La forja en caliente y la forja en frío son dos procesos distintos de trabajo del metal con características, ventajas y desventajas únicas.La forja en caliente implica dar forma al metal a altas temperaturas, normalmente por encima de su punto de recristalización, mientras que la forja en frío se realiza a temperatura ambiente o cerca de ella.La elección entre estos métodos depende de factores como las propiedades del material, la complejidad deseada de la pieza, el volumen de producción y consideraciones de coste.A continuación se ofrece una comparación detallada de los dos procesos, centrándose en sus diferencias, aplicaciones y limitaciones.
Explicación de los puntos clave:
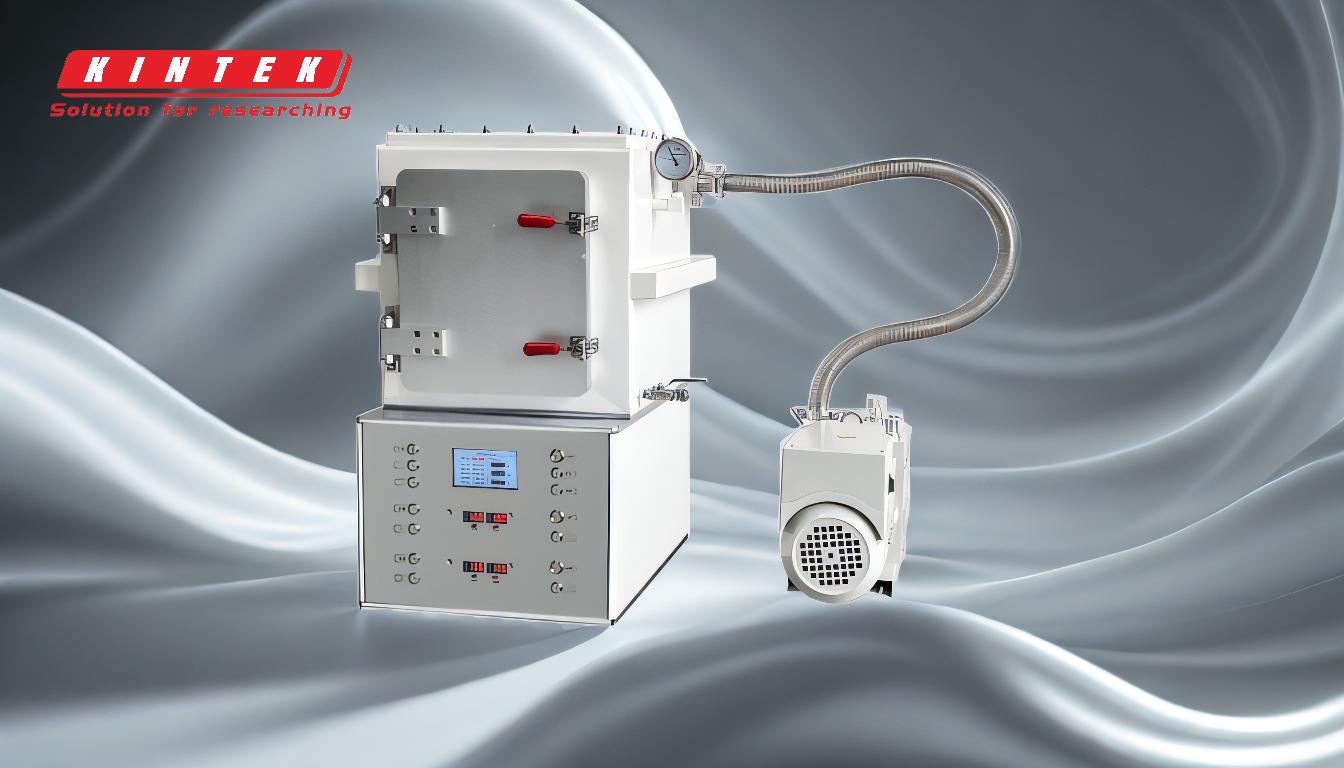
-
Temperatura y comportamiento de los materiales:
- Forja en caliente:Se realiza a temperaturas superiores al punto de recristalización del metal, normalmente entre 950°C y 1250°C para el acero.Esta alta temperatura reduce el límite elástico del metal, facilitando su moldeado y deformación.El proceso también refina la estructura del grano, mejorando propiedades mecánicas como la tenacidad y la ductilidad.
- Forja en frío:Realizado a temperatura ambiente o próxima a ella.El metal conserva su alto límite elástico, pero requiere más fuerza para deformarse.El forjado en frío aumenta la resistencia del material mediante el endurecimiento por deformación, pero puede reducir la ductilidad.
-
Microestructura y propiedades mecánicas:
- Forja en caliente:Da lugar a una estructura de grano refinada y uniforme debido a la recristalización durante el proceso.Esto mejora la tenacidad y la resistencia a la fatiga del material, haciéndolo adecuado para aplicaciones de alto esfuerzo.
- Forjado en frío:Da lugar al endurecimiento por deformación, que aumenta la resistencia y la dureza del material.Sin embargo, la falta de recristalización puede dar lugar a tensiones residuales y a una reducción de la ductilidad, lo que puede requerir un recocido para restaurar las propiedades del material.
-
Complejidad y precisión de las piezas:
- Forja en caliente:Más adecuado para piezas grandes y menos complejas debido a las características de fluidez del metal a altas temperaturas.Es difícil conseguir tolerancias estrechas, por lo que a menudo es necesario un mecanizado secundario.
- Forja en frío:Capaz de producir piezas más pequeñas y complejas con mayor precisión y mejor acabado superficial.Esto reduce la necesidad de mecanizado adicional, por lo que resulta rentable para la producción de grandes volúmenes.
-
Costes de utillaje y troqueles:
- Forja en caliente:Las matrices están sometidas a temperaturas extremas y al desgaste, por lo que requieren un mantenimiento o sustitución frecuentes.Esto aumenta los costes de utillaje, por lo que la forja en caliente resulta menos económica para pequeñas series de producción.
- Forja en frío:Las matrices experimentan menos estrés térmico, lo que se traduce en una mayor vida útil de la herramienta.Sin embargo, el diseño inicial del troquel y los costes de fabricación pueden ser elevados, lo que lo hace más adecuado para la producción a gran escala.
-
Idoneidad de los materiales:
- Forja en caliente:Ideal para metales con gran resistencia a la deformación, como el acero, el titanio y las aleaciones de níquel.También se utiliza para materiales difíciles de conformar a temperaturas más bajas.
- Forja en frío:Más adecuado para metales más blandos como el aluminio, el cobre y los aceros con bajo contenido de carbono, que pueden deformarse fácilmente sin aplicar una fuerza excesiva.
-
Consumo de energía e impacto medioambiental:
- Forja en caliente:Requiere mucha energía para calentar el metal a altas temperaturas, lo que se traduce en un mayor consumo de energía y un mayor impacto medioambiental.
- Forja en frío:Más eficiente desde el punto de vista energético, ya que no requiere calefacción, lo que la convierte en una alternativa más ecológica.
-
Aplicaciones:
- Forja en caliente:Comúnmente utilizado en industrias que requieren componentes de alta resistencia, como la aeroespacial, la automoción (por ejemplo, cigüeñales, bielas) y maquinaria pesada.
- Forja en frío:Preferido para la producción de elementos de fijación, pernos, tornillos y otros componentes pequeños de alta precisión en las industrias de automoción y electrónica.
-
Limitaciones:
- Forja en caliente:Control limitado de la microestructura, mayores requisitos de mecanizado secundario e incapacidad para producir piezas porosas o multimaterial.El coste de las matrices la hace inadecuada para series cortas.
- Forja en frío:Limitado a metales más blandos y geometrías más simples.El endurecimiento por deformación puede requerir un tratamiento térmico adicional para restaurar la ductilidad.
En resumen, la forja en caliente y la forja en frío tienen ventajas y limitaciones distintas.La forja en caliente es ideal para componentes de gran tamaño y alta resistencia con estructuras de grano refinadas, mientras que la forja en frío destaca en la producción de piezas pequeñas y precisas con un mecanizado mínimo.La elección entre una y otra depende de los requisitos específicos de la aplicación, incluidas las propiedades del material, la complejidad de la pieza y el volumen de producción.
Cuadro sinóptico:
Aspecto | Forja en caliente | Forja en frío |
---|---|---|
Temperatura | Por encima del punto de recristalización (950°C-1250°C para el acero) | A temperatura ambiente o próxima a ella |
Comportamiento del material | Menor límite elástico, estructura de grano refinada, mayor tenacidad y ductilidad | Alto límite elástico, endurecimiento por deformación, aumento de la resistencia, reducción de la ductilidad |
Complejidad de la pieza | Adecuado para piezas más grandes y menos complejas | Ideal para piezas más pequeñas y complejas de gran precisión |
Costes de utillaje | Más elevados debido a las temperaturas extremas y al desgaste | Menor tensión térmica, mayor vida útil de la herramienta, pero costes iniciales de la matriz elevados |
Materiales adecuados | Acero, titanio, aleaciones de níquel | Aluminio, cobre, aceros bajos en carbono |
Consumo de energía | Elevado consumo de energía debido a la calefacción | Eficiencia energética, no requiere calefacción |
Aplicaciones | Aeroespacial, automoción (cigüeñales, bielas), maquinaria pesada | Fijaciones, pernos, tornillos, automoción, electrónica |
Limitaciones | Control limitado de la microestructura, mecanizado secundario, coste elevado de las matrices | Limitado a metales más blandos, el endurecimiento por deformación puede requerir recocido |
¿Necesita ayuda para elegir el proceso de forja adecuado para su proyecto? Póngase en contacto hoy mismo con nuestros expertos ¡!