El tratamiento térmico, si bien es esencial para mejorar las propiedades mecánicas de los metales, presenta varias desventajas, particularmente cuando se consideran métodos de atmósfera controlada y ordinaria. El tratamiento térmico en atmósfera controlada puede provocar rugosidad en la superficie, pérdida de elementos metálicos de la superficie y desafíos en la gestión del gas, mientras que el tratamiento térmico en atmósfera ordinaria a menudo produce oxidación de la superficie y un entorno de trabajo hostil. Ambos métodos tienen limitaciones en términos de aplicabilidad y desafíos operativos, que pueden afectar la calidad y eficiencia del proceso de tratamiento.
Puntos clave explicados:
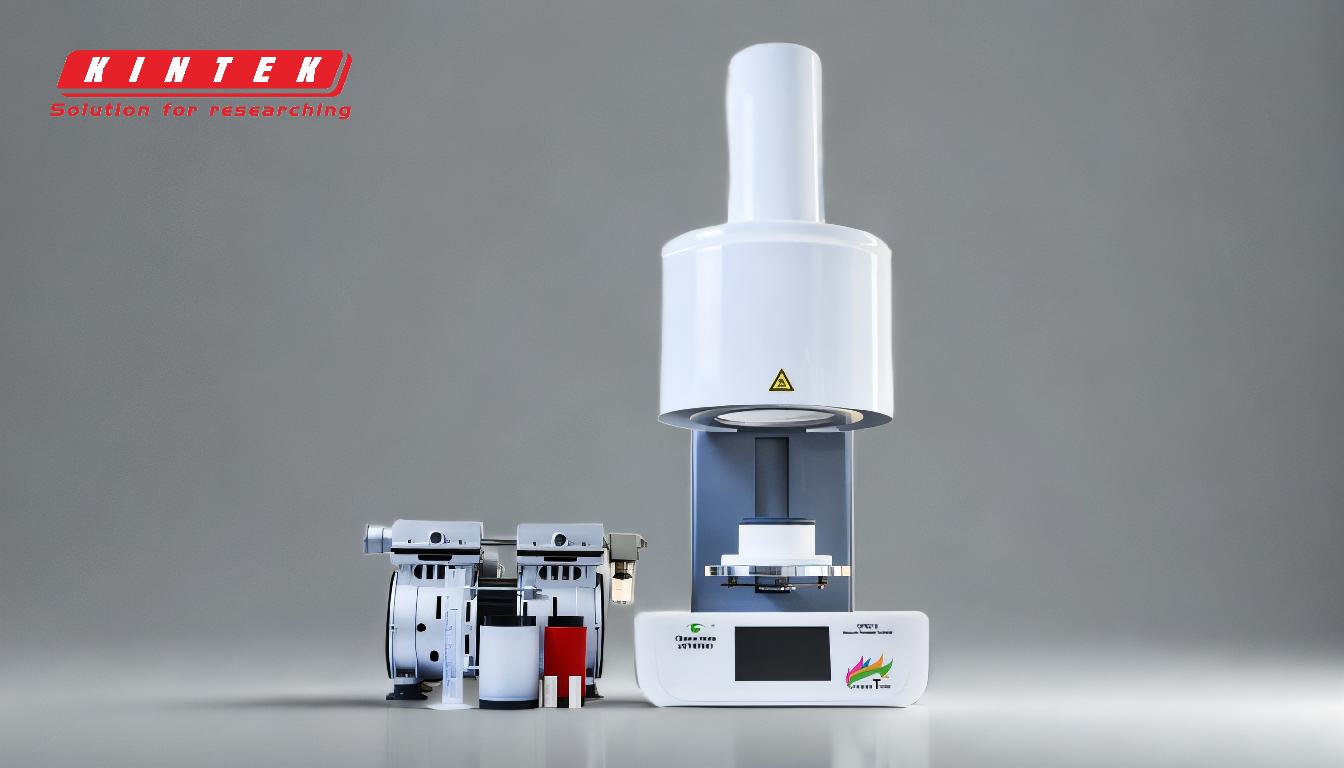
-
Problemas de calidad superficial en el tratamiento térmico en atmósfera controlada:
- Superficie rugosa y no brillante: El tratamiento térmico en atmósfera controlada a menudo da como resultado una superficie rugosa y sin brillo en la pieza de trabajo. Esto puede resultar problemático para aplicaciones que requieren un acabado suave y estéticamente agradable.
- Pérdida de elementos metálicos superficiales.: El proceso puede provocar el agotamiento de ciertos elementos metálicos de la superficie, lo que podría afectar las propiedades y el rendimiento generales del material.
-
Desafíos operativos en el tratamiento térmico con atmósfera controlada:
- Erosión de elementos calefactores eléctricos.: El ambiente dentro de un horno de atmósfera controlada puede causar erosión de los elementos calefactores eléctricos, lo que genera mayores costos de mantenimiento y posibles tiempos de inactividad.
- Uso y recuperación de gas: La gestión de los gases utilizados en el proceso y la recuperación de los gases reductores puede ser compleja y costosa, lo que se suma a los desafíos operativos.
-
Oxidación de superficies en tratamiento térmico en atmósfera ordinaria:
- Formación de película de óxido: El tratamiento térmico en atmósfera ordinaria normalmente da como resultado la formación de una película de óxido en la superficie de la pieza de trabajo. Esta capa de óxido puede afectar las propiedades del material y puede requerir un procesamiento adicional para eliminarla.
-
Ambiente de tratamiento severo:
- Condiciones ambientales: Tanto los tratamientos térmicos en atmósfera controlada como los ordinarios a menudo implican condiciones ambientales adversas, que pueden ser desafiantes para los operadores y pueden requerir equipos especializados y medidas de seguridad.
-
Aplicabilidad limitada:
- Restricciones de materiales y aplicaciones: La aplicabilidad de ambos métodos de tratamiento térmico puede estar limitada por el tipo de material que se está tratando y los requisitos específicos de la aplicación. Esto puede restringir el uso de estos métodos en ciertas industrias o para componentes particulares.
En resumen, si bien el tratamiento térmico es un proceso crítico para mejorar las propiedades de los materiales, presenta varias desventajas que deben gestionarse con cuidado. Estos incluyen problemas de calidad de la superficie, desafíos operativos, preocupaciones ambientales y limitaciones en la aplicabilidad. Comprender estos inconvenientes es esencial para seleccionar el método de tratamiento térmico adecuado y garantizar los resultados deseados en el procesamiento de materiales.
Tabla resumen:
Desventaja | Atmósfera controlada | Atmósfera ordinaria |
---|---|---|
Calidad de la superficie | Superficie rugosa y poco brillante; pérdida de elementos metálicos superficiales | Formación de película de óxido |
Desafíos operativos | Erosión de elementos calefactores eléctricos; gestión compleja de gases | Ambiente de trabajo duro |
Impacto ambiental | Duras condiciones para los operadores; equipo especializado requerido | Duras condiciones para los operadores; equipo especializado requerido |
Aplicabilidad | Limitado por el tipo de material y los requisitos de aplicación. | Limitado por el tipo de material y los requisitos de aplicación. |
¿Necesita ayuda para seleccionar el método de tratamiento térmico adecuado para sus materiales? Póngase en contacto con nuestros expertos hoy ¡Para soluciones personalizadas!