La forja es un proceso de fabricación muy versátil que ofrece numerosas ventajas, como una mayor resistencia de las piezas, formas personalizadas y especificaciones de rendimiento únicas.Resulta especialmente beneficioso para aplicaciones que requieren gran resistencia y durabilidad.El proceso comprime la estructura de grano del metal, mejorando sus propiedades mecánicas y reduciendo defectos como la porosidad y la segregación de la aleación.Sin embargo, la forja también tiene sus limitaciones, como el mayor coste inicial de las herramientas y las limitaciones para producir geometrías muy complejas.A continuación analizamos en detalle las principales ventajas y limitaciones del proceso de forja.
Explicación de los puntos clave:
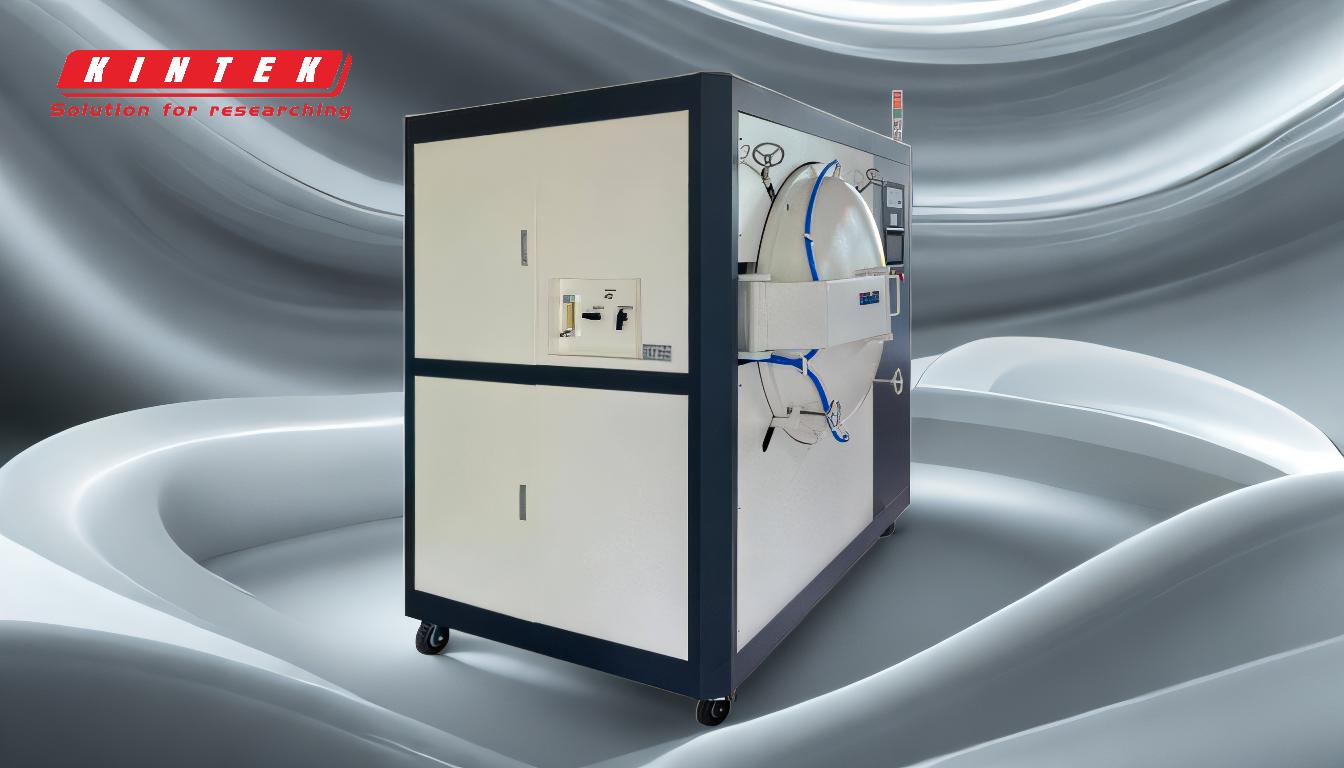
-
Ventajas de la forja:
-
Resistencia y durabilidad superiores:
- El forjado comprime la estructura de grano del metal, alineándola con la forma de la pieza.Este flujo de grano mejora la resistencia, la tenacidad y la resistencia a la fatiga del material, lo que hace que las piezas forjadas sean ideales para aplicaciones sometidas a grandes esfuerzos.
-
Propiedades metalúrgicas mejoradas:
- El proceso minimiza los defectos metalúrgicos como la porosidad, los huecos y la segregación de la aleación.El resultado es un material más uniforme y sin defectos, lo que mejora la respuesta de la pieza al tratamiento térmico y reduce el riesgo de fallos.
-
Formas y tamaños personalizados:
- La forja permite crear formas y tamaños personalizados, lo que la hace idónea para aplicaciones especializadas.El proceso puede producir piezas con especificaciones de rendimiento únicas que son difíciles de conseguir con otros métodos de fabricación.
-
Reducción del tiempo de mecanizado:
- Las piezas forjadas suelen requerir menos mecanizado que las piezas fundidas o mecanizadas.La forma casi neta producida por la forja reduce el desperdicio de material y el tiempo de mecanizado, lo que se traduce en un ahorro de costes.
-
Rentable para grandes volúmenes de producción:
- Aunque los costes iniciales de utillaje para la forja pueden ser elevados, el proceso resulta rentable para series de producción de gran volumen debido a su eficacia y a la reducción del desperdicio de material.
-
Resistencia y durabilidad superiores:
-
Limitaciones de la forja:
-
Costes iniciales de utillaje elevados:
- La forja requiere matrices y herramientas especializadas, cuyo diseño y fabricación pueden resultar caros.Esto hace que el proceso sea menos económico para la producción de bajo volumen o prototipos.
-
Complejidad geométrica limitada:
- La forja es menos adecuada para producir geometrías muy complejas o detalles intrincados en comparación con procesos como la fundición o la fabricación aditiva.El proceso es más adecuado para piezas con formas relativamente sencillas.
-
Limitaciones del material:
- No todos los materiales son adecuados para la forja.Algunas aleaciones y materiales pueden no responder bien a las altas temperaturas y presiones que implica el proceso, lo que limita la gama de aplicaciones.
-
Limitaciones de tamaño:
- El tamaño de las piezas forjadas está limitado por la capacidad del equipo de forja.Las piezas extremadamente grandes o pesadas pueden requerir equipos especializados, lo que aumenta los costes y la complejidad.
-
Acabado superficial y tolerancias:
- Las piezas forjadas suelen requerir mecanizado adicional para conseguir tolerancias y acabados superficiales precisos.Aunque la forja reduce el tiempo de mecanizado, no elimina la necesidad de operaciones secundarias.
-
Costes iniciales de utillaje elevados:
En resumen, la forja es un proceso de fabricación muy eficaz para producir piezas resistentes, duraderas y con formas personalizadas.Sus ventajas en cuanto a resistencia, propiedades metalúrgicas y rentabilidad para la producción de grandes volúmenes lo convierten en la opción preferida para muchas industrias.Sin embargo, sus limitaciones en cuanto a complejidad geométrica, costes iniciales de utillaje e idoneidad de los materiales deben tenerse muy en cuenta a la hora de seleccionar el método de fabricación adecuado para una aplicación determinada.
Cuadro sinóptico:
Aspecto | Ventajas | Limitaciones |
---|---|---|
Resistencia y durabilidad | Mayor resistencia, tenacidad y resistencia a la fatiga gracias a la estructura de grano comprimido. | Costes iniciales de utillaje elevados, lo que lo hace menos económico para la producción de bajo volumen. |
Propiedades metalúrgicas | Minimización de defectos como la porosidad y la segregación de la aleación, mejorando la uniformidad del material. | Complejidad geométrica limitada, inadecuada para diseños muy intrincados. |
Formas y tamaños personalizados | Posibilidad de producir formas y tamaños personalizados para aplicaciones especializadas. | Limitaciones de material; no todas las aleaciones son aptas para el forjado. |
Reducción del tiempo de mecanizado | La forma casi neta reduce el desperdicio de material y el tiempo de mecanizado, ahorrando costes. | Limitaciones de tamaño debidas a la capacidad de los equipos, que requieren herramientas especializadas. |
Rentabilidad | Económico para grandes volúmenes de producción gracias a su eficacia y a la reducción de residuos. | Requiere mecanizado adicional para obtener tolerancias y acabados superficiales precisos. |
¿Desea más información sobre la forja y las ventajas que puede ofrecer a su proyecto? Póngase en contacto hoy mismo con nuestros expertos para un asesoramiento personalizado.