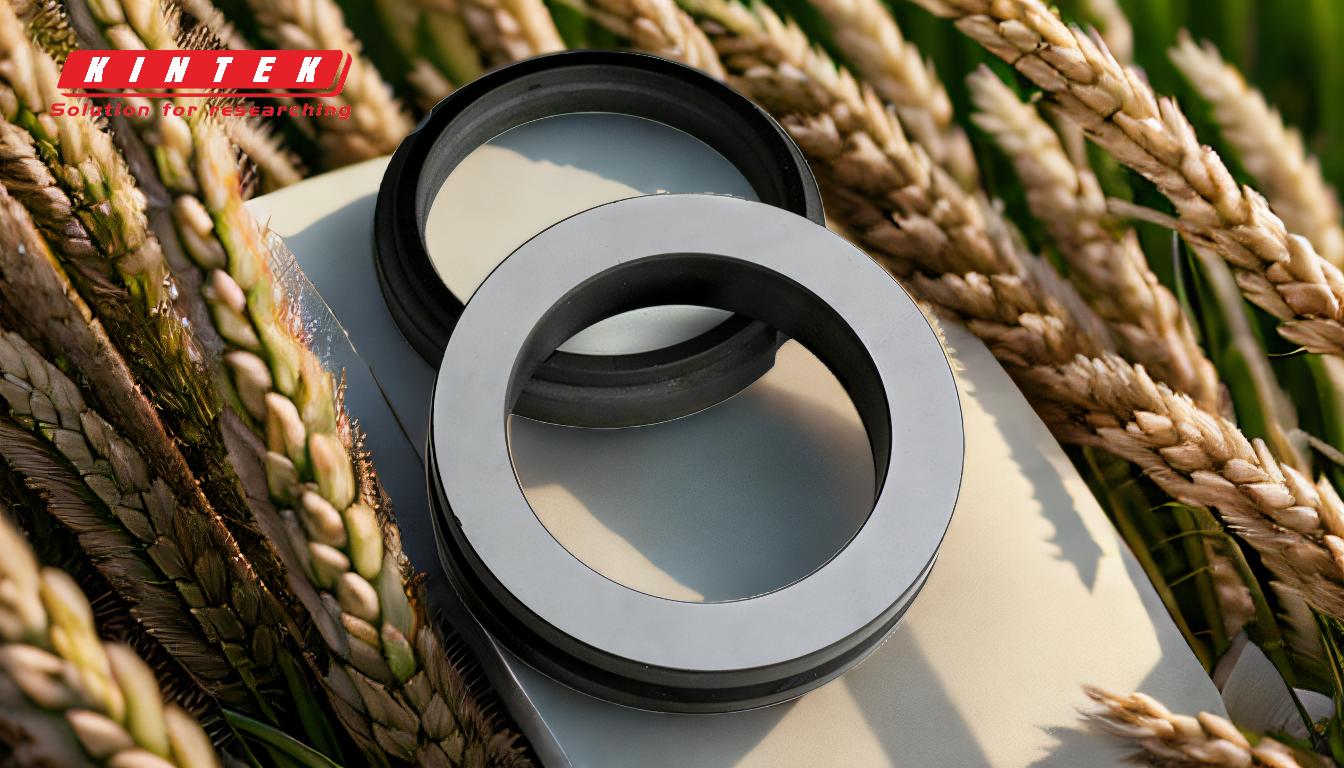
-
Visión general de los recubrimientos tipo diamante (DLC):
- Los recubrimientos DLC son capas finas, duras y resistentes al desgaste que se aplican a herramientas o componentes para mejorar su rendimiento y longevidad.
- Estos recubrimientos son amorfos, es decir, carecen de estructura cristalina, pero presentan propiedades similares a las del diamante, como alta dureza y baja fricción.
-
Métodos de recubrimiento primarios:
-
Deposición física de vapor (PVD):
- El PVD es un método muy utilizado para aplicar revestimientos de DLC.
- El proceso consiste en evaporar un material original (a menudo a base de carbono) en una cámara de vacío.
- A continuación, el material evaporado se condensa en la superficie de la herramienta, formando una capa fina y uniforme de DLC.
- El grosor del revestimiento suele oscilar entre 0,5 y 2,5 micras.
- El PVD es conocido por su capacidad para producir revestimientos adherentes de alta calidad con una excelente resistencia al desgaste.
-
Deposición química en fase vapor (CVD):
- El CVD es otro método habitual para aplicar recubrimientos DLC.
- En este proceso, la herramienta se coloca en una cámara llena de gases de hidrógeno y metano.
- Unos hilos de tungsteno calentados a más de 2.300°C proporcionan la energía necesaria para romper las moléculas de gas.
- A continuación, los átomos de carbono activado se recombinan en la superficie de la herramienta, formando una película de diamante puro.
- El CVD es especialmente eficaz para crear revestimientos más gruesos y duraderos.
-
Deposición física de vapor (PVD):
-
Pasos del proceso de aplicación de recubrimientos DLC:
-
Preparación:
- La herramienta o el componente que se va a recubrir debe limpiarse y prepararse a fondo para garantizar una adhesión adecuada del recubrimiento.
- Esto suele implicar la eliminación de cualquier contaminante superficial, como aceites u óxidos, por medios químicos o mecánicos.
-
Carga en la cámara:
- Las herramientas preparadas se cargan en la cámara de deposición.
- En PVD, la cámara se evacua para crear un vacío, mientras que en CVD, la cámara se llena con los gases apropiados.
-
Deposición:
- En el PVD, el material de partida se evapora y el vapor se condensa en la superficie de la herramienta.
- En el caso del CVD, los gases se activan y los átomos de carbono se depositan en la herramienta.
-
Enfriamiento y acabado:
- Tras la deposición, las herramientas recubiertas se dejan enfriar lentamente para evitar tensiones térmicas.
- Se inspecciona la calidad, el grosor y la adherencia del revestimiento final.
-
Preparación:
-
Parámetros clave y consideraciones:
-
Temperatura:
- Tanto los procesos PVD como CVD requieren altas temperaturas, que suelen oscilar entre 750 °C y más de 2.300 °C, según el método.
- Un control adecuado de la temperatura es crucial para garantizar la calidad y la adherencia del revestimiento.
-
Composición del gas:
- En CVD, la composición de los gases hidrógeno y metano debe controlarse cuidadosamente para lograr la deposición de carbono deseada.
-
Espesor del recubrimiento:
- El grosor del revestimiento de DLC es un factor crítico para determinar su rendimiento.
- Los revestimientos más gruesos pueden ofrecer una mayor resistencia al desgaste, pero también podrían ser más propensos a agrietarse o desprenderse.
-
Adherencia:
- Garantizar una fuerte adherencia entre el revestimiento y el sustrato es esencial para la durabilidad del revestimiento.
- Esto implica a menudo el tratamiento previo del sustrato o el uso de capas intermedias.
-
Temperatura:
-
Aplicaciones de los recubrimientos DLC:
- Los recubrimientos DLC se utilizan en una amplia gama de industrias, como la automovilística, aeroespacial, dispositivos médicos y herramientas de corte.
- Son especialmente apreciados por su capacidad para reducir la fricción, resistir el desgaste y prolongar la vida útil de los componentes sometidos a condiciones duras.
-
Ventajas y limitaciones:
-
Ventajas:
- Alta dureza y resistencia al desgaste.
- Bajo coeficiente de fricción, lo que reduce el consumo de energía y mejora la eficiencia.
- Excelente resistencia a la corrosión.
- Capacidad para revestir geometrías complejas.
-
Limitaciones:
- Alto coste del equipo y del proceso.
- Espesor limitado debido a la posibilidad de tensiones internas y grietas.
- Requiere un control preciso de los parámetros del proceso.
-
Ventajas:
-
Tendencias futuras:
- Las investigaciones en curso se centran en mejorar la adherencia, el grosor y la uniformidad de los revestimientos de DLC.
- Se espera que los avances en nanotecnología y métodos híbridos de recubrimiento mejoren aún más el rendimiento y la aplicabilidad de los recubrimientos DLC en diversas industrias.
Al comprender estos puntos clave, los compradores de equipos y consumibles pueden tomar decisiones informadas sobre la aplicación de recubrimientos tipo diamante, asegurándose de seleccionar el método y los parámetros más adecuados para sus necesidades específicas.
Cuadro sinóptico:
Aspecto | Detalles |
---|---|
Métodos principales | PVD (deposición física de vapor), CVD (deposición química de vapor) |
Espesor del revestimiento | De 0,5 a 2,5 micras (PVD), más grueso para CVD |
Parámetros clave | Temperatura (750°C a 2.300°C), composición del gas, adherencia, espesor del revestimiento |
Aplicaciones | Automoción, aeroespacial, dispositivos médicos, herramientas de corte |
Ventajas | Alta dureza, baja fricción, resistencia a la corrosión, geometrías complejas |
Limitaciones | Coste elevado, espesor limitado, se requiere un control preciso de los parámetros |
Optimice sus herramientas con recubrimientos DLC avanzados-. póngase en contacto con nuestros expertos para obtener soluciones a medida.