La sinterización es un proceso crítico en la fabricación de materiales, pero no está exento de problemas y defectos.Entre los problemas más comunes están el exceso de sinterización, la falta de sinterización, la formación de ampollas y la sudoración, que pueden comprometer la calidad y el rendimiento del producto final.Además, problemas como el alabeo y el pandeo debidos a la gravedad o la fricción pueden provocar defectos estructurales.La sinterización a alta temperatura, aunque eficaz, consume mucha energía y puede limitar la síntesis del material y la estabilidad de las fases.Los métodos tradicionales de sinterización suelen requerir un calentamiento prolongado y altas temperaturas, lo que provoca el crecimiento de granos y poros residuales.Estos defectos y limitaciones ponen de manifiesto la necesidad de controlar con precisión los parámetros de sinterización para garantizar unos resultados óptimos.
Explicación de los puntos clave:
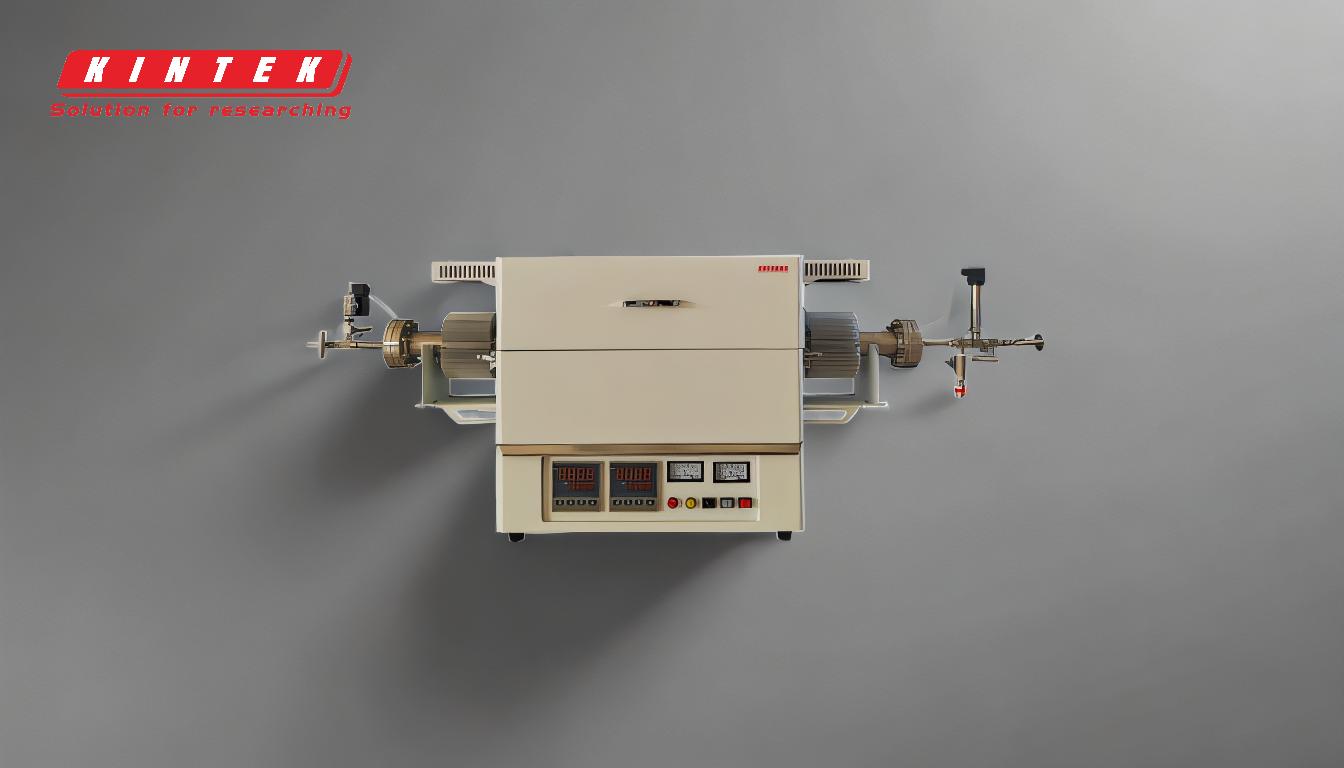
-
Oversintering:
- Definición:Se produce cuando la temperatura de sinterización es demasiado elevada o el tiempo de sinterización demasiado largo.
- Impacto:Provoca el deterioro del producto, como el crecimiento excesivo del grano, la pérdida de propiedades mecánicas o incluso la fusión del material.
- Ejemplo:En la fabricación de cerámica, el exceso de sinterización puede hacer que el material se vuelva quebradizo y pierda su integridad estructural.
-
Sinterización insuficiente:
- Definición:Se produce cuando la temperatura de sinterización es demasiado baja o el tiempo de sinterización demasiado corto.
- Impacto:Da lugar a una unión inadecuada entre las partículas, lo que provoca una resistencia mecánica deficiente y una densificación insuficiente.
- Ejemplo:En la sinterización de polvos metálicos, la sinterización insuficiente puede dar lugar a un producto final poroso con propiedades estructurales débiles.
-
Formación de ampollas:
- Definición:Defectos superficiales causados por la liberación de gases atrapados durante el proceso de sinterización.
- Impacto:Da lugar a imperfecciones superficiales, como burbujas o ampollas, que pueden afectar a la calidad estética y funcional del producto.
- Ejemplo:En las baldosas cerámicas, la formación de ampollas puede provocar irregularidades superficiales inaceptables para acabados de alta calidad.
-
Sudoración:
- Definición:Se produce cuando una fase líquida se filtra del material durante el tratamiento térmico.
- Impacto:Puede provocar la contaminación de la superficie, una distribución desigual del material y comprometer las propiedades mecánicas.
- Ejemplo:En determinadas aleaciones metálicas, la transpiración puede provocar la segregación de elementos de aleación, lo que da lugar a propiedades de material incoherentes.
-
Alabeo y hundimiento:
- Definición:Deformación del material debida a la gravedad o a la fricción durante el proceso de sinterización.
- Impacto:Da lugar a imprecisiones dimensionales y defectos estructurales en la pieza final.
- Ejemplo:En la fabricación aditiva, el alabeo puede hacer que las piezas se desvíen de su forma prevista, lo que requiere un procesamiento posterior para corregirlo.
-
Retos del sinterizado a alta temperatura:
- Definición:Procesos de sinterización que requieren temperaturas extremadamente altas.
- Impacto:Consume más energía y puede limitar los tipos de materiales que pueden sinterizarse debido a problemas de estabilidad térmica.
- Ejemplo:La sinterización a alta temperatura de los materiales cerámicos puede dar lugar a inestabilidad de fase, en la que el material puede sufrir transformaciones de fase no deseadas.
-
Crecimiento del grano y poros residuales:
- Definición:Problemas derivados de tiempos de sinterización prolongados y altas temperaturas.
- Impacto:El crecimiento de los granos puede reducir la resistencia mecánica del material, mientras que los poros residuales pueden comprometer la densidad y la integridad estructural.
- Ejemplo:En pulvimetalurgia, un crecimiento excesivo del grano puede dar lugar a una microestructura gruesa, lo que reduce la tenacidad del material.
-
Consumo de energía e impacto medioambiental:
- Definición:Elevados requisitos energéticos para los métodos tradicionales de sinterización.
- Impacto:Aumenta los costes de producción y la huella medioambiental, haciendo que el proceso sea menos sostenible.
- Ejemplo:El elevado consumo energético de los hornos de sinterización contribuye a aumentar los costes operativos y las emisiones de carbono.
-
Desafíos del control de procesos:
- Definición:Dificultad para mantener un control preciso de los parámetros de sinterización.
- Impacto:Resultados de sinterización incoherentes, con la consiguiente variabilidad en la calidad del producto.
- Ejemplo:Un control inconsistente de la temperatura puede dar lugar a piezas con densidades y propiedades mecánicas variables.
-
Limitaciones materiales:
- Definición:Limitaciones de los tipos de materiales que pueden sinterizarse eficazmente.
- Impacto:Limita la gama de aplicaciones y las innovaciones potenciales en la ciencia de los materiales.
- Ejemplo:Ciertos materiales avanzados, como las cerámicas de alto rendimiento, pueden no ser adecuados para los métodos tradicionales de sinterización debido a su sensibilidad térmica.
En conclusión, aunque el sinterizado es un potente proceso de fabricación, es esencial comprender y mitigar sus posibles defectos y limitaciones.Controlando cuidadosamente los parámetros de sinterización y explorando métodos de sinterización alternativos, los fabricantes pueden mejorar la calidad del producto y ampliar la gama de materiales que pueden sinterizarse eficazmente.
Tabla resumen:
Defecto/Limitación | Definición | Impacto | Ejemplo |
---|---|---|---|
Sobreentrelazado | Temperatura demasiado alta o tiempo demasiado largo. | Deterioro del producto, crecimiento excesivo del grano o fusión. | La cerámica se vuelve quebradiza y pierde integridad estructural. |
Sinterización insuficiente | Temperatura demasiado baja o tiempo demasiado corto. | Resistencia mecánica deficiente y densificación insuficiente. | La sinterización del polvo metálico da lugar a un producto poroso y débil. |
Formación de ampollas | Gases atrapados liberados durante la sinterización. | Imperfecciones superficiales como burbujas o ampollas. | Las baldosas cerámicas desarrollan irregularidades superficiales. |
Sudoración | La fase líquida se filtra durante el tratamiento térmico. | Contaminación superficial, distribución desigual del material. | Las aleaciones metálicas experimentan segregación de elementos, lo que da lugar a propiedades incoherentes. |
Alabeo y pandeo | Deformación debida a la gravedad o a la fricción. | Imprecisiones dimensionales y defectos estructurales. | Las piezas de fabricación aditiva se desvían de las formas previstas. |
Retos de las altas temperaturas | Temperaturas extremadamente altas. | Elevado consumo de energía y limitaciones de material. | Las cerámicas sufren transformaciones de fase no deseadas. |
Crecimiento de grano y poros | Calentamiento prolongado y altas temperaturas. | Resistencia mecánica reducida y densidad comprometida. | La pulvimetalurgia da lugar a microestructuras gruesas. |
Consumo de energía | Elevados requisitos energéticos para la sinterización tradicional. | Mayores costes e impacto medioambiental. | Los hornos de sinterización contribuyen a aumentar las emisiones de carbono. |
Control del proceso | Dificultad para mantener unos parámetros de sinterización precisos. | Calidad irregular del producto. | Las piezas tienen densidades y propiedades mecánicas variables. |
Limitaciones de los materiales | Limitaciones de los materiales sinterizables. | Limita las aplicaciones y las innovaciones. | Las cerámicas de alto rendimiento pueden no ser adecuadas para la sinterización tradicional. |
¿Tiene problemas con los defectos de sinterización?Optimice su proceso con el asesoramiento de expertos. póngase en contacto con nosotros ¡!