La soldadura por inducción, aunque eficaz y precisa, presenta varios inconvenientes que pueden afectar a su idoneidad para determinadas aplicaciones.Por ejemplo, la necesidad de un control preciso de la temperatura debido a los estrechos intervalos de fusión de los metales base y de aportación, y la posibilidad de que se reduzca la dureza del material después de la soldadura.Además, el proceso puede ser técnicamente exigente y requerir operarios cualificados y equipos especializados, lo que puede dar lugar a un mayor consumo de energía y a tiempos de procesamiento más largos.Los costes medioambientales y de limpieza antes de la soldadura también se suman al gasto total.Estos factores deben tenerse muy en cuenta a la hora de elegir la soldadura por inducción para un proyecto.
Explicación de los puntos clave:
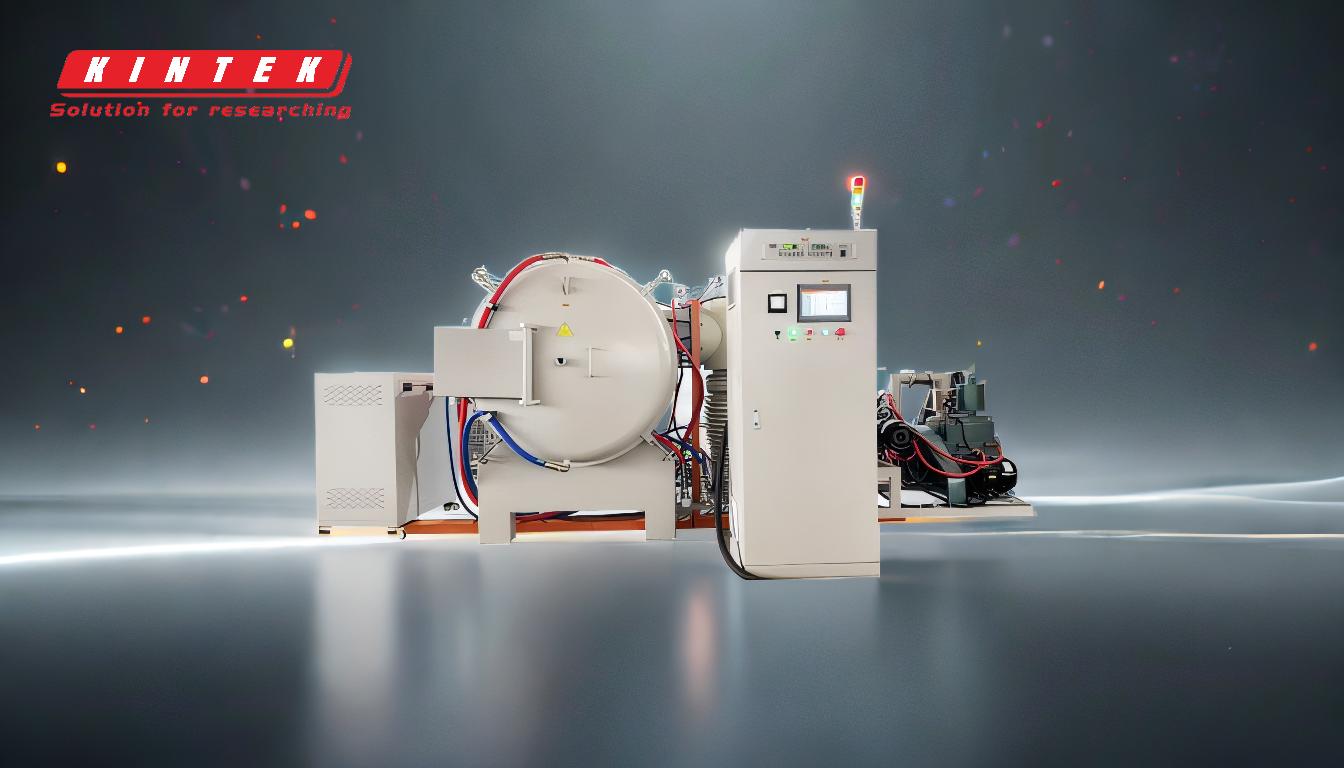
-
Control preciso de la temperatura y distribución térmica homogénea:
- La soldadura por inducción requiere un control preciso de la temperatura, ya que los intervalos de fusión de los metales base y de aportación suelen estar muy próximos.Esta precisión es crucial para evitar el sobrecalentamiento o el subcalentamiento, que pueden comprometer la calidad de la unión.Conseguir una distribución térmica homogénea también es un reto, especialmente en geometrías complejas, ya que un calentamiento desigual puede debilitar las juntas o dañar el material.
-
Reducción de la dureza del material:
- Los procesos de alta temperatura, como la soldadura por inducción, pueden reducir la dureza de ciertos materiales, en particular los metales que se someten a recocido o ablandamiento a temperaturas elevadas.Esta reducción de la dureza puede afectar a las propiedades mecánicas del producto final, haciéndolo menos adecuado para aplicaciones que requieran gran resistencia o resistencia al desgaste.
-
Dificultad técnica y mano de obra cualificada:
- La soldadura por inducción es un proceso técnicamente exigente que requiere operarios cualificados para manejar el equipo y garantizar la correcta formación de las uniones.La complejidad de la configuración y el mantenimiento de las bobinas de inducción, junto con la necesidad de un control preciso de los parámetros de calentamiento, lo hacen menos accesible para los usuarios inexpertos.
-
Elevado consumo energético:
- El proceso puede consumir mucha energía, especialmente en operaciones a gran escala o continuas.Las bobinas de inducción requieren una gran cantidad de energía eléctrica para generar los campos electromagnéticos necesarios para el calentamiento, lo que supone unos costes operativos más elevados que otros métodos alternativos de soldadura fuerte.
-
Largos tiempos de procesamiento:
- Aunque la soldadura por inducción suele ser más rápida que la soldadura en horno, puede requerir tiempos de proceso más largos que otros métodos, como la soldadura con soplete.Esto es especialmente cierto en el caso de ensamblajes complejos o cuando hay que soldar varias uniones secuencialmente, lo que puede ralentizar el ritmo de producción.
-
Elevados costes de limpieza y medioambientales:
- Antes de la soldadura por inducción, los componentes suelen requerir una limpieza a fondo para eliminar óxidos, aceites y otros contaminantes que pueden interferir en el proceso de soldadura.Este proceso de limpieza puede ser costoso y llevar mucho tiempo.Además, hay que tener en cuenta el impacto medioambiental del uso de fundentes o productos de limpieza, ya que pueden requerir métodos especiales de eliminación o contribuir a la contaminación.
-
Restricciones de diseño:
- La soldadura por inducción requiere ajustes estrechos entre los componentes para facilitar la acción capilar, que es esencial para un flujo adecuado del metal de aportación.Este requisito puede imponer restricciones de diseño, ya que las piezas deben fabricarse con tolerancias muy ajustadas.Además, la ubicación del material de soldadura debe planificarse cuidadosamente durante la fase de diseño, lo que añade complejidad al proceso.
Al conocer estas desventajas, los compradores e ingenieros pueden decidir con conocimiento de causa si la soldadura fuerte por inducción es la opción adecuada para su aplicación específica, sopesando los pros y los contras frente a otros métodos de soldadura fuerte.
Tabla resumen:
Desventaja | Descripción |
---|---|
Control preciso de la temperatura | Requiere una estrecha vigilancia para evitar el sobrecalentamiento o el subcalentamiento. |
Reducción de la dureza del material | Las altas temperaturas pueden ablandar los metales, reduciendo su resistencia y su resistencia al desgaste. |
Dificultad técnica y mano de obra cualificada | Requiere operarios cualificados y equipos especializados. |
Alto consumo de energía | Proceso intensivo en energía, lo que conlleva mayores costes operativos. |
Tiempos de procesamiento largos | Más lentos que algunas alternativas, especialmente para ensamblajes complejos. |
Costes de limpieza y medioambientales elevados | Requiere una limpieza a fondo y puede implicar fundentes perjudiciales para el medio ambiente. |
Restricciones de diseño | Las piezas deben tener tolerancias muy ajustadas, lo que añade complejidad al diseño y la fabricación. |
¿Necesita ayuda para decidir si la soldadura por inducción es adecuada para su proyecto? Póngase en contacto con nuestros expertos para un asesoramiento personalizado.