El endurecimiento por inducción, si bien es eficaz para mejorar la resistencia al desgaste y la fatiga en piezas de trabajo simples, tiene varias desventajas. No es adecuado para piezas mecánicas complejas debido a su escasa adaptabilidad, lo que limita su aplicación a piezas más simples en la producción en línea de montaje. Además, el proceso carece de capacidad de refinación, lo que requiere que los materiales de carga estén libres de óxidos y sean de composición conocida. Los elementos de aleación también pueden perderse durante el proceso debido a la oxidación, lo que hace necesario volver a agregarlos a la masa fundida. Estas limitaciones hacen que el endurecimiento por inducción sea menos versátil y más difícil de gestionar en determinados escenarios de fabricación.
Puntos clave explicados:
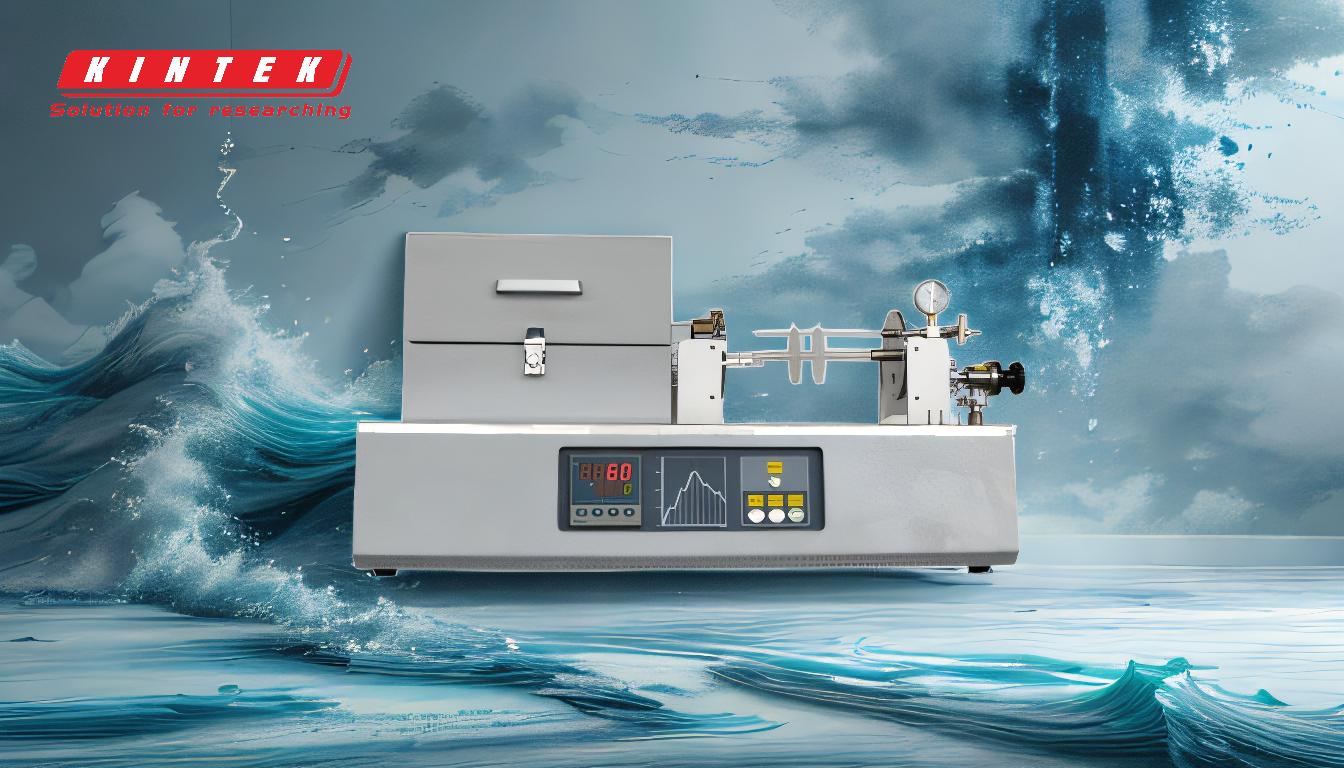
-
Poca adaptabilidad para piezas de trabajo complejas:
- El endurecimiento por inducción es eficaz principalmente para piezas de trabajo simples, como las que se utilizan en la producción en línea de montaje. Sin embargo, tiene problemas con piezas mecánicas complejas debido a su limitada adaptabilidad. El proceso requiere un control preciso del calentamiento y enfriamiento, lo que puede resultar difícil de lograr con geometrías intrincadas. Esta limitación restringe su uso a componentes más simples, reduciendo su versatilidad en la fabricación.
-
Falta de capacidad de refinación:
- A diferencia de otros procesos de endurecimiento, el endurecimiento por inducción no refina el material. Esto significa que los materiales de carga utilizados ya deben estar libres de óxidos y tener una composición conocida. Cualquier impureza o inconsistencia en el material puede generar resultados subóptimos, lo que hace que el proceso sea menos indulgente y más dependiente de materiales de entrada de alta calidad.
-
Pérdida de elementos de aleación:
- Durante el proceso de endurecimiento por inducción, algunos elementos de aleación pueden perderse debido a la oxidación. Esto puede alterar las propiedades del material y reducir la eficacia del proceso de endurecimiento. Para contrarrestar esto, es posible que los fabricantes necesiten volver a agregar estos elementos a la masa fundida, lo que agrega complejidad y costo al proceso. Este problema es particularmente problemático cuando se trabaja con materiales que requieren composiciones de aleación precisas para un rendimiento óptimo.
-
Alcance de aplicación limitado:
- Las limitaciones de la tecnología para manejar formas complejas y su dependencia de materiales de entrada de alta calidad restringen su alcance de aplicación. Es más adecuado para la producción de grandes volúmenes de piezas simples, donde se pueden maximizar los beneficios de una mayor resistencia al desgaste y a la fatiga. Sin embargo, para aplicaciones más especializadas o complejas, otros métodos de endurecimiento pueden ser más apropiados.
-
Desafíos en el control de procesos:
- Lograr resultados consistentes con el endurecimiento por inducción requiere un control preciso sobre las velocidades de calentamiento y enfriamiento. Cualquier desviación puede provocar un endurecimiento desigual, reduciendo la eficacia del proceso. Esta necesidad de un control estricto puede aumentar la complejidad del proceso de fabricación y requerir equipos y experiencia más sofisticados.
En resumen, si bien el endurecimiento por inducción ofrece ventajas significativas en términos de resistencia al desgaste y la fatiga para piezas de trabajo simples, sus desventajas (como la escasa adaptabilidad para piezas complejas, la falta de capacidad de refinación y la posible pérdida de elementos de aleación) limitan su aplicación más amplia. Estos factores lo hacen menos adecuado para ciertos escenarios de fabricación, particularmente aquellos que involucran geometrías complejas o materiales especializados.
Tabla resumen:
Desventaja | Descripción |
---|---|
Poca adaptabilidad para piezas complejas | Efectividad limitada para geometrías complejas, lo que restringe el uso a componentes más simples. |
Falta de capacidad de refinación | Requiere materiales de alta calidad y libres de óxido; sin refinar durante el proceso. |
Pérdida de elementos de aleación | La oxidación durante el endurecimiento puede provocar la pérdida de elementos de aleación, lo que requiere una nueva adición. |
Alcance de aplicación limitado | Más adecuado para la producción de grandes volúmenes de piezas simples; menos efectivo para materiales especializados. |
Desafíos en el control de procesos | Requiere un control preciso de las velocidades de calentamiento y enfriamiento para obtener resultados consistentes. |
¿Necesita una solución de endurecimiento adaptada a sus necesidades? Contáctanos hoy para explorar alternativas!